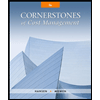
Cornerstones of Cost Management (Cornerstones Series)
4th Edition
ISBN: 9781305970663
Author: Don R. Hansen, Maryanne M. Mowen
Publisher: Cengage Learning
expand_more
expand_more
format_list_bulleted
Question
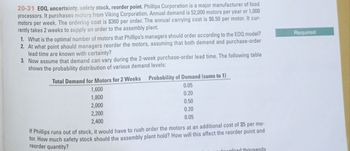
Transcribed Image Text:20-31 EOQ, uncertainty, safety stock, reorder point. Phillips Corporation is a major manufacturer of food
processors. It purchases motors from Viking Corporation. Annual demand is 52,000 motors per year or 1,000
motors per week. The ordering cost is $360 per order. The annual carrying cost is $6.50 per motor. It cur-
rently takes 2 weeks to supply an order to the assembly plant.
1. What is the optimal number of motors that Phillips's managers should order according to the EOQ model?
2. At what point should managers reorder the motors, assuming that both demand and purchase-order
lead time are known with certainty?
3. Now assume that demand can vary during the 2-week purchase-order lead time. The following table
shows the probability distribution of various demand levels:
Required
Total Demand for Motors for 2 Weeks
1,600
1,800
2,000
2,200
Probability of Demand (sums to 1)
0.05
0.20
0.50
0.20
0.05
2,400
If Phillips runs out of stock, it would have to rush order the motors at an additional cost of $5 per mo-
tor. How much safety stock should the assembly plant hold? How will this affect the reorder point and
reorder quantity?
download thousands
Expert Solution

This question has been solved!
Explore an expertly crafted, step-by-step solution for a thorough understanding of key concepts.
Step by stepSolved in 2 steps with 1 images

Knowledge Booster
Similar questions
- Subject management accoun Please help solve all.. please A company is planning to purchase 90,800 units of a particular item in the year ahead. The item is purchased in boxes each containing 10units of the item, at a price of $200 per box. A safety inventory of 250 boxes is kept. Besides, the company estimates to be charged the transporation cost of $15 per order. It should be assumed that ordering costs change in proportion to the number of orders place. The cost of holding an item in inventory for a year (including insurance, interest and space costs) is 15% of the purchase price. The cost of placing and receiving orders is to be estimated from cost data collected relating to similar orders, where costs of $5,910 were incurred on 30 orders. It should be assumed that ordering costs change in proportion to the number of orders placed. 2% should be added to the above ordering costs to allow for inflation. Assume that usage of the item will be even over the year. Required a. Calculate…arrow_forward16) can you please help with this question?arrow_forwardC E H The ABC Semi Conductor Company purchase 40,000 units of mother board each year at a cost of $30.00 per unit. The ordering cost is $10.00 per order, and the annual holding cost is estimated at 15% of the unit value. 1. What is the EOQ for the ABC? 2. What is the total annual inventory cost for the mother board if it is ordered in economic quantities? 3. How many orders should be placed each year? D Demand 40000 units H Holding Cost S Ordering Cost 4.5 $/unit/yr 10 $/order Case 1 Case 2 Case 3 Case 4 Case 5 Case 6 Case 7 Quantity Average Total Holding Cost Total Ordering Cost Total COST = 100 200 300 400 500 1000 2000arrow_forward
- Bell Computors purchases integrated chips at $350 per chip. The holding cost is $37 per unit per year, the ordering cost is $118 per order, and sales are steady at 405 per month. The company's supplier, Rich Blue Chip Manufacturing, Inc., decides to offer price concessions in order to attract larger orders. The price structure is shown below. Rich Blue Chip's Price Structure Quantity Purchased 1-99 units 100-199 units 200 or more units PricelUnit $350 $325 $300 a) What in the optimal order quantity and the minimum annual cost for Bell Computeni to order, purchase, and hold these integrated chips? The optimal order quantity after the change in pricing structure isunits (ontor your response as a whole numberd. The total annual cost for Bell computers to order, purchase, and hold the integrated chips is $ (round your response to the nearest whole number).arrow_forwardQUESTION NO 3: The Knot manufactures men’s neckwear at its Spartanburg plant. The Knot is considering implementing a JIT production system. The following are the estimated costs and benefits of JIT production: