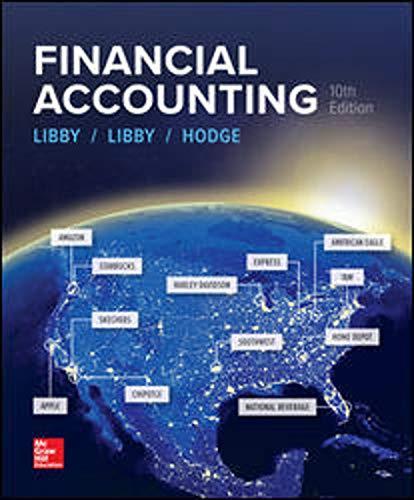
FINANCIAL ACCOUNTING
10th Edition
ISBN: 9781259964947
Author: Libby
Publisher: MCG
expand_more
expand_more
format_list_bulleted
Concept explainers
Topic Video
Question
[The following information applies to the questions displayed below.]
Performance Products Corporation makes two products, titanium Rims and Posts. Data regarding the two products follow:
Direct Labor-Hours per unit |
Annual Production |
|
Rims | 0.40 | 18,000 units |
Posts | 0.70 | 77,000 units |
Additional information about the company follows:
- Rims require $14 in direct materials per unit, and Posts require $11.
- The direct labor wage rate is $15 per hour.
- Rims are more complex to manufacture than Posts and they require special equipment.
- The ABC system has the following activity cost pools:
Estimated Activity | ||||||
Activity Cost Pool | Activity Measure | Estimated Cost |
Rims | Posts | Total | |
Machine setups | Number of setups | $ | 30,030 | 120 | 80 | 200 |
Special processing | Machine-hours | $ | 147,840 | 2,000 | 0 | 2,000 |
General factory | Direct labor-hours | $ | 576,000 | 7,000 | 29,000 | 36,000 |
Required:
1. Compute the activity rate for each activity cost pool. (Round your answers to 2 decimal places.)
Expert Solution

This question has been solved!
Explore an expertly crafted, step-by-step solution for a thorough understanding of key concepts.
This is a popular solution
Trending nowThis is a popular solution!
Step by stepSolved in 2 steps with 2 images

Knowledge Booster
Learn more about
Need a deep-dive on the concept behind this application? Look no further. Learn more about this topic, accounting and related others by exploring similar questions and additional content below.Similar questions
- Aarrow_forwardGelb Company currently makes a key part for its main product. Making this part incurs per unit variable costs of $1.30 for direct materials and $0.85 for direct labor. Incremental overhead to make this part is $1.44 per unit. The company can buy the part for $3.76 per unit. (a) Prepare a make or buy analysis of costs for this part. (Enter your answers rounded to 2 decimal places.) (b) Should Gelb make or buy the part? (a) Make or Buy Analysis Direct materials Direct labor Overhead Cost to buy Cost per unit Cost difference (b) Company should: Make Buyarrow_forwardConsider zagol manufacturing which is engaged in the manufacturing of product ABC. To produce one unit of the product the company incurs the following costs: Direct material ______$5/kg Direct labor_________$10/hour Total Manufacturing overhead __________________$30000 The company produces a total of 10000 units per month. And the actual price the product is sold is around $24. Company XYZ offers to buy a total of 5000 units this month at the price of $ 17/unit. Would you accept the order if you are the manager? (assume 20% of the manufacturing overhead is variable costarrow_forward
- Cane Company manufactures two products called Alpha and Beta that sell for $155 and $115, respectively. Each product uses only one type of raw material that costs $6 per pound. The company has the capacity to annually produce 110,000 units of each product. Its average cost per unit for each product at this level of activity are given below: Alpha Beta Direct materials $ 24 $ 12 Direct labor 23 26 Variable manufacturing overhead 22 12 Traceable fixed manufacturing overhead 23 25 Variable selling expenses 19 15 Common fixed expenses 22 17 Total cost per unit $ 133 $ 107 The company considers its traceable fixed manufacturing overhead to be avoidable, whereas its common fixed expenses are unavoidable and have been allocated to products based on sales dollars. Required: 1. What is the total amount of traceable fixed manufacturing overhead for each of the two products? what is the alpha and betaarrow_forwardCane Company manufactures two products called Alpha and Beta that sell for $185 and $120, respectively. Each product uses only one type of raw material that costs $5 per pound. The company has the capacity to annually produce 112,000 units of each product. Its average cost per unit for each product at this level of activity are given below: Alpha Beta $ 30 $ 10 Direct materials Direct labor 22 Variable manufacturing overhead 20 Traceable fixed manufacturing overhead 24 Variable selling expenses 20 Common fixed expenses 23 Total cost per unit $ 139 $ 112 The company considers its traceable fixed manufacturing overhead to be avoidable, whereas its common fixed expenses are unavoidable and have been allocated to products based on sales dollars. 