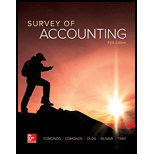
Concept explainers
Problem 6-26A Effects of the level of production on an outsourcing decision
Townsend Chemical Company makes a variety of cosmetic products, one of which is a skin cream designed to reduce the signs of aging. Townsend produces a relatively small amount (15,000 units) of the cream and is considering the purchase of the product from an outside supplier for $9 each. If Townsend purchases from the outside supplier, it would continue to sell and distribute the cream under its own brand name. Townsend’s accountant constructed the following profitability analysis:
Revenue (15,000 units × $20) | $300,000 |
Unit-level materials costs (15,000 units × $2.50) | (37,500) |
Unit-level labor costs (15,000 units × $1,80) | (27,000) |
Unit-level |
(10,500) |
Unit-level selling expenses (15,000 × $1,00) | (15,000) |
Contribution margin | 210,000 |
Skin cream production supervisor’s salary | (75,000) |
Allocated portion of facility-level costs | (45,000) |
Product-level advertising cost | (50,000) |
Contribution to companywide income | $ 40,000 |
Required
- a. Identify the cost items relevant to the make-or-outsource decision.
- b. Should Townsend continue to make the product or buy it from the supplier? Support your answer by determining the change in net income if Townsend buys the cream instead of making it.
- c. Suppose that Townsend is able to increase sales by 10,000 units (sales will increase to 25,000 units). At this level of production, should Townsend make or buy the cream? Support your answer by explaining how the increase in production affects the cost per unit.
- d. Discuss the qualitative factors that Townsend should consider before deciding to outsource the skin cream. How can Townsend minimize the risk of establishing a relationship with an unreliable supplier?
a.

The cost items that is relevant to make-or-outsource decision.
Explanation of Solution
Special order decisions: Special order decisions include circumstances in which the board must choose whether to acknowledge abnormal customer orders. These requests or orders normally necessitate special dispensation or include a demand for lesser price.
Decision making: It is a vital capacity in the management, since decision making is identified with issue, a compelling decision making accomplishes the preferred objectives or goals by taking care of such issues.
The cost items that are relevant to make-or-outsource decision are as follows:
The unit-level costs of creation can be avoided if the Product X is bought. Likewise, it is sensible to accept that the cost the salary of production supervisor can be avoided if the manufacturing development is rejected. Since Company TC will keep on promoting the item, the selling costs, product-level advertising cost, and facility-sustaining costs will proceed irrespective whether Product X is made or bought.
These costs may not be avoided by obtaining Product X. Thus, the below items would be relevant to the make-or-outsource decision. The items that is relevant to make-or-outsource decision is mentioned in the below part.
Determine the total avoidable costs
Therefore the total avoidable cost is $150,000.
b.

Whether Company TC continue to make the product or buy from the supplier by determining the change in net income.
Explanation of Solution
Determine the cost per unit
Therefore the cost per unit is $10.
Determine the increase in net income
Therefore the increase in net income is $15,000.
The reason on whether Company TC would continue to make the product or buy from the supplier is as follows:
The avoidable cost of producing Product X is $10 per unit. Since the cost to buy is just $9, Company TC can lessen its costs by acquiring instead of manufacturing Product X. By outsourcing Product X would expand income by $15,000.
c.

Whether Company TC should buy Product X if sales increase by 10,000 units.
Explanation of Solution
Determine the avoidable costs
Therefore the avoidable cost is $200,000.
Determine the cost per unit
Therefore the cost per unit is $8.
The reasons on whether Company TC should buy Product X if sales increase by 10,000 units is as follows:
The cost of the chief's pay is fixed with respect to the number of units Product X is manufactured and sold. Consequently, the cost per unit will drop and there is an increase in sales. The manufacturing cost per unit is $8.
The avoidable cost per unit at the current level of production is lower to produce than to purchase. Company TC should continue making Product X. The decision to outsource should think about future development in addition to the present creation.
d.

The qualitative factors that Company TC should consider before deciding to outsource Product X.
Explanation of Solution
The qualitative factors that Company TC should consider before deciding to outsource Product X is as follows:
Before focusing on the outsourcing decision, Company TC must think about the capacity of the provider to furnish Product X as per the organization's quality norms. Likewise, Company TC must guarantee itself that the item will be conveyed on an appropriate premise. By outsourcing, Company TC is losing the advantages of vertical integration. The organization is subject to the provider's execution.
The loss of control should be weighed in contradiction of the advantages of cost reduction. Company TC can shield itself from inconsistent providers by keeping up a rundown of licensed providers. Company TC should furnish these providers with hikes or incentives for providing exceptional services, for example, amount buys and quick invoice payment so as to increase the favored customer standing.
Want to see more full solutions like this?
