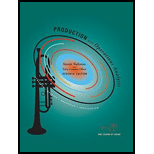
Production and Operations Analysis, Seventh Edition
7th Edition
ISBN: 9781478623069
Author: Steven Nahmias, Tava Lennon Olsen
Publisher: Waveland Press, Inc.
expand_more
expand_more
format_list_bulleted
Concept explainers
Question
Chapter 4.7, Problem 25P
Summary Introduction
To determine:
Size of the order.
Introduction:
Aggregate planning is the technique in which planning of all inputs and output of production is planned to meet any uncertainty of demand and avoid any wastage in the process.
Expert Solution & Answer

Want to see the full answer?
Check out a sample textbook solution
Students have asked these similar questions
Johnson Tire Plaza (JTP) is a large chain of tire shops, who sells various brand of automobile tires. The yearly demand of a particular brand of time is about 10,821 units per year. JTP purchases these tires from a supplier. The ordering cost is $109 per order and the holding cost is $14.6 per tire per year. The supplier always delivers the shipment within 13 days after receiving a replenishment order from JTP. The company operates 250 days per year. Assume EOQ model is applicable.
What is the number of orders per year if JTP uses an order quantity of 1,728 tires? Use at least 4 decimal places.
The Bosch factory in New Bern, NC uses dishwasher motors at a steady rate of 17308 units per year. Bosch procures
these units from a supplier at a purchase cost of $58 per unit. Bosch receives an order 26 days after it is placed.
Regardless of the number of units ordered, Bosch incurs a fixed cost of $2988 for placing, shipping, and receiving the
order. The holding cost per unit per year is 30% of the purchase cost per unit. Assume Bosch operates 364 days, 52
weeks, or 12 months per year.
Calculate the average time a unit spends in inventory between orders in DAYS for the optimal order quantity from the
problem above.
Rounding instructions
• Carry your calculations to at least 3 decimal places.
• Enter your answer rounded to one decimal place (nearest tenth).
Radovilsky Manufacturing Company, in Hayward, California, makes flashing lights for toys. The company operates its production facility
300
days per year. It has orders for about
12,200
flashing lights per year and has the capability of producing
95
per day. Setting up the light production costs
$51.
The cost of each light is
$1.00.
The holding cost is
$0.15
per light per year.
d. What is the total cost per year, including the cost of the lights?
(round your response to two decimal places).
Chapter 4 Solutions
Production and Operations Analysis, Seventh Edition
Ch. 4.4 - Prob. 1PCh. 4.4 - Prob. 2PCh. 4.4 - Prob. 3PCh. 4.4 - Prob. 4PCh. 4.4 - Prob. 5PCh. 4.4 - Prob. 6PCh. 4.4 - Prob. 7PCh. 4.4 - Prob. 8PCh. 4.4 - Prob. 9PCh. 4.5 - Prob. 10P
Ch. 4.5 - Prob. 11PCh. 4.5 - Prob. 12PCh. 4.5 - Prob. 13PCh. 4.5 - Prob. 14PCh. 4.5 - Prob. 15PCh. 4.5 - Prob. 16PCh. 4.6 - Prob. 17PCh. 4.6 - Prob. 18PCh. 4.6 - Prob. 19PCh. 4.6 - Prob. 20PCh. 4.7 - Prob. 21PCh. 4.7 - Prob. 22PCh. 4.7 - Prob. 23PCh. 4.7 - Prob. 24PCh. 4.7 - Prob. 25PCh. 4.8 - Prob. 26PCh. 4.8 - Prob. 27PCh. 4.8 - Prob. 28PCh. 4.9 - Prob. 29PCh. 4.9 - Prob. 30PCh. 4 - Prob. 31APCh. 4 - Prob. 32APCh. 4 - Prob. 33APCh. 4 - Prob. 34APCh. 4 - Prob. 35APCh. 4 - Prob. 36APCh. 4 - Prob. 37APCh. 4 - Prob. 38APCh. 4 - Prob. 39APCh. 4 - Prob. 40APCh. 4 - Prob. 41APCh. 4 - Prob. 42APCh. 4 - Prob. 43APCh. 4 - Prob. 44APCh. 4 - Prob. 45AP
Knowledge Booster
Learn more about
Need a deep-dive on the concept behind this application? Look no further. Learn more about this topic, operations-management and related others by exploring similar questions and additional content below.Similar questions
- A company would like to classify its inventory systems using ABC inventory classification system. The rules for ABC classification are STRICTLY applied such that 80% cumulative budget is assigned to A class inventory items. The next 15% cumulative budget is assigned to B class inventory items, and Only 5% of the cumulative budget is assigned to C class inventory items. The inventory items (SKU) are XYZ1, XYZ2, XYZ3, and XYZ4 respectively. The Annual demands (units per year) for these items are 290, 457, and 159. and 577 respectively. Also, the corresponding per unit prices are 19.33.126, and 90 respectively measured in OMR. Which items (among, XYZ1, XYZ2, XYZ3, and XYZ4) are classified as B class inventory Select one: a. XYZ1 b. XYZ2 c XYZ3 d.XYZ3 and XYZ4arrow_forwardMedtronic sells medical devices. The company enjoys many growth opportunities, and so it measures its inventory holding cost at the rate of 25% per year. It currently turns over its inventory 3 times per year. Its gross margin (the difference between revenue and cost) as a percentage of its revenue is an enviable 65%. a. For an item that costs Medtronic $600 to produce, what would be