29 13 26 16 18 14. Assume that Cane's customers would buy a maximum of 88,000 units of Alpha and 68,000 units of Beta. Also assume that the raw material available for production is limited to 172,000 pounds. What is the total contribution margin…arrow_forwardFogerty Company makes two products-titanium Hubs and Sprockets. Data regarding the two products follow: Direct Labor-Hours per Unit Annual Production 16,000 units 53,000 units Hubs Sprockets Additional information about the company follows: a. Hubs require $34 in direct materials per unit, and Sprockets require $13. b. The direct labor wage rate is $19 per hour. 0.80 0.40 c. Hubs require special equipment and are more complex to manufacture than Sprockets. d. The ABC system has the following activity cost pools: Activity Cost Pool (Activity Measure) Machine setups (number of setups) Special processing (machine-hours) General factory (organization-sustaining) Estimated Overhead Cost $ 26,910 $ 120,000 $ 330,800 Required: 1. Compute the activity rate for each activity cost pool. 2. Determine the unit product cost of each product according to the ABC system. Hubs 130 4,000 NA Activity Sprockets 104 0 ΝΑ Total 234 4,000 ΝΑarrow_forward
- Cane Company manufactures two products called Alpha and Beta that sell for $155 and $115, respectively. Each product uses only one type of raw material that costs $6 per pound. The company has the capacity to annually produce 110,000 units of each product. Its average cost per unit for each product at this level of activity are given below: Alpha Beta Direct materials $ 24 $ 12 Direct labor 23 26 Variable manufacturing overhead 22 12 Traceable fixed manufacturing overhead 23 25 Variable selling expenses 19 15 Common fixed expenses 22 17 Total cost per unit $ 133 $ 107 The company considers its traceable fixed manufacturing overhead to be avoidable, whereas its common fixed expenses are unavoidable and have been allocated to products based on sales dollars. 2. What is the company’s total amount of common fixed expenses? 3. Assume that Cane expects to produce and sell 87,000 Alphas during the current year. One of Cane's sales representatives has found a…arrow_forwardGelb Company currently makes a key part for its main product. Making this part incurs per unit variable costs of $1.40 for direct materials and $0.95 for direct labor. Incremental overhead to make this part is $1.48 per unit. The company can buy the part for $4.02 per unit. (a) Prepare a make or buy analysis of costs for this part. Note: Enter your answers rounded to 2 decimal places. (b) Should Gelb make or buy the part? (a) Make or Buy Analysis Direct materials Direct labor Overhead Cost to buy Cost per unit Cost difference (b) Company should: Make Buyarrow_forward! Required information [The following information applies to the questions displayed below.] Cane Company manufactures two products called Alpha and Beta that sell for $240 and $162, respectively. Each product uses only one type of raw material that costs $5 per pound. The company has the capacity to annually produce 131,000 units of each product. Its average cost per unit for each product at this level of activity is given below: Direct materials. Direct labor Variable manufacturing overhead Traceable fixed manufacturing overhead Variable selling expenses Common fixed expenses Total cost per unit Alpha $ 35 Pounds of raw materials per unit 48 27 35 Alpha 32 35 $ 212 The company's traceable fixed manufacturing overhead is avoidable, whereas its common fixed expenses are unavoidable and have been allocated to products based on sales dollars. Betal $ 15 23 11. How many pounds of raw material are needed to make one unit of each of the two products? 25 38 28 30 $ 159 Betaarrow_forward
arrow_back_ios
arrow_forward_ios
Recommended textbooks for you
- AccountingAccountingISBN:9781337272094Author:WARREN, Carl S., Reeve, James M., Duchac, Jonathan E.Publisher:Cengage Learning,Accounting Information SystemsAccountingISBN:9781337619202Author:Hall, James A.Publisher:Cengage Learning,
- Horngren's Cost Accounting: A Managerial Emphasis...AccountingISBN:9780134475585Author:Srikant M. Datar, Madhav V. RajanPublisher:PEARSONIntermediate AccountingAccountingISBN:9781259722660Author:J. David Spiceland, Mark W. Nelson, Wayne M ThomasPublisher:McGraw-Hill EducationFinancial and Managerial AccountingAccountingISBN:9781259726705Author:John J Wild, Ken W. Shaw, Barbara Chiappetta Fundamental Accounting PrinciplesPublisher:McGraw-Hill Education
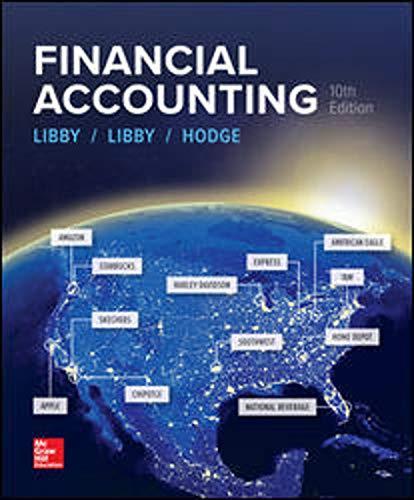
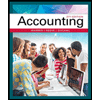
Accounting
Accounting
ISBN:9781337272094
Author:WARREN, Carl S., Reeve, James M., Duchac, Jonathan E.
Publisher:Cengage Learning,
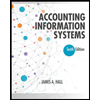
Accounting Information Systems
Accounting
ISBN:9781337619202
Author:Hall, James A.
Publisher:Cengage Learning,
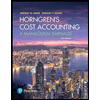
Horngren's Cost Accounting: A Managerial Emphasis...
Accounting
ISBN:9780134475585
Author:Srikant M. Datar, Madhav V. Rajan
Publisher:PEARSON
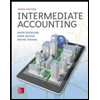
Intermediate Accounting
Accounting
ISBN:9781259722660
Author:J. David Spiceland, Mark W. Nelson, Wayne M Thomas
Publisher:McGraw-Hill Education
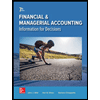
Financial and Managerial Accounting
Accounting
ISBN:9781259726705
Author:John J Wild, Ken W. Shaw, Barbara Chiappetta Fundamental Accounting Principles
Publisher:McGraw-Hill Education