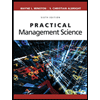
Practical Management Science
6th Edition
ISBN: 9781337406659
Author: WINSTON, Wayne L.
Publisher: Cengage,
expand_more
expand_more
format_list_bulleted
Question
WAI knows from historical records that approximately 40
percent of its labor is used in Department 101 and 60 percent
is used in Department 102. Th e reverse is true of machine time;
60 percent is used in Department 101 and 40 percent is used in
Department 102.
(a) Calculate the labor and machine hours needed in
Department 101 for each period of the MPS developed in
Problem 4.
(b) Calculate the labor and machine hours needed in
Department 102 for each period of the MPS developed in
Problem 4.
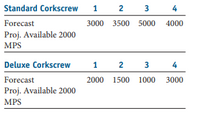
Transcribed Image Text:Standard Corkscrew
1 2
3
4
Forecast
3000 3500 5000 4000
Proj. Available 2000
MPS
Deluxe Corkscrew
1
2
3
4
Forecast
2000 1500 1000 3000
Proj. Available 2000
MPS
Expert Solution

This question has been solved!
Explore an expertly crafted, step-by-step solution for a thorough understanding of key concepts.
This is a popular solution
Trending nowThis is a popular solution!
Step by stepSolved in 2 steps with 1 images

Knowledge Booster
Similar questions
- Q1: Describe the utilization of the analysis methods for the employees work measurement. Q2: Elaborate the importance of the capacity consideration and capacity analysis while managing required demands.arrow_forwardIf 10 pallets are received each 8-hour day, what is the average number of pallets in the system on any given day? Stocking 9 persons 1. 5 hpp S/R Cycle Count person 0.5 hrs/pallet (hpp) Pricing 2 persons 1.25 hpp 1 person 0.25 hpp Spotting 1 persons 0.2 hpp O 10 pallets O 4.713 pallets O 4.375 pallets O125 pallets O Impossible to determinearrow_forwardA process has a yield of 50 percent. How many units are needed as inflow to create anoutflow of 40 units per day?a. 10b. 20c. 80d. 90arrow_forward
- 1. Which of the following quantities has no effect on the first period’s ATP calculation? a) Current on-hand Inventory b) Booked customer orders for the first periods c) MPS quantity for the first period d) Forecasted demand for the first period 2. Which one of the following is an MRP lot-sizing rule that attempts to minimize the amount to minimize the amount of average inventory? a) Periodic order quantity (POQ), WITH P=2 b)Fixed order quantity (FOQ) c) Economic order quantity (EOQ) d)Lot for Lot (L4L). 3. Which of the following statements about lot-sizing rules for MRP is true? a) The periodic order quantity (POQ) rule generates a higher level of average inventory since it creates inventory remnants. b) FOQ is a dynamic lot-sizing rule which reduces the amount of inventory, by doing a better job of matching the order quantity to the projected on-hand inventory quantity. c) The lot for lot rule minimizes inventory investment but maximizes the number of orders placed. d) In…arrow_forwardPROBLEM-3) The Sales&Operations (S&OP) process is designed to produce a plan that all departmentswithin the organization, as well as suppliers to the organization, can work. The process is also sometimes referred toas sales, inventory, and operations planning (SIOP) to emphasize the important role that inventory can play as abuffer between sales planning and operations planning. The S&OP department of the XYZ company, that producesKLM products, estimates the sales over the next six years in thousands of packages will be as follows: Assume that each worker stays on the job for at least one year and XYZ currently has eight workers. XYZ estimatesthat they will have 600000 packages on hand at the end of the current year. Assume that, on average, eachworker is paid TL 60000 per year and is responsible for producing 80000 packages. Inventory costs have beenestimated to be 20 KRS per package per year, and shortages are not allowed. XYZ estimates that it costs TL 2500for each…arrow_forwardFK Millers produces Super and Economy brands of maize flour. In the last quarter of the year of production, the following information about the units and cost of gg SUPER ECONOM Number of produced 20 60 Batch Size 10 20 Direct labor hour per unit 0.03 0.04 Direct labor cost per unit 1500 2000 Direct material cost per unit 1000 2000 Activities overhead costs Setups 20,000 Order handling 30,000 Engineering 39,900 Packaging…arrow_forward