the cost ($s) to hold this item for one year in inventory? b. For an item that costs Medtronic $350 to produce, what is the cost to hold it in inventory ($s)? (Assume it remains in inventory for the average amount of time for the company.)arrow_forwardA company would like to classify its inventory systems using ABC inventory classification system. The rules for ABC classification are STRICTLY applied such that 80% cumulative budget is assigned to A class inventory items. The next 15% cumulative budget is assigned to B class inventory items, and Only 5% of the cumulative budget is assigned to C class inventory items. The inventory items (SKU) are XYZ1, XYZ2, XYZ3, and XYZ4 respectively. The Annual demands (units per year) for these items are 290, 457, and 159, and 577 respectively. Also, the corresponding per unit prices are 19, 33, 126, and 90 respectively measured in OMR. Which items (among, XYZ1, XYZ2, XYZ3, and XYZ4) are classified as A class inventory Select one: a. Only XYZ3 b. All items c XYZ1 only d. Both XYZ3 and XYZ4arrow_forward
- Buckley Enterprise sells a product that cost $450 per unit and has a monthly demand of 5,000units. The annual holding cost per unit is calculated as 5% of the unit purchase price. It costs thebusiness $75 to place a single order. Currently the business places 12 orders each year.i) What is the total stock administrative cost of Buckley’s current inventory policy?ii) Is this the entity’s cost minimizing solution for this product each year? Explain.arrow_forwardCranium, Inc., purchases term papers from an overseas supplier under a continuous review system. The average demand for a popular mode is 300 units a day with a standard deviation of 30 units a day. It costs $60 to process each order and there is a five-day lead-time. The holding cost for a paper is $0.25 per year and the company policy is to maintain a 98% service level. Cranium operates 200 days per year. A normal distribution table is append-: this exam. a) Determine the reorder point R to satisfy a 98% cycle-service level. b) What service level does a reorder point of 1,524 imply? c) If lead-time increases by three days, what is the reorder point needed to maintain a 98% service level? d) What is the cost of holding the safety stock necessary to maintain the 98% service level?arrow_forwardA company would like to classify its inventory systems using ABC inventory classification system. The rules for ABC classification are STRICTLY applied such that 80% cumulative budget is assigned to A class inventory items. The next 15% cumulative budget is assigned to B class inventory items, and Only 5% of the cumulative budget is assigned to C class inventory items. The inventory items are XYZ1, XYZ2, XYZ3, and XYZ4 respectively. The Annual demands (units per year) for these items are 290, 457, and 159, and 577 respectively. Also, the corresponding per unit prices are 19, 33, 126, and 90 respectively measured in OMR. Which items (among, XYZ1, XYZ2, XYZ3, and XYZ4) are classified as A class inventory O a. None is correct O b. Only XYZ3 O c. XYZ1 only O d. Both XYZ3 and XYZ4 O e. All items PAGE NEXT PAGE MAG241C CURVED 144arrow_forward
- A company would like to classify its inventory systems using ABC inventory classification system. The rules for ABC classification are STRICTLY applied such that 80% cumulative budget is assigned to A class inventory items. The next 15% cumulative budget is assigned to B class inventory items, and Only 5% of the cumulative budget is assigned to C class inventory items. The inventory items are XYZ1, XYZ2, XYZ3, and XYZ4 respectively. The Annual demands (units per year) for these items are 290, 457, and 159, and 577 respectively. Also, the corresponding per unit prices are 19, 33, 126, and 90 respectively measured in OMR. Which items (among, XYZ1, XYZ2, XYZ3, and XYZ4) are classified as A class inventory O a. XYZ1 only O b. Only XYZ3 Both XYZ3 and XYZ4 d. All items O e. None is correctarrow_forwardI need a detailed explanation on how to solve this problem: A paint shop implements an inventory policy on its stock of white paint, which costs the store $6 per can. Monthly demand for cans of white paint is normal with mean 28 and standard deviation 8. The replenishment lead time is 14 weeks. Excess demand is backordered, but costs $10 per back ordered can in labor and loss of goodwill. There is a fixed cost of $15 per order, and the holding cost is based on 30% interest rate per annum. In your computations, assume 4 weeks per month. - Write down the model name and parameters. - What are the optimal lot size and reorder points for white paint (include the formulas)? - What is the optimal safety stock (include the formula)? *** Suppose the paint shop from the above problem adopts a service level policy. - What are the optimal lot size and reorder points for white paint, such that 90% of the cycles are filled without backordering (include all formulas)? - What is the fill rate…arrow_forwardA restaurant uses 5,000 quart bottles of ketchup each year. The ketchup costs $3.00 per bottle and is served only in whole bottles because its taste quickly deteriorates. The restaurant figures that it costs $10.00 each time an order is placed, and holding costs are 20 percent of the purchase price. It takes 3 weeks for an order to arrive. The restaurant operates 50 weeks per year. The restaurant would like to use an inventory system that minimizes inventory cost. The restaurant has figured that the most economical order size or EOQ is approx. 