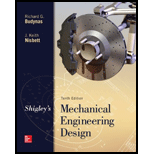
Concept explainers
The speed reducer of Prob. 14-24 is to be used for an application requiring 40 hp at 1145 rev/min. For the gear and the pinion, estimate the AGMA factors of safety for bending and wear, that is, (SF)P, (SF)G, (SH)P, and (SH)G. By examining the factors of safety, identify the threat to each gear and to the mesh.
14-24 A speed-reducer has 20° full-depth teeth, and the single-reduction spur-gear gearset has 22 and 60 teeth. The diametral pitch is 4 teeth/in and the face width is

The factor of safety for bending for pinion.
The factor of safety for bending for gear.
The factor of safety for wear for pinion.
The factor of safety for wear for gear.
Answer to Problem 25P
The factor of safety for bending for pinion is
The factor of safety for bending for gear is
The factor of safety for wear for pinion is
The factor of safety for wear for gear is
Explanation of Solution
Write the expression for diameter of pinion.
Here, the number of teeth on pinion is
Write the expression for diameter of the gear.
Here, the number of teeth on gear is
Write the expression for velocity of the pinion.
Here, the number of rotation made by pinion is
Write the expression for constant of transmission accuracy level number.
Here, the transmission accuracy level number is
Write the expression for constant
Write the expression for dynamic factor.
Write the expression for allowable bending stress number through hardened steels.
Here, the brinel hardness number is
Write the expression for stress cycle factor for bending.
Here, the number of cycles is
Write the expression for allowable stress.
Here, the reliability factor is
Write the expression for load correction factor for uncrowned teeth.
Write the expression for pinion proportion factor.
Here, the face width is
Write the expression for pinion proportion modifier for straddle mounted pinion.
Write the expression for mesh alignment factor.
Here, the empirical constant is
Write the expression for mesh alignment correction factor.
Write the expression for load distribution factor
Write the expression for overload factor for pinion.
Write the expression for overload factor for gear.
Write the expression for transmitted load in pinion.
Here, the spur gear geometry factor is
Write the expression for transmitted load for gear.
Write the expression for gear ratio.
Here, the number of teeth on gear is
Write the expression for pitting resistance stress cycle factor for pinion.
Write the expression for pitting resistance stress cycle factor for gear.
Write the expression for geometry factor.
Here, the pressure angle is
Write the expression for hardness ratio factor
Write the expression for contact fatigue strength for pinion.
Write the expression for contact fatigue strength for gear.
Write the expression for pinion contact endurance strength.
Write the expression for transmitted load.
Write the expression for gear contact strength.
Write the expression for transmitted load.
Her, the elastic coefficient is
Write the expression for transmitted load.
Write the expression for factor of safety based on load and stress for pinion bending.
Write the expression for factor of safety based on load and stress for gear bending.
Write the expression for factor of safety based on load.
Write the expression for based on stress.
Write the expression for factor of safety on load.
Write the expression for factor of safety based on stress.
Conclusion:
Substitute
Substitute
Substitute
Substitute
Substitute
Substitute
Substitute
Substitute
Substitute
Substitute
Refer to table 14-9, “Empirical constant
Substitute
Substitute
Refer Figure 14-6, “spur gear geometry factor”, to obtain the geometry factor for number of teeth
Since the thickness of gear is constant so
Rim thickness
Since the loading is uniform so
Refer table 14-2, “values of the lewis form factor
Substitute
Substitute
Substitute
Substitute
Substitute
Substitute
Substitute
Substitute
Substitute
Substitute
Substitute
Substitute
Substitute
Substitute
Substitute
Substitute
Thus, the factor of safety for bending for pinion is
Substitute
Thus, the factor of safety for bending for gear is
Substitute
Substitute
Thus, the factor of safety for wear for pinion is
Substitute
Substitute
Thus, the factor of safety for wear for gear is
The factor of safety for wear for pinion is
Want to see more full solutions like this?
