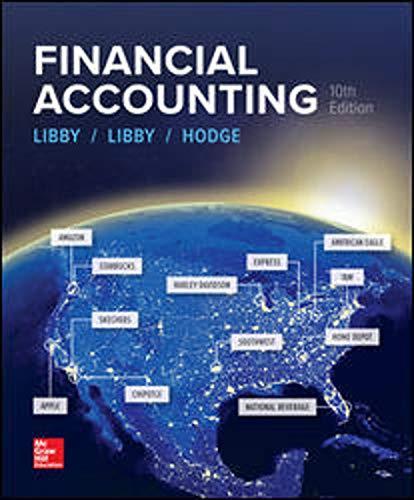
Concept explainers
Isaacson's Fine Furnishings manufactures upscale custom furniture. Isaacson's currently uses a plantwide
The Isaacson's plant completed Jobs 450 and 455 on May 15. Both jobs incurred a total of 6 DL hours throughout the entire production process. Job 450 incurred 1 MH in the Machining Department and 5 DL hours in the Finishing Department (the other DL hour occurred in the Machining Department). Job 455 incurred 5 MH in the Machining Department and 4 DL hours in the Finishing Department (the other two DL hours occurred in the Machining Department
1.Compute the plantwide overhead rate assuming that Isaacson's expects to incur 27,500total DL hours during the year.
2. Compute departmental overhead rates assuming that Isaacson's expects to incur 14,800 MH in the Machining Department and 18,000 DL hours in the Finishing Department during the year.
3.If Isaacson's continues to use the plantwide overhead rate, how much manufacturing overhead would be allocated to Job 450 and Job 455? First identify the formula, then calculate the amount of manufacturing overhead that would be allocated to the jobs if the plantwide overhead rate is used. (Round your answers to the nearest whole dollar.)
(I need the answer for number 3)


Predetermined overhead rate is the single plantwide overhead rate that will be used for allocation of overheads into various jobs or departments.
Step by stepSolved in 2 steps

- California Dreamin' manufactures 1960’s style clothing and accessories. The company produces two main products: Floral and Tie-Dye. Currently the company uses a traditional overhead rate in which Manufacturing Overhead is allocated to products based on direct labor hours logged. The projected production levels for the period are 1,000 units of Floral and 500 units of Tie-Dye. Due to profitability concerns, management is considering switching to Activity Based Costing (ABC). Management has divided Manufacturing Overhead Costs into three activities and cost pools: Assembly $32,000; Machine Setup $12,000; and Product Movement $102,600. Management has identified the following cost drivers for each overhead activity: direct labor hours for assembly, number of setups for machine setup, and number of moves for product movement. The following information has been compiled for each product line: Floral Tie-Dye direct labor requirements 0.75 direct labor hours per…arrow_forwardHeintz Products uses activity-based costing to account for product costs. The plant manager has estimated the following cost drivers and rates. Activity Centers Materials inspection Equipment maintenance Machine setups Packing and shipping Direct materials costs were $552,000 and direct labor costs were $392,000 during November, when the plant finished 7,000 pounds of product, had 20 setups, and ran the machines for 15,000 hours. There were no work-in-process inventories. Beginning Balance Required: Use T-accounts to show the flow of materials, labor, and overhead costs from the four overhead activity centers through Work-in- Process Inventory and out to Finished Goods Inventory. Use the accounts Materials Inventory, Wages Payable, Work-in-Process Inventory, Finished Goods Inventory, and four overhead applied accounts. Ending Balance Beginning Balance Ending Balance Cost Drivers Direct materials cost Machine-hours Number of production runs Pounds of finished output Debit Debit…arrow_forwardFocarrow_forward
- Hansabenarrow_forwardCampbell Company produces commercial gardening equipment. Since production is highly automated, the company allocates its overhead costs to product lines using activity-based costing. The costs and cost drivers associated with the four overhead activity cost pools follow: Cost Cost driver Unit Level $75,400 Req A and B 2,900 labor hours Production of 870 sets of cutting shears, one of the company's 20 products, took 160 labor hours and 7 setups and consumed 19 percent of the product-sustaining activities. Complete this question by entering your answers in the tabs below. Req C Allocated overhead Direct cost Total cost per unit Desired profit Sales price Required 8. Had the company used labor hours as a companywide allocation base, how much overhead would It have allocated to the cutting shears? b. How much overhead is allocated to the cutting shears using activity-based costing? c. Compute the overhead cost per unit for cutting shears first using activity-based costing and then using…arrow_forwardVishnuarrow_forward
