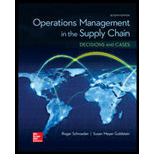
OPERATIONS MANAGEMENT IN THE SUPPLY CHAIN: DECISIONS & CASES (Mcgraw-hill Series Operations and Decision Sciences)
7th Edition
ISBN: 9780077835439
Author: Roger G Schroeder, M. Johnny Rungtusanatham, Susan Meyer Goldstein
Publisher: McGraw-Hill Education
expand_more
expand_more
format_list_bulleted
Concept explainers
Textbook Question
Chapter 14, Problem 2P
The Grinell Machine Shop makes a line of metal tables. Some of these tables are carried in finished goods inventory. A particular table has the following characteristics:
Sales = 300 per year
Setup cost = $1200 per setup (this includes machine setup for all the different parts in the table)
Carrying cost = 20 percent per year
Item cost = $25
- a. How many of these tables should be made in a production lot?
- b. How often will production be scheduled?
- c. What factors might cause the firm to
schedule a lot size different from the one you have computed?
Expert Solution & Answer

Want to see the full answer?
Check out a sample textbook solution
Students have asked these similar questions
The Grinell Machine Shop makes a line of metal tables.Some of these tables are carried in finished goods inventory. A particular table has the following characteristics: Sales = 300 per year Setup cost = $1200 per setup (this includes machine setup for all the different parts in the table) Carrying cost = 20 percent per year Item cost = $25 a. How many of these tables should be made in a production lot? b. How often will production be scheduled? c. What factors might cause the firm to schedule a lot size different from the one you have computed?
The Grinell Machine Shop makes a line of metal tables. Some of these tables are carried in finished goods inventory.A particular table has the following characteristics:Sales = 300 per yearSetup cost = $1200 per setup (this includes machinesetup for all the different parts in the table)Carrying cost = 20 percent per yearItem cost = $25a. How many of these tables should be made in a production lot?b. How often will production be scheduled?c. What factors might cause the firm to schedule a lot size different from the one you have computed?
2
Chapter 14 Solutions
OPERATIONS MANAGEMENT IN THE SUPPLY CHAIN: DECISIONS & CASES (Mcgraw-hill Series Operations and Decision Sciences)
Ch. 14.S - eXcel Suppose that for problem 1 in the chapter,...Ch. 14.S - Prob. 2PCh. 14.S - For problem 2 in the chapter, suppose the Grinell...Ch. 14.S - A producer of electronic parts wants to take...Ch. 14 - Identify the different types of inventories (raw...Ch. 14 - Why are stockout costs difficult to determine?...Ch. 14 - What is the difference between a requirements...Ch. 14 - Compare and contrast the management of finished...Ch. 14 - For a given service level, why does a P system...Ch. 14 - Under what circumstances might CPFR be useful, and...
Ch. 14 - Prob. 7DQCh. 14 - What is the appropriate role of inventory turnover...Ch. 14 - Suppose you are managing a chain of retail...Ch. 14 - The Always Fresh Grocery Store carries a...Ch. 14 - The Grinell Machine Shop makes a line of metal...Ch. 14 - The local Toyota dealer has to decide how many...Ch. 14 - Prob. 4PCh. 14 - The famous Widget Company sells widgets at the...Ch. 14 - Prob. 6PCh. 14 - Prob. 7PCh. 14 - An electronics retailer carries a particular...Ch. 14 - An electronics retailer carries a particular...Ch. 14 - The local Toyota dealer has to decide how many...Ch. 14 - The Suregrip Tire Company carries a certain type...Ch. 14 - The Suregrip Tire Company carries a certain type...Ch. 14 - eXcel 13. The Cover-up Drapery Company carries...Ch. 14 - Suppose you are the supplier of the Cover-up...