- what is the correct answer?arrow_forwardssume you are the manager of a shop that assembles power tools. You have just received an order for 50 chain saws, which are to be shipped at the start of week 8. Pertinent information on the saws follows: Item Lead Time (weeks) On Hand Components Saw 2 15 A(2), B(1), C(4) A 1 10 E(3), D(1) B 2 5 D(2), F(3) C 2 65 E(2), D(2) D 1 20 E 1 10 F 2 30 Develop the material requirements plan for component E using lot-for-lot ordering for all items. (Leave no cells blank - be certain to enter "0" wherever required.)arrow_forward23. The theory of loss aversion and reference dependence implies that (a) equilibrium allocations will usually be outside the Pareto set (b) the location of the Pareto set may depend on the initial allocation (c) the Pareto set is piecewise linear (d) the Pareto set is reduced to a single point in the Edgeworth box (e) the Pareto set lies on two adjacent sides of the Edgeworth boxarrow_forward
- Prevost Chemicals manufactures an industrial solvent at its only processing plant. A liquid chemical and labor are the two primary inputs. All other resources are included in manufacturing overhead. The plant never has any work-in-process or finished goods inventories. Information from the previous four periods of production follows: Chemical input (gallons) Labor input (hours) Solvent sales (gallons) Average price of chemical per gallon Average wage rate per hour Average sales price per gallon Manufacturing overhead (total) Required A Required B Required C Required: a. Compute the partial productivity measures for chemical for the four periods. b. Compute the partial productivity measures for labor for the four periods. c. Compute the total factor productivity for the four periods. Complete this question by entering your answers in the tabs below. Period Period 1 125,000 12,500 110,000 Period 1 $ 2.00 28.00 10.26 236,000 Compute the partial productivity measures for chemical for the…arrow_forward(1) This DC value-adding activity allows it to receive full truckloads of one product and ship full truckloads of various products to customers. a. allocation b. mixing c. assembly d. kitting (2) As Q increases for EOQ, the cost per order: a. increases b. decreases c. stays the same d. cannot be determinedarrow_forward1. which of the following aggregate plan utilizes a constant amount of labor to fulfill customer orders in each period a. Chase b. Mixed c. level d. Constant e. none of the above 2. Calculate the upper control limit for a c chart when the total number of defects are 120 in 20 batches. 3. Suppose that you want to measure the percentage of the wires that are longer than 9.2 inches. Which control chart would be appropriate to monitor the percentage of the defective wires per batch in a production line? 4. Suppose that you have 192 finished goods in your inventory and the forecast of monthly demand is as follows. Implement a level aggregate plan and calculate the production rate for the plan. June = 310 July = 190 August = 200 September = 210 October = 240 November = 200 a. 193 b. 270 c. 192 d. 216 e. 250arrow_forward
arrow_back_ios
SEE MORE QUESTIONS
arrow_forward_ios
Recommended textbooks for you
- Practical Management ScienceOperations ManagementISBN:9781337406659Author:WINSTON, Wayne L.Publisher:Cengage,Operations ManagementOperations ManagementISBN:9781259667473Author:William J StevensonPublisher:McGraw-Hill EducationOperations and Supply Chain Management (Mcgraw-hi...Operations ManagementISBN:9781259666100Author:F. Robert Jacobs, Richard B ChasePublisher:McGraw-Hill Education
- Purchasing and Supply Chain ManagementOperations ManagementISBN:9781285869681Author:Robert M. Monczka, Robert B. Handfield, Larry C. Giunipero, James L. PattersonPublisher:Cengage LearningProduction and Operations Analysis, Seventh Editi...Operations ManagementISBN:9781478623069Author:Steven Nahmias, Tava Lennon OlsenPublisher:Waveland Press, Inc.
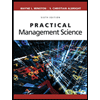
Practical Management Science
Operations Management
ISBN:9781337406659
Author:WINSTON, Wayne L.
Publisher:Cengage,
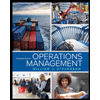
Operations Management
Operations Management
ISBN:9781259667473
Author:William J Stevenson
Publisher:McGraw-Hill Education
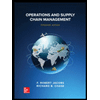
Operations and Supply Chain Management (Mcgraw-hi...
Operations Management
ISBN:9781259666100
Author:F. Robert Jacobs, Richard B Chase
Publisher:McGraw-Hill Education
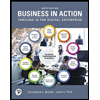
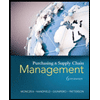
Purchasing and Supply Chain Management
Operations Management
ISBN:9781285869681
Author:Robert M. Monczka, Robert B. Handfield, Larry C. Giunipero, James L. Patterson
Publisher:Cengage Learning
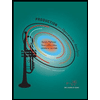
Production and Operations Analysis, Seventh Editi...
Operations Management
ISBN:9781478623069
Author:Steven Nahmias, Tava Lennon Olsen
Publisher:Waveland Press, Inc.