a. Annual additional tooling costs $250,000 annually. b. Average inventory would decline by 80% from the current level of $1,000,000. c. Insurance, space, materials-handling, and setup costs, which currently total $400,000 annually, would decline by 20%. d. The emphasis on quality inherent in JIT production would reduce rework costs by 25%. The Knot currently incurs $160,000 in annual rework costs. e. Improved product quality under JIT production would enable The Knot to raise the price of its product by $2 per unit. The Knot sells 100,000 units each year. The Knot’s required rate of return on inventory investment is 15% per year. 1. Calculate the net benefit or cost to The Knot if it adopts JIT production at the Spartanburg plant. 2. What nonfinancial and qualitative factors…arrow_forwardCASE 5 Cool Stuff, Inc. uses 800 units of a product per year on a continuous basis. The product has carrying costs of $50 per unit per year and order costs of $300 per order. It takes 30 days to receive a shipment after an order is placed and the firm requires a safety stock of 5 days usage in inventory. Required: (PLEASE ANSWER 4 TO 7 ONLY) 4. Determine the number of orders. 5. How much is the total carrying cost? 6. How much is the total ordering cost? 7. How much is the total cost of inventory 8. What will be your advice to the management?arrow_forward
- Solve this problemarrow_forward5. Genesis Company is a wholesaler. It purchases 60.000 units of Product X per month for sale to retailers. The cost of placing an order is P100. The cost of holding one unit of inventory for one year is P4. Note: Kindly input your answer with comma. Example: 10,000 Required: Previously, the company had been purchasing 5,000 units of product X per order: a. What is the ordering cost per year under the previous policy? b. The annual carrying cost? c. How much money does the company save over the policy of purchasing 5,000 units per order using the EOQ policy?arrow_forwardPlz solve correctly. An automotive supply store sells a product that has a demand of 400 units per month. Its supplier charges an ordering cost of $60 per order and $25 per unit with a 20% discount for orders of 250 units or higher. The store incurs a 20% annual holding cost. What is the store’s total annual cost (purchasing, ordering, and holding) if it orders at a quantity of 300 units? a. $121,560 b. $96,000 c. $120,000 d. $97,560arrow_forward
- Please answer the accounting question solve this onearrow_forwardGeneral Accounting Question need helparrow_forward1. A company manufactures and sells a single product. The variable cost of the product is $2.50 per unit and all production each month is sold at a price of $3.70 per unit. A potential new customer has offered to buy 6,000 units per month at a price of $2.95 per unit. The company has sufficient spare capacity to produce this quantity. If the new business is accepted, sales to existing customers are expected to fall by two units for every 15 units sold to the new customer. What would be the overall increase in monthly profit which would result from accepting the new business? (a) $1,740 (b) $2,220 (c) $2,340 (d) $2,700arrow_forward
arrow_back_ios
SEE MORE QUESTIONS
arrow_forward_ios
Recommended textbooks for you
- Cornerstones of Cost Management (Cornerstones Ser...AccountingISBN:9781305970663Author:Don R. Hansen, Maryanne M. MowenPublisher:Cengage LearningEBK CONTEMPORARY FINANCIAL MANAGEMENTFinanceISBN:9781337514835Author:MOYERPublisher:CENGAGE LEARNING - CONSIGNMENT
- Managerial Accounting: The Cornerstone of Busines...AccountingISBN:9781337115773Author:Maryanne M. Mowen, Don R. Hansen, Dan L. HeitgerPublisher:Cengage LearningPrinciples of Accounting Volume 2AccountingISBN:9781947172609Author:OpenStaxPublisher:OpenStax College
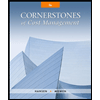
Cornerstones of Cost Management (Cornerstones Ser...
Accounting
ISBN:9781305970663
Author:Don R. Hansen, Maryanne M. Mowen
Publisher:Cengage Learning
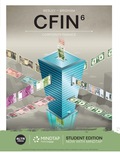
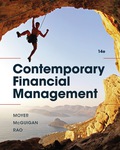
EBK CONTEMPORARY FINANCIAL MANAGEMENT
Finance
ISBN:9781337514835
Author:MOYER
Publisher:CENGAGE LEARNING - CONSIGNMENT
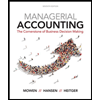
Managerial Accounting: The Cornerstone of Busines...
Accounting
ISBN:9781337115773
Author:Maryanne M. Mowen, Don R. Hansen, Dan L. Heitger
Publisher:Cengage Learning
Principles of Accounting Volume 2
Accounting
ISBN:9781947172609
Author:OpenStax
Publisher:OpenStax College