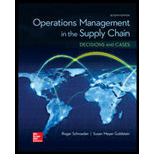
Concept explainers
A furniture factory makes two types of wooden tables, large and small. See the flowchart below.
Setup Time, Minutes | Run Time per Piece, Minutes | Capacity, Pieces per Hour | |
Wood cutting | 30 | 5 | 15 |
Male four legs | 60 | 10 | 10 |
Male tops | 60 | 12 | 8 |
Finish the wood | 20 | 8 | 12 |
Assemble and ship | 20 | 17 | 14 |
Small tables are made in batches of 100, and large tables are made in batches of 50. A batch includes a fixed setup time for the entire batch at each process step and a run time for each piece in the batch. Both large and small tables have the same processing times. The capacities of each process step are given, and apply to production of either type of table, as shown in the flowchart.
- a. What is the capacity of the system, and what is the bottleneck?
- b. What are the throughput times for batches of large and small tables?
- c. When producing at a rate of six small tables per hour on average, how many tables will be in the system?
a)

To determine: The capacity of the process.
Introduction:
Flow rate is the number of flow units through a business procedure per unit time. Flow rate refers to the number of customers who will be served per hour or the parts produced per minute.
Explanation of Solution
Given information:
A furniture factory makes large and small wooden tables. The given information is tabulated below:
Setup time (Minutes) | Run time per piece (Minutes) | Capacity (Pieces per hour) | |
Wood cutting | 30 | 5 | 15 |
Make four legs | 60 | 10 | 10 |
Make tops | 60 | 12 | 8 |
Finish the wood | 20 | 8 | 12 |
Assemble and ship | 20 | 17 | 14 |
Small wooden tables are finished in batches of 100 and large wooden tables are finished in the batches of 50. A batch includes fixed setup time and run time. Both small tables and large tables have the same processing time.
Determine the capacity:
As both large wooden table and small wooden table have same capacities, the capacity of the system is minimum of the capacity of the resources. The minimum capacity resource is 8 tables per hour and the process is making tops.
Setup time (Minutes) | Run time per piece (Minutes) | Capacity (Pieces per hour) | |
Wood cutting | 30 | 5 | 15 |
Make four legs | 60 | 10 | 10 |
Make tops | 60 | 12 | 8 |
Finish the wood | 20 | 8 | 12 |
Assemble and ship | 20 | 17 | 14 |
b)

To determine: The average throughput time.
Introduction:
Flow rate is the number of flow units through a business procedure per unit time. Flow rate refers to the number of customers who will be served per hour or the parts produced per minute.
Explanation of Solution
Given information:
A furniture factory makes large and small wooden tables. The given information is tabulated below:
Setup time (Minutes) | Run time per piece (Minutes) | Capacity (Pieces per hour) | |
Wood cutting | 30 | 5 | 15 |
Make four legs | 60 | 10 | 10 |
Make tops | 60 | 12 | 8 |
Finish the wood | 20 | 8 | 12 |
Assemble and ship | 20 | 17 | 14 |
Small wooden tables are finished in the batches of 100 and large wooden tables are finished in the batches of 50. A batch includes fixed setup time and run time. Both small tables and large tables have the same processing time.
Determine the average throughput time:
Small tables | Large tables | |
Batch size | 100 | 50 |
Wood cutting | 530 | 280 |
Make four legs | 1,060 | 560 |
Make tops | 1,260 | 660 |
Finish the wood | 820 | 420 |
Assemble and ship | 1,720 | 870 |
Total time | 4,330 | 2,230 |
Hence, the average throughput time for small tables is 4,330 minutes and the average throughput time for large tables is 2,230 minutes.
Working note:
Wood cutting for small tables:
It is calculated by adding the setup time to the multiplied value of run time and batch size.
Wood cutting for small tables=Setup time+(Run time×Batch size)=30+(5×100)=30+500=530
Wood cutting for large tables:
It is calculated by adding the setup time to the multiplied value of run time and batch size.
Wood cutting for small tables=Setup time+(Run time×Batch size)=30+(5×50)=30+250=280
Note: The calculation is carried out for all the processes.
