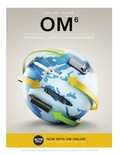
EBK OM
6th Edition
ISBN: 9781305888210
Author: Collier
Publisher: YUZU
expand_more
expand_more
format_list_bulleted
Concept explainers
Question
Chapter 8, Problem 13PA
(a)
Summary Introduction
Interpretation:Assembly line needs to be balanced based on given information.
Concept Introduction: Assembly line balancing is an important task that helps to reduce the cycle time by keeping the precedence relationships as it is.
(b)
Summary Introduction
Interpretation:Assembly line needs to be balanced based on given information.
Concept Introduction: Assembly line balancing is an important task that helps to reduce the cycle time by keeping the precedence relationships as it is.
Expert Solution & Answer

Want to see the full answer?
Check out a sample textbook solution
Students have asked these similar questions
Canine Kernels Company (CKC) manufactures two different types of dog chew toys (A and B, sold in 1,000-count boxes) that are manufactured and assembled on three different workstations (W, X, and Y) using a small-batch process (see the following figure). Batch setup times are negligible. The flowchart denotes the path each product follows through the manufacturing process, and each product’s price, demand per week, and processing times per unit are indicated as well. Purchased parts and raw materials consumed during production are represented by inverted triangles. CKC can make and sell up to the limit of its demand per week; no penalties are incurred for not being able to meet all the demand. Each workstation is staffed by a worker who is dedicated to working on that workstation alone and is paid $6 per hour. Total labor costs per week are fixed. Variable overhead costs are $3,500/week. The plant operates one 8-hour shift per day or 40 hours/week.
The senior management at Canine…
An assembly line with 17 tasks is to be balanced. The longest task is 2.4 minutes, and the totaltime for all tasks is 18 minutes. The line will operate for 450 minutes per day.a. What are the minimum and maximum cycle times?
A.J.’s Wildlife Emporium manufactures two unique birdfeed-ers (Deluxe and Super Duper) that are manufactured andassembled in up to three different workstations (X, Y, Z) us-ing a small batch process. Each of the products is producedaccording to the flowchart in Figure 5.14. Additionally, theflowchart indicates each product’s price, weekly demand,and processing times per unit. Batch setup times are neg-ligible. A.J. can make and sell up to the limit of its weeklydemand and there are no penalties for not being able to meetall of the demand. Each workstation is staffed by a workerwho is dedicated to work on that workstation alone and ispaid $16 per hour. The plant operates 40 hours per week,with no overtime. Overhead costs are $2,000 per week. Basedon the information provided, as well as the information con-tained in the flowchart, answer the following questions.
a. Using the traditional method, which bases decisionssolely on a product’s contribution to profits and over-head, what is the…
Knowledge Booster
Learn more about
Need a deep-dive on the concept behind this application? Look no further. Learn more about this topic, operations-management and related others by exploring similar questions and additional content below.Similar questions
- A.J.’s Wildlife Emporium manufactures two unique birdfeed-ers (Deluxe and Super Duper) that are manufactured andassembled in up to three different workstations (X, Y, Z) us-ing a small batch process. Each of the products is producedaccording to the flowchart in Figure 5.14. Additionally, theflowchart indicates each product’s price, weekly demand,and processing times per unit. Batch setup times are neg-ligible. A.J. can make and sell up to the limit of its weeklydemand and there are no penalties for not being able to meetall of the demand. Each workstation is staffed by a workerwho is dedicated to work on that workstation alone and ispaid $16 per hour. The plant operates 40 hours per week,with no overtime. Overhead costs are $2,000 per week. Basedon the information provided, as well as the information con-tained in the flowchart, answer the following questions.a. Using the traditional method, which bases decisionssolely on a product’s contribution to profits and over-head, what is the…arrow_forwarda. what is the bottleneck of this process? b. what is the hourly capacity of the process?arrow_forwardPositively Rivet Inc. is a small machine shop that produces sheet metal products. It had one line dedicated to the manufacture of light-duty vent hood shells, but because of strong demand it recently added a second line. The new line makes use of higher-capacity automated equipment but consists of the same basic four processes as the old line. In addition, the new line makes use of one machine per workstation, while the old line has parallel machines at the workstations. The processes, along with their machine rates, number of machines per station, and average times for a lone job to go through a station (i.e., not including queue time), are given for each line in the following table: Process Old Line New Line Rate per Machine (parts/hour) # Machines per Station Time (minute) Rate per Machine (parts/hour) # Machines per Station Time (minute) Punching 15 4 4.0 120 1 0.50 Braking 12 4 5.0 120 1 0.50 Assembly 20 2 3.0 125…arrow_forward