Chapter 13 Solutions
Survey Of Accounting
- View Policies Current Attempt in Progress Bramble Cheese Company has developed a new cheese slicer called Slim Slicer. The company plans to sell this slicer through its online website. Given market research, Bramble believes that it can charge $40 for the Slim Slicer, Prototypes of the Slim Slicer, however, are costing $43. By using cheaper materials and gaining efficiencies in mass production, Bramble believes it can reduce Slim Slicer's cost substantially. Bramble wishes to earn a return of 40% of the selling price. (a) Compute the target cost for the Slim Slicer. Target cost $ eTextbook and Medialarrow_forwardHomework i s w Asbury Coffee Enterprises (ACE) manufactures two models of coffee grinders: Personal and Commercial. The Personal grinders have a smaller capacity and are less durable than the Commercial grinders. ACE only recently began producing the Commercial model. Since the introduction of the new product, profits have been steadily declining, although sales have been increasing. The management at ACE believes that the problem might be in how the accounting system allocates costs to products. Direct materials. Direct labor The current system at ACE allocates manufacturing overhead to products based on direct labor costs. For the most recent year, which is representative, manufacturing overhead totaled $2,023,500 based on production of 30,000 Personal grinders and 10,000 Commercial grinders. Direct costs were as follows: Cost Driver Number of production runs Quality tests performed Shipping orders processed Total overhead here to search CINNAMON Management has determined that…arrow_forwardCase 2 Ethics and a Cost-Volume-Profit Application Danna Lumus, the marketing manager for a division that produces a variety of paper products, is considering the divisional manager's request for a sales forecast for a new line of paper napkins. The divisional manager has been gathering data so that he can choose between two different production processes. The first process would have a variable cost of $10 per case produced and total fixed cost of $100,000. The second process would have a variable cost of $6 per case and total fixed cost of $200,000. The selling price would be $30 per case. Danna had just completed a marketing analysis that projects annual sales of 30,000 cases. Danna is reluctant to report the 30,000 forecast to the divisional manager. She knows that the first process would be labor intensive, whereas the second would be largely automated with little labor and no requirement for an additional production supervisor. If the first process is chosen, Jerry Johnson, a…arrow_forward
- Homework, Chapter 25 Process or Sell Product J19 is produced for $3.42 per gallon. Product J19 can be sold without additional processing for $4.10 per gallon, or processed further into Product R33 at an additional cost of $0.48 per gallon. Product R33 can be sold for $4.54 per gallon. a. Prepare a differential analysis dated April 30 on whether to sellI Product J19 (Alternative 1) or process further into Product R33 (Alternative 2). Round your answers to the nearest cent. If required, use a minus sign to indicate a loss. Differential Analysis Sell Product J19 (Alt. 1) or Process Further into Product R33 (Alt. 2) April 30 Process Sell Differential Further into Product J19 Effects Product R33 (Alternative 1) (Alternative 2) (Alternative 2) Revenues, per unit $ Costs, per unit Profit (loss), per unit b. Should Product J19 be sold (Alternative 1) or processed further into Product R33 (Alternative 2)?arrow_forwardQUESTION 5 Apollonia Company is part of an HMO that operates in a large Metropolitan area. Currently, Apollonia has its own dental laboratory to produce varieties of porcelain crowns. The selling price of the crown is $150 and the unit costs to produce the crowns are as follows: $ Direct materials Direct labour Variable manufacturing overhead Variable marketing expenses 4 Fixed manufacturing overhead Total costs Manager of company, Jane has enough idle capacity to accept a one time only special order from Tom for 20,000 units of crown at $76 per unit. Jane will not incur any variable marketing expenses for the order. a. Evaluate above case above to determine whether Green Jane should accept the order. Supporting workings with calculations. b. In addition to the special order's effect on profits, determine the FIVE (5) factors should Jane's manager consider in deciding whether to accept the order.arrow_forwardQUESTION 2 FPD Ltd makes and sells three different food processor models: Household, Home Pro and Chef Pro. For many years, the Household was the only food processor made by the FPD and was highly regarded for its quality. Unfortunately, demand has steadily fallen over the past two years. William Prout, FPD's production manager, suspected the reason for the decline in sales was increasing competition from overseas suppliers with lower prices. Home Pro and Chef Pro have been added to the product line over the past six years. Both are more advanced and technologically sophisticated than the Household. As a result, they are significantly more complex to manufacture and require special materials handling, tooling and setting up for each batch produced. Given the complexity of manufacturing the Home Pro and Chef Pro, FPD charges what it believes is a premium price for both of these products. The selling price of the three models are shown in the table below. Home Pro $200.00 Household Chef…arrow_forward
