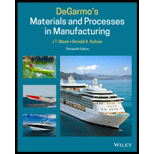
Degarmo's Materials And Processes In Manufacturing
13th Edition
ISBN: 9781119492825
Author: Black, J. Temple, Kohser, Ronald A., Author.
Publisher: Wiley,
expand_more
expand_more
format_list_bulleted
Concept explainers
Textbook Question
Chapter 27, Problem 19RQ
For a given job, how would a broach having rotor-tooth design compare in length with one having regular, full-width teeth?
Expert Solution & Answer

Want to see the full answer?
Check out a sample textbook solution
Students have asked these similar questions
Temperature (°C)
100
4. Consider the solidification of a binary Pb-10%Sn alloy. Assume that during solidification,
there is complete mixing in the liquid and no diffusion in the solid. Use the phase diagram
below to answer the following question.
(a)
Draw (on the phase diagram) the compositions of the liquid and the solid at the
interface as a function of temperature during solidification.
(b) Illustrate on the phase diagram how one would calculate the volume fraction solidified
at a given temperature.
(c)
(d)
Indicate the temperature at which solidification is complete.
Do you expect ẞ to be present in the as-cast microstructure? Explain
300
327°C
200
a
(Pb)
20
20
a + L
18.3
183°C
α + β
40
60
Composition (wt% Sn)
Liquid
600
500
232°C
B+L
400
B
61.9
97.8
300
808
100
(Sn)
200
100
Temperature (°F)
I tried this problem a couple of times and don't know where I'm going wrong can you help me out please
y(0)=1,
Using Laplace transforms solve the following differential
equations :
11) y"-4y+4y=0,
12) y+2y+2y=0,
y(0)=2.1,
y'(0) = 3.9
y'(0)=-3.
13) y+7y+12y=21e",
y(0)=3.5,
y'(0)=-10.
14) +9y=10e.
y(0)=0,
y'(0) = 0.
15) y+3y+2.25y=91³ +64,
y(0)=1,
y'(0) = 31.5
16) -6y+5y= 29 cos(21),
y(0)=3.2,
y'(0)=6.2
17) "+2y+2y=0,
y(0)=0,
y'(0)=1.
18) +2y+17y=0,
y(0)=0,
y'(0)=12.
19) y-4y+5y=0,
y(0)=1,
y'(0) = 2.
20) 9y-6y+y=0,
y(0)=3,
y'(0)=1.
21) -2y+10y=0,
y(0)=3,
y'(0)=3.
Chapter 27 Solutions
Degarmo's Materials And Processes In Manufacturing
Ch. 27 - Why is sawing one of the most efficient of the...Ch. 27 - Explain why tooth spacing (pitch) is important in...Ch. 27 - What is the tooth gullet used for on a saw blade?Ch. 27 - Explain what is meant by the set of the teeth on a...Ch. 27 - How is tooth set related to saw kerf?Ch. 27 - Why can a bandsaw blade not be hardened throughout...Ch. 27 - What are the advantages of using circular saws?Ch. 27 - Why have bandsawing machines largely replaced...Ch. 27 - Explain how the hole in Figure 27.7 is made on a...Ch. 27 - How would you calculate or estimate Tm for a...
