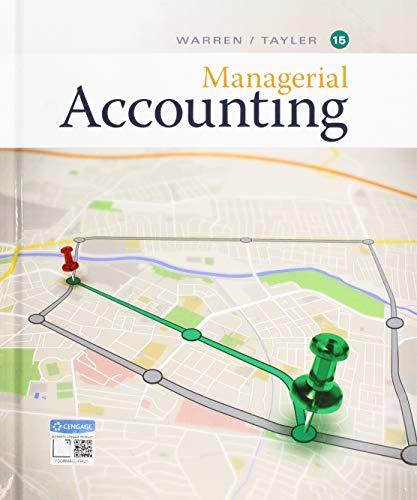
Managerial Accounting
15th Edition
ISBN: 9781337912020
Author: Carl Warren, Ph.d. Cma William B. Tayler
Publisher: South-Western College Pub
expand_more
expand_more
format_list_bulleted
Question
Need help with this accounting question
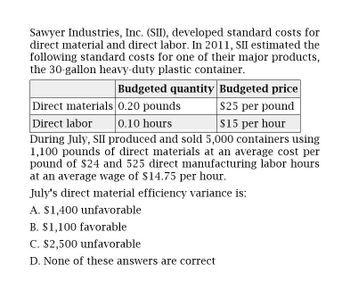
Transcribed Image Text:Sawyer Industries, Inc. (SII), developed standard costs for
direct material and direct labor. In 2011, SII estimated the
following standard costs for one of their major products,
the 30-gallon heavy-duty plastic container.
Budgeted quantity Budgeted price
Direct materials 0.20 pounds
Direct labor
0.10 hours
$25 per pound
$15 per hour
During July, SII produced and sold 5,000 containers using
1,100 pounds of direct materials at an average cost per
pound of $24 and 525 direct manufacturing labor hours
at an average wage of $14.75 per hour.
July's direct material efficiency variance is:
A. $1,400 unfavorable
B. $1,100 favorable
C. $2,500 unfavorable
D. None of these answers are correct
Expert Solution

This question has been solved!
Explore an expertly crafted, step-by-step solution for a thorough understanding of key concepts.
Step by stepSolved in 2 steps

Knowledge Booster
Similar questions
- JoyT Company manufactures Maxi Dolls for sale in toy stores. In planning for this year, JoyT estimated variable factory overhead of 600,000 and fixed factory overhead of 400,000. JoyT uses a standard costing system, and factory overhead is allocated to units produced using standard direct labor hours. The level of activity budgeted for this year was 10,000 direct labor hours, and JoyT used 10,300 actual direct labor hours. Based on the output accomplished during this year, 9,900 standard direct labor hours should have been used. Actual variable factory overhead was 596,000, and actual fixed factory overhead was 410,000 for the year. Based on this information, the variable factory overhead controllable variance for JoyT for this year was: a. 24,000 unfavorable. b. 2,000 unfavorable. c. 4,000 favorable. d. 22,000 favorable.arrow_forwardKrouse Company produces two products, forged putter heads and laminated putter heads, which are sold through specialty golf shops. The company is in the process of developing itsoperating budget for the coming year. Selected data regarding the companys two products areas follows: Manufacturing overhead is applied to units using direct labor hours. Variable manufacturing overhead Ls projected to be 25,000, and fixed manufacturing overhead is expected to be15,000. The estimated cost to produce one unit of the laminated putter head is: a. 42. b. 46. c. 52. d. 62.arrow_forwardBusiness Specialty, Inc., manufactures two staplers: small and regular. The standard quantities of direct labor and direct materials per unit for the year are as follows: The standard price paid per pound of direct materials is 1.60. The standard rate for labor is 8.00. Overhead is applied on the basis of direct labor hours. A plantwide rate is used. Budgeted overhead for the year is as follows: The company expects to work 12,000 direct labor hours during the year; standard overhead rates are computed using this activity level. For every small stapler produced, the company produces two regular staplers. Actual operating data for the year are as follows: a. Units produced: small staplers, 35,000; regular staplers, 70,000. b. Direct materials purchased and used: 56,000 pounds at 1.5513,000 for the small stapler and 43,000 for the regular stapler. There were no beginning or ending direct materials inventories. c. Direct labor: 14,800 hours3,600 hours for the small stapler and 11,200 hours for the regular stapler. Total cost of direct labor: 114,700. d. Variable overhead: 607,500. e. Fixed overhead: 350,000. Required: 1. Prepare a standard cost sheet showing the unit cost for each product. 2. Compute the direct materials price and usage variances for each product. Prepare journal entries to record direct materials activity. 3. Compute the direct labor rate and efficiency variances for each product. Prepare journal entries to record direct labor activity. 4. Compute the variances for fixed and variable overhead. Prepare journal entries to record overhead activity. All variances are closed to Cost of Goods Sold. 5. Assume that you know only the total direct materials used for both products and the total direct labor hours used for both products. Can you compute the total direct materials and direct labor usage variances? Explain.arrow_forward
