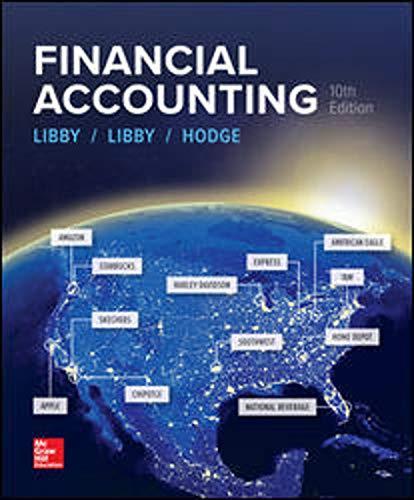
Concept explainers
Performance Gloves, Inc. produces three sizes of sports gloves: small, medium, and large. A
glove pattern is first stenciled onto leather in the Pattern Department. The stenciled patterns
are then sent to the Cut and Sew Department, where the glove is cut and sewed together.
Performance Gloves uses the multiple production department factory
allocating
Department Dollar Amount
Pattern Department $216,000
Cut and Sew Department 960,000
Total Overhead 1,176,000
The direct labor estimated for each production department was as follows:
Department Direct Labor Hours
Pattern Department 36,000
Cut and Sew Department 60,000
Total Direct Labor Hours 96,000
Direct labor hours are used to allocate the production department overhead to the products.
The direct labor hours per unit for each product for each production department were obtained
from the engineering records as follows:
Production Departments Small Glove Medium Glove Large Glove
Pattern Department .30 .35 .40
Cut and Sew Department .60 .50 .84
Total Direct Labor Hours per Unit .90 .85 1.24
a. Determine the two production department factory overhead rates.
b. Use the two production department factory overhead rates to determine the factory
overhead per unit for each product.

Trending nowThis is a popular solution!
Step by stepSolved in 3 steps

- Spacely, Corp. makes sprockets in two models: regular and professional, and wants to refine its costing system by allocating overhead using departmental rates. The estimated $843,100 of manufacturing overhead has been divided into two cost pools: Assembly Department and Packaging Department.The following data has been compiled: Spacely, Corp. Assembly Department Packaging Department Total Overhead costs $550,000 $293,100 $843,100 Machine Hours: Regular Model 153,000 35,100 188,100 Professional Model 352,400 12,600 365,000 Direct Labor Hours: Regular Model 40,300 80,600 120,900 Professional Model 322,700 413,400 736,100 (Round your answers to two decimal places when needed and use rounded answers for all future calculations).arrow_forwardLens Care Inc. (LCI) manufactures specialized equipment for polishing optical lenses. There are two models - one mainly used for fine eyewear (F-32) and another for lenses used in binoculars, cameras, and similar equipment (B-13). The manufacturing cost of each unit is calculated using activity-based costing, using the following manufacturing cost pools: Cost Pools Allocation Base Costing Rate Materials handling Number of parts $ 3.60 per part Manufacturing supervision Hours of machine time $ 14.92 per hour Assembly Number of parts $ 3.90 per part Machine setup Each setup $ 57.10 per setup Inspection and testing Logged hours $ 46.10 per hour Packaging Logged hours $ 20.10 per hour LCI currently sells the B-13 model for $4,475 and the F-32 model for $4,580. Manufacturing costs and activity usage for the two products are as follows: B-13 F-32 Direct materials $ 165.10 $ 76.08 Number of parts 172 132 Machine hours 8.50…arrow_forwardHamilton, a decorative wall clock manufacturer uses activity-based costing. Each clock consists of 20 separate parts totaling $95 in direct materials, and requires 2.5 hours of machine time to produce. Additional information is as follows: Activity Materials handling Number of parts Machining Machine hours Assembling Packaging What is the cost of machining per clock? Multiple Choice $144.00 Allocation Base $180.00 Number of parts Number of finished clocks Cost Allocation Rate $ 0.08 7.20 0.35 2.70arrow_forward
