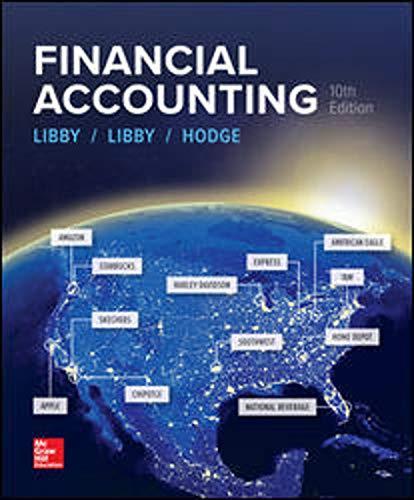
FINANCIAL ACCOUNTING
10th Edition
ISBN: 9781259964947
Author: Libby
Publisher: MCG
expand_more
expand_more
format_list_bulleted
Question
Sunland, Inc. currently manufactures a wicket as its main product. The costs per unit are as follows:
Direct materials and direct labor | $15 |
Variable |
5 |
Fixed overhead | 8 |
Total |
$28
|
Saran Company has contacted Sunland with an offer to sell it 6500 of the wickets for $22 each. If Sunland makes the wickets, variable costs are $20 per unit. Fixed costs are $8 per unit; however, $5 per unit is unavoidable. Should Sunland make or buy the wickets?
Make; savings = $6500
Make; savings = $13000
Buy; savings = $6500
Buy; savings = $19500
Expert Solution

This question has been solved!
Explore an expertly crafted, step-by-step solution for a thorough understanding of key concepts.
This is a popular solution
Trending nowThis is a popular solution!
Step by stepSolved in 2 steps with 1 images

Knowledge Booster
Learn more about
Need a deep-dive on the concept behind this application? Look no further. Learn more about this topic, accounting and related others by exploring similar questions and additional content below.Similar questions
- Stan Fawcett's company currently purchases a gear assembly from Salt Lake Supply, Inc., at $3.80 per unit with a minimum order of 3,000 units. Stan is considering instead producing the gear assembly himself. He estimates that producing it himself will cost $12,000 to set up the process and then $1.82 per unit for labor and materials. a) Using the line drawing tool, add the total cost graph for Stan to produce the assembly instead of purchasing from Salt Lake Supply. Total cost for the purchase option is already plotted. Properly label your line. Note: Carefully follow the instructions above and only draw the required object. Cost 40,000- ¡Minimum Order 36,000 32,000- 28,000- 24,000 20,000- 16,000 12,000 - 8,000- 4,000- 0+ 0 2,000 4,000 Quantity 6,000 8,000arrow_forwardVoltaic Electronics uses a standard part in the manufacture of different types of radios. The total cost of producing 36,000 parts is $ 100,000, which includes fixed costs of $ 40,000 and variable costs of $ 60,000. The company can buy the part from an outside supplier for $2 per unit and avoid 20% of the fixed costs. Assume that the company can use the freed manufacturing space to make another product that can earn a profit of $ 15,000. If Voltaic outsources, what will be the effect on operating income?A. decrease of $11,000B. increase of $ 11,000C. increase of $ 15,000D . decrease of $ 8,000arrow_forwardVista Company manufactures electronic equipment. It currently purchases the special switches used in each of its products from an outside supplier. The supplier charges Vista $5.50 per switch. Vista's CEO is considering purchasing either machine A or machine B so the company can manufacture its own switches. The projected data are as follows: Annual fixed costs Variable cost per switch Machine A $632,400 1.78 Required: 1. For each machine, what is the minimum number of switches that Vista must make annually for total costs to equal outside purchase cost? 2. What volume level would produce the same total costs regardless of the machine purchased? 3. What is the most profitable alternative for producing 235,000 switches per year and what is the total cost of that alternative? Required 1 Required 2 Required 3 Complete this question by entering your answers in the tabs below. Machine B $ 860,100 0.80 Minimum number of switches For each machine, what is the minimum number of switches that…arrow_forward
