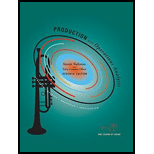
Production and Operations Analysis, Seventh Edition
7th Edition
ISBN: 9781478623069
Author: Steven Nahmias, Tava Lennon Olsen
Publisher: Waveland Press, Inc.
expand_more
expand_more
format_list_bulleted
Concept explainers
Question
Chapter 9.8, Problem 22P
Summary Introduction
Interpretation: The sequence required to be implemented to minimize the total expected time that is required for fittings and styling is to be determined.
Concept Introduction:
Optimal sequence: It is supposed to be sequences or series of jobs that have to take place to minimize the idle time and at the same time all the jobs are completed.
Expert Solution & Answer

Want to see the full answer?
Check out a sample textbook solution
Students have asked these similar questions
Joan has a small design and tailoring shop making custom outfits for women. She has two employees. Each employee only begins working on a dress when a customer order has
been received and then she makes the dress from beginning to end. The average production time of a dress is 1.8 days, with a standard deviation of 2.1 days. Historically, Joan has
been receiving orders with interarrival times of one day on average. The interarrival times of orders have a coefficient of variation of one.
(Carry at least 4 decimal places in all intermediate calculations. Round your final answer to 2 decimal places.)
What is the expected waiting time, in days, between when an order is received and when production begins on the dress?
A. 9.12 days B. 6.50 days C. 1.23 days D.3.41 days
An average of 40 jobs per day arrive at a factory. Thetime between arrivals of jobs is exponentially distributed.The factory can process an average of 42 jobs per day, andthe time to process a job is exponentially distributed.a What is the probability that exactly 180 jobs arriveat the factory during a 5-day period?b On the average, how long does it take before a jobis completed (measured from the time the job arrives atthe factory)?c What fraction of the time is the factory idle?
d What is the probability that work on a job will be-gin within 2 days of its arrival at the factory?
During an eight-hour shift, 750 non-defective parts are desired as a result of a manufacturing operation. The default operation time is 15 minutes. As the operators of machine are inexperienced, the actual time they take to perform the operation is 20 minutes, and, on average, a fifth of the parts that start to be manufactured are lost. Assuming that each one of the machines used in this operation will not be available for one hour in each shift, determine the number of machines needed.
Chapter 9 Solutions
Production and Operations Analysis, Seventh Edition
Ch. 9.5 - Prob. 1PCh. 9.5 - Prob. 2PCh. 9.5 - Prob. 3PCh. 9.5 - Prob. 4PCh. 9.5 - Prob. 5PCh. 9.6 - Prob. 6PCh. 9.6 - Prob. 7PCh. 9.6 - Prob. 8PCh. 9.6 - Prob. 9PCh. 9.6 - Prob. 10P
Ch. 9.7 - Prob. 11PCh. 9.7 - Prob. 12PCh. 9.7 - Prob. 13PCh. 9.7 - Prob. 14PCh. 9.7 - Prob. 15PCh. 9.7 - Prob. 16PCh. 9.7 - Prob. 17PCh. 9.8 - Prob. 18PCh. 9.8 - Prob. 19PCh. 9.8 - Prob. 20PCh. 9.8 - Prob. 21PCh. 9.8 - Prob. 22PCh. 9.9 - Prob. 23PCh. 9.9 - Prob. 24PCh. 9.9 - Prob. 25PCh. 9.10 - Prob. 27PCh. 9.10 - Prob. 28PCh. 9.10 - Prob. 29PCh. 9 - Prob. 30APCh. 9 - Prob. 31APCh. 9 - Prob. 32APCh. 9 - Prob. 33APCh. 9 - Prob. 34APCh. 9 - Prob. 35APCh. 9 - Prob. 36APCh. 9 - Prob. 37APCh. 9 - Prob. 38APCh. 9 - Prob. 39APCh. 9 - Prob. 40APCh. 9 - Prob. 41APCh. 9 - Prob. 42APCh. 9 - Prob. 43APCh. 9 - Prob. 44APCh. 9 - Prob. 45APCh. 9 - Prob. 46APCh. 9 - Prob. 47AP
Knowledge Booster
Learn more about
Need a deep-dive on the concept behind this application? Look no further. Learn more about this topic, operations-management and related others by exploring similar questions and additional content below.Similar questions
- Solve the question below using the attached excel templates with formulas for renting both slow and fast copies (labeled in the excel tabs). Question: The Decision Sciences Department is trying to determine whether to rent a slow or a fast copier. The department believes that an employee’s time is worth $15 per hour. The slow copier rents for $4 per hour, and it takes an employee an average of 10 minutes to complete copying. The fast copier rents for $15 per hour, and it takes an employee an average of six minutes to complete copying. On average, four employees per hour need to use the copying machine. (Assume the copying times and interarrival times to the copying machine are exponentially distributed.) Which machine should the department rent to minimize expected total cost per hour?arrow_forwardSuppose a bank has three tellers that are each busy 80 percent of the time. Estimatethe probability of delay for a randomly arriving customer.arrow_forwardFor a bank branch simulation, the assumptions on customer queueing and service facility in the branch, customer waiting in one line or many lines, and served according to first come first serve rule or priority rule are examples for structural assumptions. Select one: True Falsearrow_forward