- Reynoso Corporation manufactures titanium and aluminum tennis racquets. Reynoso's total overhead costs consist of assembly costs and inspection costs. The following information is available: Cost Titanium Aluminum Total Cost Assembly 500 mach. hours 500 mach. hours $40000 Inspections 350 150 $100000 2100 labor hours 1900 labor hours Reynoso is considering switching from one overhead rate based on labor hours to activity-based costing. Total overhead costs assigned to titanium racquets, using a single overhead rate, are O $70000. O $73500. O $98000. O $100000.arrow_forwardMarvel Parts, Incorporated, manufactures auto accessories including a set of seat covers that can be adjusted to fit most cars. According to its standards, the factory should work 1,015 hours each month to produce 2,030 sets of seat covers. The standard costs associated with this level of production are: Direct materials Direct labor Variable manufacturing overhead (based on direct labor-hours) Direct materials (8,400 yards) Direct labor Variable manufacturing overhead Total $ 59,276 $ 8,120 $ 3,857 1. Materials price vanance 1. Materials quantity variance 2. Labor rate variance 2 Labor efficiency variance 3. Vanable overhead rate variance 3. Variable overhead efficiency variance Per Set of Covers During August, the factory worked 700 direct labor-hours and produced 1,500 sets of covers. The following actual costs were recorded during the month: Total $ 42,000 $ 6,300 $3,150 $ 29.20 4.00 1.90 $ 35.10 Per Set of Covers $28.00 4.20 2.10 $34.30 At standard, each set of covers should…arrow_forwardBeto Company pays $6.50 per unit to buy a part for one of the products it manufactures. With excess capacity, the company is considering making the part. Making the part would cost $7.20 per unit for direct materials and $1.00 per unit for direct labor. The company normally applies overhead at the predetermined rate of 200% of direct labor cost. Incremental overhead to make the part would be 80% of direct labor cost. (a) Prepare a make or buy analysis of costs for this part. (Enter your answers rounded to 2 decimal places.) (b) Should Beto make or buy the part? (a) Make or Buy Analysis Direct materials Direct labor Overhead Cost to buy Cost per unit Cost difference (b) Company should Make Buyarrow_forward
- Tool Time manufactures carpenter-grade screwdrivers. The company is trying to decide whether to continue to make the case in which the screwdrivers are sold, or to outsource the case to another company. The direct material and direct labor cost to produce the cases total $2.40 per case. The overhead cost is $1.00 per case which consists of $0.40 in variable overhead that would be eliminated if the cases are bought from the outside supplier. The $0.60 of fixed overhead is based on expected production of 400,000 cases per year and consists of the salary of the case production manager of $80,000 per year, along with the remainder consisting of rent, insurance, and depreciation on equipment that will have no resale value. The manager will be laid off if the cases were bought externally. The outside supplier has offered to supply the cases for $3.40 each. How much will Tool Time save or lose if the cases are bought externally? Save $0.40 per case Lose $0.20 per case…arrow_forwardKirsten believes her company's overhead costs are driven (affected) by the number of direct labor hours because the production process is very labor Intensive. During the period, the company produced 4,700 units of Product A requiring a total of 770 labor hours and 2,200 units of Product B requiring a total of 170 labor hours. What allocation rate should be used if the company Incurs overhead costs of $15,980? Multiple Choice $17.00 per labor hour $2.32 per unit $20.75 per labor hour for Product A and $94 per labor hour for Product B None of these.arrow_forwardBlue Africa Inc. produces laptops and desktop computers. The company’s production activities mainly occur in what the company calls its Laser and Forming departments. The Cafeteria and Security departments support the company’s production activities and allocate costs based on the number of employees and square feet, respectively. The total cost of the Security Department is $241,000. The total cost of the Cafeteria Department is $403,000. The number of employees and the square footage in each department are as follows: Employees Square Feet Security Department 10 530 Cafeteria Department 24 2,400 Laser Department 40 4,800 Forming Department 50 800 Using the reciprocal services method of support department cost allocation, determine the total costs from the Security Department that should be allocated to the Cafeteria Department and to each of the production departments.arrow_forward
- AccountingAccountingISBN:9781337272094Author:WARREN, Carl S., Reeve, James M., Duchac, Jonathan E.Publisher:Cengage Learning,Accounting Information SystemsAccountingISBN:9781337619202Author:Hall, James A.Publisher:Cengage Learning,
- Horngren's Cost Accounting: A Managerial Emphasis...AccountingISBN:9780134475585Author:Srikant M. Datar, Madhav V. RajanPublisher:PEARSONIntermediate AccountingAccountingISBN:9781259722660Author:J. David Spiceland, Mark W. Nelson, Wayne M ThomasPublisher:McGraw-Hill EducationFinancial and Managerial AccountingAccountingISBN:9781259726705Author:John J Wild, Ken W. Shaw, Barbara Chiappetta Fundamental Accounting PrinciplesPublisher:McGraw-Hill Education
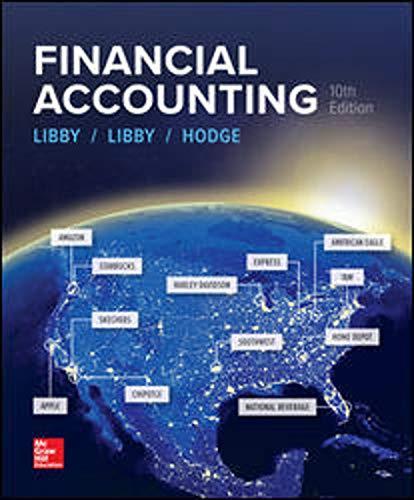
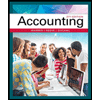
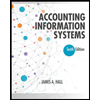
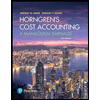
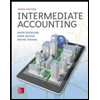
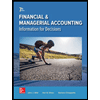