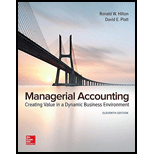
Concept explainers
Morelli Electric Motor Corporation manufactures electric motors for commercial use. The company produces three models, designated as standard, deluxe, and heavy-duty. The company uses a
For the past 10 years, the company’s pricing formula has been to set each product’s target price at 110 percent of its full product cost. Recently, however, the standard-model motor has come under increasing price pressure from offshore competitors. The result was that the price on the standard model has been lowered to $110.
The company president recently asked the controller, “Why can’t we compete with these other companies? They’re selling motors just like our standard model for 106 dollars. That’s only a buck more than our production cost. Are we really that inefficient? What gives?”
The controller responded by saying, “I think this is due to an outmoded product-costing system. As you may remember, I raised a red flag about our system when I came on board last year. But the decision was to keep our current system in place. In my judgment, our product-costing system is distorting our product costs. Let me run a few numbers to demonstrate what I mean.”
Getting the president’s go-ahead, the controller compiled the basic data needed to implement an activity-based costing system. These data are displayed in the following table. The percentages are the proportion of each cost driver consumed by each product line.
Required:
- 1. Compute the target prices for the three models, based on the traditional, volume-based product costing system.
- 2. Compute new product costs for the three products, based on the new data collected by the controller. Round to the nearest cent.
- 3. Calculate a new target price for the three products, based on the activity-based costing system. Compare the new target price with the current actual selling price for the standard-model electric motor.
- 4. Write a memo to the company president explaining what has been happening as a result of the firm’s traditional, volume-based product-costing system.
- 5. What strategic options does Morelli Electric Motor Corporation have? What do you recommend, and why?

Want to see the full answer?
Check out a sample textbook solution
Chapter 5 Solutions
Managerial Accounting: Creating Value in a Dynamic Business Environment
- Please need answer the general accounting question not use aiarrow_forwardGroot Co. (GC) sells $1,200,000 of 6-year, 10% bonds at par plus accrued interest. The bonds are dated January 1, 2026 but due to market conditions are not issued until May 1, 2026. Interest is payable on June 30 and December 31 each year. The market rate of interest at time of issue is the same as the stated rate. Required The issuance of the bonds on May 1, 2026. Assume that GC has adopted a policy of crediting accrued interest payable for the accrued interest on the date of sale. Payment of interest on June 30, 2026. Payment of interest on December 31, 2026.arrow_forward1. Define working capital and explain its importance in financial health and liquidity management. 2. Assess how the matching concept and accrual basis affect the reporting of current assets and liabilities. 3. Using a hypothetical balance sheet (you may create one), identify at least 5 current assets and 5 current liabilities and analyze how changes in these elements affect liquidity ratios. 4. Recommend at least two strategies VinGrenDom Ltd. can implement to optimize working capital.arrow_forward
- Theron Interiors manufactures handcrafted cabinetry and uses a process costing system. During the month of October, the company started Production on 720 units and completed 590 units. The remaining 120 units were 60% complete in terms of materials and 40% complete in terms of labor and overhead. The total cost incurred during the month was $45,000 for materials and $31,200 for labor and overhead. Using the weighted-average method, what is the equivalent unit cost for materials and conversion costs (labor and overhead)?arrow_forwardGeneral Accountingarrow_forwardKamala Khan has to decide between the following two options: Take out a student loan of $70,000 and study accounting full time for the next three years. The interest on the loan is 4% per year payable annually. The principle is to be paid in full after ten years. Study part time and work part time to earn $15,000 per year for the following six years. Once Kamala graduates, she estimates that she will earn $30,000 for the first three years and $40,000 the next four years. Kamala's banker says the market interest for a ten-year horizon is 6%. Required Calculate NPV of the ten-year cash flows of the two options. For simplification assume that all cash flows happen at year-end. Based on the NPV which of the two options is better for Kamala?arrow_forward
- Principles of Cost AccountingAccountingISBN:9781305087408Author:Edward J. Vanderbeck, Maria R. MitchellPublisher:Cengage Learning
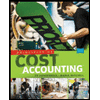