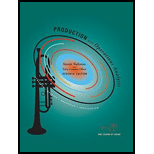
Production and Operations Analysis, Seventh Edition
7th Edition
ISBN: 9781478623069
Author: Steven Nahmias, Tava Lennon Olsen
Publisher: Waveland Press, Inc.
expand_more
expand_more
format_list_bulleted
Concept explainers
Question
Chapter 8, Problem 48AP
Summary Introduction
Interpretation: Determine the planned order releases for components F, G, and H, Assuming lot-for-lot production.
Concept Introduction: when the net requirements appearing for every period to the order of the quantity, the lot-for-lot method will be occur.it is one of the lot sizing method and also it is known as DOQ(Discrete order Quantity).
Expert Solution & Answer

Want to see the full answer?
Check out a sample textbook solution
Students have asked these similar questions
Part (A)
To control the inventory, organizations have three alternate approaches: Economic Order Quantity (EOQ).
Materials Requirements Planning (MRP) and Just-in-Time (JIT).
Discuss those three approaches identify the goal of each one? And how the organization can achieve such a goal?
Part (B)
Some threats could be happened in the production cycle, one of them is over or under production threat.
Discuss two problems and two controls related to this threat.
for the toolbar, press ALT F10 (PC) or ALT+FN+F10 (Mac).
1.
Speedy, Inc. is a company that produces automotive electrical components. A151 is a
common part for all its products. Consider the following gross requirements and inventory
data for A151 part:
Week
[Gross requirements
1
3
4
5
6
7
30
40
30
70
20
Inventory Data:
Lead time
Beginning inventory
Scheduled receipts
Holding cost
[Setup cost
1 week
40
$2.50/unit/week
$150
(i)
Based on the L4L lot-sizing rule, develop a Material Requirements Plan (MRP) for the next
8 weeks for A151 part.
Item: A151
Week
Lot size: L4L
3
4
6
8
Lead time: 1
Gross Requirements
Scheduled Receipts
On Hand Inventory
Net Requirements
Planned Order Receipts
Planned Order Releases
Exercise 2:
The demand per year (D) for product X is 12,100 units. The costs of placing an order (S) are $4.50. The unit cost (C) of the item is $25.00. The maintenance cost (H) per unit per year is 30% of the item's cost.
1. Use the economic order quantity (EOQ) model to determine:
*Optimal quantity to order* The expected number of orders*Optimal time between orders*The total annual cost of maintaining that optimal amountNOTE: Show calculations of how you arrived at each amount 2. Answer, what are the potential benefits of using EOQ analysis for inventory management? How can you help businesses strike a balance between inventory holding costs and ordering costs?
Chapter 8 Solutions
Production and Operations Analysis, Seventh Edition
Ch. 8.1 - Prob. 1PCh. 8.1 - Prob. 2PCh. 8.1 - Prob. 3PCh. 8.1 - Prob. 4PCh. 8.1 - Prob. 5PCh. 8.1 - Prob. 6PCh. 8.1 - Prob. 7PCh. 8.1 - Prob. 8PCh. 8.1 - Prob. 9PCh. 8.2 - Prob. 10P
Ch. 8.2 - Prob. 11PCh. 8.2 - Prob. 12PCh. 8.2 - Prob. 13PCh. 8.2 - Prob. 14PCh. 8.2 - Prob. 15PCh. 8.2 - Prob. 16PCh. 8.2 - Prob. 17PCh. 8.2 - Prob. 18PCh. 8.2 - Prob. 19PCh. 8.2 - Prob. 20PCh. 8.2 - Prob. 21PCh. 8.2 - Prob. 22PCh. 8.3 - Prob. 23PCh. 8.3 - Prob. 24PCh. 8.3 - Prob. 25PCh. 8.4 - Prob. 26PCh. 8.4 - Prob. 27PCh. 8.4 - Prob. 28PCh. 8.4 - Prob. 29PCh. 8.5 - Prob. 30PCh. 8.5 - Prob. 31PCh. 8.5 - Prob. 32PCh. 8.5 - Prob. 33PCh. 8.5 - Prob. 34PCh. 8.6 - Prob. 35PCh. 8.6 - Prob. 36PCh. 8.6 - Prob. 37PCh. 8.6 - Prob. 38PCh. 8.6 - Prob. 39PCh. 8.6 - Prob. 40PCh. 8 - Prob. 41APCh. 8 - Prob. 42APCh. 8 - Prob. 43APCh. 8 - Prob. 44APCh. 8 - Prob. 45APCh. 8 - Prob. 46APCh. 8 - Prob. 48APCh. 8 - Prob. 49APCh. 8 - Prob. 50APCh. 8 - Prob. 51AP
Knowledge Booster
Learn more about
Need a deep-dive on the concept behind this application? Look no further. Learn more about this topic, operations-management and related others by exploring similar questions and additional content below.Similar questions