- Riverbed Delights manufactures a wide variety of holiday and seasonal decorative items. Riverbed's activity-based costing overhead rates are: Purchasing Storing Machining Supervision Total cost $394 per order S $2 per square foot/days $100 per machine hour The Snow Man project involved 3 purchase orders, 5,400 square feet/days, 74 machine hours, and 54 direct labor hours. The cost of direct materials on the job was $20,400 and the direct labor rate is $32 per hour. Determine the total cost of the Snow Man project. $5 per direct labor hourarrow_forwardMartay Creations produces winter scarves. The scarves are produced in the Cutting and Sewing departments. The Maintenance and Security departments support these production departments, and allocate costs based on machine hours and square feet, respectively. Information about each department is provided in the following table: Department Total Cost Number of Employees Machine Hours Square Feet Maintenance Department $2,200 5 40 600 Security Department 4,500 3 0 500 Cutting Department 21,200 21 3,600 2,400 Sewing Department 24,900 19 5,400 3,000 Using the sequential method and allocating the support department with the highest costs first, allocate all support department costs to the production departments. Then compute the total cost of each production department. Line Item Description CuttingDepartment SewingDepartment…arrow_forwardGibson Company produces commercial gardening equipment. Since production is highly automated, the company allocates its overhead costs to product lines using activity-based costing. The costs and cost drivers associated with the four overhead activity cost pools follow: Cost Cost driver Unit Level $50,600 Req A and B 2,300 labor hours. Production of 890 sets of cutting shears, one of the company's 20 products, took 210 labor hours and 9 setups and consumed 10 percent of the product-sustaining activities. Complete this question by entering your answers in the tabs below. Req C a. Allocated cost b. Allocated cost Activities Batch Level $ 21,160 46 setups Required a. Had the company used labor hours as a companywide allocation base, how much overhead would it have allocated to the cutting shears? b. How much overhead is allocated to the cutting shears using activity-based costing? c. Compute the overhead cost per unit for cutting shears first using activity-based costing and then using…arrow_forward
- Activity-Based Costing: Factory Overhead Costs The total factory overhead for Bardot Marine Company is budgeted for the year at $1,347,400, divided into four activities: fabrication, $660,000; assembly, $276,000; setup, $224,400; and inspection, $187,000. Bardot Marine manufactures two types of boats: speedboats am bass boats. The activity-base usage quantities for each product by each activity are as follows: Fabrication Assembly Setup Inspection Speedboat 11,000 dlh 34,500 dlh 79 setups 138 inspections Bass boat 33,000 11,500 581 962 44,000 dlh 46,000 dlh 660 setups 1,100 inspections Each product is budgeted for 6,500 units of production for the year. a. Determine the activity rates for each activity. Fabrication per direct labor hour Assembly %$4 per direct labor hour Setup %$4 per setup Inspection per inspection b. Determine the activity-based factory overhead per unit for each product. Round to the nearest whole dollar. Speedboat per unit Bass boat %$4 per unitarrow_forwardMultiple Production Department Factory Overhead Rate Method Handy Leather, Inc., produces three sizes of sports gloves: small, medium, and large. A glove pattern is first stenciled onto leather in the Pattern Department. The stenciled patterns are then sent to the Cut and Sew Department, where the glove is cut and sewed together. Handy Leather uses the multiple production department factory overhead rate method of allocating factory overhead costs. Its factory overhead costs were budgeted as follows: Pattern Department overhead Cut and Sew Department overhead Total The direct labor estimated for each production department was as follows: Pattern Department 1,600 direct labor hours Cut and Sew Department 2,000 Total 3,600 direct labor hours Direct labor hours are used to allocate the production department overhead to the products. The direct labor hours per unit for each product for each production department were obtained from the engineering records as follows: Production Departments…arrow_forwardRundle Company produces commercial gardening equipment. Since production is highly automated, the company allocates its overhead costs to product lines using activity-based costing. The costs and cost drivers associated with the four overhead activity co pools follow: Cost Cost driver Req A and B Unit Level $ 25,200 Req C a. Allocated cost b. Allocated cost Production of 880 sets of cutting shears, one of the company's 20 products, took 130 labor hours and 10 setups and consumed 15 percent of the product-sustaining activities. Required 8. Had the company used labor hours as a companywide allocation base, how much overhead would it have allocated to the cutting shears? Complete this question by entering your answers in the tabs below. 