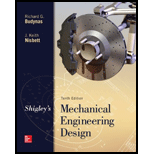
Concept explainers
The countershaft in Prob. 3–73, p. 152, is part of a speed reducing compound gear train using 20° spur gears. A gear on the input shaft drives gear A with a 2 to 1 speed reduction. Gear B drives a gear on the output shaft with a 5 to 1 speed reduction. The input shaft runs at 1800 rev/min. All gears are to be of the same material. Since gear B is the smallest gear, transmitting the largest load, it will likely be critical, so a preliminary analysis is to be performed on it. Use a module of 18.75 mm/tooth, a face-width of 4 times the circular pitch, a Grade 2 steel through-hardened to a Brinell hardness of 300, and a desired life of 12 kh with a 98 percent reliability. Determine factors of safety for bending and wear.

Want to see the full answer?
Check out a sample textbook solution
Chapter 14 Solutions
Shigley's Mechanical Engineering Design (McGraw-Hill Series in Mechanical Engineering)
- A gear train is composed of four helical gears with the three shaft axes in a single plane, as shown in the figure. The gears have a normal pressure angle of 20 and a 30 helix angle. Gear is the driver, and is rotating counterclockwise as viewed from the top. Shaft b is an idler and the transmitted load from gear 2 to gear 3 is 500 Ibf. The gears on shaft b both have a normal diametral pitch of 7 teeth/in and have 54 and 14 teeth, respectively. Find the forces exerted by gears 3 and 4 on shaft barrow_forwardNonearrow_forwardThe figure shows a pair of shaft-mounted spur gears having a diametral pitch of 5 teeth/in with an 18-tooth 20° pinion driving a 45-tooth gear. The power input is 28-hp at 1700 rev/min. Find the magnitude of the force acting on bearing D. 3 2 3 in 3 in The magnitude of the force acting on bearing Dis lbf.arrow_forward
- Need Solution through 15minarrow_forwardThe four gears shown are attached to a steel shaft that is rotating at 2 Hz. Gear B supplies 70 kW of power to the shaft. Of that power, 20kW are used by gear A, 20 kW by gear C and 30kW by gear D. G=83 GPa for steel -20KW JOKN -20kw -30kW 2m 1.5m 1.5m B (a) If a uniform shaft diameter of 125 mm B speci fied, detenmine the angle of rotation of A relative to D. O f segment Co is to be replaced lay a hollaw Shaft with an inside diameter of 80 mm, what is the outside diameter if the stress is not to excced 70 MPa.arrow_forwardA gear train is composed of four helical gears with the tree shaft axes in a single plane, as shown in the figure. The gears have a normal pressure angle of 20° and a 30°helix angle. Gear 2 is the driver, and is rotating counterclockwise as viewed from the top. Shaft b is and idler and the transmitted load from gear 2 to gear 3 is 500 lbf. The gears on shaft b both have a normal diametral pitch of 7 teeth/in and have 54 and 14 teeth, respectively. Find the forces exerted by gears 3 and 4 on shaft b.arrow_forward
- In a broaching machine shown, shaft A carries a pulley 60.96 cm in diameter which is driven by a leather flat belt from 12-inch pulley on the 30 Hp-squirrel-cage, compensator-motor shaft overhead, the latter turning 1200 rpm. Gears 2 & 4 have 12 teeth each, and 3 & 5 have 60 teeth each. Gear 5 is fast to 6, which has 10 teeth and a module of 8.465 mm/tooth and which engages with rack 7 to which is attached the broach. Assuming that there is no slipping between the pulleys and the belt. Determine: a) the speed with which the broach is drawn through the work, in m/s. b) Specify a double ply, medium weight, cemented joint leather flat belt, considering a mildly jerking loads and a center distance of 60 inches. c) Determine the belt tensions of the belt and the F, maximum stress in the straight part of F₁ ALBA belt if = 3 F₂ Gear 5 Gear 6 Gear 2 DEO CEC A HH₂ Rack 030-0=0 Gear 4 Gear 3arrow_forward1) A pair of cast iron bevel gears connect two shafts at right angles. The pitch diameters of the pinion and gear are 80 mm and 100 mm respectively. The tooth profiles