- Question 3 Assume that HASF furniture Inc., as described, currently purchases the chair cushions for its lawn set from an outside vendor for $30 per set. Modern Furniture’s chief operations officer wants an analysis of the comparative costs of manufacturing these cushions to determine whether bringing the manufacturing in-house would save the firm money. Additional information shows that if Modern furniture’s were to manufacture the cushions, the materials cost would be $16 and the labor cost would be $10 per set and that it would have to purchase cutting and sewing equipment, which would add $25,000 to annual fixed costs. NOTE: No need to enter comma between numbers Required Computation for 10,000 units What amount should have been inccrued if company produce 10,000 units What amount should have been inccrued if company purhcase 10,000 units from outside What amount company save if company make 10,000 cushionsarrow_forwardNumber 6 Tasty Time Cafeteria operates cafeteria food services in public buildings in the Midwest. Tasty Time is contemplating a major change in its cost structure. Currently, all of their cafeteria lines are staffed with hourly wage employees who hand serve the food to customers. Benson Riggs, Tasty Time's owner, is considering replacing the employees with an automated self-service system. However, before making the change, Benson would like to know the consequences of the change, since the volume of business varies significantly from location to location. Shown below are the CVP income statements for each alternative. Automated Self-Service Personal Service System $2,500,000 1.125,000 $1,375,000 875,000 S 500,000 System $2,500,000 1.875,000 625,000 125,000 S 500,000 Sales Variable costs Contribution margin Fixed costs Net Income Instructions Determine the degree of operating leverage for each alternative. Which alternative would produce the higher net income if sales increased by…arrow_forwardSpecial-Order Decision, Traditional Analysis, Qualitative Aspects Feinan Sports, Inc., manufactures sporting equipment, including weight-lifting gloves. A national sporting goods chain recently submitted a special order for 4,000 pairs of weight-lifting gloves. Feinan Sports was not operating at capacity and could use the extra business. Unfortunately, the order’s offering price of $12.70 per pair was below the cost to produce them. The controller was opposed to taking a loss on the deal. However, the personnel manager argued in favor of accepting the order even though a loss would be incurred; it would avoid the problem of layoffs and would help maintain the community image of the company. The full cost to produce a pair of weight-lifting gloves is presented below. Direct materials $7.40 Direct labor 3.80 Variable overhead 1.60 Fixed overhead 3.10 Total $15.90 No variable selling or administrative expenses would be associated with the order. Non-unit-level activity…arrow_forward
- Refer to Exercise 12.14. Suppose that for 20x2, Sanford, Inc., has chosen suppliers that provide higher-quality parts and redesigned its plant layout to reduce material movement. Additionally, Sanford implemented a new setup procedure and provided training for its purchasing agents. As a consequence, less setup time is required and fewer purchasing mistakes are made. At the end of 20x2, the information shown on page 680 is provided. Required: 1. Prepare a report that compares the non-value-added costs for 20x2 with those of 20x1. 2. What is the role of activity reduction for non-value-added activities? For value-added activities? 3. Comment on the value of a trend report.arrow_forwardQUESTION 25 A product called Wallaby has revenue of $1,250,000, variable costs of goods sold of $850,000, variable selling expenses of $275,000, and fixed costs of $225,000, creating an operating loss of $(100,000). Using differential analysis, the Company will determine whether product Wallaby should be continued or discontinued, assuming fixed costs are unaffected by the decision. What amount for the variable cost of goods sold should be used in analyzing the alternative to discontinue product Wallaby? $0 O $425,000 This is not a choice. $850,000arrow_forwardCurrent Attempt in Progress Marigold Bunyon Lumber Co. produces several products that can be sold at the split-off point or processed further and then sold. The following results are from a recent period: Sales Value Additional at Split-off Variable Costs Further Processing Sales Value after Product $160600 Green lumber $24800 $185400 28300 125000 175000 Rough lumber Sawdust 20100 105000 133200 Which products should be processed further? O All three products. Green lumber and rough lumber O Rough lumber and sawdust. Green lumber and sawdust. )arrow_forward
- Managerial AccountingAccountingISBN:9781337912020Author:Carl Warren, Ph.d. Cma William B. TaylerPublisher:South-Western College PubCornerstones of Cost Management (Cornerstones Ser...AccountingISBN:9781305970663Author:Don R. Hansen, Maryanne M. MowenPublisher:Cengage Learning
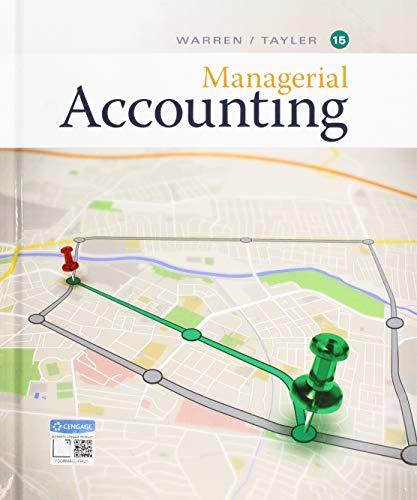
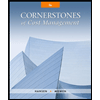