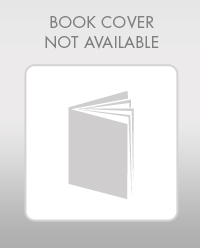
Concept explainers
Single plantwide rate and activity-based costing
Whirlpool Corporation conducted an activity-based costing study of its Evansville, Indiana, plant in order to identify its most profitable products. Assume that we select three representative refrigerators (out of 333): one low-, one medium-, and one high-volume refrigerator. Additionally, we assume the following activity-base information for each of the three refrigerators:
Prior to conducting the study, the factory
Complete the following table, using the single machine hour rate to determine the per-unit factory overhead for each refrigerator (Column A) and the three activity-based rates to determine the activity-based factory overhead per unit (Column B). Finally, compute the percent change in per-unit allocation from the single to activity-based rate methods (Column C). (Round per-unit overhead to two decimal places and percents to one decimal place.)
Why is the traditional overhead rate per machine hour greater under the single-rate method than under the activity-based method?
Interpret Column C in your table from part (A).
A.

Compute the single plant-wide overhead, ABC overhead for all the three products, and the percentage change in the allocation, and complete the Columns A, B, and C in the given table.
Explanation of Solution
Single plant-wide factory overhead rate: The rate at which the factory or manufacturing overheads are allocated to products is referred to as single plant-wide factory overhead rate.
Formula to compute single plant-wide overhead rate:
Activity-based costing (ABC) method: The costing method which allocates overheads to the products based on factory overhead rate for each activity or cost object, according to the cost pooled for the cost drivers (allocation base).
Formula to compute activity-based overhead rate:
Complete the blanks for Column A, B, and C.
Product Volume Class |
Column A (Single Rate Overhead Allocation Per Unit) (1) | Column B (ABC Overhead Allocation Per Unit) (2) | Column C (Percent Change in Allocation) (3) |
Low | $30.00 | $58.06 | |
Medium | 30.00 | 29.31 | |
High | 30.00 | 25.46 |
Table (1)
Working Note (1):
Compute factory overhead allocated per unit of each product, using single machine rate of $200 per machine hour (MH) (Column A).
Product Volume Class | Single Plant-Wide Overhead Rate | × | Total Number of MH | = | Total Factory Overhead | ÷ | Number of Units | = | Factory Overhead Per Unit |
Low | $200 | × | 24 MH | = | $4,800 | ÷ | 160 | = | $30.00 |
Medium | $200 | × | 225 MH | = | 45,000 | ÷ | 1,500 | = | $30.00 |
High | $200 | × | 900 MH | = | 180,000 | ÷ | 6,000 | = | $30 .00 |
Table (2)
Working Note (2):
Compute ABC factory overhead allocated per unit of each product (Column B).
Step 1: Compute activity cost allocated per unit of low volume refrigerators.
Activity | Activity-Based Overhead Rates | × | Actual Use of Activity-Base | = | Activity Cost |
Machining | $160 per MH | × | 24 MH | = | $3,840 |
Setup | $240 per setup | × | 14 setups | = | 3,360 |
Sales order processing | $55 per sales order | × | 38 orders | = | 2,090 |
Total activity costs allocated to low volume refrigerators | $9,290 | ||||
Number of units of low volume refrigerators | ÷160 units | ||||
Activity-based overhead cost per unit of low volume refrigerator | $58.06 |
Table (3)
Step 2: Compute activity cost allocated per unit of medium volume refrigerators.
Activity | Activity-Based Overhead Rates | × | Actual Use of Activity-Base | = | Activity Cost Allocated |
Machining | $160 per MH | × | 225 MH | = | $36,000 |
Setup | $240 per setup | × | 13 setups | = | 3,120 |
Sales order processing | $55 per sales order | × | 88 orders | = | 4,840 |
Total activity costs allocated to medium volume refrigerators | $43,960 | ||||
Number of units of medium volume refrigerators | ÷1,500 units | ||||
Activity-based overhead cost per unit of refrigerator | $29.31 |
Table (4)
Step 3: Compute activity cost allocated per unit of high volume refrigerators.
Activity | Activity-Based Overhead Rates | × | Actual Use of Activity-Base | = | Activity Cost Allocated |
Machining | $160 per MH | × | 900 MH | = | $144,000 |
Setup | $240 per setup | × | 9 setups | = | 2,160 |
Sales order processing | $55 per sales order | × | 120 orders | = | 6,600 |
Total activity costs allocated to high volume refrigerators | $152,760 | ||||
Number of units of high volume refrigerators | ÷6,000 units | ||||
Activity-based overhead cost per unit of refrigerator | $25.46 |
Table (5)
Working Note (3):
Compute the percent change in the allocation (Column C).
Product Volume Class | Column B (ABC Overhead Allocation Per Unit) | ˗ |
Column A (Single Rate Overhead Allocation Per Unit) | ÷ |
Column A (Single Rate Overhead Allocation Per Unit) | = | Percent Change in Allocation |
Low | $58.06 | ˗ | $30.00 | ÷ | $30.00 | = | 93.53% |
Medium | 29.31 | ˗ | 30.00 | ÷ | 30.00 | = | (2.3)% |
High | 25.46 | ˗ | 30.00 | ÷ | 30.00 | = | (15.1)% |
Table (6)
Note: refer to Tables (2), (3), (4), and (5) for value and computation of Column A and Column B values.
B.

