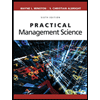
Practical Management Science
6th Edition
ISBN: 9781337406659
Author: WINSTON, Wayne L.
Publisher: Cengage,
expand_more
expand_more
format_list_bulleted
Question
Mr. Tony Stark is the owner of a soy sauce factory located in Padang Besar, Perlis. His annual soy sauce production is 48,000 bottles at the moment. His production process data are as follows:
Item |
Data |
1) Production days |
280 days per year |
2) Equipment working capacity |
50 % |
3) Staffs working capacity |
50 % |
4) Number of production batches per year |
48 batches |
Mr. Tony Stark intended to increase his kicap production by double the volume within this year. Based on all of the data given, suggest how he can achieve this targeted production without spending any extra money on the production cost?
Expert Solution

This question has been solved!
Explore an expertly crafted, step-by-step solution for a thorough understanding of key concepts.
Step by stepSolved in 2 steps

Knowledge Booster
Similar questions
- Home Country as Largest Production Country Monstansa is Yellowstone’s most important location. It is where the company was founded in 1949, it is the location of the headquarters and it is also Yellowstone’s biggest manufacturing site. More than one third of all Yellowstone products are produced in Monstansa (577,000 products in 2013). It has all the major components of manufacturing production process: a farm, an agro processing facility, an assembly line and even a label print shop. The factory builds some of the company’s most important products (A3, A4, A5 and Q5). For many of the products, Monstansa serves almost as a world market factory, supplying most countries with their respective products, and having a high level of value added for these lines. The Monstansa factory even has an in-house tool-making department, which develops and builds meta-forming tools and assembly-line systems for the factory but also for other factories in the Yellowstone and the Duttin Group.…arrow_forwardComplete the MPS record below for a single item. (Enter your responses as integers. A response of "0" is equivalent to being not applicable.) Item: A Quantity on Hand: 80 Forecast Customer orders (booked) Projected on-hand inventory MPS quantity 1 70 40 ☐☐ January 2 70 65 80 Order Policy: 100 units Lead Time: 1 week February Week 4 40 0 5 45 35 50 70 45 0 8 50 0arrow_forwardWrite an essay titled "Here, There, and Everywhere" on the construction and hardware supply company FOUR ACES.arrow_forward
- a) GOT7 Soda Pop, Inc., has a new fruits drink. The production planner has assembled the following cost data and demand forecast as follow: [GOT7 Soda Pop, Inc., mempunyai minuman buah-buahan yang baru, Perancang pengeluaran telah mengumpul data tentang kos dan ramalan permintaan seperti berikut:] Quarter Demand 1,800 First Second 1,200 Third 1,600 Fourth 1,300 Table 1: Cost and demand forecast [Jadual 1: Kos dan ramalan permintaan] Previous quater's output 1,300 cases Beginning inventory 0 cases Stockout cost Inventory holding cost Hiring employees Terminating employees Subcontracting cost Unit cost on regular time Overtime cost RM150 RM40 per case at the end of quater RM40 per case RM80 per case RM60 per case RM30 per case RM15 extra per case You as the production planner need to develop an aggregate planning. You are required to: [Anda sebagai perancang pengeluaran perlu membangunkan perancangan agregat Anda dikehendaki untuk:] i) Assess plan A: strategy that hires and fires…arrow_forwardPrevar Corporation currently purchases components from one of its suppliers. The current purchase price is $1500 per component, with annual purchase volume of 750 units. The ops manager believes that this component could be made inhouse with some minor modifications to the current factory set up. Fixed cost for dedicating a line for this component is estimated at $50,000. Raw materials for the component is estimated at $900, overhead at $200 and it would take 10 hours of labor (at $20 per hour) to produce each component.arrow_forwardRipeka, the warehouse manager at Hine would like to update the company’s inventory locator system so that the picking operation can be streamlined. While conceptually simple to do, she knows that there will be several steps to the update process that will have to be carefully managed. She needs to complete upgrade and train her staff in operating the new system before the busy season, which is only 4 months away. She identifies the various activities, expected time duration, predecessors and costs, as shown in the table. Draw the AON Network, and then determine the critical path. [Show your workings, using the grid network.] Identify the project duration – is this project feasible within the required timeframe?arrow_forward
