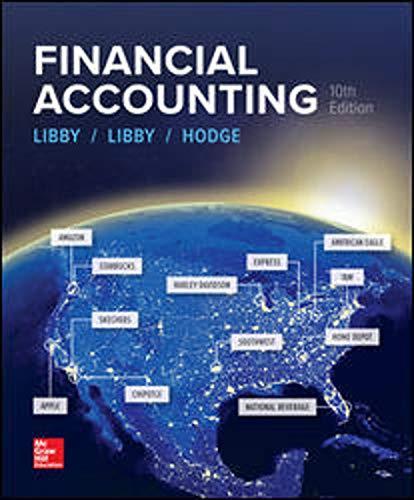
FINANCIAL ACCOUNTING
10th Edition
ISBN: 9781259964947
Author: Libby
Publisher: MCG
expand_more
expand_more
format_list_bulleted
Concept explainers
Topic Video
Question
The
Should Sellers Manufacturing produce Part Z or outsource it to Manufacturing World?
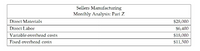
Transcribed Image Text:Sellers Manufacturing
Monthly Analysis: Part Z
Direct Materials
$28,000
Direct Labor
$6,400
Variable overhead costs
$18,000
Fixed overhead costs
$11,500
Expert Solution

This question has been solved!
Explore an expertly crafted, step-by-step solution for a thorough understanding of key concepts.
Step by stepSolved in 2 steps with 2 images

Knowledge Booster
Learn more about
Need a deep-dive on the concept behind this application? Look no further. Learn more about this topic, accounting and related others by exploring similar questions and additional content below.Similar questions
- The following production costs are provided for AudioPro Company, a manufacturer of high-quality headphones. Manufacturing Costs: Direct Materials Direct Labor Variable Overhead Fixed Overhead Total It has been determined that the headphones could be purchased from Integrated Labs at a cost of $135 plus $8 shipping costs. Assume 40% of fixed overhead allocated to making headphones relates to a production manager who would not be retained if the headphones were not produced by AudioPro. Required: a. Considering the offer from Integrated Labs, show whether AudioPro should make or buy the product. b. How would your analysis change if AudioPro could use capacity resources for alternative activities that would produce a contribution of $35 per unit? Complete this question by entering your answers in the tabs below. Required A Required B Considering the offer from Integrated Labs, show whether AudioPro should make or buy the product. Purchase Cost Headphones Shipping Cost Manufacturing Cost:…arrow_forwardRock Creek Bottling Company pays its production manager a salary of $6,000 per month. Salespersons are paid strictly on commission, at $1.50 for each case of product sold. For Rock Creek Bottling Company, the production manager's salary is an example of: Multiple Choice a variable cost. a mixed cost. a fixed cost. None of thesearrow_forwardZurgot Inc. has just organized a new division to manufacture and sell specially designed computer tables, using select hardwoods. The division's monthly costs are shown in the schedule below: Manufacturing costs: Variable costs per unit: Direct materials Variable manufacturing overhead Fixed manufacturing overhead costs (total) Selling and administrative costs: Variable Fixed (total) Units produced Units sold Zurgot regards all of its workers as full-time employees, and the company has a long-standing no-layoff policy. Furthermore, production is highly automated. Accordingly, the company includes its labour costs in its fixed manufacturing overhead. The tables sell for $489 each. During the first month of operations, the following activity was recorded: a. Absorption costing b. Variable costing 4,770 3,550 $ 192 13 $ $438,840 Cost of goods sold: 10% of sales Required: 1. Compute the unit product cost under each of the following costing method. Unit Product Cost $333,900 2. Prepare an…arrow_forward
- SOLVE ALL QUESTIONS OTHERWISE LEAVE ITarrow_forwardHeintz Products uses activity-based costing to account for product costs. The plant manager has estimated the following cost drivers and rates. Activity Centers Materials inspection Equipment maintenance Machine setups Packing and shipping Direct materials costs were $552,000 and direct labor costs were $392,000 during November, when the plant finished 7,000 pounds of product, had 20 setups, and ran the machines for 15,000 hours. There were no work-in-process inventories. Beginning Balance Required: Use T-accounts to show the flow of materials, labor, and overhead costs from the four overhead activity centers through Work-in- Process Inventory and out to Finished Goods Inventory. Use the accounts Materials Inventory, Wages Payable, Work-in-Process Inventory, Finished Goods Inventory, and four overhead applied accounts. Ending Balance Beginning Balance Ending Balance