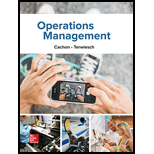
Concept explainers
The Tesla Model S, one of the most sought-after luxury cars, is produced in Tesla’s Freemont factory in California. The production process can be broken up into the following subprocesses.
Stamping: In the stamping process, coils of aluminum are unwound, cut into level pieces of sheet metal, and then inserted into stamping presses that shape the metal according to the geometry of the Model S. The presses can shape a sheet of metal in roughly 6 seconds.
Subassembly: The various pieces of metal are put together using a combination of joining techniques, including welding and adhesion. This creates the body of the vehicle.
Paint: The body of the vehicle is then moved to the paint shop. After painting is completed, the body moves through a 350° oven to cure the paint, followed by a sanding operation that ensures a clean surface.
General assembly: After painting, the vehicle body is moved to the final assembly area. Here, assembly workers and assembly robots insert the various subassemblies, such as the wiring, the dash board, the power train and the motor, the battery pack, and the seats.
Quality testing: Before being shipped to the customer, the now-assembled car is tested for its quality. It is driven on a rolling road, a test station that is basically a treadmill for cars that mimics driving on real streets.
Overall, the process is equipped with 160 robots and 3000 employees. The process produces some 500 vehicles each week. It takes a car about 3–5 days to move from the beginning of the process to the end.
Imagine you could take a tour of the Tesla plant. To prepare for this tour, draw a simple process flow diagram of the operation.
How many cars are you likely to encounter as work in progress inventory?

Want to see the full answer?
Check out a sample textbook solution
Chapter 3 Solutions
Operations Management
Additional Business Textbook Solutions
Operations Management: Processes and Supply Chains (12th Edition) (What's New in Operations Management)
Operations Management, Binder Ready Version: An Integrated Approach
Operations Management: Processes and Supply Chains (11th Edition)
Operations and Supply Chain Management 9th edition
Operations Management: Sustainability and Supply Chain Management (12th Edition)
Business in Action
- Frito-Lay, the massive Dallas-based subsidiary of PepsiCo, has 38 plants and 48,000 employees in North America. Seven of Frito-Lay’s 41 brands exceed $1 billion in sales. The production process at Frito-Lay is designed for large volumes and small variety, using expensive special-purpose equipment, and with swift movement of material through the facility. Product-focused facilities, such as Frito-Lay’s, typically have high capital costs, tight schedules, and rapid processing. Frito- Lay’s facilities are located regionally to aid in the rapid delivery of products because freshness is a critical issue. Sanitary issues and necessarily fast processing of products put a premium on an efficient layout. Production lines are designed for balanced throughput and high utilization. Cross-trained workers, who handle a variety of production lines, have promotion paths identified for their particular skill set. The supply chain is integral to success in the food industry; vendors must be chosen with…arrow_forwardFrito-Lay, the massive Dallas-based subsidiary of PepsiCo, has 38 plants and 48,000 employees in North America. Seven of Frito-Lay’s 41 brands exceed $1 billion in sales. The production process at Frito-Lay is designed for large volumes and small variety, using expensive special-purpose equipment, and with swift movement of material through the facility. Product-focused facilities, such as Frito-Lay’s, typically have high capital costs, tight schedules, and rapid processing. Frito- Lay’s facilities are located regionally to aid in the rapid delivery of products because freshness is a critical issue. Sanitary issues and necessarily fast processing of products put a premium on an efficient layout. Production lines are designed for balanced throughput and high utilization. Cross-trained workers, who handle a variety of production lines, have promotion paths identified for their particular skill set. The supply chain is integral to success in the food industry; vendors must be chosen with…arrow_forwardA catalog order-filling process can be described as follows:12 Telephone orders are taken over a 12-hour period each day. Orders are collected from each person at the end of the day and checked for errors by the supervisor of the phone department, usually the following morning. The supervisor does not send each one-day batch of orders to the data processing department until after 1:00 p.m. In the next step—data processing—orders are invoiced in the one-day batches. Then they are printed and matched back to the original orders. At this point, if the order is from a new customer, it is sent to the person who did the customer verification and setup of new customer accounts. This process must be completed before the order can be invoiced. The next step—order verification and proofreading—occurs after invoicing is completed. The orders, with invoices attached, are given to a person who verifies that all required information is present and correct to permit typesetting. If the verifier has…arrow_forward
