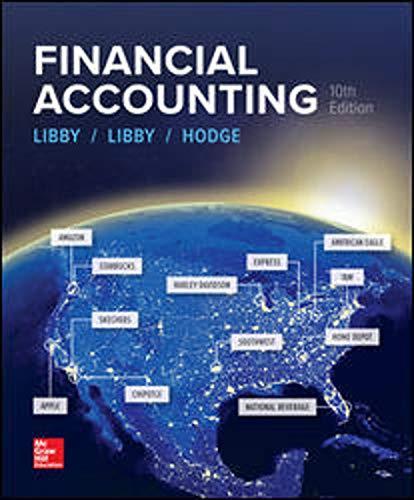
Concept explainers
Koontz Company manufactures two models of industrial components—a Basic model and an Advanced Model. The company considers all of its manufacturing
Basic | Advanced | Total | |
---|---|---|---|
Number of units produced and sold | 20,000 | 10,000 | 30,000 |
Sales | $ 3,000,000 | $ 2,000,000 | $ 5,000,000 |
Cost of goods sold | 2,300,000 | 1,350,000 | 3,650,000 |
Gross margin | 700,000 | 650,000 | 1,350,000 |
Selling and administrative expenses | 720,000 | 480,000 | 1,200,000 |
Net operating income (loss) | $ (20,000) | $ 170,000 | $ 150,000 |
Direct laborers are paid $20 per hour. Direct materials cost $40 per unit for the Basic model and $60 per unit for the Advanced model. Koontz is considering a change from plantwide overhead allocation to a departmental approach. The overhead costs in the company’s Molding Department would be allocated based on machine-hours and the overhead costs in its Assemble and Pack Department would be allocated based on direct labor-hours. To enable further analysis, the controller gathered the following information:
Molding | Assemble and Pack | Total | |
---|---|---|---|
Manufacturing overhead costs | $ 787,500 | $ 562,500 | $ 1,350,000 |
Direct labor hours: | |||
Basic | 10,000 | 20,000 | 30,000 |
Advanced | 5,000 | 10,000 | 15,000 |
Machine hours: | |||
Basic | 12,000 | – | 12,000 |
Advanced | 10,000 | – | 10,000 |
Required:
1. Using the plantwide approach:
a. Calculate the plantwide overhead rate.
b. Calculate the amount of overhead that would be assigned to each product.
2. Using a departmental approach:
a. Calculate the departmental overhead rates.
b. Calculate the total amount of overhead that would be assigned to each product.
c. Using your departmental overhead cost allocations, redo the controller’s segmented income statement (continue to allocate selling and administrative expenses based on sales dollars).
3. Koontz’s production manager has suggested using activity-based costing instead of either the plantwide or departmental approaches. To facilitate the necessary calculations, she assigned the company’s total manufacturing overhead cost to five activity cost pools as follows:
Activity Cost Pool | Activity Measure | Manufacturing Overhead |
---|---|---|
Machining | Machine-hours in Molding | $ 417,500 |
Assemble and pack | Direct labor-hours in Assemble and Pack | 282,500 |
Order processing | Number of customer orders | 230,000 |
Setups | Setup hours | 340,000 |
Other (unused capacity) | 80,000 | |
$ 1,350,000 |
She also determined that the average order size for the Basic and Advanced models is 400 units and 50 units, respectively. The molding machines require a setup for each order. One setup hour is required for each customer order of the Basic model and three hours are required to setup for an order of the Advanced model.
The company pays a sales commissions of 5% for the Basic model and 10% for the Advanced model. Its traceable fixed advertising costs include $150,000 for the Basic model and $200,000 for the Advanced model. The remainder of the company’s selling and administrative costs are organization-sustaining in nature.
Using the additional information provided by the production manager, calculate:
a. An activity rate for each activity cost pool.
b. The total manufacturing overhead cost allocated to the Basic model and the Advanced model using the activity-based approach.
c. The total selling and administrative cost traced to the Basic model and the Advanced model using the activity-based approach.
