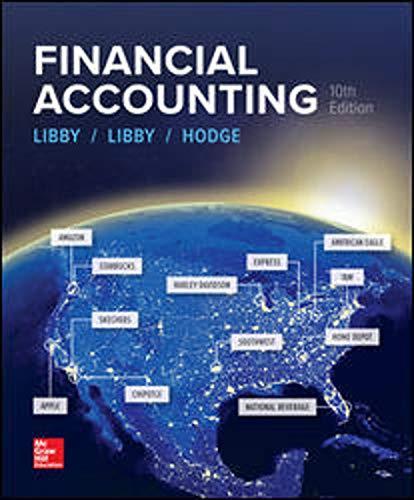
FINANCIAL ACCOUNTING
10th Edition
ISBN: 9781259964947
Author: Libby
Publisher: MCG
expand_more
expand_more
format_list_bulleted
Concept explainers
Question
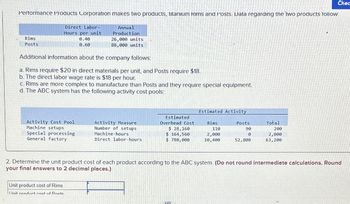
Transcribed Image Text:Performance Products Corporation makes two products, titanium Rims and Posts. Data regarding the two products follow:
Direct Labor-
Hours per unit
Rims
Posts
0.40
0.60
Annual
Production
26,000 units
88,000 units
Chec
Additional information about the company follows:
a. Rims require $20 in direct materials per unit, and Posts require $18.
b. The direct labor wage rate is $18 per hour.
c. Rims are more complex to manufacture than Posts and they require special equipment.
d. The ABC system has the following activity cost pools:
Estimated Activity
Activity Cost Pool
Machine setups
Special processing
General factory
Activity Measure
Number of setups
Machine-hours.
Estimated
Overhead Cost
$ 28,160
Rims
110
Posts
90
Total
200
$ 164,560
2,000
0
2,000
Direct labor-hours
$ 780,000
10,400
52,800
63,200
2. Determine the unit product cost of each product according to the ABC system. (Do not round intermediate calculations. Round
your final answers to 2 decimal places.)
Unit product cost of Rims
I Init product cost of Docte
Expert Solution

This question has been solved!
Explore an expertly crafted, step-by-step solution for a thorough understanding of key concepts.
This is a popular solution
Trending nowThis is a popular solution!
Step by stepSolved in 4 steps with 1 images

Knowledge Booster
Learn more about
Need a deep-dive on the concept behind this application? Look no further. Learn more about this topic, accounting and related others by exploring similar questions and additional content below.Similar questions
- Gelb Company currently makes a key part for its main product. Making this part incurs per unit variable costs of $1.30 for direct materials and $0.85 for direct labor. Incremental overhead to make this part is $1.44 per unit. The company can buy the part for $3.76 per unit. (a) Prepare a make or buy analysis of costs for this part. (Enter your answers rounded to 2 decimal places.) (b) Should Gelb make or buy the part? (a) Make or Buy Analysis Direct materials Direct labor Overhead Cost to buy Cost per unit Cost difference (b) Company should: Make Buyarrow_forwardLeach Finishing makes various metal fittings for the construction industry. Three of the fittings, models X-12, X-24, and X-30, require grinding on a patented machine of which Leach has only one. The cost of production information for the three products follow: X-12 $35 $ 20 18.0 Price per fitting Variable cost per fitting Units per hour of grinding The testing machine used for both models has a capacity of 3,230 hours annually. Fixed manufacturing costs are $496,000 annually. Required A Required B X-24 $ 51 $ 27 12.5 Required: a. Suppose that Leach Finishing can sell at most 59,200 units of any one fitting. How many units of each fitting model should Leach Finishing produce annually? b. Suppose that Leach Finishing can sell at most 18,000 units of any one fitting. How many units of each fitting should Leach Finishing produce annually? X-30 $ 70 $ 44 10.0 Complete this question by entering your answers in the tabs below. X-12 X-24 X-30 units units units Suppose that Leach Finishing can…arrow_forwardRequired information [The following information applies to the questions displayed below.] Performance Products Corporation makes two products, titanium Rims and Posts. Data regarding the two products follow: Rims Posts: Direct Labor- Hours per unit 0.40 0.60 Additional information about the company follows: a. Rims require $20 in direct materials per unit, and Posts require $18. b. The direct labor wage rate is $18 per hour. c. Rims are more complex to manufacture than Posts and they require special equipment. d. The ABC system has the following activity cost pools: Activity Cost Pool Machine setups Special processing General factory Annual Production 26,000 units 88,000 units Unit product cost of Rims Unit product cost of Posts Activity Measure Number of setups Machine-hours Direct labor-hours. Estimated Overhead Cost $28,160 $ 164,560 $ 780,000 Estimated Activity Rims 110 2,000 10,400 Posts 90 0 52,800 Total 200 2,000 63,200 2. Determine the unit product cost of each product…arrow_forward