- Vartan Information Technologies has a division called Useless Transistors. It is considering an « overhaul » of Useless Transistors’ operations or moving Useless overseas. Inventory management is receiving considerable attention. Vartan collected data for the years 2014, 2015, and a forecast for 2016. This data is provided below. What would be Useless Transistors’ weeks of supply for 2015? Projected 2014 2015 2016 Sales $127,890,000 $148,900,000 $192,340,000 Beginning Inventory $3,897,234 $5,467,983 $6,183,230 Ending Inventory $5,467,983 $6,183,230 $4,654,129 Cost of Goods Sold $16,876,400 $20,376,548 $22,346,786 Group of answer choicesarrow_forwardSapphire Aerospace operates 52 weeks per year, and its costof goods sold last year was $6,500,000. The firm carries eightitems in inventory: four raw materials, two work-in-processitems, and two finished goods. Table 12.3 shows last year’saverage inventory levels for these items, along with their unitvalues.a. What is the average aggregate inventory value?b. How many weeks of supply does the firm have?c. What was the inventory turnover last year?arrow_forwardProduction data show 35,920 units were transferred out of a stage of production and 6,150 units remained in ending WIP inventory that was 100% complete to material and 35% complete to conversion. The unit material cost is $5 for material and $8 for conversion. What is the amount of inventory transferred out and remaining in ending work in process inventory? Round to the whole unit and whole dollar, no decimals. Complete the tables below: Equivalent units data Units Materials Conversion Transferred out 35,920 Ending inventory 6,150 Units accounted for, equivalent units Cost data Transferred out $ Ending work in process: materials Ending work in process: conversion Ending work in process: total Costs to account for $ please fill in the information in the grid exactly as providedarrow_forward
- Qty Standard Labor Hour Raw Material В Standard Labor 2 Hours Raw Material INDEPENDENT DEMAND Period 1 2 3 4 5 6 Total Product A 1,000 1,000 1,000 1,000 1,000 1,000 6,000 Product B 500 500 ,500 500 16. Products A and B are produced on two different dedicated production lines. If both lines work on the same shift schedule, the ratio of workers on line A to workers on line B is A. 2:1 В. 2:3 С. 2:5 D. 4:1arrow_forwardSupplier Raw Materials Inventory Management Production Question related to the diagram: Quality Control Packaging Finished Goods Distribution Retail Customer The process starts from the supplier, goes through raw materials, inventory management, production, quality control, packaging, finished goods, distribution, retail, and finally reaches the customer. How does the 'Inventory Management' stage interact with the 'Production' stage, and what strategies can be implemented to optimize this interaction?arrow_forward10arrow_forward
arrow_back_ios
arrow_forward_ios
Recommended textbooks for you
- Practical Management ScienceOperations ManagementISBN:9781337406659Author:WINSTON, Wayne L.Publisher:Cengage,Operations ManagementOperations ManagementISBN:9781259667473Author:William J StevensonPublisher:McGraw-Hill EducationOperations and Supply Chain Management (Mcgraw-hi...Operations ManagementISBN:9781259666100Author:F. Robert Jacobs, Richard B ChasePublisher:McGraw-Hill Education
- Purchasing and Supply Chain ManagementOperations ManagementISBN:9781285869681Author:Robert M. Monczka, Robert B. Handfield, Larry C. Giunipero, James L. PattersonPublisher:Cengage LearningProduction and Operations Analysis, Seventh Editi...Operations ManagementISBN:9781478623069Author:Steven Nahmias, Tava Lennon OlsenPublisher:Waveland Press, Inc.
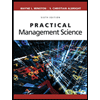
Practical Management Science
Operations Management
ISBN:9781337406659
Author:WINSTON, Wayne L.
Publisher:Cengage,
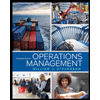
Operations Management
Operations Management
ISBN:9781259667473
Author:William J Stevenson
Publisher:McGraw-Hill Education
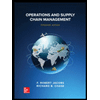
Operations and Supply Chain Management (Mcgraw-hi...
Operations Management
ISBN:9781259666100
Author:F. Robert Jacobs, Richard B Chase
Publisher:McGraw-Hill Education
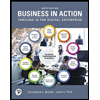
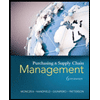
Purchasing and Supply Chain Management
Operations Management
ISBN:9781285869681
Author:Robert M. Monczka, Robert B. Handfield, Larry C. Giunipero, James L. Patterson
Publisher:Cengage Learning
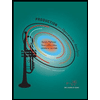
Production and Operations Analysis, Seventh Editi...
Operations Management
ISBN:9781478623069
Author:Steven Nahmias, Tava Lennon Olsen
Publisher:Waveland Press, Inc.