Knowledge Booster
Learn more about
Need a deep-dive on the concept behind this application? Look no further. Learn more about this topic, operations-management and related others by exploring similar questions and additional content below.Similar questions
- 19) In which technique of material control, materials constitute small percentage of total items, but their value is high? a. EOQ technique b. ABC analysis technique c. JIT technique d. Reorder level techniquearrow_forwardThis is in fact a production or operations scheduling system and not an inventory control system. It eliminates the holding of inventory and is based on requiring suppliers to deliver materials of the right quality to the business on the day they are needed and where they are needed.(1) Cyclical‐ordering system.(2) Materials‐requirements planning.(3) Just in time.(4) System of fixed‐order quantities.(5) Quick response system. pick which number fitsarrow_forwardA National chain of type fitters stocks a popular type for which the following information is available. The company operates on 50-week year and Normally operates from Monday to Friday only. Average usage 140 types per day Minimum usage 90 types per day Maximum usage 175 types per day Lead time 10 to 16 days Reorder quality 3000 Cost per types n$1500 Holding cost per unit 3% of unit cost Ordering cost per year n$75.50 Calculate the average level of inventory?arrow_forward
- Xemex has collected the following inventory data for the six items that it stocks: ITEM CODE UNIT COST ($) ANNUAL DEMAND (UNITS) ORDERING COST ($) CARRYING COST AS A PERCENTAGE OF UNIT COST 1 10.60 600 40 20 2 11.00 450 30 25 3 2.25 500 50 15 4 150.00 560 40 15 5 4.00 540 35 16 6 4.10 490 40 17 Lynn Robinson, Xemex’s inventory manager, does not feel that all of the items can be controlled. What ordered quantities do you recommend for which inventory product(s)?arrow_forwardA service garage uses 204 boxes of cleaning cloths a year. The boxes cost $12 each. The cost to place one order is $15, and the cost to hold one box in inventory for a year is $2.40. The EOQ is? a. 156.5 boxes b. 50.5 boxes c. 174.9 boxes d. 40.4 boxesarrow_forward6. The demand for a particular part called SKU 005 is 1,500 units a year. The cost of one SKU 005 is $40.00. It costs $50.00 to place an order for SKU 005, and the user of SKU 005 has a per year inventory carrying cost of 25% of unit cost. Assume 250 working days in the year where SKU 005 is used. (Noteshaper: Scenario #26) а. What is the combined annual holding and ordering cost of an order size of 200 units for SKU 005? b. How many of SKU 005 should be ordered, to minimize combined ordering and holding costs? c. The vendor who sells SKU 005 has just offered a 5% discount for orders of 500 or more. Now how many should be ordered? d. Once the purchasing manager for SKU 005 places an order, the vendor requires 7 working days to deliver that order. What should be the purchasing manager's reorder point?arrow_forward
- A National chain of type fitters stocks a popular type for which the following information is available. The company operates on 50-week year and Normally operates from Monday to Friday only. Average usage 140 types per day Minimum usage 90 types per day Maximum usage 175 types per day Lead time 10 to 16 days Reorder quality 3000 Cost per types n$1500 Holding cost per unit 3% of unit cost Ordering cost per year n$75.50 Calculate the ordinary coat based on the current reorder quantity?arrow_forwardFisk Corporation is trying to improve its inventory control system and has installed an online computer at its retail stores. Fisk anticipates sales of 48,400 units per year, an ordering cost of $3 per order, and carrying costs of $1.50 per unit. a. What is the economic ordering quantity? _____________Units b. How many orders will be placed during the year? _____________Orders c. What will the average inventory be? ____________Units d. What is the total cost of ordering and carrying inventory? $__________arrow_forwardNico's Manufacturing uses 2,400 units of a product per year on a continuous basis. The product carrying costs are $60 per year and ordering costs are $250 per order. It takes 20 days to receive a shipment after an order is placed and the firm requires a safety stock of 8 days of usage in inventory. 1. Calculate the economic order quantity (round up to the nearest whole unit) 2. Calculate the total cost per year to order and carry this item. 3. Their supplier has notified the company that if they increase their order quantity by 58 units they will give the company a discount. Calculate the dollar discount that the company will have to at least give to Nico's Manufacturing to be indifferent.arrow_forward
