Lauder Company manufactures and distributes various fixtures used primarily in new building construction. At the company's Bayside plant, Lauder produces two models of one widely used fixture designated by model names LC-20 and LC-50. Currently, the Bayside plant uses direct labor-hours to allocate manufacturing overhead costs to products. The vice president-manufacturing (VP-M) at Lauder has recently been considering updates to the company's costing systems as a way to ensure that managers had the best information available for decision making. However, rather than update throughout the entire firm, the VP-M and CFO agreed to test an ABC system. Because of its size and focus, the Bayside plant was selected for the experiment. An ABC study team, consisting of both plant and corporate employees was formed to propose an ABC system and compare the product costs with those reported by the current system. Based on the experiment, the executives at Lauder will decide whether to roll out the new cost system to the entire company. The study team identified four cost pools into which the manufacturing overhead costs could be grouped. There was a great deal of discussion about both the pools and the cost drivers. The final system selected consisted of the following pools and drivers. The costs were based on the forecasts for the coming year. Cost Pools Material inspection Assembly Equipment setup. Packaging and shipping. Costs $ 696,960 3,889,600 1,390,400 739,200 Activity Drivers Direct material cost Machine-hours Production runs Units shipped Data for production of the two products at the Bayside plant for the coming year of operations follows: Total direct material costs Total direct labor costs Products LC-20 LC-50 $ 950,400 $ 316,800 $ 739,200 162,140 132 422,400 $ 369,600 80,960 88 105,600 Total machine-hours Total number of production runs Number of units produced and shipped All direct labor at the Bayside plant is paid $35 per hour.
Process Costing
Process costing is a sort of operation costing which is employed to determine the value of a product at each process or stage of producing process, applicable where goods produced from a series of continuous operations or procedure.
Job Costing
Job costing is adhesive costs of each and every job involved in the production processes. It is an accounting measure. It is a method which determines the cost of specific jobs, which are performed according to the consumer’s specifications. Job costing is possible only in businesses where the production is done as per the customer’s requirement. For example, some customers order to manufacture furniture as per their needs.
ABC Costing
Cost Accounting is a form of managerial accounting that helps the company in assessing the total variable cost so as to compute the cost of production. Cost accounting is generally used by the management so as to ensure better decision-making. In comparison to financial accounting, cost accounting has to follow a set standard ad can be used flexibly by the management as per their needs. The types of Cost Accounting include – Lean Accounting, Standard Costing, Marginal Costing and Activity Based Costing.


Trending now
This is a popular solution!
Step by step
Solved in 3 steps

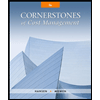
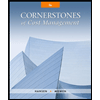