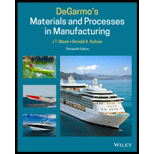
Degarmo's Materials And Processes In Manufacturing
13th Edition
ISBN: 9781119492825
Author: Black, J. Temple, Kohser, Ronald A., Author.
Publisher: Wiley,
expand_more
expand_more
format_list_bulleted
Concept explainers
Question
Chapter 27, Problem 29RQ
To determine
The relation between the feed per stroke in shaping and feed per tooth in milling.
Expert Solution & Answer

Want to see the full answer?
Check out a sample textbook solution
Students have asked these similar questions
36
2) Use the method of MEMBERS to determine the true magnitude and
direction of the forces in members1 and 2 of the frame shown below
in Fig 3.2.
300lbs/ft
member-1
member-2
30°
Fig 3.2.
https://brightspace.cuny.edu/d21/le/content/433117/viewContent/29873977/View
Can you solve this for me?
5670 mm
The apartment in the ground floor of three floors building in Fig. in Baghdad city. The details of
walls, roof, windows and door are shown. The window is a double glazing and air space thickness
is 1.3cm Poorly Fitted-with Storm Sash with wood strip and storm window of 0.6 cm glass
thickness. The thickness of door is 2.5 cm. The door is Poor Installation. There are two peoples
in each room. The height of room is 280 cm. assume the indoor design conditions are 25°C DBT
and 50 RH, and moisture content of 8 gw/kga. The moisture content of outdoor is 10.5 gw/kga.
Calculate heat gain for living room :
الشقة في الطابق الأرضي من مبنى ثلاثة طوابق في مدينة بغداد يظهر في مخطط الشقة تفاصيل الجدران والسقف
والنوافذ والباب. النافذة عبارة عن زجاج مزدوج وسمك الفراغ الهوائي 1.3 سم ضعيف الاحكام مع ساتر حماية مع إطار
خشبي والنافذة بسماكة زجاج 0.6 سم سماكة الباب 2.5 سم. الباب هو تركيب ضعيف هناك شخصان في كل غرفة.
ارتفاع الغرفة 280 سم. افترض أن ظروف التصميم الداخلي هي DBT25 و R50 ، ومحتوى الرطوبة 8…
Chapter 27 Solutions
Degarmo's Materials And Processes In Manufacturing
Ch. 27 - Why is sawing one of the most efficient of the...Ch. 27 - Explain why tooth spacing (pitch) is important in...Ch. 27 - What is the tooth gullet used for on a saw blade?Ch. 27 - Explain what is meant by the set of the teeth on a...Ch. 27 - How is tooth set related to saw kerf?Ch. 27 - Why can a bandsaw blade not be hardened throughout...Ch. 27 - What are the advantages of using circular saws?Ch. 27 - Why have bandsawing machines largely replaced...Ch. 27 - Explain how the hole in Figure 27.7 is made on a...Ch. 27 - How would you calculate or estimate Tm for a...
Ch. 27 - What is the disadvantage of using gravity to feed...Ch. 27 - What is unique about the broaching process...Ch. 27 - Can a thick saw blade be used as a broach? Why or...Ch. 27 - Broaching machines are simpler in a basic design...Ch. 27 - Why is broaching particularly well-suited for mass...Ch. 27 - In designing a broach, what would be the first...Ch. 27 - Why is it necessary to relate the design of a...Ch. 27 - What two methods can be utilized to reduce the...Ch. 27 - For a given job, how would a broach having...Ch. 27 - Why are the pitch and radius of the gullet between...Ch. 27 - Why are broaching speeds usually relatively low,...Ch. 27 - What are the advantages of shell-type broach...Ch. 27 - Why are most broaches made from alloy or...Ch. 27 - What are the advantages of TiN-coated broaching...Ch. 27 - For mass-production operations, which process is...Ch. 27 - What is the difference between the roughing teeth...Ch. 27 - The sides of a square, blind hole must be machined...Ch. 27 - The interior, flat surfaces of socket wrenches,...Ch. 27 - Prob. 29RQCh. 27 - What are some ways to improve the efficiency of a...Ch. 27 - To what extent is filing different from sawing?Ch. 27 - Prob. 32RQCh. 27 - Prob. 33RQCh. 27 - Prob. 34RQCh. 27 - A surface 12 in. long is to be machined with a...Ch. 27 - The pitch of the teeth on a simple surface broach...Ch. 27 - Estimate the (approximate maximum) horsepower...Ch. 27 - Estimate the approximate force acting in the...Ch. 27 - In cutting a 6-in.-long slot in a piece of AISI...Ch. 27 - The strength of a pull broach is determined by its...Ch. 27 - Suppose you want to shape a block of metal 7 in....Ch. 27 - Could you have saved any time in Problem 7 by...Ch. 27 - Derive the equation for shaping cutting speed.Ch. 27 - How many strokes per minute would be required to...Ch. 27 - How much time would be required to shape a flat...Ch. 27 - What is the metal removal rate in Problem 11 if...Ch. 27 - Suppose you decide to mill the flat surface...Ch. 27 - A planer has a 10-hp motor, and 75% of the motor...
