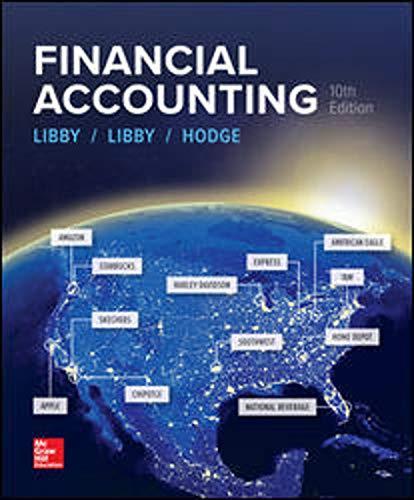
FINANCIAL ACCOUNTING
10th Edition
ISBN: 9781259964947
Author: Libby
Publisher: MCG
expand_more
expand_more
format_list_bulleted
Question
Mainstay Auto uses a standard part in the manufacture of several of its trucks. The cost of producing 40,000 parts is $120,000, which includes fixed costs of $60,000 and variable costs of $60,000. The company can buy the part from an outside supplier for $3.00 per unit, and avoid 30% of the fixed costs.
Assume that factory space freed up by purchasing the part from an outside source can be used to manufacture another product that can be sold for $12,000 profit. If Mainstay Auto makes the part, what will its operating income be?
Select one:
a. $150,000 greater than if the company bought the part
b. $30,000 greater than if the company bought the part
c. $30,000 less than if the company bought the part
d. $54,000 greater than if the company bought the part
e. $54,000 less than if the company bought the part
Expert Solution

This question has been solved!
Explore an expertly crafted, step-by-step solution for a thorough understanding of key concepts.
Step by stepSolved in 2 steps

Knowledge Booster
Learn more about
Need a deep-dive on the concept behind this application? Look no further. Learn more about this topic, accounting and related others by exploring similar questions and additional content below.Similar questions
- Tool Time manufactures carpenter-grade screwdrivers. The company is trying to decide whether to continue to make the case in which the screwdrivers are sold, or to outsource the case to another company. The direct material and direct labor cost to produce the cases total $2.40 per case. The overhead cost is $1.00 per case which consists of $0.40 in variable overhead that would be eliminated if the cases are bought from the outside supplier. The $0.60 of fixed overhead is based on expected production of 400,000 cases per year and consists of the salary of the case production manager of $80,000 per year, along with the remainder consisting of rent, insurance, and depreciation on equipment that will have no resale value. The manager will be laid off if the cases were bought externally. The outside supplier has offered to supply the cases for $3.40 each. How much will Tool Time save or lose if the cases are bought externally? Save $0.40 per case Lose $0.20 per case…arrow_forwardAdams Electronics currently produces the shipping containers it uses to deliver the electronics products it sells. The monthly cost of producing 9,300 containers follows. Unit-level materials Unit-level labor Unit-level overhead Product-level costs* Allocated facility-level costs $5,900 6,200 3,500 *One-third of these costs can be avoided by purchasing the containers. Russo Container Company has offered to sell comparable containers to Adams for $2.60 each. Required X Answer is complete but not entirely correct. $ 19,300 Yes $ 24,180 X No 11,100 26,900 a. Calculate the total relevant cost. Should Adams continue to make the containers? b. Adams could lease the space it currently uses in the manufacturing process. If leasing would produce $11,800 per month, calculate the total avoidable costs. Should Adams continue to make the containers? a. Total relevant cost a. Should Adams continue to make the containers? b. Total avoidable cost b. Should Adams continue to make the containers?arrow_forwardBramble Company manufactures widgets. Blossom Company has approached Bramble with a proposal to sell the company widgets at a price of $60500 for 100,000 units. Bramble is currently making these components in its own factory. The following costs are associated with this part of the process when 100,000 units are produced: Direct material $22700 Direct labour 23000 Manufacturing overhead 29000 Total $74700 The manufacturing overhead consists of $12300 of costs that will be eliminated if the components are no longer produced by Bramble. From Bramble’s point of view, how much is the incremental cost or savings if the widgets are bought instead of made? $14200 incremental savings $2500 incremental savings $2500 incremental cost $14200 incremental costarrow_forward