- Cherylene Brown has asked you to help her determine the best ordering policy for a new product. The demand for the new product has been forecasted to be about 1,000 units annually. To help you get a handle on the carrying and ordering costs, Cherylene has given you the list of last year's costs. She thought that these costs might be appropriate for the new product. Cost Factor Taxes for the warehouse Receiving and incoming inspection New product development Acct. dept. costs to pay invoices Inventory insurance Product advertising Spoilage Sending purchasing orders Cost ($) 2,050 1,600 2,500 500 600 800 750 900 Cost Factor Warehouse supplies Research and development Purchasing salaries & wages Warehouse salaries & wages Pilferage of inventory Purchase order supplies Inventory obsolescence Purchasing dept. overhead Cost ($) 300 2,750 30,000 12,800 800 500 300 1,000 She also told you that these data were compiled for 10,000 inventory items that were carried or held during the year. You…arrow_forwardIn ABC inventory analysis, which of the following is FALSE for class A items? Select one: a. Class A items together make up a higher percentage of total inventory value ($) than either class B or class C items. b. Tighter control of class A items (than for class B or class C items) is appropriate. c. It is advisable to manage Class A items using an automated computer system. d. Class A items together make up smaller percentage of inventory items than class C items. e. Class A items individually may have any value ($): small, medium or high.arrow_forwardHh1.arrow_forward
arrow_back_ios
SEE MORE QUESTIONS
arrow_forward_ios
Recommended textbooks for you
- Practical Management ScienceOperations ManagementISBN:9781337406659Author:WINSTON, Wayne L.Publisher:Cengage,Operations ManagementOperations ManagementISBN:9781259667473Author:William J StevensonPublisher:McGraw-Hill EducationOperations and Supply Chain Management (Mcgraw-hi...Operations ManagementISBN:9781259666100Author:F. Robert Jacobs, Richard B ChasePublisher:McGraw-Hill Education
- Purchasing and Supply Chain ManagementOperations ManagementISBN:9781285869681Author:Robert M. Monczka, Robert B. Handfield, Larry C. Giunipero, James L. PattersonPublisher:Cengage LearningProduction and Operations Analysis, Seventh Editi...Operations ManagementISBN:9781478623069Author:Steven Nahmias, Tava Lennon OlsenPublisher:Waveland Press, Inc.
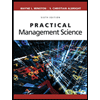
Practical Management Science
Operations Management
ISBN:9781337406659
Author:WINSTON, Wayne L.
Publisher:Cengage,
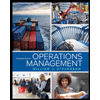
Operations Management
Operations Management
ISBN:9781259667473
Author:William J Stevenson
Publisher:McGraw-Hill Education
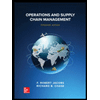
Operations and Supply Chain Management (Mcgraw-hi...
Operations Management
ISBN:9781259666100
Author:F. Robert Jacobs, Richard B Chase
Publisher:McGraw-Hill Education
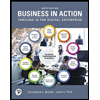
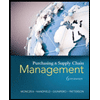
Purchasing and Supply Chain Management
Operations Management
ISBN:9781285869681
Author:Robert M. Monczka, Robert B. Handfield, Larry C. Giunipero, James L. Patterson
Publisher:Cengage Learning
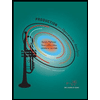
Production and Operations Analysis, Seventh Editi...
Operations Management
ISBN:9781478623069
Author:Steven Nahmias, Tava Lennon Olsen
Publisher:Waveland Press, Inc.
Inventory Management | Concepts, Examples and Solved Problems; Author: Dr. Bharatendra Rai;https://www.youtube.com/watch?v=2n9NLZTIlz8;License: Standard YouTube License, CC-BY