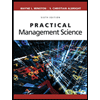
Practical Management Science
6th Edition
ISBN: 9781337406659
Author: WINSTON, Wayne L.
Publisher: Cengage,
expand_more
expand_more
format_list_bulleted
Question
I am having trouble answering question 4. Here is the data and the question. Can you hep me in any way possible?
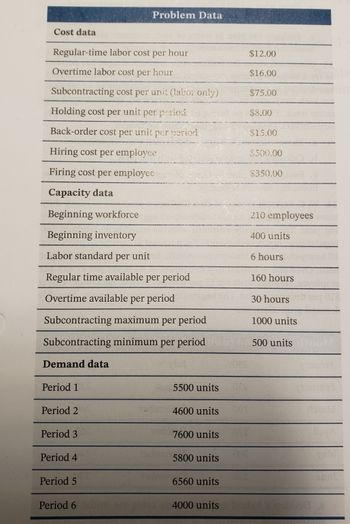
Transcribed Image Text:### Problem Data
#### Cost Data
- **Regular-time labor cost per hour:** $12.00
- **Overtime labor cost per hour:** $16.00
- **Subcontracting cost per unit (labor only):** $75.00
- **Holding cost per unit per period:** $8.00
- **Back-order cost per unit per period:** $15.00
- **Hiring cost per employee:** $500.00
- **Firing cost per employee:** $350.00
#### Capacity Data
- **Beginning workforce:** 210 employees
- **Beginning inventory:** 400 units
- **Labor standard per unit:** 6 hours
- **Regular time available per period:** 160 hours
- **Overtime available per period:** 30 hours
- **Subcontracting maximum per period:** 1000 units
- **Subcontracting minimum per period:** 500 units
#### Demand Data
- **Period 1:** 5500 units
- **Period 2:** 4600 units
- **Period 3:** 7600 units
- **Period 4:** 5800 units
- **Period 5:** 6560 units
- **Period 6:** 4000 units
This dataset provides cost, capacity, and demand information which can be used for production planning and workforce management in a manufacturing setting.
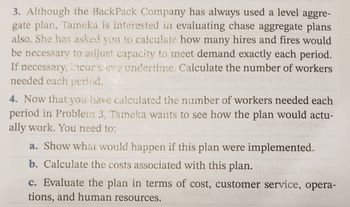
Transcribed Image Text:### Evaluating Aggregate Plans: BackPack Company Case Study
#### Task 3: Chase Aggregate Plan Evaluation
Although the BackPack Company has traditionally used a level aggregate plan, Tameka is interested in assessing chase aggregate plans as well. She has requested an analysis of the required hiring and firing to meet exact demand every period. If necessary, some undertime may be incurred. Your task is to calculate the number of workers needed for each period.
#### Task 4: Implementation and Evaluation of the Plan
After calculating the required number of workers for each period in Task 3, Tameka wants to understand the practical implications of this plan. You need to:
a. **Show what would happen if this plan were implemented.**
b. **Calculate the costs associated with this plan.**
c. **Evaluate the plan in terms of cost, customer service, operations, and human resources.**
This exercise provides a comprehensive understanding of the nuances involved in selecting and implementing aggregate planning strategies.
Expert Solution

This question has been solved!
Explore an expertly crafted, step-by-step solution for a thorough understanding of key concepts.
This is a popular solution
Trending nowThis is a popular solution!
Step by stepSolved in 3 steps with 3 images

Knowledge Booster
Similar questions
- Explain the Centroid Method technique?arrow_forwardAfter reading the stem et provided: Create a flowchart of the passenger arriving at an airport for departure process?arrow_forward3.) Compile a hypothetical list of stakeholders’ needs. Stakeholder Wants (“Whats”) System Attributes (“Hows”)arrow_forward
- Discuss the process used to overcome objections. This upcoming Tuesday will be the 3rd meeting the sales team from La Carva Luxury Bathtubs will be having with a prospect regarding bathtubs she would like to purchase. The sales team conducted a presentation five months ago to a group of prospects, which this prospect attended. While the prospect expresses great interest in the product, at the previous meetings she seems to have additional concerns regarding the bathtubs and was not able to come to a decision to make a purchase. This issue is becoming overwhelming, and the sales team intends to address this matter once and for all. Based on the listening technique in the LAER MODEL, how will this effectively address the prospect's objections? Explain. Please be mindful to use relevant personal selling and marketing concepts to support the claim.arrow_forwardPrim's MST approach may be utilized build a real-world weighted network.arrow_forwardAnswer number 3 only. Full solution. Unique answers only.arrow_forward
- Describe the role of a crisis management team in a continuity plan.arrow_forwardOnly 100% sure experts solve it correct complete solutions okkk no need chat gpt solutions. Handwriting solutions itarrow_forwardFor questions 32-35, use the word list to label the circular flow diagram. I Household Market (Households Sell. Firms Buy.) 35. Market (Firms Sell. Households Buy.) Businesse 34. Product Factor Firms sell goods and services Households sell the factors of production Households pay for the goods and servicesarrow_forward
arrow_back_ios
arrow_forward_ios
Recommended textbooks for you
- Practical Management ScienceOperations ManagementISBN:9781337406659Author:WINSTON, Wayne L.Publisher:Cengage,Operations ManagementOperations ManagementISBN:9781259667473Author:William J StevensonPublisher:McGraw-Hill EducationOperations and Supply Chain Management (Mcgraw-hi...Operations ManagementISBN:9781259666100Author:F. Robert Jacobs, Richard B ChasePublisher:McGraw-Hill Education
- Purchasing and Supply Chain ManagementOperations ManagementISBN:9781285869681Author:Robert M. Monczka, Robert B. Handfield, Larry C. Giunipero, James L. PattersonPublisher:Cengage LearningProduction and Operations Analysis, Seventh Editi...Operations ManagementISBN:9781478623069Author:Steven Nahmias, Tava Lennon OlsenPublisher:Waveland Press, Inc.
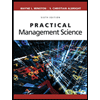
Practical Management Science
Operations Management
ISBN:9781337406659
Author:WINSTON, Wayne L.
Publisher:Cengage,
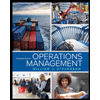
Operations Management
Operations Management
ISBN:9781259667473
Author:William J Stevenson
Publisher:McGraw-Hill Education
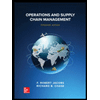
Operations and Supply Chain Management (Mcgraw-hi...
Operations Management
ISBN:9781259666100
Author:F. Robert Jacobs, Richard B Chase
Publisher:McGraw-Hill Education
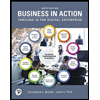
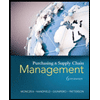
Purchasing and Supply Chain Management
Operations Management
ISBN:9781285869681
Author:Robert M. Monczka, Robert B. Handfield, Larry C. Giunipero, James L. Patterson
Publisher:Cengage Learning
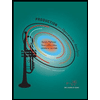
Production and Operations Analysis, Seventh Editi...
Operations Management
ISBN:9781478623069
Author:Steven Nahmias, Tava Lennon Olsen
Publisher:Waveland Press, Inc.