- Becton Labs, Incorporated, produces various chemical compounds for industrial use. One compound, called Fludex, has the following standard cost per unit: Standard Quantity or Hours Standard Price or Rate Standard Cost Direct materials 2.40 ounces $ 18.00 per ounce $ 43.20 Direct labor 0.70 hours $ 14.00 per hour 9.80 Variable manufacturing overhead 0.70 hours $ 3.00 per hour 2.10 Total standard cost per unit $ 55.10 During November, the following activity was recorded related to the production of Fludex: Materials purchased, 12,000 ounces at a cost of $198,000. There was no beginning inventory of materials; however, at the end of the month, 3,200 ounces of material remained in ending inventory. The company employs 20 lab technicians to work on the production of Fludex. During November, they each worked an average of 160 hours at an average pay rate of $12.00 per hour. Variable manufacturing overhead is assigned to Fludex on the basis of direct labor-hours.…arrow_forwardPetrillo Company produces engine parts for large motors. The company usesa standard cost system for production costing and control. The standard costsheet for one of its higher volume products (a valve) is as follows: Direct materials (7 lbs @$5,4) $37,80 Direct labor (1,75 lbs @$18) $31,50 Variable overhead (1,75 lbs @$4) $7 Fixed overhead (1,75 lbs @$3) $5,25 Standard unit cost $81,55 During the year, Petrillo had the following activity related to valve production:a. Production of valves totaled 20,600 units.b. A total of 135,400 pounds of direct materials was purchased at $5.36per pound.c. There were 10,000 pounds of direct materials in beginning inventory(carried at $5.40 per pound). There was no ending inventory. d. The company used 36,500 direct labor hours at a total cost of $656,270.e. Actual fixed overhead totaled $110,000.f. Actual variable overhead totaled $168,000.Petrillo produces all of its valves in a single plant. Normal activity is 20,000units per year. Standard…arrow_forwardCane Company manufactures two products called Alpha and Beta that sell for $155 and $115, respectively. Each product uses only one type of raw material that costs $6 per pound. The company has the capacity to annually produce 110,000 units of each product. Its average cost per unit for each product at this level of activity are given below: Alpha Beta Direct materials $ 24 $ 12 Direct labor 23 26 Variable manufacturing overhead 22 12 Traceable fixed manufacturing overhead 23 25 Variable selling expenses 19 15 Common fixed expenses 22 17 Total cost per unit $ 133 $ 107 The company considers its traceable fixed manufacturing overhead to be avoidable, whereas its common fixed expenses are unavoidable and have been allocated to products based on sales dollars. Required: 1. What is the total amount of traceable fixed manufacturing overhead for each of the two products? what is the alpha and betaarrow_forward
- Cane Company manufactures two products called Alpha and Beta that sell for $185 and $120, respectively. Each product uses only one type of raw material that costs $5 per pound. The company has the capacity to annually produce 112,000 units of each product. Its average cost per unit for each product at this level of activity are given below: Alpha Beta $ 30 $ 10 Direct materials Direct labor 22 Variable manufacturing overhead 20 Traceable fixed manufacturing overhead 24 Variable selling expenses 20 Common fixed expenses 23 Total cost per unit $ 139 $ 112 The company considers its traceable fixed manufacturing overhead to be avoidable, whereas its common fixed expenses are unavoidable and have been allocated to products based on sales dollars. 29 13 26 16 18 14. Assume that Cane's customers would buy a maximum of 88,000 units of Alpha and 68,000 units of Beta. Also assume that the raw material available for production is limited to 172,000 pounds. What is the total contribution margin…arrow_forwardFogerty Company makes two products-titanium Hubs and Sprockets. Data regarding the two products follow: Direct Labor-Hours per Unit Annual Production 16,000 units 53,000 units Hubs Sprockets Additional information about the company follows: a. Hubs require $34 in direct materials per unit, and Sprockets require $13. b. The direct labor wage rate is $19 per hour. 0.80 0.40 c. Hubs require special equipment and are more complex to manufacture than Sprockets. d. The ABC system has the following activity cost pools: Activity Cost Pool (Activity Measure) Machine setups (number of setups) Special processing (machine-hours) General factory (organization-sustaining) Estimated Overhead Cost $ 26,910 $ 120,000 $ 330,800 Required: 1. Compute the activity rate for each activity cost pool. 2. Determine the unit product cost of each product according to the ABC system. Hubs 130 4,000 NA Activity Sprockets 104 0 ΝΑ Total 234 4,000 ΝΑarrow_forwardCane Company manufactures two products called Alpha and Beta that sell for $155 and $115, respectively. Each product uses only one type of raw material that costs $6 per pound. The company has the capacity to annually produce 110,000 units of each product. Its average cost per unit for each product at this level of activity are given below: Alpha Beta Direct materials $ 24 $ 12 Direct labor 23 26 Variable manufacturing overhead 22 12 Traceable fixed manufacturing overhead 23 25 Variable selling expenses 19 15 Common fixed expenses 22 17 Total cost per unit $ 133 $ 107 The company considers its traceable fixed manufacturing overhead to be avoidable, whereas its common fixed expenses are unavoidable and have been allocated to products based on sales dollars. 2. What is the company’s total amount of common fixed expenses? 3. Assume that Cane expects to produce and sell 87,000 Alphas during the current year. One of Cane's sales representatives has found a…arrow_forward
- Gelb Company currently makes a key part for its main product. Making this part incurs per unit variable costs of $1.40 for direct materials and $0.95 for direct labor. Incremental overhead to make this part is $1.48 per unit. The company can buy the part for $4.02 per unit. (a) Prepare a make or buy analysis of costs for this part. Note: Enter your answers rounded to 2 decimal places. (b) Should Gelb make or buy the part? (a) Make or Buy Analysis Direct materials Direct labor Overhead Cost to buy Cost per unit Cost difference (b) Company should: Make Buyarrow_forwardPlease do not give image format and explanationarrow_forwardCane Company manufactures two products called Alpha and Beta that sell for $120 and $80, respectively. Each product uses only one type of raw material that costs $6 per pound. The company has the capacity to annually produce 100,000 units of each product. Its average cost per unit for each product at this level of activity are given below: Direct materials Alpha $ 30 Beta $ 12 Direct labor 20 15 Variable manufacturing overhead 7 5 Traceable fixed manufacturing overhead 16 18 Variable selling expenses 12 8 Common fixed expenses 15 10 Total cost per unit $ 100 $ 68 The company considers its traceable fixed manufacturing overhead to be avoidable, whereas its common fixed expenses are unavoidable and have been allocated to products based on sales dollars. 6. Assume that Cane normally produces and sells 90,000 Betas per year. What is the financial advantage (disadvantage) of discontinuing the Beta product line?arrow_forward
arrow_back_ios
arrow_forward_ios
Recommended textbooks for you
- AccountingAccountingISBN:9781337272094Author:WARREN, Carl S., Reeve, James M., Duchac, Jonathan E.Publisher:Cengage Learning,Accounting Information SystemsAccountingISBN:9781337619202Author:Hall, James A.Publisher:Cengage Learning,
- Horngren's Cost Accounting: A Managerial Emphasis...AccountingISBN:9780134475585Author:Srikant M. Datar, Madhav V. RajanPublisher:PEARSONIntermediate AccountingAccountingISBN:9781259722660Author:J. David Spiceland, Mark W. Nelson, Wayne M ThomasPublisher:McGraw-Hill EducationFinancial and Managerial AccountingAccountingISBN:9781259726705Author:John J Wild, Ken W. Shaw, Barbara Chiappetta Fundamental Accounting PrinciplesPublisher:McGraw-Hill Education
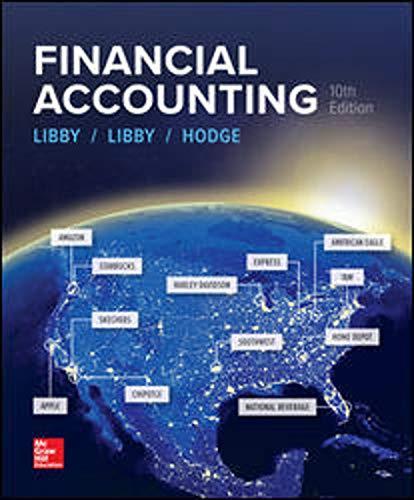
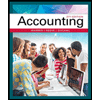
Accounting
Accounting
ISBN:9781337272094
Author:WARREN, Carl S., Reeve, James M., Duchac, Jonathan E.
Publisher:Cengage Learning,
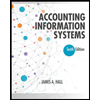
Accounting Information Systems
Accounting
ISBN:9781337619202
Author:Hall, James A.
Publisher:Cengage Learning,
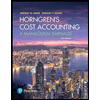
Horngren's Cost Accounting: A Managerial Emphasis...
Accounting
ISBN:9780134475585
Author:Srikant M. Datar, Madhav V. Rajan
Publisher:PEARSON
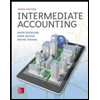
Intermediate Accounting
Accounting
ISBN:9781259722660
Author:J. David Spiceland, Mark W. Nelson, Wayne M Thomas
Publisher:McGraw-Hill Education
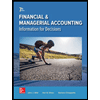
Financial and Managerial Accounting
Accounting
ISBN:9781259726705
Author:John J Wild, Ken W. Shaw, Barbara Chiappetta Fundamental Accounting Principles
Publisher:McGraw-Hill Education