1,200 labor hours b. How much overhead is allocated to the cutting shears using activity-based costing? c. Compute the overhead cost per unit for cutting shears first using activity-based costing and then using direct labor hours for allocation if 880…arrow_forward
- The Platter Valley factory of Bybee Industries manufactures field boots. The cost of each boot includes direct materials, direct labor, and manufacturing (factory) overhead. The firm traces all direct costs to products, and it assigns overhead cost to products based on direct labor hours. The company budgeted $15,000 variable factory overhead cost, $90,000 for fixed factory overhead cost and 2,500 direct labor hours (its practical capacity) to manufacture 5,000 pairs of boots in March. The factory used 2,700 direct labor hours in March to manufacture 4,800 pairs of boots and spent $15,600 on variable overhead during the month. The actual fixed overhead cost incurred for the month was $92,000. Required: 1. Compute the factory overhead flexible-budget variance, the factory overhead spending variance, and the efficiency variance for variable factory overhead for March and state whether each variance is favorable (F) or unfavorable (U). 2. Provide the appropriate journal entry to record…arrow_forwardSpacely, Corp. makes sprockets in two models: regular and professional, and wants to refine its costing system by allocating overhead using departmental rates. The estimated $843,100 of manufacturing overhead has been divided into two cost pools: Assembly Department and Packaging Department.The following data has been compiled: Spacely, Corp. Assembly Department Packaging Department Total Overhead costs $550,000 $293,100 $843,100 Machine Hours: Regular Model 153,000 35,100 188,100 Professional Model 352,400 12,600 365,000 Direct Labor Hours: Regular Model 40,300 80,600 120,900 Professional Model 322,700 413,400 736,100 (Round your answers to two decimal places when needed and use rounded answers for all future calculations).1. Compute the predetermined overhead allocation rates using machine hours as the allocation base for the Assembly Department and direct labor hours for the Packaging Department.arrow_forwardCheyenne Delights manufactures a wide variety of holiday and seasonal decorative items. Cheyenne's activity-based costing overhead rates are: Purchasing Storing Machining Supervision Total cost $385 per order $ $2 $100 per machine hour per square foot/days The Snow Man project involved 3 purchase orders, 4,500 square feet/days, 65 machine hours, and 45 direct labor hours. The cost of direct materials on the job was $19,500 and the direct labor rate is $30 per hour. Determine the total cost of the Snow Man project. $5 per direct labor hourarrow_forward
- AccountingAccountingISBN:9781337272094Author:WARREN, Carl S., Reeve, James M., Duchac, Jonathan E.Publisher:Cengage Learning,Accounting Information SystemsAccountingISBN:9781337619202Author:Hall, James A.Publisher:Cengage Learning,
- Horngren's Cost Accounting: A Managerial Emphasis...AccountingISBN:9780134475585Author:Srikant M. Datar, Madhav V. RajanPublisher:PEARSONIntermediate AccountingAccountingISBN:9781259722660Author:J. David Spiceland, Mark W. Nelson, Wayne M ThomasPublisher:McGraw-Hill EducationFinancial and Managerial AccountingAccountingISBN:9781259726705Author:John J Wild, Ken W. Shaw, Barbara Chiappetta Fundamental Accounting PrinciplesPublisher:McGraw-Hill Education
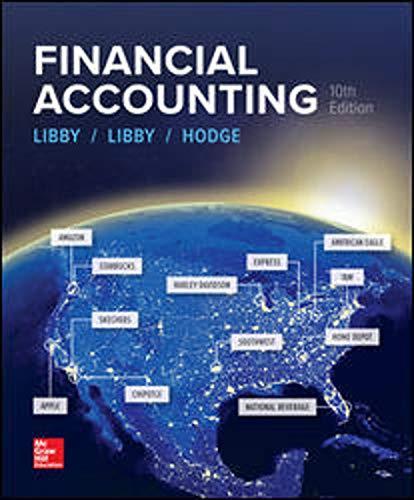
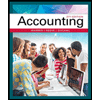
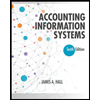
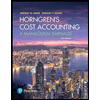
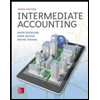
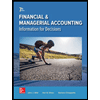