- . Aquatica makes underwater camera housings for divers. The process begins with a solid rectangular block of aluminum that is used to make a single housing. A computer numerically controlled (CNC) machine drills into the block to make the metal “frame” of the housing. Each block requires 15 minutes of drilling. The frame is then chemically treated in a series of baths. There is ample capacity in the treating stage. Finally, a worker must manually attach the various buttons and components to the metal housing. This assembly takes 120 minutes per housing per worker and Aquatica has 6 workers trained to do this task. The CNC machine requires a 30-minute setup time before the production of a batch can begin. a. If the CNC machine produces 14 housings between setups, what would be its capacity (in housings per hour)? b. Assuming the process is supply-constrained, what is the utilization (as a number between 0 and 1) of the CNC machine if it operates in batches of 14 housings? c. Assuming…arrow_forwardThese four elements make up a machine cycle, often known as a process loop. Which parts of machine cycles do people value the most? Do you have to worry about the various parts of a machine cycle needing replacement? Is there a way to solve the problem of switching between modules by adding another one?arrow_forwardSuppose a final assembly is produced by assembling two components. THE The first component, A, is produced internally and goes through three process steps, which are stamping, forging and machining, with scrap estimates of 10%, 15% and 25%, respectively. For every three produced units of component A, two are used in the final assembly and one is separate to meet spare parts needs. The second component, B, which is used exclusively in final assembly, is purchased from a supplier external and inspected on arrival; 2% do not pass inspection. A unit of the component purchased is required for each final assembly. The final assembly process produces 5% of scraps. Spare parts demands for component A and final Su assembly match to 1,000 and 5,000 units, respectively. How many input units are needed for produce component A, and how many units of component B should the firm buy?arrow_forward
- The diagram below represents a process where two components are made at stations A1 and A2 (one component is made at A1 and the other at A2). These components are then assembled at station B and moved through the rest of the process, where some additional work is completed at stations C, D, and E. Assume that one and only one person is allowed at each station. Assume that the times given below for each station represent the amount of work that needs to be done at that station by that person, with no processing time variation. Assume that inventory is not allowed to build in the system. Al 0.3 min. A2 0.4 min. B 0.75 min. D 0.65 min. 0.60 min. E 0.55 min. What is the average hourly output of the process when it is in normal operation? Average hourly output unitsarrow_forwardThe diagram below represents a process where two components are made at stations A1 and A2 (one component is made at A1 and the other at A2). These components are then assembled at station B and moved through the rest of the process, where some additional work is completed at stations C, D, and E. Assume that one and only one person is allowed at each station. Assume that the times given below for each station represent the amount of work that needs to be done at that station by that person, with no processing time variation. Assume that inventory is not allowed to build in the system. A1 0.30 min. B 0.75 min. 0.65 min. 0.90 min. 0.55 min. A2 0.40 min. What is the average hourly output of the process when it is in normal operation? (Round your answer to the nearest whole number.) Average hourly output unitsarrow_forwardIn Continuous manufacturing system, we need: Highly skilled labours and special machine tools General purpose machines and unskilled laborers. Unskilled labours and semi automatic machines Special purpose machines and Skilled laboursarrow_forward
- HP Computer's primary consumer business takes orders from customers for specific configurations of desktop and laptop computers. Customers must select from a certain model line of computer and choose from available parts, but within those constraints may customize the computer as they desire. Once the order is received, hp assembles the computer as ordered, and delivers it to the customer. What type of manufacturing process is described here?arrow_forwardCalculate Lead Time Williams Optical Inc. is considering a new lean product cell. The present manufacturing approach produces a product in four separate steps. The production batch sizes are 66 units. The process time for each step is as follows: Process Step 1 7 minutes Process Step 2 5 minutes Process Step 3 9 minutes Process Step 4 4 minutes The time required to move each batch between steps is 16 minutes. In addition, the time to move raw materials to Process Step 1 is also 16 minutes, and the time to move completed units from Process Step 4 to finished goods inventory is 16 minutes. The new lean layout will allow the company to reduce the batch sizes from 66 units to 4 units. The time required to move each batch between steps and the inventory locations will be reduced to 3 minutes. The processing time in each step will stay the same. Determine the value-added, non-value-added, and total lead times, and the value-added ratio under the present and proposed production…arrow_forwardA production process at Kenneth Day Manufacturing is shown in the figure below. The drilling operation occurs separately from, and simultaneously with, the sawing and sanding, which are independent sequential operations. A product needs to go through only one of the three assembly operations (the operations are in parallel). 6 units/hr Sawing 2.5 units/hr Sanding Drilling 1.8 units/hr Welding 7 units/hr Assembly 0.7 units/hr Assembly 0.7 units/hr Assembly 0.7 units/hrarrow_forward
- Practical Management ScienceOperations ManagementISBN:9781337406659Author:WINSTON, Wayne L.Publisher:Cengage,
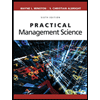