What is machining?
Machining is represented as the process in which an excessive amount of substance is eliminated from the particular element in the form of pieces. In machining, cutting tools such as rotary tools, lathe, drill press, grinder, chop saw, welders, and many more are applied to get the desired shape. As compared to other manufacturing processes, machining is precise and versatile.
The following are some advantages of machining processes.
- The surface of the materials are well finished.
- Machining can be applied to composite materials, wood, ceramics, and plastic.
- The dimensional accuracy is better in comparison to other processes.
- Various types of geometric features can be obtained through machining processes, like accurate round holes, edges, and others.
The following are some drawbacks of machining processes.
- The continual changes in the design of elements are not included in the existing layout.
- The manufacturing of complex shapes is challenging.
- In machining processes, lack of consistency in manufacturing is a major concern.
- The efficiency of the machine operator decides the accuracy of the produced element.
Some common types of machining operations processes are listed below:
- Turning
- Milling
- Facing
- Drilling
- Boring
- Knurling
- Grinding
- Electric discharge machining (EDM)
Turning
Turning is expressed as the machining process that is applied mainly on a tubular surface for decreasing its diameter. The machine and cutting tools utilized for turning operation are lathe machines and single-point cutting tools, respectively. In this process, the feed rate, as well as the depth of cut, will be conveyed by the cutting tool's longitudinal and transverse movement.
Milling
The milling operation is utilized for creating flat surfaces or stepped surfaces with the help of a multi-point cutting tool (milling cutter) and milling machines. In this process, the feed rate, as well as the depth of cut, will be conveyed by moving the workpiece in the required direction. As compared to turning operations, milling is better for performing a sequence of operations on a component.
Facing
Facing is described as the process, which is executed for making flat and smooth surfaces. It can be used with two machine tools, a lathe machine, and milling machines. The lathe machine is used in some cases for producing cylindrical components. The facing operation relies on various factors like the type of element, workpiece speed, tool size, and many more.
Drilling
The drilling process is a widely used machining process because the holes produced are usually helpful in assembly. In this process, the feed rate, as well as the depth of cut, will be conveyed by moving the worktable in the required direction. Several drill bits are utilized for creating holes more than their actual size.
Boring
The boring process is applied on the surfaces to refine the dimensions as well as the precision of the hole. The machine tool and cutting tool used in the boring operation are drilling machine, lathe machine or boring machine and single point cutter respectively. Some other functions of the boring process are roughing, semi-finishing, and casting finishing.
Knurling
The knurling process is used on surfaces to lessen the possibility of slipping. In this process, a multi-point cutter is applied on the surface, and it improves the gripping of a component. Some essential operations of the knurling process are creating patterns of cross line-shaped and diamond-shaped, straight-lined, and many more.
Grinding
The grinding process is one of the cutting processes in which grinding wheels are applied to a workpiece to discharge the unrequired layer of material. The surfaces on which grinding operations are performed are flat as well as tubular. In this process, high and accurate surface finishing is obtained. Advantages of grinding operation are machining hard materials, working at high temperatures, cutting speed, producing smooth surfaces, and others. Disadvantages of the grinding process are a tool, or the entire process is expensive, and removing an excess amount of material is not possible.
Electric discharge machining
Electric discharge machining is represented as one of the machining operations which uses electric discharges for generating the required shape. In this process, electrodes and dielectric fluid play a crucial part in extracting materials from the surface. Some of the applications of electric discharge machining are thread cutting, wire cutting, profile milling, form cutting, and drilling.
What is a machine tool?
A machine tool is expressed as a device that is useful in shaping or processing a surface to the required precision. There are different types of machine tool in the manufacturing process, which performs various operations like boring, planning, grinding, sawing, drilling, and others. Also, machine tools execute several other functions like controlling the machining parameters, feed rate, and providing power to the tool.
Some of the common types of machine tools are listed below:
- Turning machine
- Drilling machine
- Milling machine
- Grinding machine
- Shaper and planer machine
Turning machine
In turning machines, the material is eliminated with the help of cutting tools from the surface by rotating the job. Lathe machines and boring mills are the mainly used turning machines in industries. The parts of turning machines are bushings, thread roads, shafts, screws, and others.
