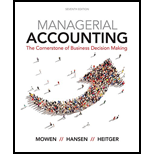
Managerial Accounting: The Cornerstone of Business Decision-Making
7th Edition
ISBN: 9781337115773
Author: Maryanne M. Mowen, Don R. Hansen, Dan L. Heitger
Publisher: Cengage Learning
expand_more
expand_more
format_list_bulleted
Question
Chapter 5, Problem 63C
1.
To determine
Analyze the flaws that are associated with the current method of assigning shipping and warehousing costs to sharp’s products.
2.
To determine
Calculate the shipping and warehousing cost per ton with the help of new method which is suggested by the JE and KA.
3.
To determine
Calculate the profit per ton of LLHC with the help of new costs. Also, compare the old profit with the new profit.
4.
To determine
Explain the role of the accounting system in supporting the given type of decision making.
5.
To determine
Discuss the reason for changes in the strategy of Mr. R.
Expert Solution & Answer

Want to see the full answer?
Check out a sample textbook solution
Students have asked these similar questions
General Accounting question
Hello tutor please provide answer accounting questions
Answer?? Financial accounting
Chapter 5 Solutions
Managerial Accounting: The Cornerstone of Business Decision-Making
Ch. 5 - Describe the two-stage process associated with...Ch. 5 - Describe the two-stage process for departmental...Ch. 5 - What are nonunit-level overhead activities?...Ch. 5 - What is product diversity?Ch. 5 - What is an overhead consumption ratio?Ch. 5 - What is activity-based product costing?Ch. 5 - Prob. 7DQCh. 5 - Explain how costs are assigned to activities.Ch. 5 - Describe the value of activity-based customer...Ch. 5 - Explain how ABC can help a firm identify its true...
Ch. 5 - Prob. 11DQCh. 5 - What are value-added activities? Value-added...Ch. 5 - What are nonvalue-added activities? Nonvalue-added...Ch. 5 - Identify and define four different ways to manage...Ch. 5 - Prob. 15DQCh. 5 - A batch-level driver is consumed by a product each...Ch. 5 - Which of the following is a nonunit-level driver?...Ch. 5 - Prob. 3MCQCh. 5 - Use the following information for Multiple-Choice...Ch. 5 - The first stage of ABC entails the assignment of...Ch. 5 - The second stage of ABC entails the assignment of...Ch. 5 - Interview questions are asked to determine a. what...Ch. 5 - Prob. 8MCQCh. 5 - Assume that the moving activity has an expected...Ch. 5 - Which of the following is a true statement about...Ch. 5 - Prob. 11MCQCh. 5 - This year, Lambert Company will ship 1,500,000...Ch. 5 - Prob. 13MCQCh. 5 - A forklift and its driver used for moving...Ch. 5 - Which of the following are nonvalue-added...Ch. 5 - Suppose that a company is spending 60,000 per year...Ch. 5 - Prob. 17MCQCh. 5 - Thom Company produces 60 units in 10 hours. The...Ch. 5 - Thom Company produces 60 units in 10 hours. The...Ch. 5 - Striving to produce the same activity output with...Ch. 5 - Use the following information for Brief Exercises...Ch. 5 - Use the following information for Brief Exercises...Ch. 5 - Calculating ABC Unit Costs Perkins National Bank...Ch. 5 - Assigning Costs to Activities McCourt Company...Ch. 5 - Activity-Based Customer Costing Sleepeze Company...Ch. 5 - Activity-Based Supplier Costing Clearsound uses...Ch. 5 - Prob. 27BEACh. 5 - Velocity and Cycle Time Kolby Company takes 36,000...Ch. 5 - Use the following information for Brief Exercises...Ch. 5 - Use the following information for Brief Exercises...Ch. 5 - Prob. 31BEBCh. 5 - Assigning Costs to Activities Craig Company...Ch. 5 - Activity-Based Customer Costing Limpio Company...Ch. 5 - Activity-Based Supplier Costing Blackburn Inc....Ch. 5 - Nonvalue-Added Costs Evans Inc. has the following...Ch. 5 - Velocity and Cycle Time Tara Company takes 8,000...Ch. 5 - Consumption Ratios; Activity Rates Saludable...Ch. 5 - Activity Rates Patten Company uses activity-based...Ch. 5 - Comparing ABC and Plantwide Overhead Cost...Ch. 5 - Activity-Based Product Costing Suppose that a...Ch. 5 - Assigning Costs to Activities, Resource Drivers...Ch. 5 - Activity-Based Customer-Driven Costs Suppose that...Ch. 5 - Activity-Based Supplier Costing Bowman Company...Ch. 5 - Use the following information for Exercises 5-44...Ch. 5 - Use the following information for Exercises 5-44...Ch. 5 - Use the following information for Exercises 5-44...Ch. 5 - Cycle Time and Velocity In the first quarter of...Ch. 5 - Product-Costing Accuracy, Consumption Ratios Plata...Ch. 5 - Product-Costing Accuracy, Consumption Ratios,...Ch. 5 - Formation of an Activity Dictionary A hospital is...Ch. 5 - Activity Rates and Activity-Based Product Costing...Ch. 5 - Value- and Nonvalue-Added Costs Waterfun...Ch. 5 - Functional-Based versus Activity-Based Costing For...Ch. 5 - Plantwide versus Departmental Rates,...Ch. 5 - Production-Based Costing versus Activity-Based...Ch. 5 - Prob. 56PCh. 5 - Customers as a Cost Object Morrisom National Bank...Ch. 5 - Grundvig Manufacturing produces several types of...Ch. 5 - Activity-Based Supplier Costing Levy Inc....Ch. 5 - Danna Martin, president of Mays Electronics, was...Ch. 5 - John Thomas, vice president of Mallett Company (a...Ch. 5 - Cycle Time, Velocity, Product Costing Goldman...Ch. 5 - Prob. 63CCh. 5 - Consider the following conversation between...
Knowledge Booster
Similar questions
arrow_back_ios
SEE MORE QUESTIONS
arrow_forward_ios
Recommended textbooks for you
- Managerial Accounting: The Cornerstone of Busines...AccountingISBN:9781337115773Author:Maryanne M. Mowen, Don R. Hansen, Dan L. HeitgerPublisher:Cengage LearningCornerstones of Cost Management (Cornerstones Ser...AccountingISBN:9781305970663Author:Don R. Hansen, Maryanne M. MowenPublisher:Cengage Learning
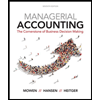
Managerial Accounting: The Cornerstone of Busines...
Accounting
ISBN:9781337115773
Author:Maryanne M. Mowen, Don R. Hansen, Dan L. Heitger
Publisher:Cengage Learning
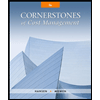
Cornerstones of Cost Management (Cornerstones Ser...
Accounting
ISBN:9781305970663
Author:Don R. Hansen, Maryanne M. Mowen
Publisher:Cengage Learning