Knowledge Booster
Learn more about
Need a deep-dive on the concept behind this application? Look no further. Learn more about this topic, mechanical-engineering and related others by exploring similar questions and additional content below.Similar questions
- How do i solve this problem?arrow_forwardQ4/ A compressor is driven motor by mean of a flat belt of thickness 10 mm and a width of 250 mm. The motor pulley is 300 mm diameter and run at 900 rpm and the compressor pulley is 1500 mm diameter. The shaft center distance is 1.5 m. The angle of contact of the smaller pulley is 220° and on the larger pulley is 270°. The coefficient of friction between the belt and the small pulley is 0.3, and between the belt and the large pulley is 0.25. The maximum allowable belt stress is 2 MPa and the belt density is 970 kg/m³. (a) What is the power capacity of the drive and (b) If the small pulley replaced by V-grooved pulley of diameter 300 mm, grooved angle of 34° and the coefficient of friction between belt and grooved pulley is 0.35. What will be the power capacity in this case, assuming that the diameter of the large pulley remain the same of 1500 mm.arrow_forwardYou are tasked with designing a power drive system to transmit power between a motor and a conveyor belt in a manufacturing facility as illustrated in figure. The design must ensure efficient power transmission, reliability, and safety. Given the following specifications and constraints, design drive system for this application: Specifications: Motor Power: The electric motor provides 10 kW of power at 1,500 RPM. Output Speed: The output shaft should rotate at 150 rpm. Design Decisions: Transmission ratio: Determine the necessary drive ratio for the system. Shaft Diameter: Design the shafts for both the motor and the conveyor end. Material Selection: Choose appropriate materials for the gears, shafts. Bearings: Select suitable rolling element bearings. Constraints: Space Limitation: The available space for the gear drive system is limited to a 1-meter-long section. Attribute 4 of CEP Depth of knowledge required Fundamentals-based, first principles analytical approach…arrow_forward
- - | العنوان In non-continuous dieless drawing process for copper tube as shown in Fig. (1), take the following data: Do-20mm, to=3mm, D=12mm, ti/to=0.6 and v.-15mm/s. Calculate: (1) area reduction RA, (2) drawing velocity v. Knowing that: ti: final thickness V. Fig. (1) ofthrearrow_forwardA direct extrusion operation produces the cross section shown in Fig. (2) from an aluminum billet whose diameter 160 mm and length - 700 mm. Determine the length of the extruded section at the end of the operation if the die angle -14° 60 X Fig. (2) Note: all dimensions in mm.arrow_forwardFor hot rolling processes, show that the average strain rate can be given as: = (1+5)√RdIn(+1)arrow_forward
- : +0 usão العنوان on to A vertical true centrifugal casting process is used to produce bushings that are 250 mm long and 200 mm in outside diameter. If the rotational speed during solidification is 500 rev/min, determine the inside radii at the top and bottom of the bushing if R-2R. Take: -9.81 mis ۲/۱ ostrararrow_forward: +0 العنوان use only In conventional drawing of a stainless steel wire, the original diameter D.-3mm, the area reduction at each die stand r-40%, and the proposed final diameter D.-0.5mm, how many die stands are required to complete this process. онarrow_forwardIn non-continuous dieless drawing process for copper tube as shown in Fig. (1), take the following data: Do-20mm, to=3mm, D=12mm, ti/to=0.6 and vo-15mm/s. Calculate: (1) area reduction RA, (2) drawing velocity v. Knowing that: t₁: final thickness D₁ V. Fig. (1) Darrow_forward
