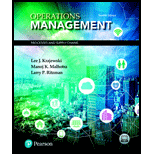
Operations Management: Processes and Supply Chains (12th Edition) (What's New in Operations Management)
12th Edition
ISBN: 9780134741062
Author: Lee J. Krajewski, Manoj K. Malhotra, Larry P. Ritzman
Publisher: PEARSON
expand_more
expand_more
format_list_bulleted
Question
Chapter 5, Problem 9P
Summary Introduction
Interpretation: The product mix for improving the profitability and change in profit needs to be determined.
Concept Introduction: Contribution margin is concerned with preparing income statement. Generally for calculating profit or loss in business it is required.
Expert Solution & Answer

Want to see the full answer?
Check out a sample textbook solution
Students have asked these similar questions
As the production planner for Xiangling Hu Products, Inc., you have been given a bill of material for a bracket that is made up of a base, 2 springs, and 4 clamps. The base is assembled from 2 clamps and 1 housing. Each clamp has 1handle and 1 casting. Each housing has 2 bearings and 2 shafts. There is no inventory on hand.
c) Compute the net quantities needed if there are 25 of the base and 100 of the clamp in stock.
Base:
units (enter your response as a whole number).
Spring:
units
Clamp:
units
Housing:
units
Handle
units
Casting:
units
Bearing:
units
Shaft:
units
As the production planner for Xiangling Hu Products, Inc., you have been given a bill of material for a bracket that is made up of a base, 2 springs, and 4 clamps. The base is assembled from 1 clamp and\ 1 housing. Each clamp has 1 handle and 2 castings.Each housing has 1 bearing and 2 shafts.There is no inventory on hand.
C) Compute the net quantities needed if there are 25 of the base and 75 of the clamp in stock.
(Product structure picture attached)
Base = (?) units
Spring = (?) units
Clamp = (?) units
Housing = (?) units
Handle = (?) units
Casting = (?) units
Bearing = (?) units
Shaft = (?) units
LMNO Gaskets has formulated a production plan for a product to meet demand over the upcoming four quarters. Demand in each of the four quarters and production, overtime, and subcontracting capacities are
reported in the table below, in addition to the feasible production plan. The relevant costs are:
• Regular time production cost is $10/unit.
Overtime production cost is $14/unit.
Subcontracting cost is $18/unit
Inventory is held at a cost of $1/unit/quarter.
• Units may be backordered at a cost of $4/unit/quarter.
Production
Resource
Regular Time Q1
Overtime Q1
Subcontract Q1
Regular Time Q2
Overtime Q2
Subcontract Q2
Regular Time Q3
Overtime Q3
Subcontract Q3
Demand in Quarter
Demand in Quarter
Q2
0
20
0
550
Q1
550
230
0
0
0
0
40
40
0
860
250
470
0
40
0
1330
What is the inventory cost for the year?
What is the backorder cost for the year?
What is the total cost for the year?
Q3
0
0
0
0
0
30
510
160
0
700
What is the total overtime production cost for the year?
Capacity
550
250
500…
Chapter 5 Solutions
Operations Management: Processes and Supply Chains (12th Edition) (What's New in Operations Management)
Ch. 5 - Take a process that you encounter on a daily...Ch. 5 - Prob. 2DQCh. 5 - How could the efficiency of the redesigned process...Ch. 5 - Bill’s Barbershop has two barbers available to...Ch. 5 - Melissa’s Photo Studio offers both individual...Ch. 5 - Figure 5.11 details the process flow for two types...Ch. 5 - Prob. 4PCh. 5 - Super Fun Industries manufactures four top-selling...Ch. 5 - Prob. 6PCh. 5 - Yost-Perry Industries (YPI) manufactures a mix of...
Ch. 5 - Prob. 8PCh. 5 - Prob. 9PCh. 5 - A.J.’s Wildlife Emporium manufactures two unique...Ch. 5 - Cooper River Glass Works (RGW) produces four...Ch. 5 - Quick Stop Pharmacy is a small family-owned,...Ch. 5 - Use the longest work element rule to balance the...Ch. 5 - Johnson Cogs wants to set up a line to serve 60...Ch. 5 - Refer back to Problem 16. Suppose that in addition...Ch. 5 - To meet holiday demand, Penny’s Pie Shop...Ch. 5 - A paced assembly line has been devised to...Ch. 5 - Prob. 20PCh. 5 - Greg Davis, a business major at the University of...Ch. 5 - Prob. 1VCCh. 5 - Which boarding scenario among the different ones...Ch. 5 - How should Southwest evaluate the gate boarding...Ch. 5 - How will Southwest know that the bottleneck had...
