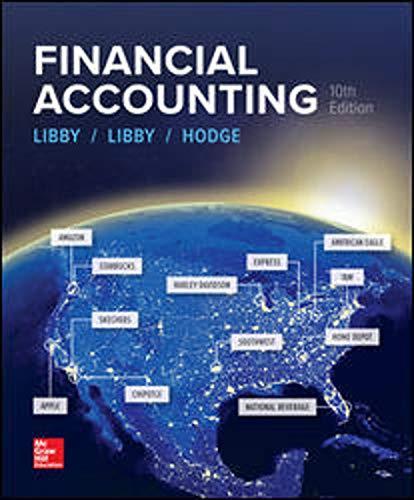
Concept explainers
Multiple Production Department Factory
Performance Gloves, Inc. produces three sizes of sports gloves: small, medium, and large. A glove pattern is first stenciled onto leather in the Pattern Department. The stenciled patterns are then sent to the Cut and Sew Department, where the glove is cut and sewed together. Performance Gloves uses the multiple production department factory overhead rate method of allocating
Pattern Department overhead | $93,500 | ||
Cut and Sew Department overhead | 153,300 | ||
Total | $246,800 |
The direct labor estimated for each production department was as follows:
Pattern Department | 1,700 | direct labor hours | |
Cut and Sew Department | 2,100 | ||
Total | 3,800 | direct labor hours |
Direct labor hours are used to allocate the production department overhead to the products. The direct labor hours per unit for each product for each production department were obtained from the engineering records as follows:
Production Departments | Small Glove | Medium Glove | Large Glove | |||
Pattern Department | 0.05 | 0.06 | 0.07 | |||
Cut and Sew Department | 0.07 | 0.09 | 0.11 | |||
Direct labor hours per unit | 0.12 | 0.15 | 0.18 |
If required, round all per unit answers to the nearest cent.
a. Determine the two production department factory overhead rates.
Pattern Department | $per dlh |
Cut and Sew Department | $per dlh |
b. Use the two production department factory overhead rates to determine the factory overhead per unit for each product.
Small glove | $ per unit |
Medium glove | $ per unit |
Large glove | $ per unit |

Trending nowThis is a popular solution!
Step by stepSolved in 2 steps with 4 images

- Multiple Production Department Factory Overhead Rate Method Handy Leather, Inc., produces three sizes of sports gloves: small, medium, and large. A glove pattern is first stenciled onto leather in the Pattern Department. The stenciled patterns are then sent to the Cut and Sew Department, where the glove is cut and sewed together. Handy Leather uses the multiple production department factory overhead rate method of allocating factory overhead costs. Its factor overhead costs were budgeted as follows: Pattern Department overhead Cut and Sew Department overhead Total The direct labor estimated for each production department was as follows: Pattern Department Cut and Sew Department Total Production Departments Pattern Department Cut and Sew Department Direct labor hours per unit Direct labor hours are used to allocate the production department overhead to the products. The direct labor hours per unit for each product for each production department were obtained from the engineering records…arrow_forwardAngle Max Industries produces a product which goes through two operations, Assembly and Finishing, before it is ready to be shipped. Next year's expected costs and activities are shown below. Direct labor hours Machine hours Overhead costs Multiple Choice Assume that the Assembly Department allocates overhead using a plantwide overhead rate based on machine hours. How much total overhead will be assigned to a product that requires 2 direct labor hour and 3.30 machine hours in the Assembly Department, and 4.50 direct labor hours and 0.4 machine hours in the Finishing Department? O$17.60. Assembly 180,000 DLH 380,000 MH $380,000 $20.40. Finishing 148,000 DLH 91, 200 MH $562, 400arrow_forwardRocky Mountain Corporation makes two types of hiking boots-Xactive and Pathbreaker. Data concerning these two product lines appear below: Direct materials per unit Direct labor cost per unit Direct labor-hours per unit Estimated annual production and sales Estimated total manufacturing overhead Estimated total direct labor-hours Activity Cost Pools and (Activity Measures) Supporting direct labor (direct labor-hours) Batch setups (setups) Product sustaining (number of products) General factory (machine-hours) Total manufacturing overhead cost The company has a conventional costing system in which manufacturing overhead is applied to units based on direct labor-hours. Data concerning manufacturing overhead and direct labor-hours for the upcoming year appear below: Req 1A Required: 1-a. Compute the predetermined overhead rate based on direct labor-hours. 1-b. Using the predetermined overhead rate and other data from the problem, determine the unit product cost of each product. 2. The…arrow_forward
