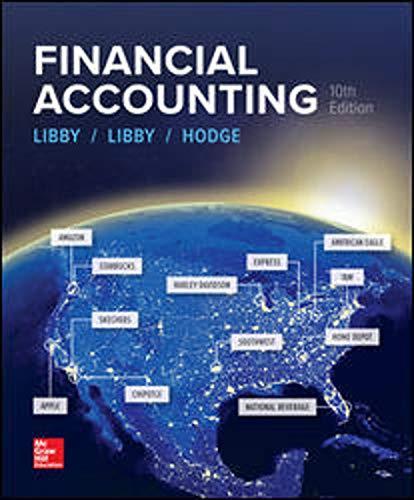
FINANCIAL ACCOUNTING
10th Edition
ISBN: 9781259964947
Author: Libby
Publisher: MCG
expand_more
expand_more
format_list_bulleted
Question
thumb_up100%
If a 70% learning curve is used, using the cumulative average time model, the cumulative direct labor hours required to produce a total eight units would be:
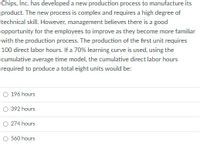
Transcribed Image Text:Chips, Inc. has developed a new production process to manufacture its
product. The new process is complex and requires a high degree of
technical skill. However, management believes there is a good
opportunity for the employees to improve as they become more familiar
with the production process. The production of the first unit requires
100 direct labor hours. If a 70% learning curve is used, using the
cumulative average time model, the cumulative direct labor hours
required to produce a total eight units would be:
O 196 hours
O 392 hours
O 274 hours
O 560 hours
Expert Solution

This question has been solved!
Explore an expertly crafted, step-by-step solution for a thorough understanding of key concepts.
This is a popular solution
Trending nowThis is a popular solution!
Step by stepSolved in 2 steps

Knowledge Booster
Learn more about
Need a deep-dive on the concept behind this application? Look no further. Learn more about this topic, accounting and related others by exploring similar questions and additional content below.Similar questions
- The management of Hartman Company is trying to determine the amount of each of two products to produce over the coming planning period. The following information concerns labor availability, labor utilization, and product profitability: Labor-Hours Required(hours/unit) Department Product 1 Product 2 Hours Available A 1.00 0.35 95 B 0.30 0.20 36 C 0.20 0.50 50 Profit contribution/unit $30.00 $15.00 (a) Develop a linear programming model of the Hartman Company problem. Solve the model to determine the optimal production quantities of products 1 and 2. If required, round your answer to two decimal places. Product 1 Product 2 Production (b) In computing the profit contribution per unit, management does not deduct labor costs because they are considered fixed for the upcoming planning period. However, suppose that overtime can be scheduled in some of the departments. Which departments would you recommend scheduling for…arrow_forwardQuan If an 80% learning curve is applicable, Grosse Point's total cost on this order would be estimated at P26,400. P32,000. c.. P38,000. a. d. P41,800. (CMA, Adapted) b. A particular manufacturing job is subject to an estimated 90% learning 59. curve. The first unit required 50 labor hours to complete. What is the cumulative average time per unit after four units are completed? 50.0 hours 45.0 hours 40.5 hours с. 40.0 hours d. a. b. 60. Grosse Point Manufacturing recently completed and sold an order of 50 units that had costs as follows: Direct materials Direct labor (1,000 hours x P8.50) Variable overhead (1,000 hours x P4.00)* Fixed overhead P 1,500 8,500 4,000 1,400 P15,400 Applied on the basis of direct labor hours Applied at the rate of 10% of variable cost If Grosse Point had experienced a 70% learning curve, the bid for the 150 units would show a 30% reduction in the total direct labor hours required with no learning curve. a. b. include increased fixed overhead costs. be 10%…arrow_forwardABC Company is producing and selling Product X. Company management anticipates that a 70% learning curve will apply to the production of a new item. The cost of first item is $1,500 in materials. First item will take 500 labor hours. The cost per labor hour is $4 per hour. Variable overheads are 130% of labor costs. ABC Company has a profit mark-up for its products in amount of 20%. What is the cost of the third unit of Product X? O $3.238 $3,420 O $2.620 O $2.788arrow_forward
- Post a listing of recommendations - with full explanations - regarding areas of possible cost savings for the company. Include recommendations for at least four of the six activities, and your targeted savings is at least $1 million (~ 25%). Be specific and explain how the cost savings will be achieved. Activities that can be reduced listed on the picture.arrow_forwardPlease solve a and barrow_forwardConsider a process with a unit cost of $40 for the first unit; that is, c(1) = 40, anda learning rate of LR = 0.9. What will be the unit costs for the 16th unit?arrow_forward