- 12:16 +1 (876) 474-5168 10/31/20, 5:53 PM Exercise 2: ABC analysis Perform an ABC analysis on the foilowing set of products. Annual Item Demand Unit Cost A211 1200 $9 $90 $6 $150 $2000 $120 $90 B390 100 C003 4500 D100 400 E707 35 F660 250 G473 1000 H921 100 $75 LUILOANS ICESarrow_forwardITEMS 18 to 20 ARE BASED ON THE FOLLOWING INFORMATION: The following information pertains to Emy Manufacturing Corporation's Product X: Annual demand 33,750 units Annual cost to hold one unit of inventory P15 Setup cost (or the cost to initiate a production run) P500 Beginning inventory of product X 0 At present, the Company produces 2,250 units of Product X per production runt for a total of 15 production runs per year. The company is considering to use the EOQ model to determine the economic lot size and the number of production runs that will minimize the total inventory carrying cost and setup cost for Product X. At present, the company's total annual inventory costs is P 7,500. c. P24,375. P16,875. d. P22,500.arrow_forwardM13 SPR (4) SPM Axle (2) T889 SPM (8) The M13 Bill of Material is given here. The table below shows your current inventory levels of each item. Item Quantity Axle SPM 76 SPR 3. T889 8. How many additional units of SPM are needed to make 95 M13s?arrow_forward
- 2.)Birka Styles & Co is introducing a new line of beachwear for their retail stores. The manager needs to decide how many lots of the new beachwear to order for their stores. The marketing came up with a payoff table (see below) considering information about the price, projected sales level, and cost of inventory and ordering. DEMAND Order size Low Medium High 1 lot 12,000 15,000 15,000 2 lots 9,000 25,000 35,000 3 lots 6,000 35,000 60,000 If the owner of Birka Styles & Co is an optimist, how many lots should the manager order?arrow_forward2.)Birka Styles & Co is introducing a new line of beachwear for their retail stores. The manager needs to decide how many lots of the new beachwear to order for their stores. The marketing came up with a payoff table (see below) considering information about the price, projected sales level, and cost of inventory and ordering. DEMAND Order size Low Medium High 1 lot 12,000 15,000 15,000 2 lots 9,000 25,000 35,000 3 lots 6,000 35,000 60,000 A)If the owner of Birka Styles & Co is an optimist, how many lots should the manager order? B)If the owner of Birka Styles & Co is a pessimist, how many lots should the manager order? C)The owner wants to use minimax regret. How many lots should the manager order?arrow_forwarda. If demand for the new videotape recorder is expected to be constant with a rate of 20 units per month, what is the recommended order quantity for the videotape recorder? b. What are the estimated annual inventory holding and ordering costs associated with this product? c. How many orders will be placed per year? d. With 250 working days per year, what is the cycle time for this product?arrow_forward
- Production Quantity Model A manufacturing company operates 300 days a year with an annual demand for component C of 43,200 units. The fabrication department at the company is able to produce 800 units per day and send them over to assembly while production is in progress. If assembly sends a work order for 11,200 units of component C to fabrication, how long is the order receipt period? Given the order quantity in the previous question, what is the average inventory level for component C?arrow_forwardBest-Appliance makes high-powered industrial strength microwave oven and wants to create an MRP for their oven assembly with a minimum cost possible. Following table show gross requirements of their product for twelve weeks. Develop a Part Period Balancing (PPB) solution and calculate the total relevant costs for the plan. Week Gross requirements 1 30 Week Gross requirements On-hand at beginning of week 40 On-hand at end of week Order receipt Order release Total relevant cost for this plan is = $ 2 3 30 1 30 4 2 5 40 70 20 Also, for this plan the Holding cost = $2.50/unit/week; setup cost = $200; lead time = 1 week; beginning inventory = 40 units. Use the table below to develop a PPB solution for MRP (enter your responses as whole numbers). 3 30 6 7 8 4 5 40 (enter your response as a whole number). 6 ॥ 70 9 10 70 7 20 10 11 8 D 12 50 9 10 11 12 10 70 50arrow_forwarda. Determine an A-B-C classification for these items:Item Unit Cost Annual Volume (00)1 $100 252 80 303 15 604 50 105 11 706 60 857 10 60b. Find the EOQ given this information: D = 4,500 units/year, S = $36, and H = $10 per unit per year.c. Find the economic production quantity given this information.D = 18,000 units/year, S = $100, H = $40 per unit per year, p = 120 units per day,and u = 90 units/dayarrow_forward