Cost Drivers Direct materials cost Machine-hours Number of production runs Pounds of finished output Debit Debit…arrow_forwardHaver Company currently pays an outside supplier $35 per unit for a part for one of its products. Haver is considering two alternative methods of making the part. Method 1 for making the part would require direct materials of $15 per unit, direct labor of $18 per unit, and incremental overhead of $3 per unit. Method 2 for making the part would require direct materials of $15 per unit, direct labor of $12 per unit, and incremental overhead of $7 per unit. Required: 1. Compute the cost per unit for each alternative method of making the part. 2. Should Haver make or buy the part? If Haver makes the part, which production method should it use? Complete this question by entering your answers in the tabs below. Required 1 Required 2 Should Haver make or buy the part? If Haver makes the part, which production method should it use? Should Haver make or buy the part? If Haver makes the part, which production method should it use?arrow_forward
- Koontz Company manufactures two models of industrial components-a Basic model and an Advanced Model. The company considers all of its manufacturing overhead costs to be fixed and it uses plantwide manufacturing overhead cost allocation based on direct labor-hours. Koontz's controller prepared the segmented income statement that is shown below for the most recent year (he allocated selling and administrative expenses to products based on sales dollars): Basic Advanced Total Number of units produced and sold 20,000 10,000 30,000 $ 5,000,000 3,650,000 1,350,000 1,200,000 $3,000,000 $2,000,000 1,350,000 650,000 480,000 Sales Cost of goods sold Gross margin Selling and administrative expenses 2,300,000 700,000 720,000 (20,000) Net operating income (loss) $4 $4 170,000 150,000 Direct laborers are paid $20 per hour. Direct materials cost $40 per unit for the Basic model and $60 per unit for the Advanced model. Koontz is considering a change from plantwide overhead allocation to a departmental…arrow_forwardMarine Components produces parts for airplanes and ships. The parts are produced to specification by their customers, who pay either a fixed price (the price does not depend directly on the cost of the job) or price equal to recorded cost plus a fixed fee (cost plus). For the upcoming year (year 2), Marine expects only two clients (client 1 and client 2). The work done for client 1 will all be done under fixed-price contracts while the work done for client 2 will all be done under cost-plus contracts. The controller at Marine Components chose direct labor cost as the allocation base in year 2, based on what she considered reflected the relation between overhead and direct labor cost. Year 3 is approaching and again the company only expects two clients: client 1 and client 3. Work for client 1 will continue to be billed using fixed-price contracts, and client 3 will be billed based on cost-plus contracts. Manufacturing overhead for year 3 is estimated to be $18 million. Other…arrow_forwardScenario:You are a management accountant of EON and Brothers Ltd., a manufacturing company thatproduces two products simultaneously in one of their production plants. You are asked to producea management report on costing techniques. This company follows a traditional approach to costingand absorbs production overhead using machine hours. The company’s policy is to add a 50%markup on the unit cost to obtain the selling price.The relevant information is given below:EON and Brothers Ltd. produces two similar products called Alfa and Beta.Total Overheads = £155,000Machine Hours = 58980 hrsProduct Alfa BetaProduction Units 2,580 5,100Material Cost per unit £31 £51Labour Cost per unit £21 £17Machine Hours per unit 11 6After discussing with all the important people of the production plant, you have allocated theoverhead costs as mentioned below:% OverheadsSet up Costs 30Inspections 40Materials Handling 30Cost Pools are as mentioned below:Alfa Beta Total6Setups 400 65 465Inspections 500 275…arrow_forward