Ch. 27 - What is the disadvantage of using gravity to feed...Ch. 27 - What is unique about the broaching process...Ch. 27 - Can a thick saw blade be used as a broach? Why or...Ch. 27 - Broaching machines are simpler in a basic design...Ch. 27 - Why is broaching particularly well-suited for mass...Ch. 27 - In designing a broach, what would be the first...Ch. 27 - Why is it necessary to relate the design of a...Ch. 27 - What two methods can be utilized to reduce the...Ch. 27 - For a given job, how would a broach having...Ch. 27 - Why are the pitch and radius of the gullet between...Ch. 27 - Why are broaching speeds usually relatively low,...Ch. 27 - What are the advantages of shell-type broach...Ch. 27 - Why are most broaches made from alloy or...Ch. 27 - What are the advantages of TiN-coated broaching...Ch. 27 - For mass-production operations, which process is...Ch. 27 - What is the difference between the roughing teeth...Ch. 27 - The sides of a square, blind hole must be machined...Ch. 27 - The interior, flat surfaces of socket wrenches,...Ch. 27 - Prob. 29RQCh. 27 - What are some ways to improve the efficiency of a...Ch. 27 - To what extent is filing different from sawing?Ch. 27 - Prob. 32RQCh. 27 - Prob. 33RQCh. 27 - Prob. 34RQCh. 27 - A surface 12 in. long is to be machined with a...Ch. 27 - The pitch of the teeth on a simple surface broach...Ch. 27 - Estimate the (approximate maximum) horsepower...Ch. 27 - Estimate the approximate force acting in the...Ch. 27 - In cutting a 6-in.-long slot in a piece of AISI...Ch. 27 - The strength of a pull broach is determined by its...Ch. 27 - Suppose you want to shape a block of metal 7 in....Ch. 27 - Could you have saved any time in Problem 7 by...Ch. 27 - Derive the equation for shaping cutting speed.Ch. 27 - How many strokes per minute would be required to...Ch. 27 - How much time would be required to shape a flat...Ch. 27 - What is the metal removal rate in Problem 11 if...Ch. 27 - Suppose you decide to mill the flat surface...Ch. 27 - A planer has a 10-hp motor, and 75% of the motor...
Additional Engineering Textbook Solutions
Find more solutions based on key concepts
Look at the following pseudocode class definitions: Class Vegetable Public Module message () Display Im a veget...
Starting Out with Programming Logic and Design (5th Edition) (What's New in Computer Science)
Why are constructors useful for performing start-up operations?
Starting Out with Java: From Control Structures through Objects (7th Edition) (What's New in Computer Science)
What is an algorithm?
Starting Out With Visual Basic (8th Edition)
Distinguish among data definition commands, data manipulation commands, and data control commands.
Modern Database Management
What is the purpose of a DBMS?
Database Concepts (8th Edition)
Porter’s competitive forces model: The model is used to provide a general view about the firms, the competitors...
Management Information Systems: Managing The Digital Firm (16th Edition)
Knowledge Booster
Learn more about
Need a deep-dive on the concept behind this application? Look no further. Learn more about this topic, mechanical-engineering and related others by exploring similar questions and additional content below.Similar questions
- 4. Consider the rectangulan 2535 Let 16 a and section discussed 977b + class. in ie make a M thin" rectangle, Can you you show that Q = Go {a² = x² } . Imax = 2 Ga ты J =arrow_forward1. Consider a circular shaft in torsion that of radius r=b has a key way as shown, circle of radius a Let us try the solution x₁ (5,0) = k (6² = r²) (1- 2 awso 1.1 Does this solve the problem for the stres rer 1,2 Solve for is and 23.arrow_forward3. - a For an elliptical cross that the tangent to section resultant shear can you s stress is show ellipse with the same 24 i ratio of eccentricity, in passes through to point alb that in question, it + Parrow_forward
