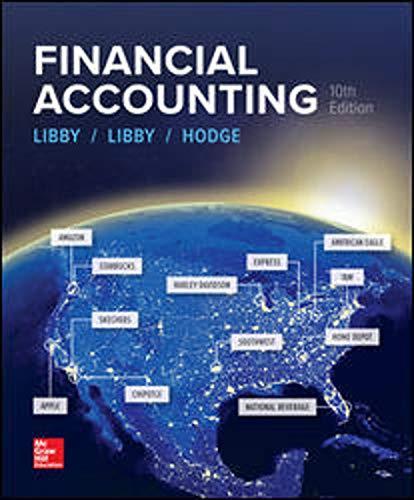
Concept explainers
6. Brees, Inc., a manufacturer of golf carts, has just received an offer from a supplier to provide 2,500 units of a component used in its main product. The component is a track assembly that is currently produced internally. The supplier has offered to sell the track assembly for $66 per unit. Brees is currently using a traditional, unit-based costing system that assigns overhead to jobs on the basis of direct labor hours. The estimated traditional full cost of producing the track assembly is as follows:
Direct materials | $40.00 |
Direct labor | 16.00 |
Variable overhead | 5.00 |
Fixed overhead | 40.00 |
Prior to making a decision, the company’s CEO commissioned a special study to see whether there would be any decrease in the fixed overhead costs. The results of the study revealed the following:
3 setups—$1,180 each (The setups would be avoided, and total spending could be reduced by $1,180 per setup.)
One half-time inspector is needed. The company already uses part-time inspectors hired through a temporary employment agency. The yearly cost of the part-time inspectors for the track assembly operation is $11,730 and could be totally avoided if the part were purchased.
Engineering work: 450 hours, $45/hour. (Although the work decreases by 450 hours, the engineer assigned to the track assembly line also spends time on other products, and there would be no reduction in his salary.)
75 fewer material moves at $30 per move.
Required:
1. Ignore the special study, and determine whether the track assembly should be produced internally or purchased from the supplier.
2. Now, using the special study data, repeat the analysis.
It is ________ expensive to buy outside.
3. Which of the listed items is not a qualitative factor that would affect the decision?

Trending nowThis is a popular solution!
Step by stepSolved in 2 steps

- Tool Time manufactures carpenter-grade screwdrivers. The company is trying to decide whether to continue to make the case in which the screwdrivers are sold, or to outsource the case to another company. The direct material and direct labor cost to produce the cases total $2.40 per case. The overhead cost is $1.00 per case which consists of $0.40 in variable overhead that would be eliminated if the cases are bought from the outside supplier. The $0.60 of fixed overhead is based on expected production of 400,000 cases per year and consists of the salary of the case production manager of $80,000 per year, along with the remainder consisting of rent, insurance, and depreciation on equipment that will have no resale value. The manager will be laid off if the cases were bought externally. The outside supplier has offered to supply the cases for $3.40 each. How much will Tool Time save or lose if the cases are bought externally? Save $0.40 per case Lose $0.20 per case…arrow_forwardSampson Jewelry Corporation manufactures custom jewelry. In the past, Sampson has been using a traditional overhead allocation system based solely on direct labor hours. Sensing that this system was distorting costs and selling prices, Sampson has decided to switch to an activity-based costing system using three activity cost pools. Information on these activity cost pools are as follows: Activity Cost Pool Total Cost Total Activity Labor Related $40,000 8,000 Direct labor hours Machine Related $50,000 12,500 Machine Hours Quality Control $12,000 800 Inspections Sampson has received an order and will complete as Job #309 and expect to incur $900 of direct material, 30 hours of direct labor at $40 per hour, 80 machine hours, and 5 inspections. Sampson needs a markup of 40% on the job.Required:A). Calculate the activity rate and compute is the expected cost of job#309 under the activity-based costing system? What should be the quote on this job?