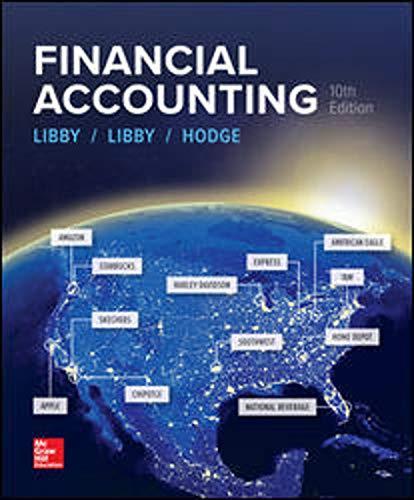
Concept explainers
Activity-Based Costing
Southeastern Paper Company manufactures three products (computer paper, newsprint, and specialty paper) in a continuous production process. Senior management has asked the controller to conduct an activity-based costing study. The controller identified the amount of factory
Activity | Activity Costs | ||
Production | $220,000 | ||
Setup | 117,000 | ||
Moving | 21,000 | ||
Shipping | 105,000 | ||
Product engineering | 102,000 | ||
Total | $565,000 |
The activity bases identified for each activity are as follows:
Activity | Activity Base | |
Production | Machine hours | |
Setup | Number of setups | |
Moving | Number of moves | |
Shipping | Number of customer orders | |
Product engineering | Number of test runs |
The activity-base usage quantities and units produced for the three products were determined from corporate records and are as follows:
Machine Hours |
Number of Setups |
Number of Moves |
Number of Customer Orders |
Number of Test Runs |
Units | |||||||
Computer paper | 400 | 80 | 230 | 310 | 50 | 1,000 | ||||||
Newsprint | 500 | 30 | 70 | 140 | 15 | 1,250 | ||||||
Specialty paper | 200 | 150 | 300 | 550 | 105 | 500 | ||||||
Total | 1,100 | 260 | 600 | 1,000 | 170 | 2,750 |
Each product requires 0.4 machine hour per unit.
Required:
1. Determine the activity rate for each activity.
Activity Rate | |
Production | $fill in the blank 1 /mh |
Setup | $fill in the blank 2 /setup |
Moving | $fill in the blank 3 /move |
Shipping | $fill in the blank 4 /cust. ord. |
Product Engineering | $fill in the blank 5 /test run |
2. Determine the total and per-unit activity cost for all three products. Round "Activity cost per unit" answers to two decimal places.
Computer Paper | Newsprint | Specialty Paper | |
Total activity cost | $fill in the blank 6 | $fill in the blank 7 | $fill in the blank 8 |
Activity cost per unit | $fill in the blank 9 | $fill in the blank 10 | $fill in the blank 11 |

Trending nowThis is a popular solution!
Step by stepSolved in 2 steps with 2 images

- Maxx Inc. has provided the following data from its activity-based costing system:Activity Cost Pools Total Cost Total ActivityDesigning products $383,900 6,580 product design hoursSetting up batches $52,678 7366 batch set-upsAssembling products $25,122 4,018 assembly hoursThe activity rate for the “designing products” activity cost pool is:arrow_forwardActivity-Based Product Costing Sweet Sugar Company manufactures three products (white sugar, brown sugar, and powdered sugar) in a continuous production process. Senior management has asked the controller to conduct an activity-based costing study. The controller identified the amount of factory overhead required by the critical activities of the organization as follows: Activity Budgeted Activity Cost Production $415,800 Setup 268,800 Inspection 131,200 Shipping 111,600 Customer service 93,800 Total $1,021,200 The activity bases identified for each activity are as follows: Activity Activity Base Production Machine hours Setup Number of setups Inspection Number of inspections Shipping Number of customer orders Customer service Number of customer service requests The activity-base usage quantities and units produced for the three products were determined from corporate records and are as follows: Machine Hours Number…arrow_forwardEntries for Flow of Factory Costs for Process Costing Keoni Inc. manufactures a sugar product by a continuous process, involving three production departments-Refining, Sifting, and Packing. Assume that records indicate that direct materials, direct labor, and applied factory overhead for the first department, Refining, were $522,500, $182,900, and $120,200, respectively. Also, work in process in the Refining Department at the beginning of the period totaled $29,300, and work in process at the end of the period totaled $36,100. a. Journalize the entries to record the flow of costs into the Refining Department during the period for (1) direct materials, (2) direct labor, and (3) factory overhead. If an amount box does not require an entry, leave it blank. 1. 2. 3. b. Journalize the entry to record the transfer of production costs to the second department, Sifting. If an amount box does not require an entry, leave it blank.arrow_forward
