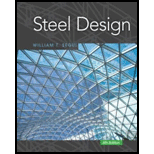
(a)
If the compression member is adequate to support the loads using LRFD.

Answer to Problem 4.7.3P
Explanation of Solution
Given information:
Concept used:
Calculation:
From AISC manual, the radius of gyration for the given material is 5.34 in. and 3.05 in.
Taking the higher value of slenderness ratio is 62.95.
Check:
Use AISC equation 3-2.
From AISC manual, the gross area for the given material is
Check for slender:
The flange is non-slender.
The web is non-slender.
Hence, the section is safe.
Conclusion:
The section
(b)
The compression member is adequate to support the loads using ASD.

Answer to Problem 4.7.3P
Explanation of Solution
Given information:
Concept used:
Calculation:
From AISC manual, the radius of gyration for the given material is 5.34 in. and 3.05 in.
Taking the higher value of slenderness ratio is 62.95.
Check:
Use AISC equation 3-2.
From AISC manual, the gross area for the given material is
Check for slender
The flange is non-slender.
The web is non-slender.
Hence, the section is safe.
Conclusion:
The section
Want to see more full solutions like this?
Chapter 4 Solutions
Steel Design (Activate Learning with these NEW titles from Engineering!)
- Please do not use design aid - R. Show step by step and every formular usedarrow_forwardFollowing is the variation of the field standard penetration number (№60) in a sand deposit: Depth (m) N60 1.5 6 3 8 4.5 9 6 8 7.5 9 13 14 The groundwater table is located at a depth of 6 m. Given: the dry unit weight of sand from 0 to a depth of 6 m is 16 kN/m³, and the saturated unit weight of sand for depth 6 to 12 m is 18.2 kN/m². Use the relationship given in the equation CN = 1 σo/Pa 0.5 to calculate the corrected penetration numbers. (Round your answers to the nearest whole number.) Depth (m) Neo (N1)00 1.5 3 6 8 4.5 9 6 7.5 9 14 8 13arrow_forward1,5 m 1,5 m A 1,6 KN F 0,8 m E 0,8 marrow_forward
- 5.85 The flow pattern through the pipe contraction is as shown, and the Q of water is 60 cfs. For d = 2 ft and D = 6 ft, what is the pressure at point B if the pressure at point C is 3200 psf? D E Problem 5.85 20° Barrow_forwardPlease solve problem 8.13 (the highlighted question).arrow_forwardThe following figure shows a vertical retaining wall with a granular backfill: 100.0 50.0 40.0 30.0 20.0 10.0- 5.0- 4.0 3.0- 2.0- = +1 0.8 0.6 0.4 0.2 0.0 -0.2 -0.4 -0.6 -0.8 -0.9 1.0- 0 10 20 30 40 45 ' (deg) (a) Figure Caquot and Kerisel's solution for K 3 Let H = 4m, a = 17.5°, y = 17.5 kN/m³, ' = 35°, and 8' = 10°. For given values of ' and 8', R' = 0.53. Based on Caquot and Kerisel's solution, what would be the passive force per meter length of the wall? (Enter your answer to two significant figures.) Pp= kN/marrow_forward
- The dam presented below is 180 m long (in the direction perpendicular to the plane of thecross-section). For the water elevations given on the drawing:a) Construct the flow net (minimum number of equipotential lines should be 10),b) Calculate the rate of seepage for the entire dam,c) Find the total uplift force on the dam (ignore barriers), andd) Estimate the hydraulic gradient at points A, B, and Darrow_forwardThe influence line for moment at B for the beam shown is A -6 m- B a. O at A, 6 at B, and 15 at C b. 1 at A, 1 at B, and 1 at C c. O at A, 0 at B, and -9 at C d. O at A, 1 at B, and 1 and C -9 m-arrow_forwardConsider the following figure: H/3 Pa Given: H = 7 m, y = 13 kN/m³, ø′ = 25°, c′ = 12 kN/m², and a = 10°. For given values, K₁ = 0.296. Calculate the Rankine active force per unit length of the wall after the occurrence of the tensile crack. (Enter your answer to three significant figures.) Pa = kN/marrow_forward
- Wall movement to left 45+ '/2 45 + 6'/2 Rotation of wall about this point A vertical retaining wall shown in the figure above is 7 m high with a horizontal backfill. For the backfill, assume that y = 14.5 kN/m³, ' = 26°, and c′ = 18 kN/m². Determine the Rankine active force per unit length of the wall after the occurrence of the tensile crack. (Enter your answer to three significant figures.) Pa = kN/marrow_forwardConsider the following figure: 0.6 "d 0.5 k₁ = 0 0.4 03 =0 kh = 0.2 0.3 0.025 0.2 0.05 0.1 0.1 0.2 0 -0.1 ↓ 0 5 10 15 20 25 30 35 40 45 ' (deg) For a retaining wall with a vertical back and horizontal backfill with a c'-' soil, the following are given: H = 10 ft Y = 111 lb/ft³ ' = 25° kh = 0.2 k₁ = 0 c = 113 lb/ft² Determine the magnitude of active force Pae on the wall. (Enter your answer to two significant figures.) Pae = lb/ftarrow_forwardA 13.0 ft high vertical wall retains an overconsolidated soil where OCR = 1.5, c' = 0, and ' magnitude and the location of the horizontal load on the wall, assuming the at-rest condition. Use Ysat (Enter your answers to three significant figures.) 33°. If the entire soil behind the wall is submerged with the water level at the ground surface, determine the 127 lb/ft³. Activity Frame P₁ = lb/ft Height above the bottom of the wall = O Icon Kov ftarrow_forward
- Steel Design (Activate Learning with these NEW ti...Civil EngineeringISBN:9781337094740Author:Segui, William T.Publisher:Cengage Learning
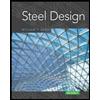