Discuss the reasons for the difference in machine rate under single plant-wide approach and ABC approach.
Explanation of Solution
The machine hour rate under ABC, $160 per machine hour, as computed in Part (1), is different from the $200 single machine rate under single plant-wide approach. This is because the ABC method allocates all the overheads based on the activities under production. So, setup and sales order processing activities are allocated their share in factory overheads.
C.

Discuss the percent change in allocation (Column C).
Explanation of Solution
As per the ABC method, low volume refrigerator has high activity cost per unit comparatively. This is because this product consumes high overheads for the setup activity with highest cost. The company could reduce the cost of setup activity.
Want to see more full solutions like this?
Chapter 18 Solutions
Financial And Managerial Accounting
- Data for the two departments of Kimble & Pierce Company for June of the current fiscal year are as follows: Drawing Department Winding Department Work in process, June 1 Completed and transferred to next 7,400 units, 30% completed 2,900 units, 60% completed 101,400 units 100,400 units processing department during June Work in process, June 30 5,600 units, 75% completed 3,900 units, 30% completed Production begins in the Drawing Department and finishes in the Winding Department. If all direct materials are placed in process at the beginning of production, determine the direct materials and conversion equivalent units of production for June for the Winding Department.arrow_forwardGeneral Accountingarrow_forwardFinancial Accounting please answer the questionarrow_forward
- A business purchases equipment for $25,000, paying $6,000 in cash and signing a note payable for the remainder. What amount should be recorded as a liability?HELParrow_forwardMyrna and Geoffrey filed a joint tax return in 2017. Their AGI was $85,000, and itemized deductions were $13,700, which included $4,000 in state income tax. In 2018, they received a $1,800 refund of the state income taxes that they paid in 2017. The standard deduction for married filing jointly in 2017 was $12,700. Under the tax benefit rule, how much of the state income tax refund is included in gross income in 2018?(General Account)arrow_forwardAssume the company uses variable costing. Determine its product cost per unit.arrow_forward
- Annenbaum Corporation uses the weighted-average method in its process costing system. This month, the beginning inventory in the first processing department consisted of 2,400 units. The costs and percentage completion of these units in the beginning inventory were: Cost Percent Complete Materials costs $ 7,700 65% Conversion costs $ 8,800 45% A total of 10,500 units were started and 7,900 units were transferred to the second processing department during the month. The following costs were incurred in the first processing department during the month: Cost Materials costs $ 1,27,500 Conversion costs $2,09,000 The ending inventory was 50% complete with respect to materials and 35% complete with respect to conversion costs. What are the equivalent units for conversion costs for the month in the first processing department?arrow_forwardGive me answerarrow_forwardCool Sky reports the following costing data on its product for its first year of operations. During this first year, the company produced 42,000 units and sold 34,000 units at a price of $120 per unit Manufacturing costs Direct materials per unit Direct labor per unit Variable overhead per unit Fixed overhead for the year $ 48 $ 18 $ 6 $ 4,20,000 Selling and administrative costs Variable selling and administrative cost per unit Fixed selling and administrative cost per year $ 11 $ 1,05,000 Assume the company uses variable costing. Prepare its income statement for the year under variable costing.arrow_forward
- Managerial AccountingAccountingISBN:9781337912020Author:Carl Warren, Ph.d. Cma William B. TaylerPublisher:South-Western College PubFinancial And Managerial AccountingAccountingISBN:9781337902663Author:WARREN, Carl S.Publisher:Cengage Learning,Cornerstones of Cost Management (Cornerstones Ser...AccountingISBN:9781305970663Author:Don R. Hansen, Maryanne M. MowenPublisher:Cengage Learning
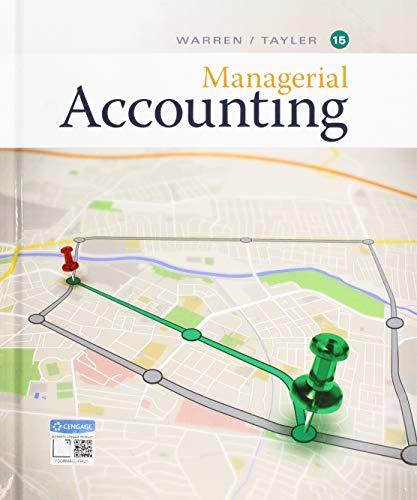
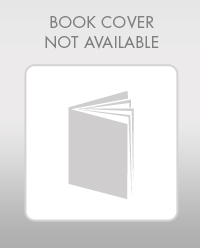
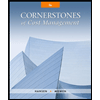