- Greenwood Company manufactures two products-13,000 units of Product Y and 5,000 units of Product Z. The company uses a plantwide overhead rate based on direct labor-hours. It is considering implementing an activity- based costing (ABC) system that allocates all of its manufacturing overhead to four cost pools. The following additional information is available for the company as a whole and for Products Y and Z: Activity Cost Pool Machining Machine setups Production design General factory Activity Measure Machining Windows DESKTOP- Windows Number of setups Number of products Direct labor-hours Total overhead cost Activity Measure Machine-hours Number of setups Number of products Direct labor-hours Product Y FEB +1 (252) 484-2153 Oh nun Product Y Product Z 8,800 3,200 240 40 1 1 8,800 3,200 11. Using the plantwide overhead rate, what percentage of the total overhead cost is allocated to Product Y an Product Z? (F your intermediate calculations to 2 decimal places. Round your answers to 2…arrow_forwardTeach Gear Inc. produces 3 types of office equipment; Bronze, silver and Gold and uses an activity-based product costing system. They have identified 5 activities. Each activity, it costs and related activity driver is summarized below: Activity Material handling Material insertion Activity Units to be produced Orders to be shipped Number of parts per unit Machine hours per unit Labor hours per unit Cost Tasks: Automated Machinery finishing Packaging The following data are provided for each product line: Activity driver Number of parts Number of parts 350,000 Machine hours 150,000 Labor hours 90,000 Orders shipped Bronze P120,000 240,000 6,000 1,200 4. 1 2 Silver 4,000 800 5 2 3 Gold 2,000 400 8 3 لنا Make a narrative recommend the unit cost per unit of Bronze, Silver and Gold using the ABC system. In support of your recommendation show your solution presenting: 1. The computation of the activity cost rates 2. the computation of the estimated volume (TOTAL PARTS, TOTAL MACHINE HOURS,…arrow_forwardMello Manufacturing Company is a diversified manufacturer that manufactures three products (Alpha, Beta, and Omega) in a continuous production process. Senior management has asked the controller to conduct an activity-based costing study. The controller identified the amount of factory overhead required by the critical activities of the organization as follows: Activity Activity Cost Pool Production $259,200 Setup 55,000 Materials handling 9,750 Inspection 60,000 Product engineering 123,200 Total $507,150 The activity bases identified for each activity are as follows: Activity Activity Base Production Machine hours Setup Number of setups Materials handling Number of parts Inspection Number of inspection hours Product engineering Number of engineering hours The activity-base usage quantities and units produced for the three products were determined from corporate records and are as follows: Machine Hours Number of…arrow_forward
- XYZ has provided the following data from its activity-based costing system: Activity Cost Pool Total Cost Total Activity Assembly $228,060 18,000 machine-hours Processing orders $ 34,068 1,600 orders Inspection $125,560 1,700 inspection hours The company makes 420 units of product YBY a year, requiring a total of 460 machine-hours, 80 orders, and 20 inspection-hours per year. The product's direct materials cost is $48.96 per unit and its direct labor cost is $25.36 per unit. According to the activity-based costing system, the average cost of product YBY is closest to: O a. $93.99 per unit O b. None of the given answer is correct. O. $95.77 per unit O d. $94.00 per unit O e. $94.26 per unit CLEAR MY CHOICE MacBook Air 20 F3 F1 $ % & # 5 6. 7 8 1 2 3 4 T. Y Q W E と K F G تثبيت A (( S V alt الأوامر C. I Rarrow_forwardActivity-Based Costing: Factory Overhead Costs The total factory overhead for Bardot Marine Company is budgeted for the year at $1,207,500, divided into four activities: fabrication, $595,000; assembly, $266,000; setup, $189,000; and inspection, $157,500. Bardot Marine manufactures two types of boats: speedboats and bass boats. The activity-base usage quantities for each product by each activity are as follows: Inspection Speedboat Bass boat Fabrication Assembly 462 525 setups Each product is budgeted for 7,500 units of production for the year. a. Determine the activity rates for each activity. 17 per direct labor hour 7 per direct labor hour Setup Inspection Fabrication 8,750 dlh $ $ Speedboat Bass boat Assembly Setup 28,500 dlh 9,500 38,000 dlh 26,250 35,000 dlh 63 setups 360 per setup 180 per inspection b. Determine the activity-based factory overhead per unit for each product. Round to the nearest whole dollar. $ per unit $ per unit 109 inspections 766 875 inspectionsarrow_forward
- AccountingAccountingISBN:9781337272094Author:WARREN, Carl S., Reeve, James M., Duchac, Jonathan E.Publisher:Cengage Learning,Accounting Information SystemsAccountingISBN:9781337619202Author:Hall, James A.Publisher:Cengage Learning,
- Horngren's Cost Accounting: A Managerial Emphasis...AccountingISBN:9780134475585Author:Srikant M. Datar, Madhav V. RajanPublisher:PEARSONIntermediate AccountingAccountingISBN:9781259722660Author:J. David Spiceland, Mark W. Nelson, Wayne M ThomasPublisher:McGraw-Hill EducationFinancial and Managerial AccountingAccountingISBN:9781259726705Author:John J Wild, Ken W. Shaw, Barbara Chiappetta Fundamental Accounting PrinciplesPublisher:McGraw-Hill Education
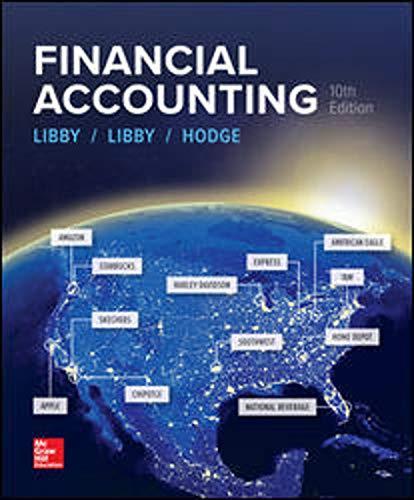
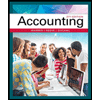
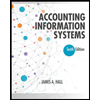
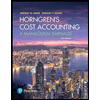
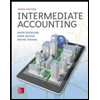
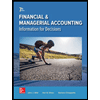