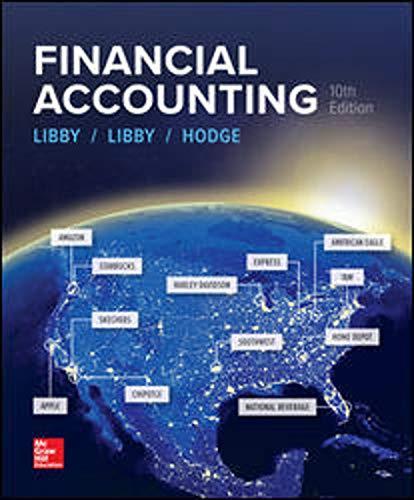
Concept explainers
A firm has recently added a new product to their offerings. Manufacturing reports that production is going smoothly and factory workers are becoming familiar with the manufacture of this product. All expectations are that the current rate of learning will continue and the manufacture of future units will be more efficient (i.e., take less time). The following shown table shows the results for the first two units produced. The firm has an order for two additional units. Assuming the pattern of learning curve continues (same rate): Solve, a. At what rate is learning occurring? b. How long will it take to produce the fourth unit? c. If the labor rate is $15 per hour, what is the cumulative average labor cost per unit for the first four units produced?
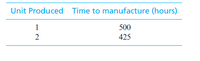

Trending nowThis is a popular solution!
Step by stepSolved in 3 steps with 4 images

- You have just been hired by FAB Corporation, the manufacturer of a revolutionary new garage door opening device. The president has asked that you review the company’s costing system and “do what you can to help us get better control of our manufacturing overhead costs.” You find that the company has never used a flexible budget, and you suggest that preparing such a budget would be an excellent first step in overhead planning and control. After much effort and analysis, you determined the following cost formulas and gathered the following actual cost data for March: Cost Formula Actual Cost in March Utilities $16,200 + $0.20 per machine-hour $ 21,600 Maintenance $38,100 + $1.70 per machine-hour $ 62,500 Supplies $0.80 per machine-hour $ 14,200 Indirect labor $94,100 + $1.60 per machine-hour $ 123,800 Depreciation $67,900 $ 69,600 During March, the company worked 16,000 machine-hours and produced 10,000 units. The company had originally planned to work 18,000 machine-hours during March.…arrow_forwardCurrent Designs faces a number of important decisions that require incremental analysis. Current Designs is always working to identify ways to increase efficiency while becoming more environmentally conscious. During a recent brainstorming session, one employee suggested to Diane Buswell, controller, that the company should consider replacing the current rotomold oven as a way to realize savings from reduced energy consumption. The oven operates on natural gas, using 17,000 therms of natural gas for an entire year. A new, energy-efficient rotomold oven would operate on 15,000 therms of natural gas for an entire year. After seeking out price quotes from a few suppliers, Diane determined that it would cost approximately $250,000 to purchase a new, energy-efficient rotomold oven. She determines that the expected useful life of the new oven would be 10 years, and it would have no salvage value at the end of its useful life. Current Designs would be able to sell the current oven today for…arrow_forwardThe management of International Cookwares believes that delivery performance measures must be improved if the company is to maintain its competitive edge. The following data are considered to be typical of the time to complete orders. • Process time: 4 days • Wait time to the start of production: 15 days • Move time: 3 days ● Inspection time: 2 days • Queue time during the production process: 8 days What is the delivery cycle time?arrow_forward
- Transmissions are delivered to the fabrication line four at a time. It takes one hour for transmissions to be delivered. Approximately five vehicles are produced each hour, and management has decided that 40 percent of expected demand should be maintained as safety stock. How many Kanban card sets are needed? (Round up your answer to the next whole number.) The Deming Cycle is: A. a checklist that enables managers to evaluate employee performance more systematically. B. a systematic method of evaluating potential facility locations. C. a process for finding potential quality errors before they occur. D. a process for using identical production steps in the creation of different types of products.arrow_forwardNorthern Defense manufactures radar systems. It has just completed the manufacture of its first newly designed system, RS-32. Manufacturing data for the RS-32 follow: (Click icon to view data) Requirement Calculate the total variable costs of producing 2, 4, and 8 units. Begin by calculating the cumulative total time in labor-hours using the cumulative average-time learning model. (Round the cumulative average time per unit to the nearest whole number.) Cumulative number of Cumulative average time Cumulative total time: per unit: Labor-hours Labor-hours 3700 units 2 4 8 3700 ← Data table Direct material cost Direct manufacturing labor time for first unit Learning curve for manufacturing labor time per radar system Direct manufacturing labor cost Variable manufacturing overhead cost Using the formula for an 85% learning curve, b = In 0.85 In 2 Print = $ $ $ -0.162519 0.693147 81,000 per unit of RS-32 3,700 direct manufacturing labor-hours 85% cumulative average timeª Done 28 per direct…arrow_forwardDengerarrow_forward