Compute the throughput time for small tables:
While adding the time taken, the maximum amount should be chosen from the process of making four legs and tops, as they can be done in parallel.
Throughput time=530+1,260+820+1,720=4,330
Compute the throughput time for large tables:
While adding the time taken, the maximum amount should be chosen from the process of making four legs and tops, as they can be done in parallel.
Throughput time=280+660+420+870=2,230
c)

To determine: The number of tables in the system.
Introduction:
Flow rate is the number of flow units through a business procedure per unit time. Flow rate refers to the number of customers who will be served per hour or the parts produced per minute.
Explanation of Solution
Given information:
A furniture factory makes large and small wooden tables. The given information is tabulated below:
Setup time (Minutes) | Run time per piece (Minutes) | Capacity (Pieces per hour) | |
Wood cutting | 30 | 5 | 15 |
Make four legs | 60 | 10 | 10 |
Make tops | 60 | 12 | 8 |
Finish the wood | 20 | 8 | 12 |
Assemble and ship | 20 | 17 | 14 |
Small wooden tables are finished in the batches of 100 and large wooden tables are finished in the batches of 50. A batch includes fixed setup time and run time. Both small tables and large tables have the same processing time. The factory is producing at the rate of six small tables per hour.
Formula to determine the average number of tables in the system:
I=T×R
Here
I refers to the number of orders in the systems.
T refers to the average throughout time.
R refers to the average flow rate in the process.
Determine the average number of tables in the system:
It calculated by multiplying the average throughput time with the average flow rate in the process.
I=T×R=(4,33060)×6=72.167×6=433 tables
Hence, the average number of tables in the system is 433 tables.
Want to see more full solutions like this?
Chapter 6 Solutions
OPERATIONS MANAGEMENT IN THE SUPPLY CHAIN: DECISIONS & CASES (Mcgraw-hill Series Operations and Decision Sciences)
- An investigation of career development opportunities and job satisfaction atarrow_forwardThe Donald Fertilizer Company produces industrial chemical fertilizers. The projected manufacturing requirements (in gallons) for the next four quarters are 90,000, 90,000, 60,000, and 140,000 respectively. A level workforce is desired, relying only on anticipation inventory as a supply option. Stockouts and backorders are to be avoided, as are overtime and undertime. a. Determine the quarterly production rate required to meet total demand for the year, and minimize the anticipation inventory that would be left over at the end of the year. Beginning inventory is 0. The quarterly production rate is 95000 gallons. (Enter your response as an integer.) b. Specify the anticipation inventory that will be produced. (Enter your responses as an integers.) Quarter Anticipation inventory (gallons) 1 5000 2 10000 3 4 45000 c. Suppose that the requirements (in gallons) for the next four quarters are revised to 140,000, 60,000, 90,000, and 90,000 respectively. If total demand is the same, what level…arrow_forwardPlease help with the attached Capstone proposal Requirements:arrow_forward
- Long term capacity plans and how to properly make decisions regarding long-term planning Long-term capacity plans cover periods longer periods of time. These plans are suitable for large businesses that want to scale their operations with a proven strategy for achieving production targets and meeting customer demands. Long-term capacity plans consider other factors apart from the productive requirements of the company. How important is it, in your mind, to properly make decisions regarding long-term capacity planning? How does this decision impact the present and future profitability of an organization? Be specific and give examples.arrow_forwardIn addition to the Amazon case study you provided, I'm curious if you've encountered other examples of companies successfully applying Little's Law to enhance their supply chain risk management practices. For instance, have you seen organizations use queuing theory to assess the potential ripple effects of disruptions, stress-test their contingency plans, or identify critical control points that require heightened monitoring and agility? Please provide a referencearrow_forwardSam's Pet Hotel operates 48 weeks per year, 6 days per week, and uses a continuous review inventory system. It purchases kitty litter for $13.00 per bag The following information is available about these bags: > Demand 85 bags/week >Order cost $60.00/order > Annual holding cost = 35 percent of cost > Desired cycle-service level 80 percent > Lead time = 4 weeks (24 working days) > Standard deviation of weekly demand = 15 bags > Current on-hand inventory is 320 bags, with no open orders or backorders. a. Suppose that the weekly demand forecast of 85 bags is incorrect and actual demand averages only 65 bags per week. How much higher will total costs be, owing to the distorted EOQ caused by this forecast error? The costs will be $higher owing to the error in EOQ. (Enter your response rounded to two decimal places.)arrow_forward