- Lazer Tag manufactures computer parts within a relevant range of 50,000 to 100,000 units per year. Complete the following manufacturing cost schedule (a through j) for Lazer Tag. Fill in the following chart. Parts Produced 50,000 100,000 TOTAL COSTS: Variable $75,000 ? Fixed 50,000 ? Total ? ? COSTS PER UNIT: Variable ? ? Fixed ? ? Total ? ?arrow_forward13. A manager is interested in improving productivity at a plant by changing the layout of the workstation. For each of 10 workers, she measures the time it takes to complete a task before the change and after the change. She calculates the following summary statistics for the sample difference: mean sample difference (between before and after) = 8.5 and sample standard deviation of the difference = 11.38. Assuming that the difference in time taken to complete the task is normally distributed, what is the critical value used to determine whether the mean difference (in task completion time) between before and after the change is not equal to zero at the 5% level of significance? Use our textbook statistical table to answer the question. a. ±2.2281 b. ±2.1009 c. ±2.2622 d. ±1.96arrow_forwardThe following data are available: Actual OH is 300,000; Overapplied OH is 25,000; Budgeted machine hours is 27,500; Budgeted Variable Overhead is 100,000; Actual Machine hours is 25,000. If normal costing was used, what is the total budgeted OH used?arrow_forward
- An analysis of a particular mixed cost indicates it will be an average of $0.65 per hour at an activity level of 18,000 hours and $11,700 in total at an activity level of 20,000 hours. Assuming that this activity is within the relevant range, what is the cost expected to total at an activity level of 16,000 hoursarrow_forwardThe president has read in industry journals that throughput time, MCE, and delivery cycle time are important measures of performance, but no one is sure how they are computed. You have been asked to assist the company, and you have gathered the following data relating to these measures: Average per Month (in days) 1 2 3 4 Wait time per order before start of production Inspection time per unit Process time per unit Queue time per unit Move time per unit 9.0 11.5 12.0 14.0 0.8 0.7 0.7 0.7 2.1 2.0 1.9 1.8 2.8 4.4 6.0 7.0 0.3 0.4 0.4 0.5 Required: 1-a. Compute the throughput time for each month. 1-b. Compute the manufacturing cycle efficiency (MCE) for each month. 1-c. Compute the delivery cycle time for each month. 3-a. Refer to the inspection time, process time, and so forth, given for month 4. Assume that in month 5 the inspection time, process time, and so forth, are the same as for month 4, except that the company is able to completely eliminate the queue time during production using…arrow_forwardBased on the outcome of the calculations(image attached), draw the five (5) S-Curves for the individual.arrow_forward
arrow_back_ios
SEE MORE QUESTIONS
arrow_forward_ios
Recommended textbooks for you
- AccountingAccountingISBN:9781337272094Author:WARREN, Carl S., Reeve, James M., Duchac, Jonathan E.Publisher:Cengage Learning,Accounting Information SystemsAccountingISBN:9781337619202Author:Hall, James A.Publisher:Cengage Learning,
- Horngren's Cost Accounting: A Managerial Emphasis...AccountingISBN:9780134475585Author:Srikant M. Datar, Madhav V. RajanPublisher:PEARSONIntermediate AccountingAccountingISBN:9781259722660Author:J. David Spiceland, Mark W. Nelson, Wayne M ThomasPublisher:McGraw-Hill EducationFinancial and Managerial AccountingAccountingISBN:9781259726705Author:John J Wild, Ken W. Shaw, Barbara Chiappetta Fundamental Accounting PrinciplesPublisher:McGraw-Hill Education
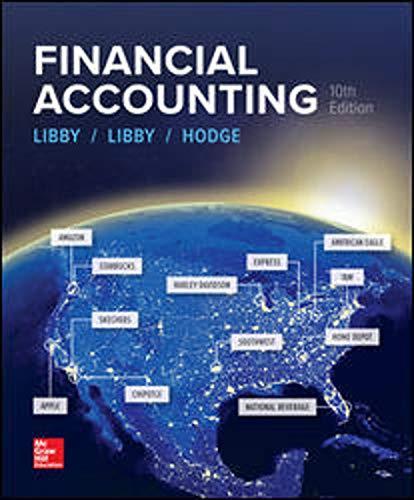
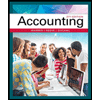
Accounting
Accounting
ISBN:9781337272094
Author:WARREN, Carl S., Reeve, James M., Duchac, Jonathan E.
Publisher:Cengage Learning,
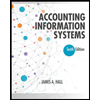
Accounting Information Systems
Accounting
ISBN:9781337619202
Author:Hall, James A.
Publisher:Cengage Learning,
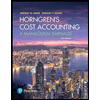
Horngren's Cost Accounting: A Managerial Emphasis...
Accounting
ISBN:9780134475585
Author:Srikant M. Datar, Madhav V. Rajan
Publisher:PEARSON
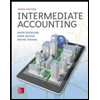
Intermediate Accounting
Accounting
ISBN:9781259722660
Author:J. David Spiceland, Mark W. Nelson, Wayne M Thomas
Publisher:McGraw-Hill Education
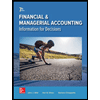
Financial and Managerial Accounting
Accounting
ISBN:9781259726705
Author:John J Wild, Ken W. Shaw, Barbara Chiappetta Fundamental Accounting Principles
Publisher:McGraw-Hill Education