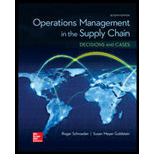
OPERATIONS MANAGEMENT IN THE SUPPLY CHAIN: DECISIONS & CASES (Mcgraw-hill Series Operations and Decision Sciences)
7th Edition
ISBN: 9780077835439
Author: Roger G Schroeder, M. Johnny Rungtusanatham, Susan Meyer Goldstein
Publisher: McGraw-Hill Education
expand_more
expand_more
format_list_bulleted
Concept explainers
Textbook Question
Chapter 14, Problem 5P
The famous Widget Company sells widgets at the rate of 80,000 units per year. Each widget sells for $100, and it costs 30 percent to carry widgets in inventory for a year. The process of widget production has been automated over the years, and it now costs $1000 to change over the widget production line to other products that are made on the same line.
- a. What is the economical lot size for the production of widgets?
- b. How many lots will be produced each year?
- c. What are the annual cost of carrying widgets and the annual cost of changeover?
- d. What factors or changes in assumptions might cause the Widget Company to produce a larger lot than the economic lot size calculated in part a?
Expert Solution & Answer

Want to see the full answer?
Check out a sample textbook solution
Students have asked these similar questions
The average expense of keeping inventory for an integrated circuit producer is 48 percent.What inventory keeping expense (in $) does an object cost $300 and has an estimated one-month inventory supply?
6000 units of a part are needed every year. Currently, this part is manufactured internally. Each production run costs 500 dollars to set up. The part costs 5 dollars. The carrying cost is 10% per year. The company has the option of ordering this part from another company. This would increase the part’s cost to 6 dollars, although the fixed cost of ordering would be low at 300 dollars per order. Should the company continue manufacturing the part, or order it? Show your calculations.
Give typing answer with explanation and conclusion
Chapter 14 Solutions
OPERATIONS MANAGEMENT IN THE SUPPLY CHAIN: DECISIONS & CASES (Mcgraw-hill Series Operations and Decision Sciences)
Ch. 14.S - eXcel Suppose that for problem 1 in the chapter,...Ch. 14.S - Prob. 2PCh. 14.S - For problem 2 in the chapter, suppose the Grinell...Ch. 14.S - A producer of electronic parts wants to take...Ch. 14 - Identify the different types of inventories (raw...Ch. 14 - Why are stockout costs difficult to determine?...Ch. 14 - What is the difference between a requirements...Ch. 14 - Compare and contrast the management of finished...Ch. 14 - For a given service level, why does a P system...Ch. 14 - Under what circumstances might CPFR be useful, and...
Ch. 14 - Prob. 7DQCh. 14 - What is the appropriate role of inventory turnover...Ch. 14 - Suppose you are managing a chain of retail...Ch. 14 - The Always Fresh Grocery Store carries a...Ch. 14 - The Grinell Machine Shop makes a line of metal...Ch. 14 - The local Toyota dealer has to decide how many...Ch. 14 - Prob. 4PCh. 14 - The famous Widget Company sells widgets at the...Ch. 14 - Prob. 6PCh. 14 - Prob. 7PCh. 14 - An electronics retailer carries a particular...Ch. 14 - An electronics retailer carries a particular...Ch. 14 - The local Toyota dealer has to decide how many...Ch. 14 - The Suregrip Tire Company carries a certain type...Ch. 14 - The Suregrip Tire Company carries a certain type...Ch. 14 - eXcel 13. The Cover-up Drapery Company carries...Ch. 14 - Suppose you are the supplier of the Cover-up...