Knowledge Booster
Similar questions
- Fedori Corporation has a Parts Division that does work for other Divisions in the company as well as for outside customers. The company's Machinery Division has asked the Parts Division to provide it with 4,000 special parts each year. The special parts would require P23.00 per unit in variable production costs. The Machinery Division has a bid from an outside supplier for the special parts at P37.00 per unit. In order to have time and space to produce the special part, the Parts Division would have to cut back production of another part-the YR24 that it presently is producing. The YR24 sells for P40.00 per unit, and requires P28.00 per unit in variable production costs. Packaging and shipping costs of the YR24 are P3.00 per unit. Packaging and shipping costs for the new special part would be only P1.50 per unit. The Parts Division is now producing and selling 15,000 units of the YR24 each year. Production and sales of the YR24 would drop by 20% if the new special part is produced for…arrow_forwardIn the context of an Accident and Emergency Department, high demand variation can be addressed by having: Select one alternative: Yield Management. Over staffing and preferential access. Marketing. Standby capacity and flexible staffing. Demand management.arrow_forwardFrom the following production plan, the Manager wants to determine the quantities to order and wants to use the following dynamic methods. Estimate the quantities to order by the Silver and Meal method in order to cover demand at a lower cost and run out of final inventory. The unit cost is $ 20 while the preparation cost is $ 100 and keeping a unit in inventory is $ 2 per period.** In case in some period it is not requested, please write 0arrow_forward
- Boysen produces enamel and acrylic paint from two particular raw materials M1 and M2. The following data provides the data regarding the production restrictions.arrow_forwardJuliette loves to eat ice cream and spends a fortune each week buying it. In an effort to save money, she is considering making her own ice cream at home. The cost of an ice cream maker is $150 and the cost of ingredients is $6 for each 1.5 L batch. The cost of the same 1.5 L is $10 at the store. If she eats three litres of ice cream per month, will she save money by making her favourite treat at home? Assume the ice cream maker has a one-year warrant and breaks immediatelv after.arrow_forwardBased on customer benefit packages and value chain for the restaurant business determine the order qualifier and order winners for the restaurant business?arrow_forward
- The Alpha Beta Company produces two products; A and B, that are made from components C and D. Given the follow-ing product structures, master scheduling requirements, and inventory information, determine when orders shouldbe released for A, B, C, and D and the size of those orders.arrow_forwardJuliette loves to eat ice cream and spends a fortune each week buying it. In an effort to save money, she is considering making her own ice cream at home. The cost of an ice cream maker is $155 and the cost of ingredients is $4 for each 1.5 L batch. The cost of the same 1.5 L is $12 at the store. If she eats three litres of ice cream per month, will she save money by making her favourite treat at home? Assume the ice cream maker has a one-year warranty and breaks immediately after.Cost of making the ice creamCost of buying the ice creamBest optionarrow_forwardYost-Perry Industries’ (YPI) senior management team wants to improve the profitability of the firm by accepting the right set of orders. Currently, decisions are made using the traditional method, which is to accept as much of the highest contribution margin product as possible (up to the limit of its demand), followed by the next highest contribution margin product, and so on until all available capacity is utilized. Because the firm cannot satisfy all the demand, the product mix must be chosen carefully. Jay Perry, the newly promoted production supervisor, is knowledgeable about the TOC and the bottleneck-based method for scheduling. He believes that profitability can indeed be improved if bottleneck resourcesare exploited to determine the product mix. What is the change in profits if, instead of the traditional method that YPI has used thus far, the bottleneck method advocated by Jay is used for selecting the product mix?arrow_forward
- Develop a production plan and calculate the annual cost for a firm whose demand forecast is fall, 10,000; winter, 8,000; spring, 7,000; summer, 12,000. Inventory at the beginning of fall is 500 units. At the beginning of fall, you currently have 30 workers, but you plan to hire temporary workers at the beginning of summer and lay them off at the end of summer. In addition,you have negotiated with the union an option to use the regular workforce on overtime during winter or spring if overtime is necessary to prevent stock-outs at the end of those quarters. Overtime is not available during the fall. Relevant costs are hiring, $100 for each temp; layoff, $200 for each worker laid off; inventory holding, $5 per unit-quarter; backorder, $10 per unit; straight time, $5 per hour; over time, $8 per hour. Assume that productivity is 0.5 units per worker hour, with eight hours per day and 60 days per season. (Answer in Appendix D)arrow_forwardDevelop a production schedule to produce the exact production requirements by varying the workforce size for the following problem. The monthly forecasts for Product X for January, February, and March are 1,020, 1,550, and 1,220, respectively. Safety stock policy recommends that half of the forecast for that month be defined as safety stock. There are 22 working days in January, 19 in February, and 21 in March. Beginning inventory is 560 units. Manufacturing cost is $200 per unit, storage cost is $3 per unit per month, standard pay rate is $8 per hour, overtime rate is $12 per hour, cost of stockout is $10 per unit per month, hiring and training cost is $220 per worker, layoff cost is $320 per worker, and worker productivity is 0.1 unit per hour. Assume that you start off with 42 workers and that they work 8 hours per day. (Leave no cells blank - be certain to enter "0" wherever required. Input all values as positive values. Round Workers Required up to next higher whole number. Round…arrow_forwardDevelop a production plan and calculate the annual cost for a firm whose demand forecast is fall, 11,000; winter, 8,000; spring, 6,000; summer, 13,000. Inventory at the beginning of fall is 500 units. At the beginning of fall you currently have 30 workers, but you plan to hire temporary workers at the beginning of summer and lay them off at the end of summer. In addition, you have negotiated with the union an option to use the regular workforce on overtime during winter or spring if overtime is necessary to prevent stockouts at the end of those quarters. Overtime is not available during the fall. Relevant costs are hiring, $100 for each temp; layoff $200 for each worker laid off; inventory holding, $5 per unit-quarter; backorder, $10 per unit; straight time, $5 per hour; overtime, $8 per hour. Assume that the productivity is 0.5 unit per worker hour, with eight hours per day and 60 days per season. a. What is the total cost for this plan?arrow_forward
arrow_back_ios
SEE MORE QUESTIONS
arrow_forward_ios
Recommended textbooks for you
- Practical Management ScienceOperations ManagementISBN:9781337406659Author:WINSTON, Wayne L.Publisher:Cengage,
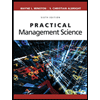
Practical Management Science
Operations Management
ISBN:9781337406659
Author:WINSTON, Wayne L.
Publisher:Cengage,