- Bridgeport Racers makes bicycles. It has always purchased its bicycle tires from the Cullumber Tires at $26 each but is currently considering making the tires in its own factory. The estimated costs per unit of making the tires are as follows: Direct materials $9 Direct labor $5 Variable manufacturing overhead $8 The company’s fixed expenses would increase by $73,000 per year if managers decided to make the tire.(a1) Calculate total relevant cost to make or buy if the company needs 11,300 tires a year. Make Buy Total relevant cost $enter a dollar amount $enter a dollar amount (a2) Ignoring qualitative factors, if the company needs 11,300 tires a year, should it continue to purchase them from Balyo or begin to produce them internally? The company select an option should not continueshould continue to purchase the tires.arrow_forwardTamarisk Manufacturing incurs unit costs of $7.20 ($5.20 variable and $2.00 fixed) in making a sub-assembly part for its finished product. A supplier offers to make 17,200 of the parts for $5.70 per unit. If it accepts the offer, Tamarisk will save all variable costs and $1.00 of fixed costs. Prepare an analysis showing the total cost savings, if any, that Tamarisk will realize by buying the part. (Round per unit answers to 2 decimal places, eg. 15.25. If an amount reduces the net income then enter with a negative sign preceding the number, e.g.-15,000 or parenthesis, e.g. (15,000).)arrow_forwardDiamond Computer Company has been purchasing carrying cases for its portable computers at a purchase price of $84 per unit. The company, which is currently operating below full capacity, charges factory overhead to production at the rate of 50% of direct labor cost. The fully absorbed unit costs to produce comparable carrying cases are expected to be as follows: Direct materials $56 Direct labor 20 Factory overhead (50% of direct labor) 10 Total cost per unit $86 If Diamond Computer Company manufactures the carrying cases, fixed factory overhead costs will not increase and variable factory overhead costs associated with the cases are expected to be 10% of the direct labor costs. Required: A. Prepare a differential analysis, dated February 24 to determine whether the company should make (Alternative 1) or buy (Alternative 2) the carrying case. Refer to the lists of Labels and Amount Descriptions for the exact wording of the answer choices for text…arrow_forward
- Dineshkakaarrow_forwardStan Fawcett's company currently purchases a gear assembly from Salt Lake Supply, Inc., at $3.80 per unit with a minimum order of 3,000 units. Stan is considering instead producing the gear assembly himself. He estimates that producing it himself will cost $12,000 to set up the process and then $1.82 per unit for labor and materials. a) Using the line drawing tool, add the total cost graph for Stan to produce the assembly instead of purchasing from Salt Lake Supply. Total cost for the purchase option is already plotted. Properly label your line. Note: Carefully follow the instructions above and only draw the required object. Cost 40,000- ¡Minimum Order 36,000 32,000- 28,000- 24,000 20,000- 16,000 12,000 - 8,000- 4,000- 0+ 0 2,000 4,000 Quantity 6,000 8,000arrow_forwardVoltaic Electronics uses a standard part in the manufacture of different types of radios. The total cost of producing 36,000 parts is $ 100,000, which includes fixed costs of $ 40,000 and variable costs of $ 60,000. The company can buy the part from an outside supplier for $2 per unit and avoid 20% of the fixed costs. Assume that the company can use the freed manufacturing space to make another product that can earn a profit of $ 15,000. If Voltaic outsources, what will be the effect on operating income?A. decrease of $11,000B. increase of $ 11,000C. increase of $ 15,000D . decrease of $ 8,000arrow_forward
