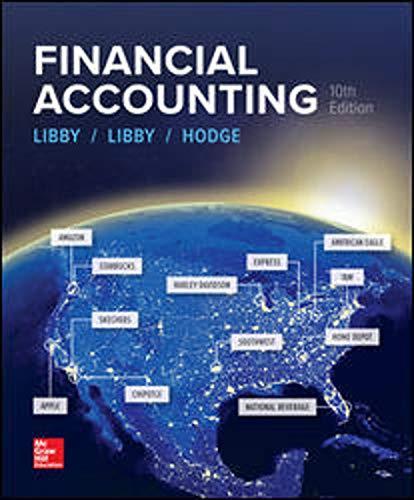
Komatsu, Ltd.
Komatsu Ltd was one of Japan's largest heavy industrial manufacturers. Komatsu was a large international firm with revenues of ¥989 billion. The company was organized on three major lines of business: Construction equipment, industrial machinery, and electronic-applied products.
Construction Equipment
Komatsu was the world's 2nd-largest manufacturer of a complete line of construction equipment. The firm's product line contained over 300 models, including bulldozers, hydraulic excavators, wheel loaders, and dump trucks. With a more than 30% share of the domestic excavator market, Komatsu was the largest player in the Japanese market.
The Product Development Process and Design for
The product development process at Komatsu lasted 2 years on average.
The Product Planning Stage
The product planning process, which was last updated in 1981, began with the preparation of a long-range development plan.
The Design Stage
The objective of the design stage of product development was to prepare the product for prototype production. The design phase consisted of 3 major steps: 1st, a conceptual drawing of the product: 2nd, layout drawings for the product and third, detailed parts drawings. During the first step, the first of four design-for-manufacturability studies was conducted. The A study evaluated the feasibility of achieving the target cost and the overall manufacturability of the design .
The Trial Production Stage
The objective of the trial production stage was to finalize the design of the product Trial production consisted of producing prototypes of each product and was conducted at the plants at which the product was to be manufactured. The completion of trial production allowed the final, or D. study to be carried out . This study examined the ease of production and assembly of the new product and confirmed its quality. If any problems were encountered, a Trial-Manufacture Problem Document was issued.
Reducing the Time to Market
Players in the highly competitive market for excavators and bulldozers had begun to compete based on the time it took to get new products to market. Part of Komatsu's plan to improve its design for manufacturing was to change its relationship with its suppliers. In 1993, Komatsu manufactured about 30% of its products, designed and subcontracted another 50%, and purchased from outside suppliers the remaining 20%.
Target Costing
Throughout the product development
These preliminary target costs or target values, were used to help identify when the application of cost reduction techniques was required.
Product engineers were expected to identify several design alternatives for each major subassembly of a new product. Two factors were considered: quality and cost. A new design alternative was only adopted if it achieved both the desired levels of quality and cost. Frequently, one of the alternatives proposed produced a higher quality product but at a higher cost. The product engineers then explored ways to manufacture the higher quality alternative at a lower cost. If a cost-effective way to implement the new alternative was identified, then it was adopted; otherwise, the alternative was abandoned or subject to further study for future applications.
The process of design analysis in the way the engine and torque converter, transmission, and steering clutch and brakes were positioned in the firm's larger bulldozers. In the old design, these three modules were physically separate. This approach, required 86 hours to mount and dismount these modules during maintenance.
The process of functional analysis at Komatsu can be illustrated by the development of the target cost of an excavator cooling system. It began with an analysis of the functions of the cooling system and how they were achieved. The primary function was identified as its cooling capacity; secondary functions included how quickly it started cooling after the engine was first switched on and how stable a temperature it maintained.
The determinants of cooling capacity were ranked in the order of importance. The most important determinant of cooling capacity was identified as the surface area of the radiator. The second most important determinant was the size of the fan, followed by the rotation speed of the fan, the volume of water in the system, and the ambient air temperature, The functional analysis began by plotting the cooling capacity versus the radiator surface area for all existing products that used the same type of cooling system.
Required:
What are the strengths and weaknesses of Komatsu's target costing system?

