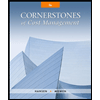
Cornerstones of Cost Management (Cornerstones Series)
4th Edition
ISBN: 9781305970663
Author: Don R. Hansen, Maryanne M. Mowen
Publisher: Cengage Learning
expand_more
expand_more
format_list_bulleted
Concept explainers
Topic Video
Question
Christie's Co. manufactures cookies. The company has two departments, Mixing and Baking. For the Baking Department, material is added at the beginning of the process. Work happens evenly throughout the process, so Conversion Costs are added evenly to the product. Once mixing is complete, the cookies pieces are immediately transferred to the Baking Department. Once the baking is complete, the final product is transferred to Finished Goods Inventory. Data for the Baking Department is as follows:
Units | Transfer $ | Direct Materials $ |
% Complete | Conv Costs | % Complete | |
Opening WIP | 550 | $3,500 | $2,800 | 100% | $2,100 | 30% |
New units & Costs | 2,000 | $12,300 | $8,100 | $14,000 | ||
Ending WIP | 680 | ??? | 65% |
Calculate the physical and equivalent units for Transferred-In, Direct Materials and Conversion Costs
Expert Solution

This question has been solved!
Explore an expertly crafted, step-by-step solution for a thorough understanding of key concepts.
This is a popular solution
Trending nowThis is a popular solution!
Step by stepSolved in 2 steps with 1 images

Knowledge Booster
Learn more about
Need a deep-dive on the concept behind this application? Look no further. Learn more about this topic, accounting and related others by exploring similar questions and additional content below.Similar questions
- Time Clock Shop manufactures clocks on an automated assembly line. It utilizes two cost categories: direct materials and conversion costs. Each product must pass through the Assembly Department and the Testing Department. Direct materials are added at the beginning of production, while conversion costs are allocated evenly throughout production. The company uses weighted-average costing. Data for the Assembly Department are given in the table. (Click the icon to view the table.) What is the total amount debited to the work-in-process account during the month of June at Time Clock Shop? A. $450,000 B. $2,270,000 C. $3,250,000 D. $2,000,000 E. $2,450,000 Table Work in process, beginning inventory Direct materials (100% complete) Conversion costs (50% complete) Units started during June Work in process, ending inventory Direct materials (100% complete) Conversion costs (75% complete) Work in process, beginning inventory Direct materials Conversion costs Direct materials costs added during…arrow_forwardDiamond Inc. manufactures jewelry. The company has two departments, Assembly and Polishing. For the Polishing Department, material is added when the process is 80% complete. Work happens evenly throughout the process, so Conversion Costs are added evenly to the product. Once assembly is complete, the jewelry pieces are immediately transferred to the Polishing Department. Once the polishing is complete, the final product is transferred to Finished Goods Inventory. Data for the Polishing Department is as follows: Equiv Units Ending Equiv Units Open WIP New Costs Transferred-In 200 60 $250 $15,050 Direct Materials 140 - $500 $1,500 Conversion Costs 182 42 $1,250 $4,000 Actual units Ending Inventory 60 Units Transferred out 140 Provide calculations in good form for the costs per equivalent units and the total cost reconciliation for the department. If Diamond…arrow_forwardZia Company makes flowerpots from recycled plastic in two departments, Molding and Packaging. Zia uses the weighted average method, and units completed in the Molding department are transferred to the Packaging department. Production unit Information for the Molding department follows. Molding-Direct Materials Beginning work in process inventory Units started this period Ending work in process inventory Production cost Information for the Molding department for the same period follows. Units Beginning work in process inventory (direct materials) Direct materials added this period 3,900 27,500 3,000 (b) Equivalent units of production (c) Cost per equivalent unit of production Percent Complete 70% QS 16-18 (Algo) Weighted average: Computing equivalent units and cost per EUP (direct materials) LO P1 80% Compute the Molding department's (a) units completed and transferred out, (b) equivalent units of production for direct materials, and c) cost per equivalent unit of production for direct…arrow_forward