- Jameson Company produces paper towels. The company has established the following direct materials and direct labor standards for one case of paper towels: During the first quarter of the year, Jameson produced 45,000 cases of paper towels. The company purchased and used 135,700 pounds of paper pulp at 0.38 per pound. Actual direct labor used was 91,000 hours at 12.10 per hour. Required: 1. Calculate the direct materials price and usage variances. 2. Calculate the direct labor rate and efficiency variances. 3. Prepare the journal entries for the direct materials and direct labor variances. 4. Describe how flexible budgeting variances relate to the direct materials and direct labor variances computed in Requirements 1 and 2.arrow_forwardLean accounting Dashboard Inc. manufactures and assembles automobile instrument panels for both eCar Motors and Greenville Motors. The process consists of a lean product cell for each customers instrument assembly. The data that follow concern only the eCar lean cell. For the year, Dashboard Inc. budgeted the following costs for the eCar production cell: Dashboard Inc. plans 2,000 hours of production for the eCar cell for the year. The materials cost is 240 per instrument assembly. Each assembly requires 24 minutes of cell assembly time. There was no April 1 inventory for either Raw and In Process Inventory or Finished Goods Inventory. The following summary events took place in the eCar cell during April: A. Electronic parts and wiring were purchased to produce 450 instrument assemblies in April. B. Conversion costs were applied for the production of 400 units in April. C. 380 units were started, completed, and transferred to finished goods in April. D. 350 units were shipped to customers at a price of 800 per unit. Instructions 1. Determine the budgeted cell conversion cost per hour. 2. Determine the budgeted cell conversion cost per unit. 3. Journalize the summary transactions (a) through (d). 4. Determine the ending balance in Raw and In Process Inventory and Finished Goods Inventory. 5. How does the accounting in a lean environment differ from traditional accounting?arrow_forwardAdam Corporation manufactures computer tables and has the following budgeted indirect manufacturing cost information for the next year: If Adam uses the step-down (sequential) method, beginning with the Maintenance Department, to allocate support department costs to production departments, the total overhead (rounded to the nearest dollar) for the Machining Department to allocate to its products would be: a. 407,500. b. 422,750. c. 442,053. d. 445,000.arrow_forward
- Nashler Company has the following budgeted variable costs per unit produced: Budgeted fixed overhead costs per month include supervision of 98,000, depreciation of 76,000, and other overhead of 245,000. Required: 1. Prepare a flexible budget for all costs of production for the following levels of production: 160,000 units, 170,000 units, and 175,000 units. 2. What is the per-unit total product cost for each of the production levels from Requirement 1? (Round each unit cost to the nearest cent.) 3. What if Nashler Companys cost of maintenance rose to 0.22 per unit? How would that affect the unit product costs calculated in Requirement 2?arrow_forwardDouglas Davis, controller for Marston, Inc., prepared the following budget for manufacturing costs at two different levels of activity for 20X1: During 20X1, Marston worked a total of 80,000 direct labor hours, used 250,000 machine hours, made 32,000 moves, and performed 120 batch inspections. The following actual costs were incurred: Marston applies overhead using rates based on direct labor hours, machine hours, number of moves, and number of batches. The second level of activity (the right column in the preceding table) is the practical level of activity (the available activity for resources acquired in advance of usage) and is used to compute predetermined overhead pool rates. Required: 1. Prepare a performance report for Marstons manufacturing costs in the current year. 2. Assume that one of the products produced by Marston is budgeted to use 10,000 direct labor hours, 15,000 machine hours, and 500 moves and will be produced in five batches. A total of 10,000 units will be produced during the year. Calculate the budgeted unit manufacturing cost. 3. One of Marstons managers said the following: Budgeting at the activity level makes a lot of sense. It really helps us manage costs better. But the previous budget really needs to provide more detailed information. For example, I know that the moving materials activity involves the use of forklifts and operators, and this information is lost when only the total cost of the activity for various levels of output is reported. We have four forklifts, each capable of providing 10,000 moves per year. We lease these forklifts for five years, at 10,000 per year. Furthermore, for our two shifts, we need up to eight operators if we run all four forklifts. Each operator is paid a salary of 30,000 per year. Also, I know that fuel costs about 0.25 per move. Assuming that these are the only three items, expand the detail of the flexible budget for moving materials to reveal the cost of these three resource items for 20,000 moves and 40,000 moves, respectively. Based on these comments, explain