Knowledge Booster
Learn more about
Need a deep-dive on the concept behind this application? Look no further. Learn more about this topic, operations-management and related others by exploring similar questions and additional content below.Similar questions
- The demand for a particular part called SKU 005 is 1,500 units a year. The cost of one SKU 005 is $64.00. It costs $60.00 to place an order SKU 005, and the user of SKU 005 has a per year inventory carrying cost of 25% of unit cost. Assume that there are 250 working days in the year where SKU 005 is used. Once the purchasing manager for SKU 005 places an order, it always takes the vendor 5 working days to deliver that order. What should the purchasing manager’s reorder point be? ) A. 12 ОВ. 30 Ос. 36 O D. 24 O E. 5arrow_forwardWhich of the following is an element of inventory holding costs? All of these are elements of inventory holding costs. investment costs housing costs material handling costs pilferage, scrap, and obsolescencearrow_forwardFerdows Electronics, Inc. (FEI), produces short runsof custom microwave radios for railroads and other industrial clients.You have been asked to reduce inventory by introducing akanban system. After several hours of analysis, you develop thefollowing data for connectors used in one work cell. How manykanbans do you need for this connector? ~Daily demand = l ,500 radiosProduction lead time = l daySafety stock = l /2 dayKanban size = 250 radiosarrow_forward
- The demand for a particular part called SKU 005 is 1,200 units a year. The cost of one SKU 005 is $40.00. It costs $60.00 to place an order SKU 005, and the user of SKU 005 has a per year inventory carrying cost of 25% of unit cost. Assume that there are 250 working days in the year where SKU 005 is used. Once the purchasing manager for SKU 005 places an order, it always takes the vendor 5 working days to deliver that order. What should the purchasing manager's reorder point be? O A. 24 O B. 36 O C. 30 O D. 5 O E. 12arrow_forwardAn integrated circuit manufacturer’s annual cost of holding inventory is 48 percent.What inventory holding cost (in $) does it incur for an item that costs $300 and has aone-month supply of inventory on average?arrow_forwardIn the A-B-C classification system, items which account for sixty percent of the total dollar-volume for few inventory items would be classified as: O a) A items b) B items c) C items d) e) B items plus C items A items plus B itemsarrow_forward
- Please select the item that is NOT a cost associated with inventory Holding or carrying costs Insurance to protect inventory Interest costs on the money invested in equipment and raw materials. Depreciation Storage facilities Taxes (in some states)arrow_forwardIn inventory management, high holding costs calls for high inventory levels. A.True B.Falsearrow_forwardThe management of two different-sized sachets of maize meal—5 kg and 3 kg—is entrusted to you. The larger sachet is priced at R45 and the smaller one is R30, according to Shoprite your primary supplier. Currently, the promotion for the smaller packet says, "Buy ONE get the second HALF PRICE!" Propose which size of Sugar currently gives you the best value for money.what is the annual demand of Maize Meal = 750 units (bigger size), Delivered purchase cost = R35/units, Annual carrying cost percentage= 25 percent, Order cost = R50/order. The lead time is 10 working days. Assuming 20 working days per month. Determine the Economic Order QuantityDetermine the reorder pointDetermine the average inventorySuppose orders are placed only at review time. what is the optimal period and the optimal order quantity.arrow_forward
- Annual purchasing salaries are $65,000, operating expenses for the purchasingdepartment are $25,000, and inspecting and receiving costs are $25 per order. If thepurchasing department places 9000 orders a year, what is the average cost of ordering? What is the annual cost of ordering?arrow_forwardPlease do not give solution in image format thankuarrow_forwardWhich of the following is not a category of inventory? O A. Raw Materials B. Work-In-Process (WIP) C. Maintenance, Repair, and Operating Supplies (MRO). OD. All of the above are categories of inventoryarrow_forward
arrow_back_ios
SEE MORE QUESTIONS
arrow_forward_ios
Recommended textbooks for you
- Practical Management ScienceOperations ManagementISBN:9781337406659Author:WINSTON, Wayne L.Publisher:Cengage,Operations ManagementOperations ManagementISBN:9781259667473Author:William J StevensonPublisher:McGraw-Hill EducationOperations and Supply Chain Management (Mcgraw-hi...Operations ManagementISBN:9781259666100Author:F. Robert Jacobs, Richard B ChasePublisher:McGraw-Hill Education
- Purchasing and Supply Chain ManagementOperations ManagementISBN:9781285869681Author:Robert M. Monczka, Robert B. Handfield, Larry C. Giunipero, James L. PattersonPublisher:Cengage LearningProduction and Operations Analysis, Seventh Editi...Operations ManagementISBN:9781478623069Author:Steven Nahmias, Tava Lennon OlsenPublisher:Waveland Press, Inc.
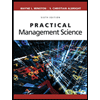
Practical Management Science
Operations Management
ISBN:9781337406659
Author:WINSTON, Wayne L.
Publisher:Cengage,
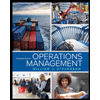
Operations Management
Operations Management
ISBN:9781259667473
Author:William J Stevenson
Publisher:McGraw-Hill Education
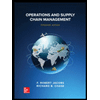
Operations and Supply Chain Management (Mcgraw-hi...
Operations Management
ISBN:9781259666100
Author:F. Robert Jacobs, Richard B Chase
Publisher:McGraw-Hill Education
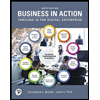
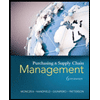
Purchasing and Supply Chain Management
Operations Management
ISBN:9781285869681
Author:Robert M. Monczka, Robert B. Handfield, Larry C. Giunipero, James L. Patterson
Publisher:Cengage Learning
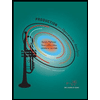
Production and Operations Analysis, Seventh Editi...
Operations Management
ISBN:9781478623069
Author:Steven Nahmias, Tava Lennon Olsen
Publisher:Waveland Press, Inc.
Inventory Management | Concepts, Examples and Solved Problems; Author: Dr. Bharatendra Rai;https://www.youtube.com/watch?v=2n9NLZTIlz8;License: Standard YouTube License, CC-BY