- Muskoge Company uses a process-costing system. The companymanufactures a product that is processed in two departments: Moldingand Assembly. In the Molding Department, direct materials are added atthe beginning of the process; in the Assembly Department, additionaldirect materials are added at the end of the process. In both departments, conversion costs are incurred uniformly throughout theprocess. As work is completed, it is transferred out. The following tablesummarizes the production activity and costs for February: Required:1. Using the weighted average method, prepare the following forthe Molding Department: a. A physical flow scheduleb. An equivalent units calculationc. Calculation of unit costs. Round to four decimal places.d. Cost of ending work in process and cost of goods transferred out e. A cost reconciliation2. Prepare journal entries that show the flow of manufacturingcosts for the Molding Department. Materials are added at thebeginning of the process.3. Repeat…arrow_forwardHealthway uses a process-costing system to compute the unit costs of the minerals that it produces. It has three departments: Mixing, Tableting, and Bottling. In Mixing, at the beginning of the process all materials are added and the ingredients for the minerals are measured, sifted, and blended together. The mix is transferred out in gallon containers. The Tableting Department takes the powdered mix and places it in capsules. One gallon of powdered mix converts to 1,600 capsules. After the capsules are filled and polished, they are transferred to Bottling where they are placed in bottles, which are then affixed with a safety seal and a lid and labeled. Each bottle receives 50 capsules. During July, the following results are available for the first two departments (direct materials are added at the beginning in both departments): Overhead in both departments is applied as a percentage of direct labor costs. In the Mixing Department, overhead is 200 percent of direct labor. In the Tableting Department, the overhead rate is 150 percent of direct labor. Required: 1. Prepare a production report for the Mixing Department using the weighted average method. Follow the five steps outlined in the chapter. Round unit cost to three decimal places. 2. Prepare a production report for the Tableting Department. Materials are added at the beginning of the process. Follow the five steps outlined in the chapter. Round unit cost to four decimal places.arrow_forwardBenson Pharmaceuticals uses a process-costing system to compute the unit costs of the over-the-counter cold remedies that it produces. It has three departments: mixing, encapsulating, and bottling. In mixing, the ingredients for the cold capsules are measured, sifted, and blended (with materials assumed to be uniformly added throughout the process). The mix is transferred out in gallon containers. The encapsulating department takes the powdered mix and places it in capsules (which are necessarily added at the beginning of the process). One gallon of powdered mix converts into 1,500 capsules. After the capsules are filled and polished, they are transferred to bottling, where they are placed in bottles that are then affixed with a safety seal, lid, and label. Each bottle receives 50 capsules. During March, the following results are available for the first two departments: Overhead in both departments is applied as a percentage of direct labor costs. In the mixing department, overhead is 200% of direct labor. In the encapsulating department, the overhead rate is 150% of direct labor. Required: 1. Prepare a production report for the mixing department using the weighted average method. Follow the five steps outlined in the chapter. (Note: Round to two decimal places for the unit cost.) 2. Prepare a production report for the encapsulating department using the weighted average method. Follow the five steps outlined in the chapter. (Note: Round to four decimal places for the unit cost.) 3. CONCEPTUAL CONNECTION Explain why the weighted average method is easier to use than FIFO. Explain when weighted average will give about the same results as FIFO.arrow_forward