how this additional information can help Marston better manage its costs. (Especially consider how activity-based budgeting may provide useful information for non-value-added activities.)arrow_forwardJillian Manufacturing Inc. manufactures a single product and uses a standard cost system. The factory overhead is applied on the basis of direct labor hours. A condensed version of the company’s flexible budget follows: The product requires 3 lb of materials at a standard cost of $5 per pound and 2 hours of direct labor at a standard cost of $10 per hour. For the current year, the company planned to operate at the level of 6,250 direct labor hours and to produce 3,125 units of product. Actual production and costs for the year follow: Required: For the current year, compute the factory overhead rate that will be used for production. Show the variable and fixed components that make up the total predetermined rate to be used. Prepare a standard cost card for the product. Show the individual elements of the overhead rate as well as the total rate. Compute (a) standard hours allowed for production and (b) under- or overapplied factory overhead for the year. Determine the reason for any under- or overapplied factory overhead for the year by computing all variances, using each of the following methods: Two-variance method Three-variance method (appendix) Four-variance method (appendix)arrow_forward
- Shinto Corp. uses a standard cost system and manufactures one product. The variable costs per product follow: Budgeted fixed overhead costs for the month are $4,000, and Shinto expected to manufacture 2,000 units. Actual production, however, was only 1,800 units. Materials prices were 10% over standard, and labor rates were 5% over standard. Of the factory overhead expense, only 80% was used, and fixed overhead was $100 over budget. The actual variable overhead cost was $4,800. In materials usage, 8% more parts were used than were allowed for actual production by the standard, and 6% more labor hours were used than were allowed. Required: Calculate the materials and labor variances. Calculate the variances for overhead by the four-variance method. (Hint: First compute the fixed and variable overhead rates per hour.)arrow_forwardLens & Shades sells sunglasses for $37 each and is estimating sales of 21,000 units in January and 19,000 in February. Each lens consist of 2.00 mm of plastic costing $2.50 per mm, 1.7 oz of dye costing $2.80 per ounce. and 0.50 hours direct labor at a labor rate of $18 per unit. Desired inventory levels are: Prepare a sales budget, production budget, direct materials budget for silicon and solution, and a direct labor budget.arrow_forwardCloud Shoes manufactures recovery sandals and is planning on producing 12.000 units in March and 11,500 in April. Each sandal requires 1.2 yards if material, which costs $3.00 per yard. The companys policy is to have enough material on hand to equal 15% of next months production needs and to maintain a finished goods inventory equal to 20% of the next months production needs. What is the budgeted cost of purchases for March?arrow_forward
arrow_back_ios
SEE MORE QUESTIONS
arrow_forward_ios
Recommended textbooks for you
- Managerial AccountingAccountingISBN:9781337912020Author:Carl Warren, Ph.d. Cma William B. TaylerPublisher:South-Western College PubFinancial And Managerial AccountingAccountingISBN:9781337902663Author:WARREN, Carl S.Publisher:Cengage Learning,Cornerstones of Cost Management (Cornerstones Ser...AccountingISBN:9781305970663Author:Don R. Hansen, Maryanne M. MowenPublisher:Cengage Learning
- Principles of Cost AccountingAccountingISBN:9781305087408Author:Edward J. Vanderbeck, Maria R. MitchellPublisher:Cengage LearningPrinciples of Accounting Volume 2AccountingISBN:9781947172609Author:OpenStaxPublisher:OpenStax CollegeExcel Applications for Accounting PrinciplesAccountingISBN:9781111581565Author:Gaylord N. SmithPublisher:Cengage Learning
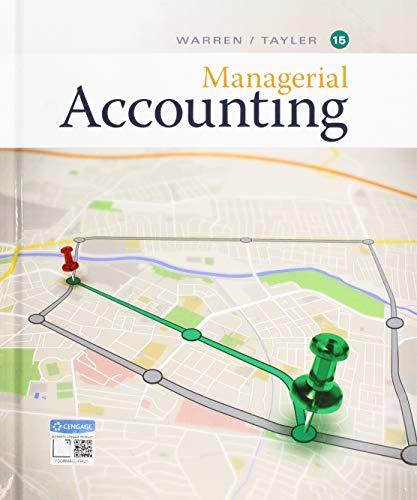
Managerial Accounting
Accounting
ISBN:9781337912020
Author:Carl Warren, Ph.d. Cma William B. Tayler
Publisher:South-Western College Pub
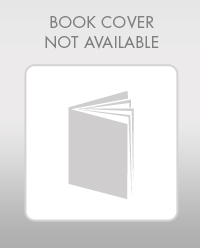
Financial And Managerial Accounting
Accounting
ISBN:9781337902663
Author:WARREN, Carl S.
Publisher:Cengage Learning,
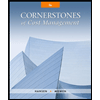
Cornerstones of Cost Management (Cornerstones Ser...
Accounting
ISBN:9781305970663
Author:Don R. Hansen, Maryanne M. Mowen
Publisher:Cengage Learning
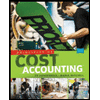
Principles of Cost Accounting
Accounting
ISBN:9781305087408
Author:Edward J. Vanderbeck, Maria R. Mitchell
Publisher:Cengage Learning
Principles of Accounting Volume 2
Accounting
ISBN:9781947172609
Author:OpenStax
Publisher:OpenStax College
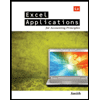
Excel Applications for Accounting Principles
Accounting
ISBN:9781111581565
Author:Gaylord N. Smith
Publisher:Cengage Learning