Step by stepSolved in 6 steps

- Medical Equipment Ltd produces components for medical robotic equipment. It has two divisions, the motor division and the medical application division. The motor division currently manufactures 100,000 motors, selling 80,000 motors externally for $100 per motor and 20,000 to the medical application division for $50 per motor. The following table provides total details for the motors. Medical applications division External customers Transfer price/Sales 1,000,000 8,000,000 Variable costs (900,000) (3,600,000) Fixed costs (400,000) (1,200,000) Gross margin (300,000) 3,200,000 Unit sales 20,000 80,000 If the motor division negotiated a transfer price of $62.50 per motor, what would the contribution margin and profit margin for the internal transfer to the medical application division become? a. Contribution margin zero; Profit zero b. Contribution margin $20; Profit zero c.…arrow_forwardMackenzie Mining has two operating divisions, Northern and Southern, that share the common costs of the company’s human resources (HR) department. The annual costs of the HR department total $25,000,000 a year. You have the following selected information about the two divisions: Number of Employees Wage and Salary Expense ($000) Northern 2,915 $ 241,800 Southern 2,385 148,200 Required: What is the HR cost that is charged to each division if the number of employees is used as the allocation basis? What is the HR cost that is charged to each division if the wage and salary expense total is used as the allocation basis?arrow_forwardWhitehill Chemicals has two operating divisions. Its Formulation Division in the United States mixes, processes, and tests basic chemicals, and then ships them to Ireland, where the company's Commercial Division uses the chemicals to produce and sell various products. Operating expenses amount to $26.6 million in the U.S. and $78.6 million in Ireland exclusive of the costs of any goods transferred from the U.S. Revenues in Ireland are $201 million. If the chemicals were purchased from one of the company's Irish mixing divisions, the costs would be $39.6 million. However, if it had been purchased from an independent U.S. supplier, the cost would be $52.6 million. The marginal income tax rate is 20 percent in the U.S. and 12 percent in Ireland. Required: What is the company's total tax liability to both jurisdictions for each of the two alternative transfer pricing scenarios ($39.6 million and $52.6 million)? Note: Enter your answers in dollars and not in millions of dollars. Total tax…arrow_forward
- Carving Creations jointly produces wood chips and sawdust used in agriculture. The wood chips and sawdust are actually by-products of the company’s core operations, but Carving Creations accounts for them just like normally produced goods because of their large volumes. One jointly produced batch yields 3,000 cubic yards of wood chips and 10,000 cubic yards of sawdust, and the estimated cost per batch is $21,400. However, the joint production of each good is not equally weighted. Management at Carving Creations estimates that for the time it takes to produce 10 cubic yards of wood chips in the joint production process, only 2 cubic yards of sawdust are produced. Given this information, allocate the joint costs of production to each product using the weighted average method.arrow_forwardThe centralized computer technology department of Lee Company has expenses of$264,000. The department has provided a total of 2,500 hours of service for the period. TheRetail Division has used 1,125 hours of computer technology service during the period, andthe Commercial Division has used 1,375 hours of computer technology service. How mucheach division should be charged for computer technology department services?arrow_forwardFederated Manufacturing Incorporated (FMl) produces electronic components in three divisions: industrial, commercial, and consumer products. The commercial products division annually purchases 10,000 units of part 23-6711, which the industrial division produces for use in manufacturing one of its own products. The commercial division is growing rapidly; it is expanding its production and now wants to increase its purchases of part 23-6711 to 15,000 units per year. The problem is that the industrial division is at full capacity. No new investment in the industrial division has been made for some years because top management sees little future growth in its products, so its capacity is unlikely to increase soon. The commercial division can buy part 23-6711 from Advanced Micro Incorporated or from Admiral Electric, a customer of the industrial division now purchasing 650 units of part 88-461. The industrial division's sales to Admiral would not be affected by the commercial division's…arrow_forward
- AccountingAccountingISBN:9781337272094Author:WARREN, Carl S., Reeve, James M., Duchac, Jonathan E.Publisher:Cengage Learning,Accounting Information SystemsAccountingISBN:9781337619202Author:Hall, James A.Publisher:Cengage Learning,
- Horngren's Cost Accounting: A Managerial Emphasis...AccountingISBN:9780134475585Author:Srikant M. Datar, Madhav V. RajanPublisher:PEARSONIntermediate AccountingAccountingISBN:9781259722660Author:J. David Spiceland, Mark W. Nelson, Wayne M ThomasPublisher:McGraw-Hill EducationFinancial and Managerial AccountingAccountingISBN:9781259726705Author:John J Wild, Ken W. Shaw, Barbara Chiappetta Fundamental Accounting PrinciplesPublisher:McGraw-Hill Education
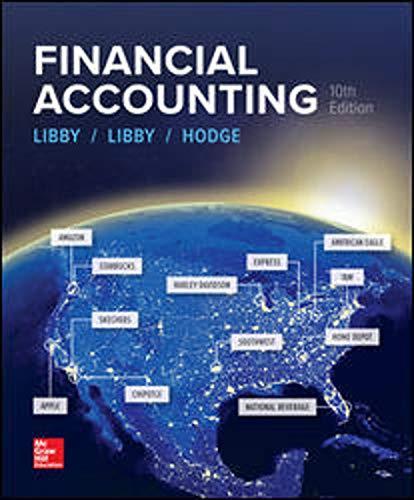
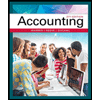
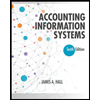
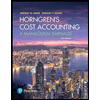
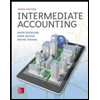
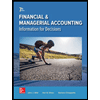