Concept explainers
The rolling force and the power requirement for single pass.
The rolling force and the power requirement for double pass.

Answer to Problem 6.120P
Rolling force is
Rolling force is
Explanation of Solution
Given:
The initial height is
The final height is
The radius of the rollers is
The coefficient of friction is
The width of the sheet is
Velocity of the roll surface is
Formula used:
The expression for change in height for single pass is given as,
The expression for change in height for double pass is given as,
The expression for contact length for single passis given as,
The expression for contact length is given as,
The expression for rolling force is given as,
The rolling force for double pass can be given as,
Here,
The expression for roll separatingstressis given as,
Here, strength coefficient is
The expression for the strain is given as,
The expression for the angular velocity is given as,
The expression for the arm length is given as,
The expression for the arm length in double pass is given as,
The expression for the torque is given as,
The expression for the torque for double pass is given as,
The expression for the power is given as,
The expression for the power for double pass is given as,
Calculation:
The change in height can be calculated as,
The contact length can be calculated as,
The strain can be calculated as,
The roll separating stress can be calculated as,
Refer to table 2.2“Typical values of strength coefficient
The force for single pass can be calculated as,
The angular velocity can be calculated as,
The arm length can be calculated as,
The torque can be calculated as,
The power can be calculated as,
The change in height for double pass can be calculated as,
The contact length for double pass can be given as,
The arm length for the double pass can be calculated as,
The rolling force for double pass can be given as,
The torque for the double pass can be given as,
The power required for double pass can be given as,
Conclusion:
Therefore, rolling force is
Therefore, rolling force is
Want to see more full solutions like this?
Chapter 6 Solutions
EBK MANUFACTURING PROCESSES FOR ENGINEE
- Estimate the power for annealed low carbon steel strip 200 mm wide and 10 mm thick, rolled to a thickness of 6 mm. The roll radius is 200 mm, and the roll rotates at 200 rev/min; use coefficient of friction at the die-work interface (p)=0.1. A low carbon steel such as AISI 1020 has K (strength coefficient) = 530 MPa and n ( strain hardening exponent) =0.26a)1059 kWb)950 kWc)1183 kWd)875 kWarrow_forwardEstimate the roll force, F, and the torque for an AISI 1020 carbon-steel strip that is 200 mmwide, 10 mm thick, and rolled to a thickness of 7 mm. The roll radius is 200 mm, and itrotates at 200 rpm. Note that K = 530 MPa and n = 0.26.arrow_forward2. A 300 mm wide, 40 mm thick plate is reduced to 30 mm thickness in one pass by hot rolling. Roll diameter is 200 mm and entrance speed is 16 m/min. Material constants C and m at the process temperature are given as 50 MPa and 0.05 respectively. Determine: a. The minimum friction coefficient required to make this operation possible, b. Assuming that the minimum level of friction is maintained, calculate the exit velocity of the plate by considering there is no widening, c. Calculate the force and power requirement to apply the pass.arrow_forward
- A hot/cold rolling setup is shown right. The operation first hot rolls a 3/8” thick plate, 12” wide (w), of6061 Aluminum, to an intermediate thickness, then finally through cold rolling, down to 1/4” thick plate.The friction factor μ is assumed to be constant at 0.15 for the hot roll, 0.12 for the cold rolling stage. Thefirst set of rolls operate at 50 RPM. Also ignore any width increase during rolling. CW=13% or .13 What is the plate thickness (mm) prior to the last rolls, t1, if the last set of rollers perform cold work reduction listed below at .13 or 13% Note that 9.52 mm is equal to 3/8 of an inch.arrow_forwardA 300mm thick slab is being cold rolled using roll of 600mm diameter.If the coefficient of friction is 0.08. Determine the maximum possible reduction.arrow_forwardA metal strip is to be rolled from an initial wrought thickness of 3.5 mm to a final rolled thickness of 2.5 mm in a single pass rolling mill having rolls of 250 mm diameter. The strip is 450 mm wide. The average coefficient of friction in the roll gap is 0.08. Taking plane strain low stress of 140 MPa, for the metal and assuming negligible spreading, the roll separating force is.....arrow_forward
- Question 1 solid cylindrical work piece is reduced in height by an open die forging process using flat dies on a mechanical press, powered by a 20 kW motor which operates at 35 strokes per minute with a stroke length of 160 mm. The work piece is 60 mm high and 100 mm in diameter and is to be reduced in height by 15%. The coefficient of friction during the operation is 0,18. Calculate the flow stress of work piece material if the press is set to operate at 90% of its maximum capacity.arrow_forward15.A 4.50-in-thick slab that is 9 in wide and 24 in long is to be reduced in a single pass in a two-high rolling mill to a thickness of 3.87 in. The roll rotates at a speed of 5.50 rev/min and has a radius of 17.0 in. The work material has a strength coefficient = 30,000 lb/in2 and a strain hardening exponent= 0.15. The roll force is 483,000 lb 583,000 lb 383,000 lb nonearrow_forwardThe thickness of a metallic sheet is reduced from an initial value of 16 mm to a final value of 10 mm in one single pass rolling with a pair of cylindrical rollers each of diameter of 400 mm. The bite angle in degree will bearrow_forward
- A strip with a cross section 120 mm x 6 mm is being rolled with 20% reduction area, using rolls of 400 mm diameter. The coefficient of friction is 0.1. Determine : The final strip thickness. (1) The angle of bite (M) Length of deformation zone (iv) Minimum possible thickness of sheet that can be produced in one passarrow_forwardA 300 mm thick slab is being cold rolled using roll of 600 mm diameter. If the coefficient of friction is 0.08, the maximum possible reduction is,arrow_forwardA cylindrical ingot with D0 = 50 mm and h0 = 40 mm is cold forged using an open die.The final height is 20 mm. The coefficient of form / friction between the die and the workpiece isconsider Kf = 1.10.The material from which the ingot is made has the following characteristics:K = 600 MPa and η = 0.12.Determine the force (F) on the operation:a) Force required at the moment of reaching the yield point (ℇ = 0.002)b) Force required when you have a height of h = 30 mmc) Force required when there is a final height of h = 20 mmd) Construct the graphs: Force vs Δh and effort vs Δharrow_forward
- Elements Of ElectromagneticsMechanical EngineeringISBN:9780190698614Author:Sadiku, Matthew N. O.Publisher:Oxford University PressMechanics of Materials (10th Edition)Mechanical EngineeringISBN:9780134319650Author:Russell C. HibbelerPublisher:PEARSONThermodynamics: An Engineering ApproachMechanical EngineeringISBN:9781259822674Author:Yunus A. Cengel Dr., Michael A. BolesPublisher:McGraw-Hill Education
- Control Systems EngineeringMechanical EngineeringISBN:9781118170519Author:Norman S. NisePublisher:WILEYMechanics of Materials (MindTap Course List)Mechanical EngineeringISBN:9781337093347Author:Barry J. Goodno, James M. GerePublisher:Cengage LearningEngineering Mechanics: StaticsMechanical EngineeringISBN:9781118807330Author:James L. Meriam, L. G. Kraige, J. N. BoltonPublisher:WILEY
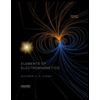
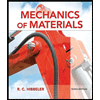
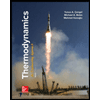
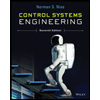
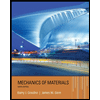
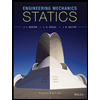