- A vertical true centrifugal casting process is used to produce bushings that are 250 mm long and 200 mm in outside diameter. If the rotational speed during solidification is 500 rev/min, determine the inside radii at the top and bottom of the bushing if R-2Rb. Take: 8-9.81 m/sarrow_forwardIn conventional drawing of a stainless steel wire, the original diameter D.-3mm, the area reduction at each die stand r-40%, and the proposed final diameter D₁-0.5mm, how many die stands are required to complete this process.arrow_forwardA vertical true centrifugal casting process is used to produce bushings that are 250 mm long and 200 mm in outside diameter. If the rotational speed during solidification is 500 rev/min, determine the inside radii at the top and bottom of the bushing if R-2Rb. Take: 8-9.81 m/sarrow_forward
arrow_back_ios
SEE MORE QUESTIONS
arrow_forward_ios
Recommended textbooks for you
- Elements Of ElectromagneticsMechanical EngineeringISBN:9780190698614Author:Sadiku, Matthew N. O.Publisher:Oxford University PressMechanics of Materials (10th Edition)Mechanical EngineeringISBN:9780134319650Author:Russell C. HibbelerPublisher:PEARSONThermodynamics: An Engineering ApproachMechanical EngineeringISBN:9781259822674Author:Yunus A. Cengel Dr., Michael A. BolesPublisher:McGraw-Hill Education
- Control Systems EngineeringMechanical EngineeringISBN:9781118170519Author:Norman S. NisePublisher:WILEYMechanics of Materials (MindTap Course List)Mechanical EngineeringISBN:9781337093347Author:Barry J. Goodno, James M. GerePublisher:Cengage LearningEngineering Mechanics: StaticsMechanical EngineeringISBN:9781118807330Author:James L. Meriam, L. G. Kraige, J. N. BoltonPublisher:WILEY
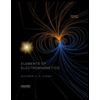
Elements Of Electromagnetics
Mechanical Engineering
ISBN:9780190698614
Author:Sadiku, Matthew N. O.
Publisher:Oxford University Press
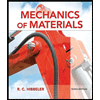
Mechanics of Materials (10th Edition)
Mechanical Engineering
ISBN:9780134319650
Author:Russell C. Hibbeler
Publisher:PEARSON
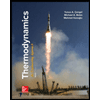
Thermodynamics: An Engineering Approach
Mechanical Engineering
ISBN:9781259822674
Author:Yunus A. Cengel Dr., Michael A. Boles
Publisher:McGraw-Hill Education
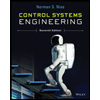
Control Systems Engineering
Mechanical Engineering
ISBN:9781118170519
Author:Norman S. Nise
Publisher:WILEY
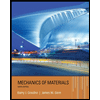
Mechanics of Materials (MindTap Course List)
Mechanical Engineering
ISBN:9781337093347
Author:Barry J. Goodno, James M. Gere
Publisher:Cengage Learning
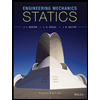
Engineering Mechanics: Statics
Mechanical Engineering
ISBN:9781118807330
Author:James L. Meriam, L. G. Kraige, J. N. Bolton
Publisher:WILEY
The Most Common Metal Machining Processes (Metal Machining Video 1); Author: Sofeast Ltd;https://www.youtube.com/watch?v=uxVJ3qtezGw;License: Standard YouTube License, CC-BY
Machining process and Machine Tools; Author: Amar Gandhi;https://www.youtube.com/watch?v=X2mUJ8baaE0;License: Standard Youtube License