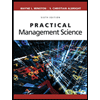
Concept explainers
ITEMS 18 to 20 ARE BASED ON THE FOLLOWING INFORMATION:
The following information pertains to Emy Manufacturing Corporation's Product X:
Annual demand 33,750 units
Annual cost to hold one unit of inventory P15
Setup cost (or the cost to initiate a production run) P500
Beginning inventory of product X 0
At present, the Company produces 2,250 units of Product X per production runt for a total of 15 production runs per year. The company is considering to use the EOQ model to determine the economic lot size and the number of production runs that will minimize the total inventory carrying cost and setup cost for Product X.
- At present, the company's total annual inventory costs is
- P 7,500. c. P24,375.
- P16,875. d. P22,500.

Step by stepSolved in 2 steps

- XYZ company has determined that the annual demand for type A material is 20,000 pounds. Salma, who works in her brother's factory, is in charge of purchasing. She estimates that it costs $15 every time an order is placed. This cost includes her wages, the cost of the forms used in placing the order, and so on. Furthermore, she estimates that the cost of carrying one pound in inventory for a year is 0.05 $. Assume that the demand is constant throughout the year. (Note: $ is a dollar sign) a) If we are going to use the EOQ inventory model, mention all the assumptions that are made to validate that model. b) How many pounds of type A material should Huda order (i.e. Q*) at a time if she wishes to minimize total inventory cost? c) How many orders per year would be placed? d) What would the annual ordering cost be? e) What would the average inventory be? f) What would the annual holding cost be? See equations below if needed: Annual Ordering cost Annual hdding: Number of orders placed per…arrow_forwardItem X is a standard item stocked in a company's inventory of spare parts. Each year, the firm uses about 2,000 units of Item X, which costs Php 1,000 per unit. Storage costs, which include insurance and cost of capital, amount to 18 percent of item unit cost. Placing an order for more of Item X costs Php 400. The company operates 360 days per year and Item X is received 9 days after placement of order.arrow_forwardGreen Gardens' owner has asked your advice about a possible problem at his business. Over the last 6 months the large-sized lawn and garden inventory (ie, tables, chairs, planters, etc.) has appeared to be short. The inventory records that employees use to determine what is on hand show that more inventory is available than can actually be located. This has cause frustration and mis-trust in the inventory records for the sales employees. The owner realizes that the problem is bigger than just frustrated employees. He is afraid that inventory is being stolen, a problem he didn't think possible given that these are large items that are not easily moved. Requirements: Provide the owner with two internal controls that he could implement to reduce the likelihood of theft of the lawn and garden inventory.arrow_forward
- The fixed quantity version of EOQ compares and contrasts with the fixed interval version. Where will each of the scenarios be used?arrow_forwardFuego Limited is a table-glass retailer located in Vancouver. The company purchases glasses from Anderson PLC. The details of the table glasses are as follows: The purchase price per glass – $3,000 Cost of an order - $500 The annual cost of carrying a glass - 2% of the purchase price Monthly Demand - 1,250 Units The company has been offered a discount of 1% on the price of a table glass if the lot size is 3,000 table glasses at a time. Required: i. Calculate the Economic Order Quantity. ii. Calculate the total inventory cost. iii. Draw a graph and discuss the behavior of the total inventory holding cost, total ordering cost, and total cost for the given scenario. iv. Advise whether the quantity discount offer can be accepted (Assume that the inventory carrying cost does not vary according to the discount policy)arrow_forwardProblem 7 Lynne Chappell manages the inventory of supplies in a large hospital. To determine which items should be closely monitored, Lynne decided to use the ABC classification schemeto group the items on the basis of their value. Asthe following table shows, she took a random sample of20 items and recorded the annual usage and unit cost ofeach. How should each item be classified?Inventory Item Unit cost(in U.S.dollars) AnnualUsageP21 $80 800A12 $400 70K43 $50 100S54 $60 90C25 $50 130D76 $30 170E27 $20 200F38 $300 90H19 $520 120Q10 $10 100R82 $20 80G65 $80 70L71 $220 200M94 $70 80V45 $15 60T62 $30 180I17 $20 80W22 $300 90O37 $700 85N88 $5 100arrow_forward
- Practical Management ScienceOperations ManagementISBN:9781337406659Author:WINSTON, Wayne L.Publisher:Cengage,Operations ManagementOperations ManagementISBN:9781259667473Author:William J StevensonPublisher:McGraw-Hill EducationOperations and Supply Chain Management (Mcgraw-hi...Operations ManagementISBN:9781259666100Author:F. Robert Jacobs, Richard B ChasePublisher:McGraw-Hill Education
- Purchasing and Supply Chain ManagementOperations ManagementISBN:9781285869681Author:Robert M. Monczka, Robert B. Handfield, Larry C. Giunipero, James L. PattersonPublisher:Cengage LearningProduction and Operations Analysis, Seventh Editi...Operations ManagementISBN:9781478623069Author:Steven Nahmias, Tava Lennon OlsenPublisher:Waveland Press, Inc.
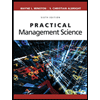
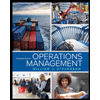
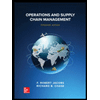
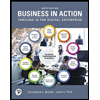
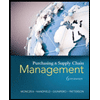
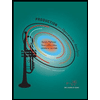