- Wallis Company manufactures only one product and uses a standard cost system. The company uses a predetermined plantwide overhead rate that relies on direct labor-hours as the allocation base. All of the company's manufacturing overhead costs are fixed—it does not incur any variable manufacturing overhead costs. The predetermined overhead rate is based on a cost formula that estimated $2,884,000 of fixed manufacturing overhead for an estimated allocation base of 288,400 direct labor-hours. Wallis does not maintain any beginning or ending work in process inventory. The company’s beginning balance sheet is as follows: Wallis Company Balance Sheet 1/1/XX (dollars in thousands) Assets Cash $ 740 Raw materials inventory 190 Finished goods inventory 310 Property, plant, and equipment, net 8,900 Total assets $ 10,140 Liabilities and Equity Retained earnings $ 10,140 Total liabilities and equity $ 10,140 The company’s standard cost card for its…arrow_forwardCompanion Computer Company has been purchasing carrying cases for its portable computers at a purchase price of $56 per unit. The company, which is currently operating below full capacity, charges factory overhead to production at the rate of 43% of direct labor cost. The fully absorbed unit costs to produce comparable carrying cases are expected to be as follows: Direct materials $27 Direct labor 22 Factory overhead (43% of direct labor) 9.46 Total cost per unit $58.46 If Companion Computer Company manufactures the carrying cases, fixed factory overhead costs will not increase and variable factory overhead costs associated with the cases are expected to be 16% of the direct labor costs. Question Content Area a. Prepare a differential analysis dated February 24 to determine whether the company should make (Alternative 1) or buy (Alternative 2) the carrying case. If required, round your answers to two decimal places. If an amount is zero, enter "0". For those boxes…arrow_forwardBeto Company pays $6.50 per unit to buy a part for one of the products it manufactures. With excess capacity, the company is considering making the part. Making the part would cost $7.20 per unit for direct materials and $1.00 per unit for direct labor. The company normally applies overhead at the predetermined rate of 200% of direct labor cost. Incremental overhead to make the part would be 80% of direct labor cost. (a) Prepare a make or buy analysis of costs for this part. (Enter your answers rounded to 2 decimal places.) (b) Should Beto make or buy the part? (a) Make or Buy Analysis Direct materials Direct labor Overhead Cost to buy Cost per unit Cost difference (b) Company should Make Buyarrow_forward
arrow_back_ios
SEE MORE QUESTIONS
arrow_forward_ios
Recommended textbooks for you
- AccountingAccountingISBN:9781337272094Author:WARREN, Carl S., Reeve, James M., Duchac, Jonathan E.Publisher:Cengage Learning,Accounting Information SystemsAccountingISBN:9781337619202Author:Hall, James A.Publisher:Cengage Learning,
- Horngren's Cost Accounting: A Managerial Emphasis...AccountingISBN:9780134475585Author:Srikant M. Datar, Madhav V. RajanPublisher:PEARSONIntermediate AccountingAccountingISBN:9781259722660Author:J. David Spiceland, Mark W. Nelson, Wayne M ThomasPublisher:McGraw-Hill EducationFinancial and Managerial AccountingAccountingISBN:9781259726705Author:John J Wild, Ken W. Shaw, Barbara Chiappetta Fundamental Accounting PrinciplesPublisher:McGraw-Hill Education
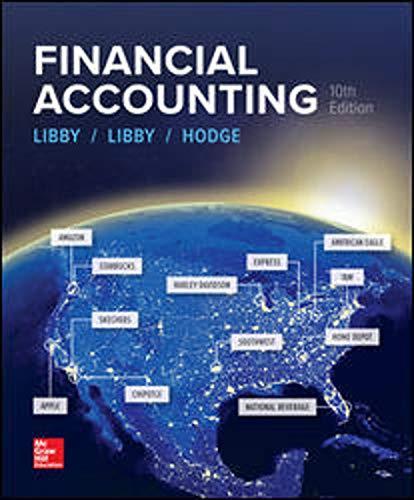
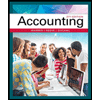
Accounting
Accounting
ISBN:9781337272094
Author:WARREN, Carl S., Reeve, James M., Duchac, Jonathan E.
Publisher:Cengage Learning,
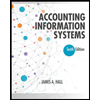
Accounting Information Systems
Accounting
ISBN:9781337619202
Author:Hall, James A.
Publisher:Cengage Learning,
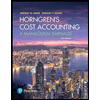
Horngren's Cost Accounting: A Managerial Emphasis...
Accounting
ISBN:9780134475585
Author:Srikant M. Datar, Madhav V. Rajan
Publisher:PEARSON
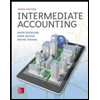
Intermediate Accounting
Accounting
ISBN:9781259722660
Author:J. David Spiceland, Mark W. Nelson, Wayne M Thomas
Publisher:McGraw-Hill Education
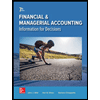
Financial and Managerial Accounting
Accounting
ISBN:9781259726705
Author:John J Wild, Ken W. Shaw, Barbara Chiappetta Fundamental Accounting Principles
Publisher:McGraw-Hill Education