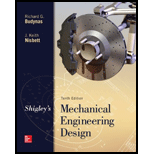
Concept explainers
The power rating for new gear-set.

Answer to Problem 29P
The power rating for new gear-set is
Explanation of Solution
Write the expression for diameter of pinion.
Here, the number of teeth on pinion is
Write the expression for diameter of the gear.
Here, the number of teeth on gear is
Write the expression for velocity of the pinion.
Here, the number of rotation made by pinion is
Write the expression for constant of transmission accuracy level number.
Here, the transmission accuracy level number is
Write the expression for constant
Write the expression for dynamic factor.
Write the expression for allowable bending stress number through hardened steels.
Here, the brinel hardness number is
Write the expression for gear ratio.
Here, the number of teeth on gear is
Write the expression for stress cycle factor for bending for pinion.
Here, the number of cycles is
Write the expression for stress cycle factor for bending for gear.
Write the expression for allowable stress for pinion.
Here, the reliability factor is
Write the expression for allowable stress for gear.
Write the expression for load correction factor for uncrowned teeth.
Write the expression for pinion proportion factor.
Here, the face width is
Write the expression for pinion proportion modifier for straddle mounted pinion.
Write the expression for mesh alignment factor.
Here, the empirical constant is
Write the expression for mesh alignment correction factor.
Write the expression for load distribution factor
Write the expression for overload factor for pinion.
Here, the Lewis form factor for pinion is
Write the expression for overload factor for gear.
Here, the lewis form factor for gear is
Write the expression for transmitted load in pinion.
Here, the spur gear geometry factor for pinion is
Write the expression for power for pinion.
Write the expression for transmitted load for gear.
Here the spur gear geometry factor for gear is
Write the expression for power for gear.
Write the expression for pitting resistance stress cycle factor for pinion.
Write the expression for pitting resistance stress cycle factor for gear.
Write the expression for geometry factor.
Here, the pressure angle is
Write the expression for hardness ratio factor
Write the expression for contact fatigue strength for pinion.
Write the expression for contact fatigue strength for gear.
Write the expression for pinion contact endurance strength.
Write the expression for transmitted load.
Here, the elastic coefficient is
Write the expression for power of pinion.
Write the expression for gear contact strength.
Write the expression for transmitted load.
Write the expression for power of gear.
Write the expression for rated power.
Conclusion:
Substitute
Substitute
Substitute
Substitute
Substitute
Substitute
Substitute
Substitute
Substitute
Substitute
Substitute
Substitute
Substitute
Refer to table 14-9, “Empirical constant
Substitute
Substitute
Refer Figure 14-6, “spur gear geometry factor”, to obtain the geometry factor for number of teeth
Since the thickness of gear is constant so
Rim thickness
Since the loading is uniform so
Refer table 14-2, “values of the lewis form factor
Substitute
Substitute
Substitute
Substitute
Substitute
Substitute
Substitute
Substitute
Substitute
Substitute
Substitute
Substitute
Substitute
Substitute
Substitute
Substitute
Substitute
Substitute
Thus, the rating of speed reducer for power is
Want to see more full solutions like this?
