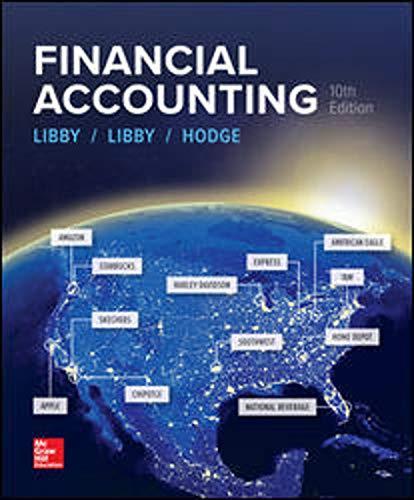
Concept explainers
Cari Colors is a manufacturer of a specialized paint. All paint go through an identical
manufacturing process. Every effort is made to ensure that all paint are identical and meet
many demanding performance specifications. The product-costing system at the POS plant
has a single direct-cost category (direct materials) and a single indirect-cost category
(conversion costs). All paint passes through two departments –the Mixing Department and
the Testing Department. Direct materials are added to the beginning of the process in Mixing.
Conversion costs are added evenly throughout the two departments. When Mixing
Department finishes work on the paint, it is immediately transferred to Testing.
Cari Colors uses the Weighted-average method of
Department for October 2017 are.
Summarize the total Mixing Department costs for October 2017, and assign these
costs to units completed (and transferred out) and to units in ending work in process
using the Weighted-average method.
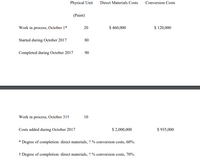

Trending nowThis is a popular solution!
Step by stepSolved in 2 steps

- ! Required information [The following information applies to the questions displayed below.] Victory Company uses weighted average process costing. The company has two production processes. Conversion cost is added evenly throughout each process. Direct materials are added at the beginning of the first process. Additional information for the first process follows. Beginning work in process inventory Units started this period Units completed and transferred out Ending work in process inventory Beginning work in process inventory Direct materials Conversion Costs added this period Direct materials Conversion Total costs to account for Cost per equivalent unit of production Units Total costs + Equivalent units of production (from part 1) Cost per equivalent unit of production 67,000 893,000 770,000 190,000 $ 499,200 88,400 3,340,800 1,679,600 Direct Materials Percent Complete 100% 100% Costs EUP Conversion Percent Complete 80% $ 587,600 2. Compute cost per equivalent unit of production…arrow_forwardChristie's Co. manufactures cookies. The company has two departments, Mixing and Baking. For the Baking Department, material is added at the beginning of the process. Work happens evenly throughout the process, so Conversion Costs are added evenly to the product. Once mixing is complete, the cookies pieces are immediately transferred to the Baking Department. Once the baking is complete, the final product is transferred to Finished Goods Inventory. Data for the Baking Department is as follows: Units Transfer $ DirectMaterials $ % Complete Conv Costs % Complete Opening WIP 550 $3,500 $2,800 100% $2,100 30% New units & Costs 2,000 $12,300 $8,100 $14,000 Ending WIP 680 ??? 65% Calculate the physical and equivalent units for Transferred-In, Direct Materials and Conversion Costsarrow_forwardGladden Dock Company manufactures boat docks on an assembly line. Its costing system uses two cost categories, direct materials and conversion costs. Each product must pass through the Assembly Department and the Finishing Department. This problem focuses on the Assembly Department. Direct materials are added at the beginning of the production process. Conversion costs are allocated evenly throughout production. The firm uses FIFO method and the controller prepared the following (correct) equivalent unit calculation. Unitscompleted Physical Units Direct Materials Conversion WIP, beginning 70 0 52.5 Started and completed 30 30 30 WIP, ending 10 10 5 Totals 110 40 87.5 Cost per Equiv Unit $4,000 $16,000 Work in process, beginning inventory: Current Costs:Direct materials $140,000 Direct materials $ 160,000Conversion costs $260,000 Conversion…arrow_forward
- The Calgary Company is a food processing company based in Aberta. It operates under the weighted average method of process costing and has two departments: cleaning and cleaning department, conversion costs are added evenly during the process, and direct materials are added at the beginning of the process Spoiled units are detected upon insp and are disposed of at zero net disposal value. All completed work is transferred to the packaging department Summary data for May follow (Click the icon to Required For the deaning deg process Carry unit For each cost categ Enter the physical u Fl Work in process, be Started during cum To account for Completed and tran Normal spolage Abnormal spolage Work in process, ending Accounted for Data table The Calgary Company: Cleaning Dept. Work in process, beginning inventory (May 1) Degree of completion of beginning work in process Started during May Good units completed and transferred out during May Work in process, ending inventory (May 31) Degree…arrow_forwardQualCo manufactures a single product in two departments: Cutting and Assembly. Information for the Cutting department for May follows. Beginning work in process inventory