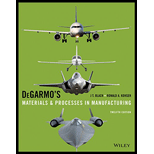
DeGarmo's Materials and Processes in Manufacturing
12th Edition
ISBN: 9781118987674
Author: J. T. Black, Ronald A. Kohser
Publisher: WILEY
expand_more
expand_more
format_list_bulleted
Concept explainers
Textbook Question
Chapter 21, Problem 11RQ
For orthogonal machining, the cutting edge radius is assumed to be small compared to the uncut chip thickness. Why?
Expert Solution & Answer

Want to see the full answer?
Check out a sample textbook solution
Students have asked these similar questions
Following are the data in an orthogonal cutting
operation.
Rake angle = 15°
Cutting speed = 20 m/min
Chip thickness = 0.7 mm
Width of cut = 4.5 mm
Cutting ratio = 0.714
Assuming Merchant's theory, coefficient of friction at
the tool-chip interface is
Make a figure and explain how shear plane angle effect the power
requirements in the machining. How can you reduce the power
requirements during machining in orthogonal cutting?
What is surface roughness?
Surface finish is one of the most important measures for determining the quality of products in machining. Explain in some details.
Chapter 21 Solutions
DeGarmo's Materials and Processes in Manufacturing
Ch. 21 - Why has the metal-cutting process resisted...Ch. 21 - What variables must be considered in understanding...Ch. 21 - Which of the seven basic chip formation processes...Ch. 21 - How is feed related to speed in the machining...Ch. 21 - Before you select speed and feed for a machining...Ch. 21 - Milling has two feeds. What are they, and which...Ch. 21 - What is the fundamental mechanism of chip...Ch. 21 - What is the difference between oblique machining...Ch. 21 - What are the implications of Figure 21.13, given...Ch. 21 - Note that the units for the approximate equation...
Ch. 21 - For orthogonal machining, the cutting edge radius...Ch. 21 - How do the magnitude of the strain and strain rate...Ch. 21 - Why is titanium such a difficult metal to machine?...Ch. 21 - Explain why you get segmented or discontinuous...Ch. 21 - Why is metal cutting shear stress such an...Ch. 21 - Which of the three cutting forces in oblique...Ch. 21 - How is the energy in a machining process typically...Ch. 21 - Where does the energy consumed in metal cutting...Ch. 21 - What are two ways of estimating the primary...Ch. 21 - What are the three different ways to perform...Ch. 21 - Why does the cutting force Fc increase with...Ch. 21 - Why doesnt the cutting force Fc increase with...Ch. 21 - Prob. 23RQCh. 21 - How does the selection of the machining parameters...Ch. 21 - Suppose you had a machining operation (boring)...Ch. 21 - Make a sketch like that shown in Figure 21.1 with...Ch. 21 - Show how you would do near orthogonal machining in...Ch. 21 - Can you do orthogonal machining on a shaper or...Ch. 21 - What process and material combination would yield...Ch. 21 - What is meant by the statement that machining...Ch. 21 - Prob. 31RQCh. 21 - Figure 21.4 provides suggested cutting speeds and...Ch. 21 - For problem 1, suppose you selected a speed of 145...Ch. 21 - If the cutting forces is 1000 lb calculate the...Ch. 21 - Explain how you would estimate the cutting force...Ch. 21 - For a turning operation, you have selected a...Ch. 21 - For a slab milling operation using a...Ch. 21 - The power required to machine metal is related to...Ch. 21 - In order to drill a hole in the material described...Ch. 21 - Suppose you have the data in Table 21.A obtained...Ch. 21 - Calculate the horsepower that a process is going...Ch. 21 - Explain how you would estimate the cutting force...Ch. 21 - Derive equations for F and N using the circular...Ch. 21 - Prob. 14PCh. 21 - Prob. 15PCh. 21 - A manufacturing engineer needs an estimate of the...Ch. 21 - Using Figure 21.4 for input data, determine the...Ch. 21 - Estimate the horsepower needed to remove metal at...Ch. 21 - For a turning process, the horsepower required was...
Additional Engineering Textbook Solutions
Find more solutions based on key concepts
A piston/cylinder arrangement with a linear spring similar to Fig. P3.33 contains R-134a at 60 F, x=0.6 and a v...
Fundamentals Of Thermodynamics
The rigid beam is supported by the three suspender bars. Bars AB and EF are made of aluminum and bar CD is made...
Mechanics of Materials (10th Edition)
24. If we increase the temperature in a reactor by 90 degrees Fahrenheit [°F], how many degrees Celsius [°C] wi...
Thinking Like an Engineer: An Active Learning Approach (3rd Edition)
Water at 15C is flowing downward in a vertical tube 7.5m long. The pressure is 550kPa at the top and 585kPa at ...
Applied Fluid Mechanics (7th Edition)
The onset of turbulence in a gas flowing within a circular tube occurs at ReD,c2300 , while a transition from i...