- Activity Rates and Product Costs using Activity-Based Costing Lonsdale Inc. manufactures entry and dining room lighting fixtures. Five activities are used in manufacturing the fixtures. These activities and their associated budgeted activity costs and activity bases are as follows: Activity Casting Assembly Inspecting Setup Materials handling Activity Base Machine hours Direct labor hours Number of inspections Number of setups Number of loads Units produced Budgeted Activity Cost Activity Base Corporate records were obtained to estimate the amount c activity to be used by the two products. The estimated activity-base usage quantities and units produced follow: Entry Dining Total 5,440 4,830 10,270 4,680 7,030 11,710 1,870 590 2,460 270 810 10,800 Activity Casting Assembly Inspecting Setup Materials handling a. Determine the activity rate for each activity. If required, round the rate to the nearest dollar. Activity Rate $ $ $ $225,940 Machine hours 222,490 39,360 46,860 50,470 $ Direct…arrow_forwardVishnuarrow_forwardShow Me How Support department cost allocation- Martay Creations produces winter scarves. The scarves are produced in the Cutting and Sewing departments. The Maintenance and Security departments support these production departments, and allocate costs based on machine hours and square feet, respectively. Information about each department is provided in the following table: Department Maintenance Department Security Department Cutting Department Sewing Department Total Cost Number of Employees $2,200 5 4,500 3 21,200 21 24,900 19 Machine Hours 40 Square Feet 600 0 500 3,600 2,400 5,400 3,000 Using the sequential method and allocating the support department with the highest costs first, allocate all support department costs to the production departments. Then compute the total cost of each production department. Cutting Department Sewing Department Production departments' total costs $ Darrow_forward
- Activity-Based Product Costing Sweet Sugar Company manufactures three products (white sugar, brown sugar, and powdered sugar) in a continuous production process. Senior management has asked the controller to conduct an activity-based costing study. The controller identified the amount of factory overhead required by the critical activities of the organization as follows: Activity Budgeted Activity Cost Production $415,800 Setup 268,800 Inspection 131,200 Shipping 111,600 Customer service 93,800 Total $1,021,200 The activity bases identified for each activity are as follows: Activity Activity Base Production Machine hours Setup Number of setups Inspection Number of inspections Shipping Number of customer orders Customer service Number of customer service requests The activity-base usage quantities and units produced for the three products were determined from corporate records and are as follows: Machine Hours Number…arrow_forwardRequired information Greenwood Company manufactures two products-15,000 units of Product Y and 7,000 units of Product Z. The company uses a plantwide overhead rate based on direct labor-hours. It is considering implementing an activity-based costing (ABC) system that allocates all of its manufacturing overhead to four cost pools. The following additional information is available for the company as a whole and for Products Y and Z: Activity Cost Pool Machining Machine setups Production design General factory Activity Measure Machining Number of setups Number of products Direct labor-hours Activity Measure Machine-hours Number of setups Number of products Direct labor-hours Estimated Overhead Cost $ 227,700 $ 153,908 Product Y Product Z 8,700 60 1 8,700 2,300 210 1 1,300 Expected Activity 11,000 MHS 270 setups $ 91,000. $ 257,000 2 products 10,000 DLHS 14. Using the ABC system, what percentage of the Product Design cost is assigned to Product Y and Product Z? (Round your answers to 2…arrow_forwardCycle Time, Velocity, Product Costing Mulhall, Inc., has a JIT system in place. Each manufacturing cell is dedicated to the production of a single product or major subassembly. One cell, dedicated to the production of mopeds, has four operations: machining, finishing, assembly, and qualifying (testing). The machining process is automated, using computers. In this process, the model’s frame and engine are constructed. In finishing, the frame is sandblasted, buffed, and painted. In assembly, the frame and engine are assembled. Finally, each model is tested to ensure operational capability. For the coming year, the moped cell has the following budgeted costs and cell time (both at theoretical capacity): Budgeted conversion costs $5,541,120 Budgeted materials $18,668,000 Cell time 35,520 Theoretical output 17,760 models During the year, the following actual results were obtained: Actual conversion costs $5,541,120 Actual materials $4,009,000 Actual cell time…arrow_forward
- AccountingAccountingISBN:9781337272094Author:WARREN, Carl S., Reeve, James M., Duchac, Jonathan E.Publisher:Cengage Learning,Accounting Information SystemsAccountingISBN:9781337619202Author:Hall, James A.Publisher:Cengage Learning,
- Horngren's Cost Accounting: A Managerial Emphasis...AccountingISBN:9780134475585Author:Srikant M. Datar, Madhav V. RajanPublisher:PEARSONIntermediate AccountingAccountingISBN:9781259722660Author:J. David Spiceland, Mark W. Nelson, Wayne M ThomasPublisher:McGraw-Hill EducationFinancial and Managerial AccountingAccountingISBN:9781259726705Author:John J Wild, Ken W. Shaw, Barbara Chiappetta Fundamental Accounting PrinciplesPublisher:McGraw-Hill Education
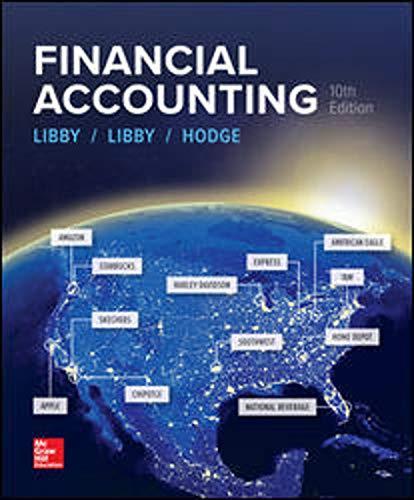
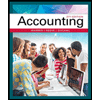
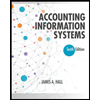
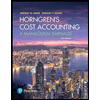
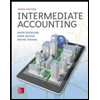
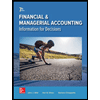