Units started and completed Units completed and transferred out Ending work in process inventory Beginning work in process inventory Direct materials Conversion Costs added this period Direct materials Conversion Total costs to account for Equivalent units of production (EUP) Cost per equivalent unit of production + Equivalent units of production Cost per equivalent unit of production Cost assignment Beginning work in process To complete beginning work in process Direct materials Conversion Started and completed Direct materials Conversion Completed and transferred out Ending work in process Direct materials Conversion Total costs accounted for Units EUP Units 37,500 150,000 187,500 51, 250 Required: 1-3. Using the FIFO method, assign May's costs to the units transferred out and assign costs to its ending work in…arrow_forwardWhat is the total costs transferred to Department 2? What is the total costs transferred to the Storeroom?arrow_forward
- Vishnuarrow_forwardMuskoge Company uses a process-costing system. The company manufactures a product that isprocessed in two departments: Molding and Assembly. In the Molding Department, directmaterials are added at the beginning of the process; in the Assembly Department, additionaldirect materials are added at the end of the process. In both departments, conversion costs areincurred uniformly throughout the process. As work is completed, it is transferred out. Thefollowing table summarizes the production activity and costs for February: Molding AssemblyBeginning inventories: Physical units 10,000 8,000 Costs: Transferred in — $ 45,400 Direct materials $22,000 — Conversion costs $13,800 $ 16,700Current production: Units started 25,000 ? Units transferred out 30,000 35,000 Costs: Transferred in — ? Direct materials $ 56,250 $ 40,250 Conversion costs $103,500 $142,845 Percentage of completion: Beginning inventory 40% 55% Ending inventory 80 50Required:3. Using the FIFO method, prepare the following for…arrow_forwardManjiarrow_forward
- Devereaux Cycles makes three models of scooter: Commuter, Sport, and X-treme. The scooters are produced in four departments: Assembly, Detailing, Customization, and Packaging. All three models are started in Assembly, where all materials are assembled. The Commuter is then sent to Packaging, where it is packaged and transferred to finished goods inventory. The Sport is then transferred to Detailing. Once the detailing process is completed, the Sport models are transferred to Packaging and then finished goods. The X- Treme model is assembled and then transferred to Customization, and then Packaging. When packaged, it is transferred to finished goods. Data for February are shown in the following table. Conversion costs are allocated based on the number of units processed in each department. No work-in-process inventories are maintained in any department. Materials Conversion costs: Assembly Detailing Customization Packaging Total conversion costs Commuter Sport X-Treme Total $ 3,694,000…arrow_forwardPlease help. Thank you!arrow_forwardCampbell Electronics produces video games in three market categories: commercial, home, and miniature. Campbell has traditionally allocated overhead costs to the three products using the companywide allocation base of direct labor hours. The company recently implemented an ABC system when it installed computer-controlled assembly stations that rendered the traditional costing system ineffective. In implementing the ABC system, the company identified the following activity cost pools and cost drivers: Category Unit Batch Product Facility Additional data for each of the product lines follow: Direct materials cost Direct labor cost Number of labor hours Number of machine hours Number of production orders Research and development time Number of units. Square footage Required Total Pooled Cost $ 376,000 206,400 109,600 304,000 Type of Product a. Commercial a. Home a. Miniature Combined total b. Commercial b. Home b. Miniature Combined total Types of Costs Indirect labor wages, supplies,…arrow_forward
- AccountingAccountingISBN:9781337272094Author:WARREN, Carl S., Reeve, James M., Duchac, Jonathan E.Publisher:Cengage Learning,Accounting Information SystemsAccountingISBN:9781337619202Author:Hall, James A.Publisher:Cengage Learning,
- Horngren's Cost Accounting: A Managerial Emphasis...AccountingISBN:9780134475585Author:Srikant M. Datar, Madhav V. RajanPublisher:PEARSONIntermediate AccountingAccountingISBN:9781259722660Author:J. David Spiceland, Mark W. Nelson, Wayne M ThomasPublisher:McGraw-Hill EducationFinancial and Managerial AccountingAccountingISBN:9781259726705Author:John J Wild, Ken W. Shaw, Barbara Chiappetta Fundamental Accounting PrinciplesPublisher:McGraw-Hill Education
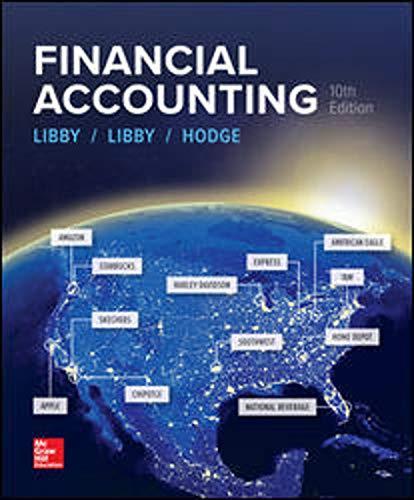
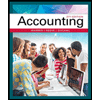
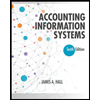
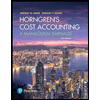
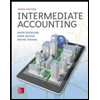
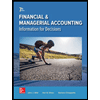