The diagram of the lathe machine is given below:
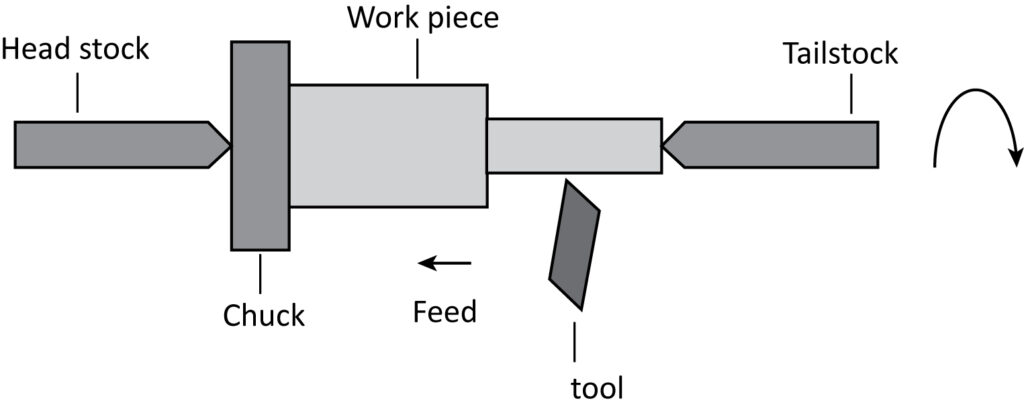
Drilling machine
In drilling machines, a drill bit with a pointed edge is utilized for forming holes on a surface. Some parts of drilling machines are base, spindle, drill head, column, and table. Many processes like counter-boring, tapping, boring, reaming are performed on drilling machines.
Milling machine
In milling machines, a rotary cutter is used for removing undesired material from the job. Some parts of milling machines are base, saddle, spindle, column, over-arm, ram, power mechanism, and table. Many processes like surface finishing, profile milling are performed on milling machines.
The diagram of the milling machine is given below:
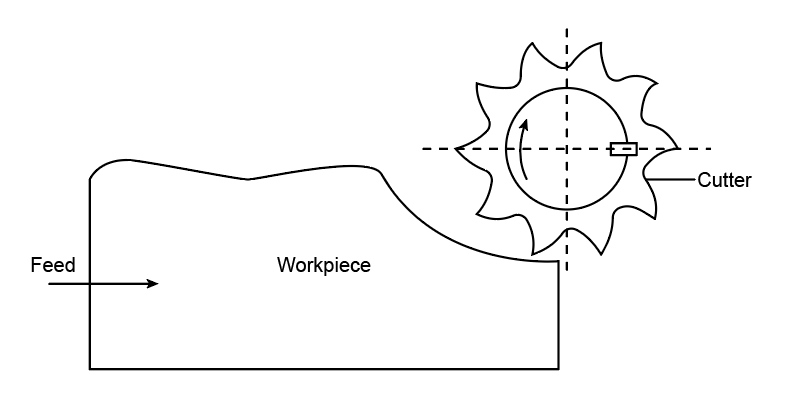
Grinding machine
In grinding machines, an abrasive wheel is utilized to eliminate material from the workpiece. Some grinding machine members are the base, table, abrasive wheel, wheel head, and column. Types of grinding machines are surface grinding, cylindrical grinding, jig grinding, and gear grinding.
Shaper and planer machine
The shaper and planer machine utilizes straight movement among jobs and cutting tools for removing material. Some of the shaper machine components are base, ram, tool head, table, column, stroke adjuster, and clapper box. Various machining operations performed in shaper machines are horizontal or vertical cutting, inclined cutting, and irregular cutting.
The diagram of the shaper machine is given below:
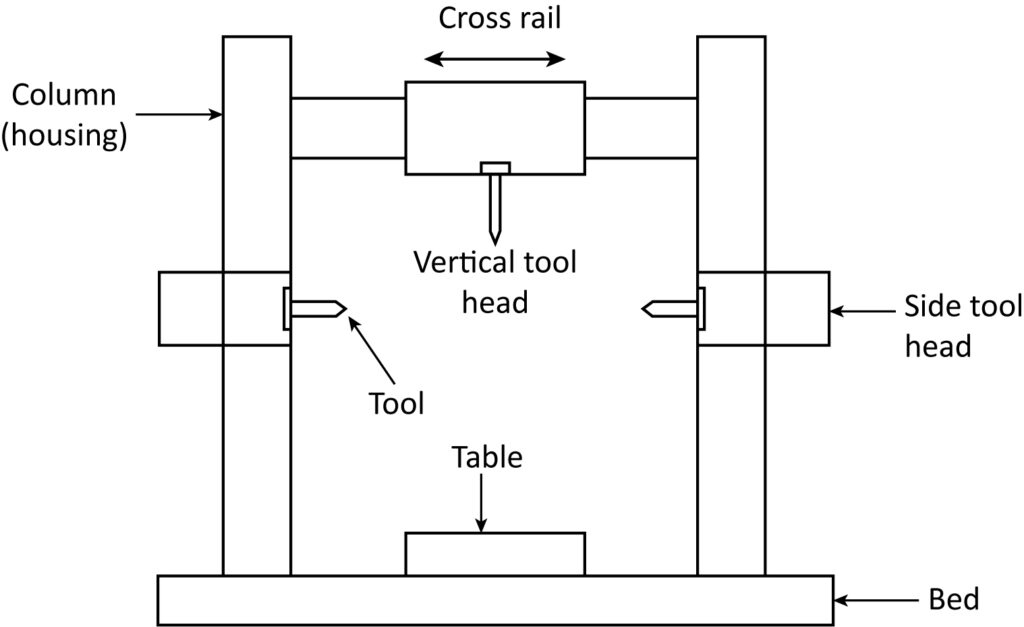
Common Mistakes
- Students get confused between the drilling process and the boring process because both of them are somehow similar machining operations. However, they are two different processes because, in drilling, a hole is originated on a surface, whereas in boring, the hole is enlarged.