…arrow_forwardWaterway Engine Incorporated produces engines for the watercraft industry. An outside manufacturer has offered to supply several component parts used in the engine assemblies, which are currently being produced by Waterway. The supplier will charge Waterway $315 per engine for the set of parts. Waterway's current costs for those part sets are direct materials, $140; direct labor, $80; and manufacturing overhead applied at 100% of direct labor. Variable manufacturing overhead is considered to be 20% of the total, and fixed overhead will not change if the part sets are acquired from the outside supplier. Required: a. What would be the net cost advantage or disadvantage if Waterway decided to purchase the parts? b. Should Waterway Engine continue to make the part sets or accept the offer to purchase them for $315? a. b. Waterway Engine Incorporated shouldarrow_forward
- Collins Co. produces a part used in the manufacture of one of its products. The unit product cost is $40, computed as follows: Direct materials, direct labor, and variable overhead $24 Fixed overhead $16 Total $40 An outside supplier has offered to provide the parts for only $30 each. If the parts are purchased from the outside supplier, (1) the company estimates that 25% of the fixed overhead cost above could be eliminated; (2) the company can use the freed capacity to launch a new product, earning a contribution margin of $5 per unit. Based on these data, the per-unit dollar financial advantage or disadvantage of purchasing from the outside supplier would be: Multiple Choice a)$7 financial disadvantage b)$8 financial advantage c)$2 financial disadvantage d)$3 financial advantagearrow_forwardThe Grouper Company manufactures 1,478 units of a part that could be purchased from an outside supplier for $14 each. Grouper’s costs to manufacture each part are as follows: Direct materials $2 Direct labor 4 Variable manufacturing overhead 3 Fixed manufacturing overhead 8 Total $17 All fixed overhead is unavoidable and is allocated based on direct labor. The facilities that are used to manufacture the part have no alternative uses. (a) Calculate relevant cost to make. Relevent cost to make $ ___ per unit (c) Calculate net cost to buy if Grouper leases the manufacturing facilities to another company for $9,260 per year. Net cost to buy $ ______arrow_forwardSydney Anime Apparel (SAA) manufacturers graphic t-shirts depicting popular anime characters. SAA uses a traditional plant-wide POHR to allocate their manufacturing costs to products. They estimated a total cost of $606,000. They identified direct labor hours as the cost driver. For the current year, they estimated a total of 80,800 direct labor hours, and actually incurred 76,200 in the production of their t-shirts. What is the applied manufacturing overhead costs? Give your answer to the nearest whole dollar.arrow_forward
- Vikramarrow_forwardHaver Company currently pays an outside supplier $15 per unit for a part for one of its products. Haver is considering two alternative methods of making the part. Method 1 for making the part would require direct materials of $5 per unit, direct labor of $8 per unit, and ncremental overhead of $3 per unit. Method 2 for making the part would require direct materials of $5 per unit, direct labor of $2 per unit, and incremental overhead of $7 per unit. Required: 1. Compute the cost per unit for each alternative method of making the part. 2. Should Haver make or buy the part? If Haver makes the part, which production method should it use? Complete this question by entering your answers in the tabs below. Required 1 Required 2 Compute the cost per unit for each alternative method of making the part. Make with Method Make with 1 Method 2 Cost per unit Cost per unit Required t Buy Required 2 >arrow_forwardFountain Water Products (FWP) manufacturers water bottles. They have historically used a traditional system that allocated the manufacturing overhead costs based on machine hours. FWP is looking at switching to an ABC system in order to ensure more accurate product costing. They first want to