- 2. Consider the rod with an elliptical that strain 4 a Cross secton considered in class, Integrate the was displacement displacements, relations to obtain thearrow_forwardPlease answer Oxygen at 300 kPa and 90°C flowing at an average velocity of 3 m/s is expanded in an adiabatic nozzle. What is the maximum velocity of the oxygen at the outlet of this nozzle when the outlet pressure is 60 kPa? Use the table containing the ideal gas specific heats of various common gases. The maximum velocity of the oxygen at the outlet of this nozzle is 532.5 Numeric ResponseEdit Unavailable. 532.5 incorrect.m/s.arrow_forwardA container filled with 70 kg of liquid water at 95°C is placed in a 90-m3 room that is initially at 12°C. Thermal equilibrium is established after a while as a result of heat transfer between the water and the air in the room. Assume the room is at the sea level, well sealed, and heavily insulated. NOTE: This is a multi-part question. Once an answer is submitted, you will be unable to return to this part. Determine the amount of heat transfer between the water and the air in the room. The amount of heat transfer between the water and the air in the room is kJ.arrow_forward
- A strain gauge rosette that is attached to the surface of a stressed component gives 3 readings (ɛa = A, b = B, &c = C). If the strain gauge rosette is of the D° type (indicating the angle between each of the gauges), construct a Mohr's Strain Circle overleaf. You should assume that gauge A is aligned along the x-axis. Using the Mohr's Strain Circle calculate the: (i) principal strains (ε1, 2)? (ii) principal angles (1, 2)? You should measure these anticlockwise from the y-axis. (iii) maximum shear strain in the plane (ymax)?arrow_forwardQ1. If the yield stress (σy) of a material is 375MPa, determine whether yield is predicted for the stresses acting on both the elements shown below using: (a) Tresca Criterion (b) Von Mises Criterion P Element A R S Element B Note: your values for P (vertical load on Element A) should be negative (i.e. corresponding to a compressive vertical load).arrow_forwardQ. After a puncture a driver is attempting to remove a wheel nut by applying a force of P KN to one end of a wheel brace as shown in Fig. 1. In cross-section the brace is a hollow steel tube (see section aa) of internal diameter r mm and external diameter q mm. wheel nut n Position S P m r q Section aa Fig, 1 (a) Calculate (i) the twisting moment, (ii) the bending moment, and (iii) the shear force in the brace at position S due to the applied load P. (b) Calculate (i) the shear stress due to twisting, and (ii) the bending stress at position S. Note that the shear force will not produce any shear stress at S. (c) Calculate the maximum shearing stress in the brace at position S using the Maximum Shear Stress Criterion. 2 Mechanics of Materials 2 Tutorials Portfolio: Exercise 5 (d) If the maximum permissible shear stress in the steel is 200 MPa, determine the maximum torque that can be applied by the brace without the risk of failure at S.arrow_forward
- Calculate the first 5 Fourier series coefficients (A0-4 and B1-5 ) for the estimated R wave.arrow_forwardRefrigerant-134a is expanded isentropically from 600 kPa and 70°C at the inlet of a steady-flow turbine to 100 kPa at the outlet. The outlet area is 1 m2, and the inlet area is 0.5 m2. Calculate the inlet and outlet velocities when the mass flow rate is 0.65 kg/s. Use the tables for R-134a. The inlet velocity is m/s. The outlet velocity is m/s.arrow_forwardA container filled with 70 kg of liquid water at 95°C is placed in a 90-m3 room that is initially at 12°C. Thermal equilibrium is established after a while as a result of heat transfer between the water and the air in the room. Assume the room is at the sea level, well sealed, and heavily insulated. NOTE: This is a multi-part question. Once an answer is submitted, you will be unable to return to this part. Determine the final equilibrium temperature. Use the table containing the ideal gas specific heats of various common gases. The final equilibrium temperature is °C.arrow_forward
arrow_back_ios
SEE MORE QUESTIONS
arrow_forward_ios
Recommended textbooks for you
- Precision Machining Technology (MindTap Course Li...Mechanical EngineeringISBN:9781285444543Author:Peter J. Hoffman, Eric S. Hopewell, Brian JanesPublisher:Cengage Learning
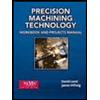
Precision Machining Technology (MindTap Course Li...
Mechanical Engineering
ISBN:9781285444543
Author:Peter J. Hoffman, Eric S. Hopewell, Brian Janes
Publisher:Cengage Learning
The Most Common Metal Machining Processes (Metal Machining Video 1); Author: Sofeast Ltd;https://www.youtube.com/watch?v=uxVJ3qtezGw;License: Standard YouTube License, CC-BY
Machining process and Machine Tools; Author: Amar Gandhi;https://www.youtube.com/watch?v=X2mUJ8baaE0;License: Standard Youtube License