Fundamentals of Heat and Mass Transfer
5.23 Using the method of sections, determine the forces in members BD and BE of the truss shown.
Applied Statics and Strength of Materials (6th Edition)
Knowledge Booster
Learn more about
Need a deep-dive on the concept behind this application? Look no further. Learn more about this topic, mechanical-engineering and related others by exploring similar questions and additional content below.Similar questions
- In an orthogonal machining with a tool of 9 degree orthogonal rake angle, the uncut chip thickness is 0.2mm. The chip thickness fluctuates between 0.25 mm and 0.4 mm. The ratio of the maximum shear angle to the minimum shear angle during machining isarrow_forwardIn orthogonal machining operation the chip thickness and the uncut chip thickness are equal to 0.45 mm. If the tool rake and is 0 deg. What is the shear plane angle?arrow_forwardAssume that, in orthogonal cutting, the rake angle is 20 and the friction angle is 35 at thechip-tool interface. Determine the percentage change in chip thickness when the frictionangle is 50. Note that Merchant’s equation is more preferable.arrow_forward
- (b) An orthogonal cutting operation is being carried out under the following conditions: depth of cut, to = 0.1 mm, chip thickness, to = 0.2 mm, width of cut = 4 mm, cutting speed, v = 3 m/s, rake angle, a = 10°, Cutting force, Fc = 500 N, and Thrust force, F1= 200 N. Calculate the percentage of the total energy that is dissipated in the shear plane of cutting process.arrow_forwardMake a figure and explain how shear plane angle effect the power requirements in the machining. How can you reduce the power requirements during machining in orthogonal cutting? plzz do it in 45 minutesarrow_forwardwhat are the three basic parameters (cutting variables) in the machining process? how to calculate themarrow_forward
- In an orthogonal machining with a tool of 9 orthogonal rake angle, the uncut chip thickness is 0.2 mm. The chip thickness fluctuates between 0.25 mm and 0.4 mm. The ratio of the maximum shear angle to the minimum shear angle during machining isarrow_forwardThe orthogonal cutting of steel is done with 10° rake tool with a depth of cut of 4mm feed rate of 0.4mm/rev. The cutting speed is 200m/min. The chip thickness ratio is 0.35. The vertical cutting force is 1200N and the horizontal cutting force is 700N. Calculate from the Merchant's theory, the various work done in metal cutting and shear stress.arrow_forwardA 600mm*30mm flat surface of a plate is to be finish machined on a shaper .The plate has been fixed with 600 mm side along the tool travel direction. If the tool over-travel at each end of the plate is 20 mm, average cutting speed is 8 m/min, feed rate is 0.3 mm/stroke and the ratio of return time to cutting time of the tool is 1:2 Determine time required for machining?arrow_forward
- In an orthogonal turning process, the chip thickness is 0.32 mm , feed is 0.2 mm/rev, then calculate the cutting ratio.arrow_forwardIn a turning operation, the workpiece diameter is Dm=44.00 mm and the diameter after the operation should be 22.00 mm. The cutting speed is set to 105.00 m/min and the federate is 0.03 mm/rev. Calculate the material 3 removal rate (Cm²Imin) for this operation (Do not input units). Your Answer: Answerarrow_forwardI need the answer as soon as possiblearrow_forward
arrow_back_ios
SEE MORE QUESTIONS
arrow_forward_ios
Recommended textbooks for you
- Elements Of ElectromagneticsMechanical EngineeringISBN:9780190698614Author:Sadiku, Matthew N. O.Publisher:Oxford University PressMechanics of Materials (10th Edition)Mechanical EngineeringISBN:9780134319650Author:Russell C. HibbelerPublisher:PEARSONThermodynamics: An Engineering ApproachMechanical EngineeringISBN:9781259822674Author:Yunus A. Cengel Dr., Michael A. BolesPublisher:McGraw-Hill Education
- Control Systems EngineeringMechanical EngineeringISBN:9781118170519Author:Norman S. NisePublisher:WILEYMechanics of Materials (MindTap Course List)Mechanical EngineeringISBN:9781337093347Author:Barry J. Goodno, James M. GerePublisher:Cengage LearningEngineering Mechanics: StaticsMechanical EngineeringISBN:9781118807330Author:James L. Meriam, L. G. Kraige, J. N. BoltonPublisher:WILEY
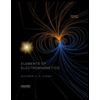
Elements Of Electromagnetics
Mechanical Engineering
ISBN:9780190698614
Author:Sadiku, Matthew N. O.
Publisher:Oxford University Press
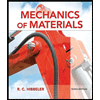
Mechanics of Materials (10th Edition)
Mechanical Engineering
ISBN:9780134319650
Author:Russell C. Hibbeler
Publisher:PEARSON
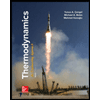
Thermodynamics: An Engineering Approach
Mechanical Engineering
ISBN:9781259822674
Author:Yunus A. Cengel Dr., Michael A. Boles
Publisher:McGraw-Hill Education
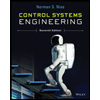
Control Systems Engineering
Mechanical Engineering
ISBN:9781118170519
Author:Norman S. Nise
Publisher:WILEY
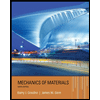
Mechanics of Materials (MindTap Course List)
Mechanical Engineering
ISBN:9781337093347
Author:Barry J. Goodno, James M. Gere
Publisher:Cengage Learning
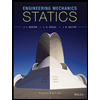
Engineering Mechanics: Statics
Mechanical Engineering
ISBN:9781118807330
Author:James L. Meriam, L. G. Kraige, J. N. Bolton
Publisher:WILEY
The Most Common Metal Machining Processes (Metal Machining Video 1); Author: Sofeast Ltd;https://www.youtube.com/watch?v=uxVJ3qtezGw;License: Standard YouTube License, CC-BY
Machining process and Machine Tools; Author: Amar Gandhi;https://www.youtube.com/watch?v=X2mUJ8baaE0;License: Standard Youtube License