of the gears are of 14 1/2° composite form. The allowable static stress for both the gears is 55 MPa. If the pinion transmits 2.75 kW at 1100 r.p.m., find the module and number of teeth on each gear from the standpoint of strength and check the design from the standpoint of wear. Take surface endurance limit as 630 MPa and modulus of elasticity for cast iron as 84 kN/mm². A0a& ENG 1222/20 nere to searcharrow_forwardThe upper half of a compound Epicyclic gearset is shown in Figure, with input shaft I rotating at a constant speed of 700 rpm in a clockwise direction and generating 12 kW input power. The Annulus wheel A2 is coupled to an auxiliary gear N on shaft X and forms a compound wheel with gear O. The Annulus A1 rotates in a counter-clockwise direction at a speed of 5,300 rpm. Calculate the following using this condition: Number of gear teeth:P1 = 30 , A1 = 120P2 = 50 , A2 = 140N = 60 , O = 120 a) The output shaft O (NO), shaft X (NX), and gear ratio speed and direction (n). b) Calculate the speed and direction of output shaft O (NO), shaft X (NX), and gear ratio if Annulus wheel A1 is locked (n). c) The braking torque (Tb) that must be applied to Annulus wheel A1 to keep it stationary (magnitude and direction), assuming gear transmission efficiency of 90%.arrow_forward
- Three 14.5° pressure angle spur gears with a diametral pitch of 8 are meshed. The input pinion on the left is running clockwise at 3101 rpm and transmits 3.2 Hp. Gear 1 (Pinion) Input N1 = 20 teeth Gear 2 Idler Gear 3 Output N3 = 25 teeth N2 = 75 teeth Answer the following: 1. Pinion (Gear 1) pitch diameter (1 mark) 2. Gear 2 pitch diameter (1 mark) 3. Gear 3 pitch diameter (1 mark) 4. Circular pitch (1 mark) 5. Addenda (1 mark) 6. Center distance from gear 1 to gear 3 (2 marks) 7. Line of action length for gear 1 contacting gear 2 (2 marks) 8. Contact ratio of gear 1 and 2 (2 marks) 9. Gear ratio from gear 1 to gear 3 (1 mark) 10. Draw a free-body diagram of Gear 2, showing the radial and tangential forces. Calculate these forces. What is the reaction force in the bearing? (3 marks)arrow_forwardThe four helical gears shown in figure have a module in the normal plane of 4 mm and a pressure angle in the normal plane of 0.35 rad. The motor shaft rotates 550 rpm and transmits 20 kW. Other data are on the drawing. (a) What is the speed ratio between the motor (input) and output shafts? (b) Determine all force components that the 20-tooth pinion applies to the 50-tooth gear. Make a sketch showing these forces applied to the gear. (c) The same as part (b), except for the force components that the 50-tooth gear exerts on the 25- tooth pinion 100 50 teeth 200 125 25 teeth ψ = 0.35 rad right hand Motor 20 teeth ψ = 0.50 rad left hand 50 teeth Outputarrow_forwardPLEASE ANSWER NUMBER 3 MECH 222: PLEASE GIVE DETAILED SOLUTIONS AND CORRECT ANSWERS. I WILL REPORT TO BARTLEBY THOSE TUTORS WHO WILL GIVE INCORRECT ANSWERS.arrow_forward
- Elements Of ElectromagneticsMechanical EngineeringISBN:9780190698614Author:Sadiku, Matthew N. O.Publisher:Oxford University PressMechanics of Materials (10th Edition)Mechanical EngineeringISBN:9780134319650Author:Russell C. HibbelerPublisher:PEARSONThermodynamics: An Engineering ApproachMechanical EngineeringISBN:9781259822674Author:Yunus A. Cengel Dr., Michael A. BolesPublisher:McGraw-Hill Education
- Control Systems EngineeringMechanical EngineeringISBN:9781118170519Author:Norman S. NisePublisher:WILEYMechanics of Materials (MindTap Course List)Mechanical EngineeringISBN:9781337093347Author:Barry J. Goodno, James M. GerePublisher:Cengage LearningEngineering Mechanics: StaticsMechanical EngineeringISBN:9781118807330Author:James L. Meriam, L. G. Kraige, J. N. BoltonPublisher:WILEY
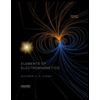
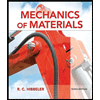
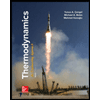
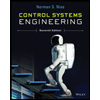
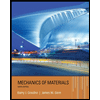
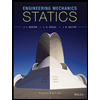