- Colby Company makes cases for cell phones of all sizes and types for sale through specialty retailers. The company makes a standard model for the most recent iPhone as well as a deluxe model. Management has designed an ABC system with the following activity cost pools and activity rates for these models: Activity Cost Pool Supporting manufacturing Order processing Customer service Management would like an analysis of the profitability of a particular customer, Cell City, which has ordered the following products over the last 12 months: Number of cases Number of orders Direct labour-hours per case Selling price per case Direct materials cost per case. Sales Costs: Activity Rates $2 per direct labour-hour $19 per order $60 per customer Direct materials Direct labour Supporting manufacturing Order processing Customer service The company's direct labour rate is $20 per hour. Required: Using the company's ABC system, compute the customer margin of Cell City. Customer margin Standard Model…arrow_forwardWhat impact does an increase in expenses have on net income?arrow_forwardYou have just been hired by FAB Corporation, the manufacturer of a revolutionary new garage door opening device. The president has asked that you review the company's costing system and "do what you can to help us get better control of our manufacturing overhead costs." You find that the company has never used a flexible budget, and you suggest that preparing such a budget would be an excellent first step in overhead planning and control. After much effort and analysis, you determined the following cost formulas and gathered the following actual cost data for March: Utilities Maintenance Supplies Indirect labor. Depreciation Cost Formula $16,900 $0.14 per machine-hour $38, 300+ $1.30 per machine-hour $0.70 per machine-hour $94,700+ $1.50 per machine-hour $68, 100 Actual Cost in March $ 21,360 $ 56,800 $ 13, 100 $ 124, 100 $ 69,808 During March, the company worked 17,000 machine-hours and produced 11,000 units. The company had originally planned to work 19,000 machine-hours during…arrow_forward
- DataSpan, Incorporated, automated its plant at the start of the current year and installed a flexible manufacturing system. The company is also evaluating its suppliers and moving toward Lean Production. Many adjustment problems have been encountered, including problems relating to performance measurement. After much study, the company has decided to use the performance measures below, and it has gathered data relating to these measures for the first four months of operations. Throughput time (days) Delivery cycle time (days) Manufacturing cycle efficiency (MCE) Percentage of on-time deliveries Total sales (units) 1 2 Month ? ? ? ? ? ? 91% 86% 3,460 3,312 Move time per unit Process time per unit Wait time per order before start of production Queue time per unit Inspection time per unit 3 ? ? ? 82% 3,143 4 Management has asked for your help in computing throughput time, delivery cycle time, and MCE. The following average times have been logged over the last four months: ? ? ? 78% 3,025…arrow_forwardManagement of Mittel Company would like to reduce the amount of time between when a customer places an order and when the order is shipped. For the first quarter of operations during the current year the following data were reported: Inspection time Wait time (from order to start of production) Process time Move time Queue time Required: 1. Compute the throughput time. (Round your answer to 1 decimal place.) 2. Compute the manufacturing cycle efficiency (MCE) for the quarter. (Round your percentage answer to nearest whole percent.) 3. What percentage of the throughput time was spent in non-value-added activities? (Round your percentage answer to nearest whole percent.) 4. Compute the delivery cycle time. (Round your intermediate calculations and final answer to 1 decimal place.) 5. If by using Lean Production all queue time during production is eliminated, what will be the new MCE? (Do not round intermediate calculations. Round your percentage answer to 1 decimal place.) 1. Throughput…arrow_forwardOverview In the article for this assignment, Plaskett shows that ERP systems are helpful for companies to establish needed agility. ERP systems are also discussed in length in Chapter 6 of your textbook. Accurate, up-to-date information on business products can help reduce production times and make businesses more effective. Read this article before you begin the assignment: ERP System Enables Gearmaker to Achieve Needed Agility. Instructions Using the same framework used by Plaskett, answer the following in 3 pages of paper Summarize the factors that made the ERP system successful in Gearmaker. Apply the same ERP analysis process to a company of your choice and describe the potential impact on its operations. Use at least three quality resources in this assignment. Note: Wikipedia and similar websites do not qualify as quality resources. This course requires the use of Strayer Writing Standards (SWS). The library is your home for SWS assistance, including citations and…arrow_forward
- AccountingAccountingISBN:9781337272094Author:WARREN, Carl S., Reeve, James M., Duchac, Jonathan E.Publisher:Cengage Learning,Accounting Information SystemsAccountingISBN:9781337619202Author:Hall, James A.Publisher:Cengage Learning,
- Horngren's Cost Accounting: A Managerial Emphasis...AccountingISBN:9780134475585Author:Srikant M. Datar, Madhav V. RajanPublisher:PEARSONIntermediate AccountingAccountingISBN:9781259722660Author:J. David Spiceland, Mark W. Nelson, Wayne M ThomasPublisher:McGraw-Hill EducationFinancial and Managerial AccountingAccountingISBN:9781259726705Author:John J Wild, Ken W. Shaw, Barbara Chiappetta Fundamental Accounting PrinciplesPublisher:McGraw-Hill Education
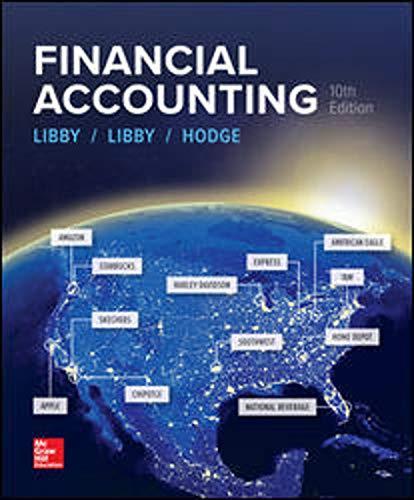
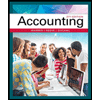
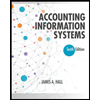
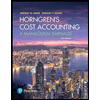
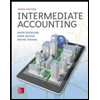
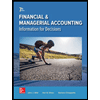