- Problem: A class contains 30 students, Ten are Female (F) and Caviteno (C), 12 are male (M) and Caviteno; 6 are female and non-Caviteno; 2 are male and non-Caviteno A name is randomly selected from the class roster and it is female. What is the probability that the student is a Caviteno?arrow_forwardThe Acme Machine Shop has five machines that periodically break down and require service.The average time between breakdowns is 4 days, distributed according to an exponential distribution.The average time to repair a machine is 1 day, distributed according to an exponentialdistribution. One mechanic repairs the machines in the order in which they break down. Determine the probability that the mechanic is idle.arrow_forwardFive jobs are waiting for processing through two work centers. Their processing time (in minutes) at each work center is contained in the table below. Each job requires work center Sigma before work center Delta. According to Johnson's rule, what sequence of jobs will minimize the completion time for all jobs? Job Sigma Delta R 20 10 S 25 30 T 30 20 U 35 35 V 15 25 Part 2 A. V−S−U−T−R B. V−R−U−S−T C. R−V−T−S−U D. S−U−T−V−R E. R−S−T−U−Varrow_forward
- One possible solution method for the machine-to job assignment problem is the following heuristic procedure. Assign the machine to job 1 that completes job 1 quickest. Then assign the machine to job 2 that, among all machines that still have some capacity, completes job 2 quickest. Keep going until a machine has been assigned to all jobs. Does this heuristic procedure yield the optimal solution for this problem? If it does, see whether you can change the job times so that the heuristic does not yield the optimal solution.arrow_forwardestablish the significance of random numbers in Monte Carlo simulations.arrow_forwardAt Trojans Urgent Care Clinic, there is one triage nurse, 5 nurse practitioners, and 3 doctors. Patients arrive to the triage nurse, and the triage nurse decides if their case can be handled by a nurse practitioner or must be handled by a doctor. The triage nurse can detect patients whose case can be handled by a nurse practitioner in on average 5 minutes with standard deviation 1 minute; however, the triage nurse spends on average 10 minutes with standard deviation 3 minutes with patients whose case is eventually handled by a doctor. Patients seeing a nurse practitioner spend on average 30 minutes with standard deviation 8 minutes with the nurse practitioner, and patients seeing a doctor spend on average 45 minutes with standard deviation 10 minutes with the doctor. 60% of arriving patients are cared for by a nurse practitioner and 40% of arriving patients are cared for by a doctor. Patients leave the Urgent Care Clinic after seeing either the nurse practitioner or the doctor. a) If 8…arrow_forward
- Chapter 5. (M/M/s/K Model). Leia is responsible for 12 computers in the IT offices in a small business called DataWish. Each computer runs on an average for 4 weeks and requires an average of ½ or 0.5 weeks to get reset by Leia before it can start up again. If we assign the Poisson distribution to the “arrival” of each computer for service and an exponential distribution to the actual service provided, answer the following questions: a. The arrival rate would be units per week and the service rate would be units per week. b. Calculate the following operating characteristics for the M/M/s/K system: Utilization Factor (ρ) % Performance Measures P0 (probability that sytem is empty) % L (average units in system) units Lq (average units waiting in queue) units W (average time in the system) weeks Wq (average time in the queue) weeks c. If we assign a cost of waiting as $750 per week per computer and $800 per week of…arrow_forwardChapter 5. (M/M/s/K Model). Leia is responsible for 8 computers in the IT offices in a small business called DataWish. Each computer runs on an average for 3 weeks and requires an average of ½ or 0.5 weeks to get reset by Leia before it can start up again. If we assign the Poisson distribution to the "arrival" of each computer for service and an exponential distribution to the actual service provided, answer the following questions: a. The arrival rate would be units per week and the service rate would be units per week. b. Calculate the following operating characteristics for the M/M/s/K system: Utilization Factor (p) % Performance Measures PO (probability that sytem is empty) L (average units in units system) La (average units waiting in queue) units W (average time in the weeks system) Wq (average time in the queue) weeks c. If we assign a cost of waiting as $500 per week per computer and $800 per week of hiring Leia, what is the Total Time Cost per week cost of servicing the…arrow_forwardChapter 5. (M/M/s/K Model). Leia is responsible for 8 computers in the IT offices in a small business called DataWish. Each computer runs on an average for 3 weeks and requires an average of ½ or 0.5 weeks to get reset by Leia before it can start up again. If we assign the Poisson distribution to the "arrival" of each computer for service and an exponential distribution to the actual service provided, answer the following questions: a. The arrival rate would bel units per week and the service rate would be units per week. b. Calculate the following operating characteristics for the M/M/s/K system: Utilization Factor (p) Performance Measures c. If we assign a cost of waiting as $500 per week per computer and $800 per week of hiring Leia, what is the Total Time Cost per week cost of servicing the machines? PO (probability that sytem is empty) % dollars L (average units in system) units d. If DataWish decides to hire another individual to help Leia, what would the new Total Time Cost per…arrow_forward
arrow_back_ios
SEE MORE QUESTIONS
arrow_forward_ios
Recommended textbooks for you
- Practical Management ScienceOperations ManagementISBN:9781337406659Author:WINSTON, Wayne L.Publisher:Cengage,
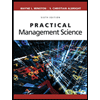
Practical Management Science
Operations Management
ISBN:9781337406659
Author:WINSTON, Wayne L.
Publisher:Cengage,