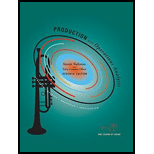
Concept explainers
a)
Interpretation: find the optimal order policy during 100week quarter based on the silver-meal heuristic and also calculate the total holding and ordering costs incurred over the 10-week period.
Concept Introduction: One of the forward method is Silver meal heuristic method. This method defined as planning the production in manufacturing and also within the minimum cost to determine the quantities of the production to achieve the requirement of the process. It is also called as dynamic-lot-size model.
b)
Interpretation: Determine the optimal policy and compare the total holding and ordering cost over the 10 weeks to the answer obtained in part (a).
Concept Introduction: Production Order Quantity(POQ) is determines that the volume of the optimal production for the every order of production for the goods with the independent demand.one of the model EOQ(Economic Order Quantity)refers that the goods are shipped in bulk of orders at a time.
c)
Interpretation: Determine the economical in general to face a smooth or a spiky demand pattern based on the results of part (a) and part (b)
Concept Introduction: Spiky demand refers to bulk orders of the product. Suppose when bulk orders occurs, the overall historical demand curve yields to have a rather spiky shape. This kind of shape refers that certain orders for the significant percentage of the total demand.

Want to see the full answer?
Check out a sample textbook solution
Chapter 8 Solutions
Production and Operations Analysis, Seventh Edition
- وبة واضافة هذه القيمة الى القيم Ex: Assign each job for each worker at minimum total Cost عمل لكل عامل وبأقل كلفة ممكنة obs الأعمال Workors العمال J1 J2 J3 J4 W₁ 15 13 14 12 W2 11 12 15 13 W3 13 12 10 11 W4 15 17 14 16arrow_forwardThe average completion time (flow time) for the sequence developed using the FCFS rule = 11.75 days (round your response to two decimal places). The percentage utilization for the sequence developed using the FCFS rule = 42.55 % (enter your response as a percentage rounded to two decimal places). b) Using the SPT (shortest processing time) decision rule for sequencing the jobs, the order is (to resolve a tie, use the order in which the jobs were received): An Alabama lumberyard has four jobs on order, as shown in the following table. Today is day 205 on the yard's schedule. In what sequence would the jobs be ranked according to the decision rules on the left: Job Due Date A 212 B 209 C 208 D 210 Duration (days) 6 3 3 8 Sequence 1 Job B 2 3 4 A D The average tardiness (job lateness) for the sequence developed using the SPT rule = 5.00 days (round your response to two decimal places). The average completion time (flow time) for the sequence developed using the SPT rule = 10.25 days…arrow_forwardWith the aid of examples, fully discuss any five (5) political tactics used in organisations.arrow_forward
- a. With the aid of examples, define discrimination. b. Fully discuss any four (4) types of discrimination in the workplacearrow_forwardRead the Following Extract and Answer the Questions that Follows:The word politics has a somewhat negative connotation. It suggests that someone is attempting touse means or to gain ends that are not sanctioned by the organisation. Political behaviour, as we’vedefined it is quite neutral. Similarly, power is not inherently negative. Whether a person viewspower and politics as unsavoury topics depends on several considerations, most important perhapsbeing where the individual stands on a specific issue in each situation. Nonetheless, most managersare reluctant to admit to political character of their own work settings.Discuss any Five (5) Political tactics you know.arrow_forwardDescribe current features of Cigna Accredo pharmacy own appraisal forms and compare the system used against the textbook’s description of desirable features of appraisal forms. What improvements would you recommend and why?arrow_forward
- Provide a recommendation of a combination of different methods of performance data that could be used to arrive at an overall score for each person being rated in cigna Accredo pharmacy. Explain the comprehensive system you have recommended and why you have chosen this combination of tools. Support your answer with research.arrow_forwardAlready got wrong answer Plz Don't use chatgptarrow_forwardThe RTY calculation for the following process steps would be: A ➡ ○ A.YA+YB+YC+YD OB. (YA)(YB)(YCYD) OC. ((YA+YB+YC+YD)/4)*4 ○ D. (1/YA)+(1/YB)+(1/YC)+YD B C Darrow_forward
- Can you guys help me with this? 1. What did you learn about the case, the concepts of transformational leadership; transactional leadership; Herzberg's Two Factors; Maslow's Hierarchy of needs theories that been applied through the case? Here is the case: Theranos (2003-2018):Overview: Theranos promised to revolutionize blood testing but was exposed formisleading claims about its technology, leading to its collapse 2. What did you learn about the case between Elon Musk and Twitter, the concepts of transformational leadership; transactional leadership; Herzberg's Two Factors Theory; Maslow's Hierarchy of needs theories that been applied through the case? 3. What did you learn about the case of Blockbuster's decline and their failure to adapt with digital streaming, the concepts of autocratic leadership; transactional leadership; Herzberg's Two Factors; Maslow's Hierarchy of needs theories that been applied through the case?arrow_forwardCan you guys help me with this? 1. What did you learn about the case, the concepts of transformational leadership; transactional leadership; Herzberg's Two Factors; and Maslow's Hierarchy of needs theories that have been applied through the case? Here is the case: The COVID-19 Pandemic Response (2020-Present): Overview: Global leaders had to navigate an unprecedented health crisis, balancingpublic health needs with economic pressures. 2. What did you learn about the case, the concepts of transformational leadership; transactional leadership; Herzberg's Two Factors Theory; and Maslow's Hierarchy of Needs theories that have been applied through the case? Here's the case: Google Glass (2013):Overview: Google launched its augmented reality glasses with high expectations, butprivacy concerns and limited functionality led to poor adoption 3. What did you learn about the case of Kodak's failure to keep up with digital photography, the concepts of autocratic leadership; transformational…arrow_forwardWith the above information do the following:1. Based on the From-To chart presented develop an ActivityRelationship Chart for this operation.2. Develop a Space-Relationship Diagram for this operation.3. Evaluate the actual layout using the “Distance Traveled byProduct” technique discussed in class (use rectilinear distance inall calculations).4. Develop two layout improvement alternatives.5. Evaluate alternatives using the “Distance Traveled by Product”technique discussed in class (use rectilinear distance in allcalculations).6. Make a layout recommendation based on alternatives evaluatedarrow_forward
- Practical Management ScienceOperations ManagementISBN:9781337406659Author:WINSTON, Wayne L.Publisher:Cengage,Operations ManagementOperations ManagementISBN:9781259667473Author:William J StevensonPublisher:McGraw-Hill EducationOperations and Supply Chain Management (Mcgraw-hi...Operations ManagementISBN:9781259666100Author:F. Robert Jacobs, Richard B ChasePublisher:McGraw-Hill Education
- Purchasing and Supply Chain ManagementOperations ManagementISBN:9781285869681Author:Robert M. Monczka, Robert B. Handfield, Larry C. Giunipero, James L. PattersonPublisher:Cengage LearningProduction and Operations Analysis, Seventh Editi...Operations ManagementISBN:9781478623069Author:Steven Nahmias, Tava Lennon OlsenPublisher:Waveland Press, Inc.
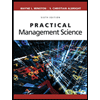
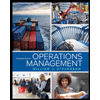
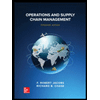
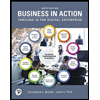
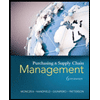
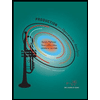