- Value Electronics uses a standard part in the manufacture of different types of radios. The total cost of producing 32,000 parts is $90,000, which includes fixed costs of $30,000 and variable costs of $60,000. The company can buy this part from an external supplier for $5 per unit and avoid 10% of the fixed costs. If Value Electronics decides to outsource the production of the part, how will it impact its operating income? A. Operating income increases by $97,000. B. Operating income decreases by $100,000. C. Operating income decreases by $97,000. D. Operating income increases by $100,000.arrow_forwardJordan electronics currently produces the shipping containers it uses to deliver the electronics products it sells. The monthly costs of producing 9,100 containers follow Unit-level material $6,000 Unit-level labor $6,700 unit-level overhead $3,300 product-level costs* $11,700 Allocated facility-level costs $26,500 *one-third of these costs can be avoided by purchasing the containers. Russo container company has offered to sell comparable containers to Jordan for $2.80 each. Required a) Calculate the total relevant cost should Jordan continue to make the containers. b) Jordan could lease the space it currently uses in the manufacturing process if leasing would produce $11,700 per month, and calculate the total avoidable costs. Should Jordan continue to make the containers? a) Total relevant cost should Jordan continue to make the containers? Total avoidable cost Should Jordan continue to make the containers?arrow_forwardplease step by step solution.arrow_forward
- Dewey Manufacturing has been approached by a new customer with an offer to purchase 500 units of its hands-free automotive model SMAK at a price of $15,000 per unit. Existing sales would not be affected, and Dewey has sufficient capacity to produce the special order. Fixed overhead will not change if Dewey accepts the order or not. Unit cost data is: Per Unit: Direct Materials $6,000 Direct Labor $2,500 Variable OVHD $3,500 Fixed OVHD $10,000 $22,000 Normal sales price is $27,000. Assume Dewey decides to accept the order. How much will their operating income change? Should they have accepted the orderarrow_forwardBlue Spruce Tech produces 60,000 iPhone adapters with the following costs:arrow_forward
arrow_back_ios
arrow_forward_ios
Recommended textbooks for you
- AccountingAccountingISBN:9781337272094Author:WARREN, Carl S., Reeve, James M., Duchac, Jonathan E.Publisher:Cengage Learning,Accounting Information SystemsAccountingISBN:9781337619202Author:Hall, James A.Publisher:Cengage Learning,
- Horngren's Cost Accounting: A Managerial Emphasis...AccountingISBN:9780134475585Author:Srikant M. Datar, Madhav V. RajanPublisher:PEARSONIntermediate AccountingAccountingISBN:9781259722660Author:J. David Spiceland, Mark W. Nelson, Wayne M ThomasPublisher:McGraw-Hill EducationFinancial and Managerial AccountingAccountingISBN:9781259726705Author:John J Wild, Ken W. Shaw, Barbara Chiappetta Fundamental Accounting PrinciplesPublisher:McGraw-Hill Education
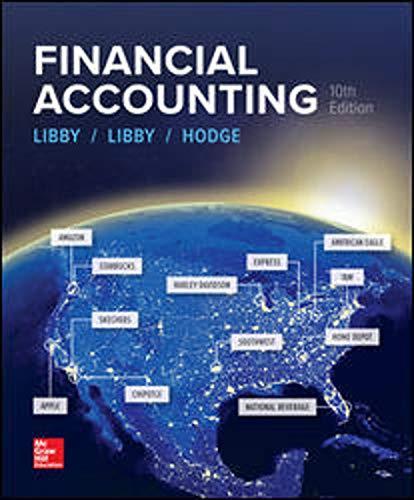
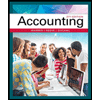
Accounting
Accounting
ISBN:9781337272094
Author:WARREN, Carl S., Reeve, James M., Duchac, Jonathan E.
Publisher:Cengage Learning,
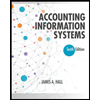
Accounting Information Systems
Accounting
ISBN:9781337619202
Author:Hall, James A.
Publisher:Cengage Learning,
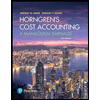
Horngren's Cost Accounting: A Managerial Emphasis...
Accounting
ISBN:9780134475585
Author:Srikant M. Datar, Madhav V. Rajan
Publisher:PEARSON
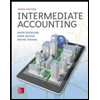
Intermediate Accounting
Accounting
ISBN:9781259722660
Author:J. David Spiceland, Mark W. Nelson, Wayne M Thomas
Publisher:McGraw-Hill Education
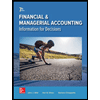
Financial and Managerial Accounting
Accounting
ISBN:9781259726705
Author:John J Wild, Ken W. Shaw, Barbara Chiappetta Fundamental Accounting Principles
Publisher:McGraw-Hill Education