- Canine Kernels Company (CKC) manufactures two different types of dog chew toys (A and B, sold in 1,000-count boxes) that are manufactured and assembled on three different workstations (W, X, and Y) using a small-batch process (see Figure). Batch setup times are negligible. The flowchart denotes the path each product follows through the manufacturing process, and each product’s price, demand per week, and processing times per unit are indicated as well. Purchased parts and raw materials consumed during production are represented by inverted triangles. CKC can make and sell up to the limit of its demand per week; no penalties are incurred for not being able to meet all the demand. Each workstation is staffed by a worker who is dedicated to work on that workstation alone, and is paid $6 per hour. Total labor costs per week are fixed. Variable overhead costs are $3,500/week. The plant operates one 8-hour shift per day, or 40 hours/week. Which of the three workstations, W, X, or Y, has the…arrow_forwardThree departments- milling (M), drilling (D), andsawing (S)- are assigned to three work areas in Victor Berardis'smachine shop in Kent, Ohio. The number of workpieces movedper day and the distances between the centers of the work areas,in feet, follow. Pieces Moved between Work Areas Each Day lt costs $2 to move I workpiece I foot.What is the cost?arrow_forwardConsider a four-step serial process with the number of workers at each step and processing times given in the following table. Process Step 1 2 3 4 Number of Workers 1 5 4 5 Time per Customer (in Minutes) Assuming that the process starts out empty and is worker-paced, how long will it take (in minutes) to serve 20 customers? (Round to nearest minute.) minutes to serve 20 customers 8 19 13 5arrow_forward
- A production process at Kenneth Day Manufacturing is shown in the figure below. The drilling operation occurs separately from, and simultaneously with, the sawing and sanding, which are independent sequential operations. A product needs to go through only one of the three assembly operations (the operations are in parallel). 2.1 units/hr Sawing 5 units/hr Sanding Drilling 5 units/hr Welding 2.5 units/hr a) Sawing is the bottleneck. b) The bottleneck time is 28.57 minutes per unit (round your response to two decimal places). c) The throughput time of the overall system is 89.58 minutes (round your response to two decimal places). Assembly Q 0.8 units/hr Assembly 0.8 units/hr Assembly 0.8 units/hrarrow_forwardThe route shcet for a part is as follows: A - F - E -D - C – B – A - F Two hundred picces will flow through from the first machine A to the final machine F based on the given sequencec of operations. A unit load size of 50 is initially specified at the first machine. However, duc to lot sizing decisions, the unit load size is doubled after processing on machine D. If one vehicle (c.g., lift truck) is used to transport the unit loads from machinc to machine, determine the total number of trips that the vchicle has to make, assuming that the vehicle capacity is one unit load.arrow_forwardKiko Teddy Bear is a manufacturer of stuffed teddy bears. Kiko would like to be able to produce 40 teddy bears per hour on its assembly line. The following information will assist in answering the questions that follow: Task Information for Kiko Teddy Bear What is the maximum possible output of the line? What is the theoretical minimum number of workstations using the cycle time computed in” b “above Assign tasks to workstations using the cycle time in “b” above.arrow_forward
- Balancing a production line includes the following tasks, EXCEPT: O Finding a cycle time in which each workstation can complete its tasks Take into account precedence relationships among tasks Identify the task with the longest operation time O Calculate the number of workstations that completes the job in the minimum amount of timearrow_forwardCanine Kennels Company (CKC) manufactures two different types of dog chew toys (A and B, sold in 1,000-count boxes) that are manufactured and assembled on three different workstations (W, X, and Y) using a small-batch process (see the figure below). Batch setup times are negligible. The flowchart denotes the path each product follows through the manufacturing process, and each product's price, demand per week, and processing times per unit are indicated as well. Purchased parts and raw materials consumed during production are represented by inverted triangles. CKC can make and sell up to the limit of its demand per week; no penalties are incurred for not being able to meet all the demand. Each workstation is staffed by a worker who is dedicated to work on that workstation alone and is paid $10 per hour. Total labor costs per week are fixed. Variable overhead costs are $3,500/week. The plant operates one 8-hour shift per day, or 40 hours/week. Product A $4 Raw materials Product B $7 Raw…arrow_forwardCanine Kennels Company (CKC) manufactures two different types of dog chew toys (A and B, sold in 1,000-count boxes) that are manufactured and assembled on three different workstations (W, X, and Y) using a small-batch process (see the figure below). Batch setup times are negligible. The flowchart denotes the path each product follows through the manufacturing process, and each product's price, demand per week, and processing times per unit are indicated as well. Purchased parts and raw materials consumed during production are represented by inverted triangles. CKC can make and sell up to the limit of its demand per week; no penalties are incurred for not being able to meet all the demand. Each workstation is staffed by a worker who is dedicated to working on that workstation alone and is paid $6 per hour. Total labor costs per week are fixed. Variable overhead costs are $3,500/week. The plant operates one 8-hour shift per day or 40 hours/week. Which of the three workstations, W, X, or…arrow_forward
arrow_back_ios
SEE MORE QUESTIONS
arrow_forward_ios
Recommended textbooks for you
- Practical Management ScienceOperations ManagementISBN:9781337406659Author:WINSTON, Wayne L.Publisher:Cengage,
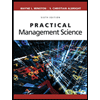
Practical Management Science
Operations Management
ISBN:9781337406659
Author:WINSTON, Wayne L.
Publisher:Cengage,
Inventory Management | Concepts, Examples and Solved Problems; Author: Dr. Bharatendra Rai;https://www.youtube.com/watch?v=2n9NLZTIlz8;License: Standard YouTube License, CC-BY