4. Using your activity-based cost assignments from requirement 3, prepare a contribution format segmented income statement that is adapted from Exhibit 6-8. (Hint: Organize all of the company’s costs into three categories: variable expenses, traceable fixed expenses, and common fixed expenses.)
5. Using your contribution format segmented income statement from requirement 4, calculate the break-even point in dollar sales for the Advanced model.

Trending nowThis is a popular solution!
Step by stepSolved in 4 steps

- Godiva company has two products, A and B. The company uses activity-based costing to allocate overhead costs of $100,000. Data relating to the company's activity pools for the current year are given below: Cost Pool Total cost in Total Number of Activity Measures Used Cost Pool Product A Product B Total Activity 1 $42,000 100 200 300 Activity 2 $10,000 20 5 25 Activity 3 $48,000 3,000 3,000 6,000 Compute the activity rate (allocation rate) for Activity 2: $500 $2,000 $400 $140arrow_forwardManjiarrow_forwardLarner Corporation is a diversified manufacturer of industrial goods. The company's activity-based costing system contains the following six activity cost pools and activity rates: Activity Cost Pool Labor-related Machine-related Machine setups Production orders Shipments $ 140.00 per shipment General factory $ 7.00 per direct labor-hour Cost and activity data have been supplied for the following products: Direct labor-hours Machine-hours Machine setups Production orders Shipments Activity Rates $7.00 per direct labor-hour Direct materials cost per unit Direct labor cost per unit Number of units produced per year $7.00 per machine-hour $30.00 per setup $200.00 per order Unit product cost Total Expected Activity J78 378 1,200 2,200 6 5 7 B52 30 50 1 1 1 Required: Compute the unit product cost of each product listed above. (Do not round intermediate calculations. Round your answers to 2 decimal places.) B52 378 $5.50 $ 4.75 4,000 B52 $32.00 $9.00 100arrow_forward
- Wilmington Company has two manufacturing departments-Assembly and Fabrication. It considers all of its manufacturing overhead costs to be fixed costs. The first set of data that is shown below is based on estimates from the beginning of the year. The second set of data relates to one particular job completed during the year-Job Bravo. Estimated Data Manufacturing overhead costs Direct labor-hours Machine-hours Job Bravo Direct labor-hours Machine-hours Assembly $ 1,170,000 65,000 26,000 Assembly Fabrication 14 6 6 9 Fabrication $ 1,430,000 39,000 130,000 Total 20 15 1. Plantwide manufacturing overhead applied to Job Bravo 2. Manufacturing overhead applied from Assembly to Job Bravo 2. Manufacturing overhead applied from Fabrication to Job Bravo 2. Total departmental manufacturing overhead applied to Job Bravo Required: 1. If Wilmington used a plantwide predetermined overhead rate based on direct labor-hours, how much manufacturing overhead would be applied to Job Bravo? 2. If…arrow_forwardKlumper Corporation is a diversified manufacturer of industrial goods. The company's activity-based costing system contains the following six activity cost pools and activity rates: Activity Cost Pool Supporting direct labor Machine processing Machine setups Production orders. Shipments Product sustaining Activity data have been supplied for the following two products: Total Expected Activity Activity Rates $ 7 per direct labor-hour $ 4 per machine-hour $50 per setup $ 170 per order $ 130 per shipment $ 800 per product Number of units produced per year Direct labor-hours Machine-hours Machine setups Production orders Shipments Product sustaining K425 200 1,075 2,200 11 11 22 2 M67 2,000 40 30 2 2 2 2 Required: How much total overhead cost would be assigned to K425 and M67 using the activity-based costing system?arrow_forwardMultiple Choice $685 per order $675 per order $544 per order $665 per orderarrow_forward