compare the traditional and ABC costing systems to determine if it is worth the effort and costs to implement and maintain. They estimate a total overhead cost of $459,000. Under the traditional system they identified machine hours as the cost driver, and estimated a total of 51,000 machine hours. They actually incurred 48,700 machine hours in production. The total applied MOH calculated under the more precise ABC system was $320,000. The ABC costing system will cost $50,000 to implement. FWP has determined that a benefit of more accurate costing by $80,000 is worth the $50,000 implementation cost. What is the difference between the ABC costing and traditional system? Enter your number as a…arrow_forward
- Marvel Parts, Incorporated, manufactures auto accessories. One of the company's products is a set of seat covers that can be adjusted to fit nearly any small car. The company has a standard cost system in use for all of its products. According to the standards that have been set for the seat covers, the factory should work 1,015 hours each month to produce 2,030 sets of covers. The standard costs associated with this level of production are: Direct materials Direct labor Variable manufacturing overhead (based on direct labor-hours) Direct materials (8,400 yards) Direct labor Variable manufacturing overhead Total $ 59,276 $ 8,120 $ 3,857 During August, the factory worked only 700 direct labor-hours and produced 1,500 sets of covers. The following actual costs were recorded during the month: Per Set of Covers $ 29.20 4.00 1.90 $ 35.10 Total $ 42,000 $ 6,300 $ 3,150 1. Materials price variance 1. Materials quantity variance 2. Labor rate variance 2. Labor efficiency variance 3. Variable…arrow_forwardZesta Company produces a part used in the manufacture of one of its products. The unit product cost is $18, computed as follows: Direct materials $ 8 Direct labor 4 Variable manufacturing overhead Fixed manufacturing overhead Unit product cost 1 $ 18 An outside supplier has offered to provide the annual requirement of 4,000 of the parts for only $14 each. The company estimates that 60% of the fixed manufacturing overhead cost above could be eliminated if the parts are purchased from the outside supplier. Based on these data, whether the company accept or reject the supplier offer? And Why?arrow_forwardBeto Company pays $7.30 per unit to buy a part for one of the products it manufactures. With excess capacity, the company is considering making the part. Making the part would cost $8.40 per unit for direct materials and $1.00 per unit for direct labor. The company normally applies overhead at the predetermined rate of 200% of direct labor cost. Incremental overhead to make the part would be 80% of direct labor cost. (a) Prepare a make or buy analysis of costs for this part. (Enter your answers rounded to 2 decimal places.) (b) Should Beto make or buy the part? (a) Make or Buy Analysis Direct materials Direct labor Overhead Cost to buy Cost per unit Cost difference (b) Company should: Make Buyarrow_forward
- AccountingAccountingISBN:9781337272094Author:WARREN, Carl S., Reeve, James M., Duchac, Jonathan E.Publisher:Cengage Learning,Accounting Information SystemsAccountingISBN:9781337619202Author:Hall, James A.Publisher:Cengage Learning,
- Horngren's Cost Accounting: A Managerial Emphasis...AccountingISBN:9780134475585Author:Srikant M. Datar, Madhav V. RajanPublisher:PEARSONIntermediate AccountingAccountingISBN:9781259722660Author:J. David Spiceland, Mark W. Nelson, Wayne M ThomasPublisher:McGraw-Hill EducationFinancial and Managerial AccountingAccountingISBN:9781259726705Author:John J Wild, Ken W. Shaw, Barbara Chiappetta Fundamental Accounting PrinciplesPublisher:McGraw-Hill Education
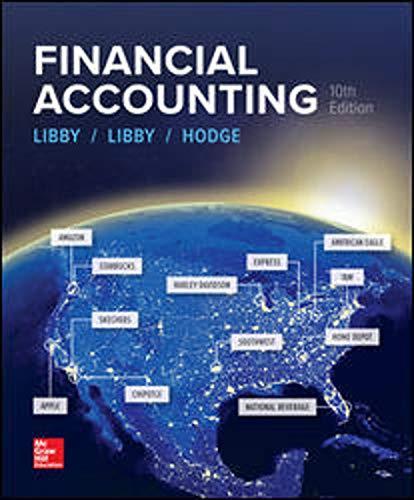
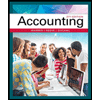
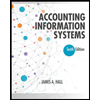
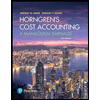
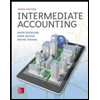
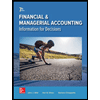