- Vista Company manufactures electronic equipment. It currently purchases the special switches used in each of its products from an outside supplier. The supplier charges Vista $5.50 per switch. Vista's CEO is considering purchasing either machine A or machine B so the company can manufacture its own switches. The projected data are as follows: Annual fixed costs Variable cost per switch Machine A $632,400 1.78 Required: 1. For each machine, what is the minimum number of switches that Vista must make annually for total costs to equal outside purchase cost? 2. What volume level would produce the same total costs regardless of the machine purchased? 3. What is the most profitable alternative for producing 235,000 switches per year and what is the total cost of that alternative? Required 1 Required 2 Required 3 Complete this question by entering your answers in the tabs below. Machine B $ 860,100 0.80 Minimum number of switches For each machine, what is the minimum number of switches that…arrow_forwardAncinas Company produces printers and uses a standard part in the manufacture of several of its printers. The cost of producing 43,000 parts is $280,000, which includes fixed costs of $136,000 and variable costs of $144,000. The company can buy the part from an outside supplier for $5.00 per unit, and avoid 30% of the fixed costs. If Ancinas Company makes the part, how much will its operating income be? $30,200 less than if the company bought the part. $30,200 greater than if the company bought the part. $65,000 greater than if the company bought the part. $65,000 less than if the company bought the part.arrow_forwardA company makes 36,000 motors to be used in the production of its blender. The average cost per motor at this level of activity is: Direct materials Direct labor Variable manufacturing overhead Fixed manufacturing overhead An outside supplier recently began producing a comparable motor that could be used in the blender. The price offered to the company for this motor is $23.95. There would be no other use for the production facilities and none of the fixed manufacturing overhead cost could be avoided. The annual financial advantage (disadvantage) for the company as a result of making the motors rather than buying them from the outside supplier would be: Multiple Choice O O O ($68,400) $214,200 $9.50 $ 8.50 $ 3.45 $ 4.40 90,000 $158,400arrow_forward
arrow_back_ios
SEE MORE QUESTIONS
arrow_forward_ios
Recommended textbooks for you
- AccountingAccountingISBN:9781337272094Author:WARREN, Carl S., Reeve, James M., Duchac, Jonathan E.Publisher:Cengage Learning,Accounting Information SystemsAccountingISBN:9781337619202Author:Hall, James A.Publisher:Cengage Learning,
- Horngren's Cost Accounting: A Managerial Emphasis...AccountingISBN:9780134475585Author:Srikant M. Datar, Madhav V. RajanPublisher:PEARSONIntermediate AccountingAccountingISBN:9781259722660Author:J. David Spiceland, Mark W. Nelson, Wayne M ThomasPublisher:McGraw-Hill EducationFinancial and Managerial AccountingAccountingISBN:9781259726705Author:John J Wild, Ken W. Shaw, Barbara Chiappetta Fundamental Accounting PrinciplesPublisher:McGraw-Hill Education
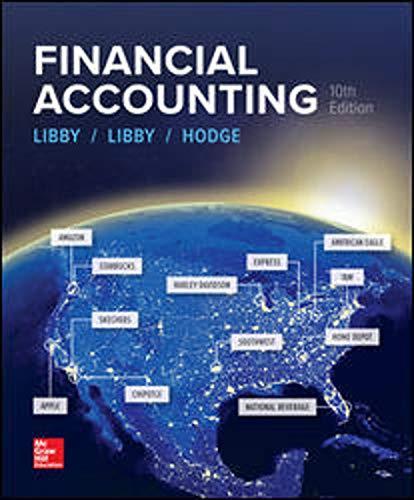
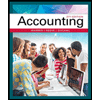
Accounting
Accounting
ISBN:9781337272094
Author:WARREN, Carl S., Reeve, James M., Duchac, Jonathan E.
Publisher:Cengage Learning,
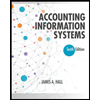
Accounting Information Systems
Accounting
ISBN:9781337619202
Author:Hall, James A.
Publisher:Cengage Learning,
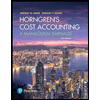
Horngren's Cost Accounting: A Managerial Emphasis...
Accounting
ISBN:9780134475585
Author:Srikant M. Datar, Madhav V. Rajan
Publisher:PEARSON
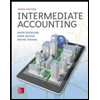
Intermediate Accounting
Accounting
ISBN:9781259722660
Author:J. David Spiceland, Mark W. Nelson, Wayne M Thomas
Publisher:McGraw-Hill Education
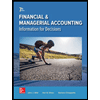
Financial and Managerial Accounting
Accounting
ISBN:9781259726705
Author:John J Wild, Ken W. Shaw, Barbara Chiappetta Fundamental Accounting Principles
Publisher:McGraw-Hill Education