Chapter 14 Solutions
Shigley's Mechanical Engineering Design (McGraw-Hill Series in Mechanical Engineering)
- A 50 mm transmission shaft transmitting 15 kW power at 200 rpm is supported on two deep grove ball bearings 750 mm apart and two gears are key to it. The pinion and gear have 30 and 100 teeth respectively. The pinion is located at 100 mm to the left of the right bearing, whereas the gear is located at 150 mm to the right of the left bearing The module and pressure angle of gear is 5 and 20o involute. Pinion delivers power horizontally to the right and gear received power in a vertical direction from below as shown in Figure l. The expected life of 15,00 h assumes the torque is the same for both pinion and gear and the bearings are under radial load only. Find the pitch diameters of pinion and gear. The torque transmits by the shaft Find force FC and FD Select suitable deep groove ball bearings at A and B B 150 500 100 Fe N-arrow_forwardQ1 Design a 4:1 spur-gear reduction for a 59 kW, three-phase squirrel-cage induction motor running at 1244 rev/min. The load is smooth, providing a reliability of 99.9 % at 109 revolutions of the pinion. Gearing space is meager. Use pinion materials to be Nitralloy 135M, grade 2 steel and nitrided through-hardened grade 1 steel material to keep the gear size small. The gears are heat-treated first then nitrided. Consider temperature factor is 1.1 for 250 0C.arrow_forwardA 57-tooth spur gear is in mesh with a 23-tooth pinion. The gearset transmits 125 hp at 1000 pinion rpm. Size the spur gears for a bending failure safety factor of at least 2 assuming a steady torque, 25∘ pressure angle, full-depth teeth, Qν = 9, an AISI 4140 steel pinion, and a class 40 cast iron gear. Part A Find the appropriate standard diametral pitch for the gearset. Part B Find the minimum required face width of the gears needed to satisfy the safety requirementsarrow_forward
- What is the dynamic factor, Kv?arrow_forwardProvide the complete step-by-step solution, given data, conversion of units, and sketch for this problem. A turbine at 30,000 rpm is used to drive a reduction gear delivering 3 hp at 3,000rpm. The gears are 20 degrees involute herringbone gears of 28 pitch and 2 1/8 ineffective width. The pinion has 20 teeth with a helix angle of 23 deg. Determine theload normal to the tooth surface. A. 20.4 lbs B. 24.4 lbs C. 28.4 lbs D. 32.4arrow_forwardA commercial enclosed spur gearset has 22 teeth on the pinion and 60 teeth on the gear. The pressure angle is 20° and the overload factor Ko =1. The diametral pitch is 8 teeth/in and the face width is 5 in. The pinion speed is 1000 rev/min and its cycle life is to be 10° revolutions at a reliability R =0.50. The quality number is 5 and the tooth are crowned. The material is a through-hardened steel, grade 2, with Brinell hardnesses of 250 core and case of both gears. For a conservative design and bending stress design factor of 2, rate the pinion (power) for these conditions using the AGMA method.arrow_forward
- 14-23 A spur gearset has 17 teeth on the pinion and 51 teeth on the gear. The pressure angle is 20° and the overload factor K, = 1. The diametral pitch is 6 teeth/in and the face width is 2 in. The pinion speed is 1120 rev/min and its cycle life is to be 10" revolu- tions at a reliability R = 0.99. The quality number is 5. The material is a through- hardened steel, grade 1, with Brinell hardnesses of 232 core and case of both gears. For a design factor of 2, rate the gearset for these conditions using the AGMA method.arrow_forwardWhat is the size factor, Ks, for the pinion? This should be an exact value.arrow_forwardA parallel shaft helical gear consists of a 20 dts drive pinion And a 96 driven gear. Both gears have a transverse diametrical pitch of 20 dts / in, a helix angle of 25 and a pressure angle on = 20 . The face width is 4 in., AND the gears are moving at 1600 ft / min, on the pitch line. The impeller is made of steel UNSG 10180 CD and without heat treatment; the driven one is made of grade 30 cast iron. Based on flexural strength calculations, evaluate the capacity or safe maximum power at hp. Consider general industrial service, and nG = 4.arrow_forward
- 14-4 A steel spur pinion has 15 teeth cut on the 20° full-depth system with a module of 5 mm and a face width of 60 mm. The pinion rotates at 200 rev/min and transmits 5 kW to the mating steel gear. What is the resulting bending stress?arrow_forwardThe gears of a gear wheel with a module of 4 mm, width of 60 mm and number of 18 teeth were broken during operation. If the gear wheel is made of cast iron (GG-25), with what torque is it loaded? Given: Speed factor Kv= 1.25; force distribution factor K m = 1; operating factor K 0 = 1.5; For GG-25 σem= 55 N / mm 2 , K f = 2.arrow_forwardAsaparrow_forward
- Elements Of ElectromagneticsMechanical EngineeringISBN:9780190698614Author:Sadiku, Matthew N. O.Publisher:Oxford University PressMechanics of Materials (10th Edition)Mechanical EngineeringISBN:9780134319650Author:Russell C. HibbelerPublisher:PEARSONThermodynamics: An Engineering ApproachMechanical EngineeringISBN:9781259822674Author:Yunus A. Cengel Dr., Michael A. BolesPublisher:McGraw-Hill Education
- Control Systems EngineeringMechanical EngineeringISBN:9781118170519Author:Norman S. NisePublisher:WILEYMechanics of Materials (MindTap Course List)Mechanical EngineeringISBN:9781337093347Author:Barry J. Goodno, James M. GerePublisher:Cengage LearningEngineering Mechanics: StaticsMechanical EngineeringISBN:9781118807330Author:James L. Meriam, L. G. Kraige, J. N. BoltonPublisher:WILEY
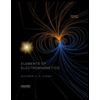
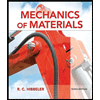
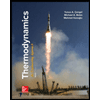
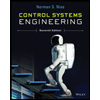
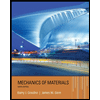
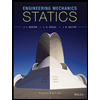