- Osprey Sports stocks everything that a musky fisherman could want in the Great North Woods. A particular musky lure has been very popular with local fishermen as well as those who buy lures on the Internet from Osprey Sports. The cost to place orders with the supplier is $3030/order; the demand averages 55 lures per day, with a standard deviation of 11 lure; and the inventory holding cost is $1.001.00/lure/year. The lead time form the supplier is 1010 days, with a standard deviation of 33 days. It is important to maintain a 9898 percent cycle-service level to properly balance service with inventory holding costs. Osprey Sports is open 350 days a year to allow the owners the opportunity to fish for muskies during the prime season. The owners want to use a continuous review inventory system for this item. Refer to the standard normal table LOADING... for z-values. Part 2 a. What order quantity should be used? enter your response here lures. (Enter your response rounded to the…arrow_forward9. Research Methodology Fully explain the Quantitative research methodology that and add in the following sub-sections: . Data Collection • Data Analysisarrow_forwardRuby-Star Incorporated is considering two different vendors for one of its top-selling products which has an average weekly demand of 40 units and is valued at $80 per unit. Inbound shipments from vendor 1 will average 340 units with an average lead time (including ordering delays and transit time) of 2 weeks. Inbound shipments from vendor 2 will average 550 units with an average lead time of 1 week. Ruby-Star operates 52 weeks per year; it carries a 2-week supply of inventory as safety stock and no anticipation inventory. a. The average aggregate inventory value of the product if Ruby-Star used vendor 1 exclusively is $ (Enter your response as a whole number.)arrow_forward
- The Carbondale Hospital is considering the purchase of a new ambulance. The decision will rest partly on the anticipated mileage to be driven next year. The miles driven during the past 5 years are as follows: Year Mileage 1 3,000 2 3 4 4,000 3,450 3,850 5 3,800 a) Using a 2-year moving average, the forecast for year 6 = miles (round your response to the nearest whole number). b) If a 2-year moving average is used to make the forecast, the MAD based on this = miles (round your response to one decimal place). (Hint: You will have only 3 years of matched data.) c) The forecast for year 6 using a weighted 2-year moving average with weights of 0.40 and 0.60 (the weight of 0.60 is for the most recent period) = ☐ miles (round your response to the nearest whole number). miles (round your response to one decimal place). (Hint: You will have only 3 years of The MAD for the forecast developed using a weighted 2-year moving average with weights of 0.40 and 0.60 = matched data.) d) Using…arrow_forwardTask time estimates for the modification of an assembly line at Jim Goodale's Carbondale, Illinois, factory are as follows: B D G Time Activity (in hours) Immediate Predecessor(s) A 5.0 B 7.5 C 5.0 A DEFC 8.0 B, C 4.5 Figure 2 A B, C 7.7 D G 5.0 E, F This exercise contains only part a. a) The correct precedence diagram for the project is shown in 目 F B Figure 3 A E B E ☑ D Farrow_forwardDave Fletcher was able to determine the activity times for constructing his laser scanning machine. Fletcher would like to determine ES, EF, LS, LF, and slack for each activity. The total project completion time and the critical path should also be determined. Here are the activity times: Activity Time (weeks) Immediate Predecessor(s) Activity Time (weeks) Immediate Predecessor(s) A 6 E 3 B B 8 F 6 B C 3 A G 11 C, E D 1 A H 7 D, F Dave's earliest start (ES) and earliest finish (EF) are: Activity ES .EF A 0 6 B 0 8 C 3 9 D 6 E F 8 G 22 H 21 Dave's latest start (LS) and latest finish (LF) are: Activity LS LF H 15 G 11 F 9arrow_forward
- Practical Management ScienceOperations ManagementISBN:9781337406659Author:WINSTON, Wayne L.Publisher:Cengage,
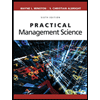