409 (rounding up the decimals). Suppose that things have become uncertain and that customer demand is no more constant. Customer demand is now normally distributed with mean being the same as given in the problem description and standard deviation = 30 units per week. The supply source is still very reliable and as a result the lead time is constant. Find out the safety stock needed to achieve 95% customer service level. O 55 65 075 85 None of…arrow_forward
- The owner and manager of a hardware store reevaluates his inventory policy for hammers. sells an average of 50 hammers a month, so you have placed purchase orders for 50 hammers with a distributor at a cost of $20 each at the end of each month. But the owner does not place all the store orders and find that this takes much of your time. He estimates that the value of his time spent ordering hammers is $75. a) What must be the unit cost of maintaining hammers for the current policy of the hardware store to be Optimal according to the EOQ model? b) If the distributor delivers an order for hammers in 5 business days (out of an average of 25 per month), what should be the reorder point, according to the EOQ model?arrow_forwardCranium, Inc., purchases term papers from an overseas supplier under a continuous review system. The average demand for a popular model is 300 units a day with a standard deviation of 30 units a day. It costs $60 to process each order and there is a five-day lead-time. The holding cost for a paper is $0.25 per year and the company policy is to maintain a 98% service level. Cranium operates 200 days per year.arrow_forwardABC Inc., purchases Widgets from an overseas supplier under a continuous review system. The average demand for a popular model is 300 units a day with a Lead Time standard deviation of 70 units. It costs $60 to process each order and there is a five-day lead-time. The holding cost for a widget is $0.25 per year and the company policy is to maintain a 98% service level. ABC operates 200 days per year. What is the additional cost in $ of holding the safety stock necessary to maintain the 98% service level? What service level in % does a reorder point of 1,570 imply?arrow_forward
arrow_back_ios
SEE MORE QUESTIONS
arrow_forward_ios
Recommended textbooks for you
- Practical Management ScienceOperations ManagementISBN:9781337406659Author:WINSTON, Wayne L.Publisher:Cengage,Operations ManagementOperations ManagementISBN:9781259667473Author:William J StevensonPublisher:McGraw-Hill EducationOperations and Supply Chain Management (Mcgraw-hi...Operations ManagementISBN:9781259666100Author:F. Robert Jacobs, Richard B ChasePublisher:McGraw-Hill Education
- Purchasing and Supply Chain ManagementOperations ManagementISBN:9781285869681Author:Robert M. Monczka, Robert B. Handfield, Larry C. Giunipero, James L. PattersonPublisher:Cengage LearningProduction and Operations Analysis, Seventh Editi...Operations ManagementISBN:9781478623069Author:Steven Nahmias, Tava Lennon OlsenPublisher:Waveland Press, Inc.
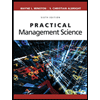
Practical Management Science
Operations Management
ISBN:9781337406659
Author:WINSTON, Wayne L.
Publisher:Cengage,
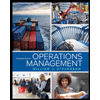
Operations Management
Operations Management
ISBN:9781259667473
Author:William J Stevenson
Publisher:McGraw-Hill Education
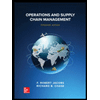
Operations and Supply Chain Management (Mcgraw-hi...
Operations Management
ISBN:9781259666100
Author:F. Robert Jacobs, Richard B Chase
Publisher:McGraw-Hill Education
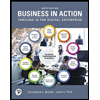
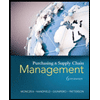
Purchasing and Supply Chain Management
Operations Management
ISBN:9781285869681
Author:Robert M. Monczka, Robert B. Handfield, Larry C. Giunipero, James L. Patterson
Publisher:Cengage Learning
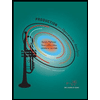
Production and Operations Analysis, Seventh Editi...
Operations Management
ISBN:9781478623069
Author:Steven Nahmias, Tava Lennon Olsen
Publisher:Waveland Press, Inc.
Inventory Management | Concepts, Examples and Solved Problems; Author: Dr. Bharatendra Rai;https://www.youtube.com/watch?v=2n9NLZTIlz8;License: Standard YouTube License, CC-BY