- Shaper and planer machines also create misconceptions among students. The shaper machine is utilized for smaller workpieces, whereas the planer machine is being used for large workpieces.
Context and Applications
The topic machining processes and machine tools are very much significant in the several professional exams and courses for undergraduate, Diploma level, graduate, postgraduate. For example:
- Bachelors of Technology in Mechanical Engineering
- Bachelors of Technology in Civil Engineering
- Masters in Technology in Mechanical Engineering
- Doctor of Philosophy in Mechanical Engineering
- Diploma in Mechanical Engineering
Related Concepts
- CNC machining
- Drilling operations and milling operations
- Numerical control
- CNC machining process
- Types of milling cutter
- Examples of machine tools
- Electro-chemical machining (ECM), Broaching and fabricating
- Ultrasonic and additive manufacturing
- Forging and its wide variety
- Single-point tool
- Conventional machining
- Drill press and drill bits
Practice Problems
Q1. Which of the surface is obtained through surface grinding?
a. Cylindrical holes
b. Tapered surface
c. Flat surface
d. Inclined surface
Correct answer: (c)
Explanation: The grinding process is defined as a metal removing process in which grinding wheels are applied over a workpiece to remove the extra material. Flat or tubular surfaces are obtained by grinding operations.
Q2. In order to remove the drill and socket, which of the given tool is applied?
a. Drill drawer
b. Drill puller
c. Both options (a) and (b)
d. None of the above
Correct answer: (d)
Explanation: Drill drift is a tool used to remove the drill and socket. In contrast, a drill puller is used to make a drill over a surface. A drill puller is also commonly named as a drill bit.
Q3. Which of the following process is utilized for developing quality screw threads?
b. Thread cutting
a. Thread milling
c. Thread chasing
d. Both (a) and (b)
Correct answer: (c)
Explanation: Thread chasing is a very precise operation used to produce high-quality screw threads. The tool used in thread chasing is named as the chaser.
Q4. What kind of surfaces are produced by engine lathe in turning operation?
a. Flat surfaces
b. Cylindrical surfaces
c. None of these
d. All of the above
Correct answer: (b)
Explanation: The turning operation is used to produce cylindrical surfaces on a lathe machine. In turning operation, the workpiece is rotated about the fixed axis, and the cutting tool is moved over the workpiece piece surface.
Q5. In shaper machine, the clamper box is a part of __________.
a. Tool slide
b. Ram
c. Column
d. None of these
Correct answer: (d)
Explanation: The shaper machine utilizes straight movement over the jobs with cutting tools to remove material. The various components of the shaper machine are base, ram, tool head, table, column, stroke adjuster, and clapper box.
Want more help with your mechanical engineering homework?
*Response times may vary by subject and question complexity. Median response time is 34 minutes for paid subscribers and may be longer for promotional offers.
Search. Solve. Succeed!
Study smarter access to millions of step-by step textbook solutions, our Q&A library, and AI powered Math Solver. Plus, you get 30 questions to ask an expert each month.
Manufacturing Engineering and Technology
Manufacturing Processes
Machining Processes and Machine Tools
Machining Processes and Machine Tools Homework Questions from Fellow Students
Browse our recently answered Machining Processes and Machine Tools homework questions.
Search. Solve. Succeed!
Study smarter access to millions of step-by step textbook solutions, our Q&A library, and AI powered Math Solver. Plus, you get 30 questions to ask an expert each month.