- Entries for materials cost flows in a process cost system The Hershey Company manufactures chocolate confectionery products. The three largest raw materials are cocoa, sugar, and dehydrated milk. These raw materials first go into the Blending Department. The blended product is then sent to the Molding Department, where the bars of candy are formed. The candy is then sent to the Packing Department, where the bars are wrapped and boxed. The boxed candy is then sent to the distribution center, where it is eventually sold to food brokers and retailers. Show the accounts debited and credited for each of the following business events: A. Materials used by the Blending Department B. Transfer of blended product to the Molding Department C. Transfer of chocolate to the Packing Department D. Transfer of boxed chocolate to the distribution center E. Sale of boxed chocolatearrow_forwardRameriz Company is a process manufacturer with two production departments, Blending and Filling. All direct materials are introduced in Blending from the materials store area. What is included in the cost transferred to Filling?arrow_forwardClassify each of the following departments in a factory that produces crme-filled snack cakes as a producing department or a support department. a. Janitorial b. Baking c. Inspection d. Mixing e. Engineering f. Grounds g. Purchasing h. Packaging i. Icing (frosts top of snack cakes and adds decorative squiggle) j. Filling (injects crme mixture into baked snack cakes) k. Personnel l. Cafeteria m. General factory n. Machine maintenance o. Bookkeepingarrow_forward
- Muskoge Company uses a process-costing system. The company manufactures a product that isprocessed in two departments: Molding and Assembly. In the Molding Department, directmaterials are added at the beginning of the process; in the Assembly Department, additionaldirect materials are added at the end of the process. In both departments, conversion costs areincurred uniformly throughout the process. As work is completed, it is transferred out. Thefollowing table summarizes the production activity and costs for February: Molding AssemblyBeginning inventories: Physical units 10,000 8,000 Costs: Transferred in — $ 45,400 Direct materials $22,000 — Conversion costs $13,800 $ 16,700Current production: Units started 25,000 ? Units transferred out 30,000 35,000 Costs: Transferred in — ? Direct materials $ 56,250 $ 40,250 Conversion costs $103,500 $142,845 Percentage of completion: Beginning inventory 40% 55% Ending inventory 80 50Required:3. Using the FIFO method, prepare the following for…arrow_forwardFast Company produces its product through two processing departments: Cutting and Assembly. Information for the Cutting department follows. Beginning work in process inventory Units started this period Units completed and transferred out Ending work in process inventory Beginning work in process inventory Direct materials Conversion Costs added this period Direct materials Conversion Total costs to account for Required 1 Required 2 Unit reconciliation: Units to account for: Units to account for Total units accounted for: Total units accounted for Equivalent units of production (EUP) Equivalent Units of Production Cost per equivalent unit of production Units Total costs + Equivalent units of production Cost per equivalent unit of production Cost Assignment Completed and transferred out Direct materials Conversion 30,000 140,000 150,000 20,000 Complete this question by entering your answers in the tabs below. Ending work in process Direct materials Conversion Required: 1. Prepare the…arrow_forwardWhiffle Company produces children's whiffle ball sets using a three-step sequential process that includes molding, coloring and finishing. When the sets are completely finished, out of which account should the cost be transferred? OA. WIP Inventory- Coloring OB. WIP Inventory-Molding OC. WIP Inventory - Finishing (...)arrow_forward
arrow_back_ios
SEE MORE QUESTIONS
arrow_forward_ios
Recommended textbooks for you
- Cornerstones of Cost Management (Cornerstones Ser...AccountingISBN:9781305970663Author:Don R. Hansen, Maryanne M. MowenPublisher:Cengage LearningManagerial Accounting: The Cornerstone of Busines...AccountingISBN:9781337115773Author:Maryanne M. Mowen, Don R. Hansen, Dan L. HeitgerPublisher:Cengage LearningManagerial AccountingAccountingISBN:9781337912020Author:Carl Warren, Ph.d. Cma William B. TaylerPublisher:South-Western College Pub
- Financial And Managerial AccountingAccountingISBN:9781337902663Author:WARREN, Carl S.Publisher:Cengage Learning,
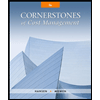
Cornerstones of Cost Management (Cornerstones Ser...
Accounting
ISBN:9781305970663
Author:Don R. Hansen, Maryanne M. Mowen
Publisher:Cengage Learning
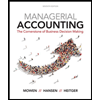
Managerial Accounting: The Cornerstone of Busines...
Accounting
ISBN:9781337115773
Author:Maryanne M. Mowen, Don R. Hansen, Dan L. Heitger
Publisher:Cengage Learning
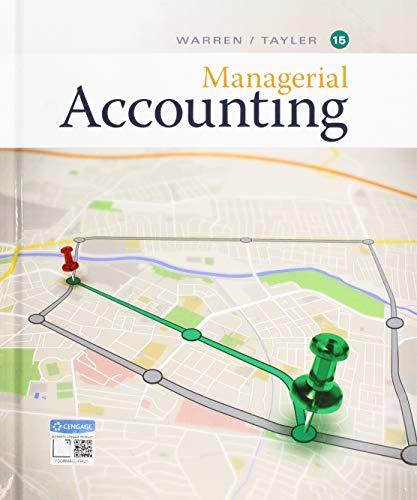
Managerial Accounting
Accounting
ISBN:9781337912020
Author:Carl Warren, Ph.d. Cma William B. Tayler
Publisher:South-Western College Pub
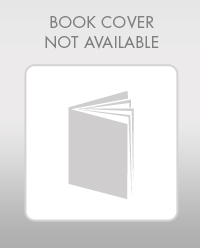
Financial And Managerial Accounting
Accounting
ISBN:9781337902663
Author:WARREN, Carl S.
Publisher:Cengage Learning,