Chapter 14 Solutions
Shigley's Mechanical Engineering Design (McGraw-Hill Series in Mechanical Engineering)
- Compute the values for all the geometrical features for a pair of straight bevel gears having a diametral pitch of 8, a 20° pressure angle, 16 teeth in the pinion, and 48 teeth in the gear. Specify a suitable face width. The shafts are at 90°. tad wo m that ratates at1750 comarrow_forwardWhat is the surface strength geometry factor, I? This should be an exact value.arrow_forwardi need correct explanation my best wishes tonarrow_forward
- For full depth of involute spur gears. minimum number of teeth of pinion to avoid interference depends upon (a) pressure angles B.Speed ratio C.circular pitch D pitch diameterarrow_forwardA pair of Straight teeth spur geard, having 2ó involutek full depth teerh is to halee tyanj mitted Power 12 KW at 30e rpm of the Pinich. The speed ratío is 3. The allowable s tati'c StYesse) for gear of cast brom and Pinion of steel are 6o Mpa and lo5 Mpa, respectilely. Assume the number of teeth Pinion as 16 and face width as 14 times of tha module. A SSume Steedy load Conditng and 8-10 hours of service per day. Given: be=84 Mpa, Ges=6o0 MPa, C=80,E, = 200000 HPa , Ea ノ HPa 4.5 4.5+earrow_forwardQ8:- An epicyclic gear speed reduction is shown in the Fig. below. The driving shaft carries on the arm A a pin on which the compound wheels B and C are free to revolve. Wheel C meshes with the fixed wheel E and wheel B meshes with the wheel D which is keyed to the driven shaft. The number of teeth on the wheels are:- Zg=27, Z,=30, Zp=24 and ZĘ=21. Find the ratio of the speed of the driving shaft to the speed of the driven shaft. A Input output Earrow_forward
- A pair of gears with 14.5° full-depth teeth are to transmit 5 hp at 1800 rpm of the pinion; mw= 2.5; Np = 20 teeth; carefully cut teeth; intermittent service; Kf= 1.45. A. Determine the diametral pitch, B. face width, C. and tooth numbers if the pinionis to be made of phosphor gear bronze (SAE 65, Table AT 3arrow_forward14-23 A spur gearset has 17 teeth on the pinion and 51 teeth on the gear. The pressure angle is 20° and the overload factor K, = 1. The diametral pitch is 6 teeth/in and the face width is 2 in. The pinion speed is 1120 rev/min and its cycle life is to be 10" revolu- tions at a reliability R = 0.99. The quality number is 5. The material is a through- hardened steel, grade 1, with Brinell hardnesses of 232 core and case of both gears. For a design factor of 2, rate the gearset for these conditions using the AGMA method.arrow_forwardThe figure shows a double-reduction helical gearset. Pinion 2 is the driver, and it receives a torque of 1200 Ibf • in from its shaft in the direction shown. Pinion 2 has a normal diametral pitch of 8 teeth/in, 14 teeth, and a normal pressure angle of 20° and is cut right-handed with a helix angle of 30°. The mating gear 3 on shaft b has 36 teeth. Gear 4, which is the driver for the second pair of gears in the train, has a normal diametral pitch of 3 teeth/in, 15 teeth, and a normal pressure angle of 20° and is cut left-handed with a helix angle of 15°. Mating gear S has 45 teeth. Find the magnitude and direction of the force exerted by the bearings C and D on shaft b if bearing C can take only a radial load while bearing D is mounted to take both radial and thrust loads.arrow_forward
- Elements Of ElectromagneticsMechanical EngineeringISBN:9780190698614Author:Sadiku, Matthew N. O.Publisher:Oxford University PressMechanics of Materials (10th Edition)Mechanical EngineeringISBN:9780134319650Author:Russell C. HibbelerPublisher:PEARSONThermodynamics: An Engineering ApproachMechanical EngineeringISBN:9781259822674Author:Yunus A. Cengel Dr., Michael A. BolesPublisher:McGraw-Hill Education
- Control Systems EngineeringMechanical EngineeringISBN:9781118170519Author:Norman S. NisePublisher:WILEYMechanics of Materials (MindTap Course List)Mechanical EngineeringISBN:9781337093347Author:Barry J. Goodno, James M. GerePublisher:Cengage LearningEngineering Mechanics: StaticsMechanical EngineeringISBN:9781118807330Author:James L. Meriam, L. G. Kraige, J. N. BoltonPublisher:WILEY
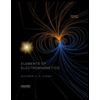
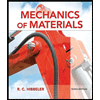
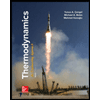
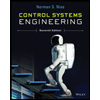
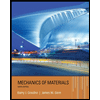
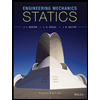