- Determine an A-B-C classification for these items: Which items are A, B, and C - explain how you derive the answers? Use a table or excel spreadsheet to illustrate your work. Item Unit Cost Annual Volume (000)1 300 252 90 303 30 604 50 105 15 706 100 407 10 60 Hint:Determine the Annual Dollar Value (Unit Cost * Annual Volume) for each item and the sum of the individual Annual Dollar Values. Arrange the items in descending order based on Annual Dollar Values. Then, determine the percentage of items and the percentage of…arrow_forwardDemand for portable music players for joggers has caused Nancy Industries (Nancy) to grow almost 50 percent over the past year. The number of joggers continues to expand, so Nancy expects demand for music player to also expand, because, as yet, no safety laws have been passed to prevent joggers from wearing them. Demands for the players for last year was as follows : Month Demand (units) Jan 4200 Feb 4300 Mar 4000 Apr 4400 May 5000 Jun 4700 Jul 5300 Aug 4900 Sep 5400 Oct 5700 Nov 6300 Dec 6000 Question : From the choice of simple moving average, weighted moving average, exponential smoothing, and linear regression analysis, which forecasting technique would you consider the most accurate to Nancy Industries? Why?arrow_forwardSemans is a manufacturer that produces bracket assemblies. Demand for bracket assemblies (X) is 131 units. The following is in indented form: ITEM DESCRIPTION Bracket assembly Wall board USAGE 1 A 4 Hanger subassembly Hanger casting Ceramic knob Rivet head screw Metal tong Plastic cap E G 2 Below is a table indicating current inventory levels: Item Inventory A B E G 23 18 55 25 200 170 1,100 90 b. What are the net requirements of each item in the MPS? (Leave no cells blank be certain to enter "0" wherever requirec Item Net Requirements A F Nevtarrow_forward
arrow_back_ios
SEE MORE QUESTIONS
arrow_forward_ios
Recommended textbooks for you
- Practical Management ScienceOperations ManagementISBN:9781337406659Author:WINSTON, Wayne L.Publisher:Cengage,Operations ManagementOperations ManagementISBN:9781259667473Author:William J StevensonPublisher:McGraw-Hill EducationOperations and Supply Chain Management (Mcgraw-hi...Operations ManagementISBN:9781259666100Author:F. Robert Jacobs, Richard B ChasePublisher:McGraw-Hill Education
- Purchasing and Supply Chain ManagementOperations ManagementISBN:9781285869681Author:Robert M. Monczka, Robert B. Handfield, Larry C. Giunipero, James L. PattersonPublisher:Cengage LearningProduction and Operations Analysis, Seventh Editi...Operations ManagementISBN:9781478623069Author:Steven Nahmias, Tava Lennon OlsenPublisher:Waveland Press, Inc.
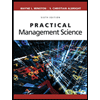
Practical Management Science
Operations Management
ISBN:9781337406659
Author:WINSTON, Wayne L.
Publisher:Cengage,
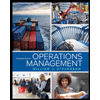
Operations Management
Operations Management
ISBN:9781259667473
Author:William J Stevenson
Publisher:McGraw-Hill Education
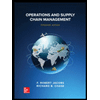
Operations and Supply Chain Management (Mcgraw-hi...
Operations Management
ISBN:9781259666100
Author:F. Robert Jacobs, Richard B Chase
Publisher:McGraw-Hill Education
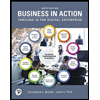
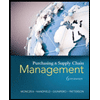
Purchasing and Supply Chain Management
Operations Management
ISBN:9781285869681
Author:Robert M. Monczka, Robert B. Handfield, Larry C. Giunipero, James L. Patterson
Publisher:Cengage Learning
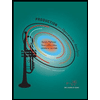
Production and Operations Analysis, Seventh Editi...
Operations Management
ISBN:9781478623069
Author:Steven Nahmias, Tava Lennon Olsen
Publisher:Waveland Press, Inc.
Inventory Management | Concepts, Examples and Solved Problems; Author: Dr. Bharatendra Rai;https://www.youtube.com/watch?v=2n9NLZTIlz8;License: Standard YouTube License, CC-BY