- Ivanhoe Inc. has conducted the following analysis related to its product lines using a traditional costing system (volume-based) and an activity-based costing system. Both the traditional and activity-based costing systems include direct materials and direct labour costs. Products Product 440X Product 137Y Product 249S (a) Sales Revenue $201,000 172,000 Operating income 87,000 Total Costs Traditional $55,000 74,000 26,000 Additional information related to product usage by these pools is as follows: ABC $50,036 70,668 34,296 For each product line, calculate operating income using the traditional costing system. Product 440X Traditional costing system $ Product 137Y $ Product 249Sarrow_forwardLarner Corporation is a diversified manufacturer of industrial goods. The company's activity-based costing system contains the following six activity cost pools and activity rates: Activity Rates $8.00 per direct labor-hour Activity Cost Pool Labor-related Machine-related Machine setups Production orders Shipments $9.00 per machine-hour $ 50.00 per setup $100.00 per order $ 180.00 per shipment General factory $9.00 per direct labor-hour Cost and activity data have been supplied for the following products: Direct materials cost per unit Direct labor cost per unit Number of units produced per year Direct labor-hours Machine-hours Machine setups Production orders Shipments Unit product cost Total Expected Activity J76 379 900 2,900 4 8 12 852 50 20 B52 4 Required: Compute the unit product cost of each product listed above. (Do not round intermediate calculations. Round your answers to 2 decimal places.) 378 $ 4.50 $ 4.75 4,000 852 $ 45.00 $10.00. 500arrow_forwardHansabenarrow_forward
- Wilmington Company has two manufacturing departments-Assembly and Fabrication. It considers all of its manufacturing overhead costs to be fixed costs. The first set of data that is shown below is based on estimates from the beginning of the year. The second set of data relates to one particular job completed during the year-Job Bravo. Estimated Data Manufacturing overhead costs Direct labor-hours Machine-hours Job Bravo Direct labor-hours Machine-hours Assembly $ 600,000 50,000 20,000 Assembly Fabrication 11 3 3 6 Total 14 9 1. Plantwide manufacturing overhead applied to Job Bravo 2. Manufacturing overhead applied from Assembly to Job Bravo 2. Manufacturing overhead applied from Fabrication to Job Bravo 2. Total departmental manufacturing overhead applied to Job Bravo Fabrication $ 800,000 30,000 100,000 Total $ 1,400,000 80,000 120,000 Required: 1. If Wilmington used a plantwide predetermined overhead rate based on direct labor-hours, how much manufacturing overhead would be applied…arrow_forwardsharadarrow_forwardGadubhaiarrow_forward
- AccountingAccountingISBN:9781337272094Author:WARREN, Carl S., Reeve, James M., Duchac, Jonathan E.Publisher:Cengage Learning,Accounting Information SystemsAccountingISBN:9781337619202Author:Hall, James A.Publisher:Cengage Learning,
- Horngren's Cost Accounting: A Managerial Emphasis...AccountingISBN:9780134475585Author:Srikant M. Datar, Madhav V. RajanPublisher:PEARSONIntermediate AccountingAccountingISBN:9781259722660Author:J. David Spiceland, Mark W. Nelson, Wayne M ThomasPublisher:McGraw-Hill EducationFinancial and Managerial AccountingAccountingISBN:9781259726705Author:John J Wild, Ken W. Shaw, Barbara Chiappetta Fundamental Accounting PrinciplesPublisher:McGraw-Hill Education
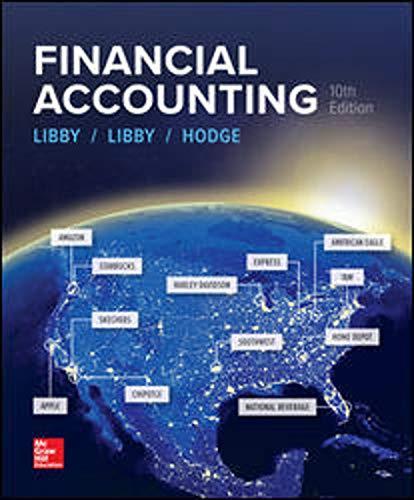
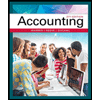
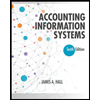
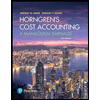
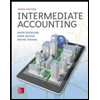
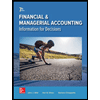