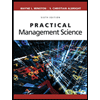
Practical Management Science
6th Edition
ISBN: 9781337406659
Author: WINSTON, Wayne L.
Publisher: Cengage,
expand_more
expand_more
format_list_bulleted
Concept explainers
Topic Video
Question
Production data show 35,920 units were transferred out of a stage of production and 6,150 units remained in ending WIP inventory that was 100% complete to material and 35% complete to conversion. The unit material cost is $5 for material and $8 for conversion. What is the amount of inventory transferred out and remaining in ending work in process inventory? Round to the whole unit and whole dollar, no decimals.
Complete the tables below:
Equivalent units data
Units | Materials | Conversion | |
---|---|---|---|
Transferred out | 35,920 | ||
Ending inventory | 6,150 | ||
Units accounted for, equivalent units |
Cost data
Transferred out | $ | |
---|---|---|
Ending work in process: materials | ||
Ending work in process: conversion | ||
Ending work in process: total | ||
Costs to account for | $ |
please fill in the blank boxes
Expert Solution

This question has been solved!
Explore an expertly crafted, step-by-step solution for a thorough understanding of key concepts.
This is a popular solution
Trending nowThis is a popular solution!
Step by stepSolved in 3 steps

Knowledge Booster
Learn more about
Need a deep-dive on the concept behind this application? Look no further. Learn more about this topic, operations-management and related others by exploring similar questions and additional content below.Similar questions
- Terminator, Inc., manufactures a motorcycle part in lots of 300 units. The raw materials cost for the part is $170, and the value added in manufacturing 1 unit from its components is $320, for a total cost per completed unit of $490. The lead time to make the part is 4 weeks, and the annual demand is 4,200 units. Assume 50 working weeks per year. a. How many units of the part are held, on average, as cycle inventory? units. (Enter your response as an integer.)arrow_forwardAssume you are the manager of a shop that assembles power tools. You have just received an order for 55 chain saws, which are to be shipped at the start of week 8. Pertinent information on the saws follows: Item Lead Time (weeks) On Hand Saw A B C D E F 2 1 2 2 1 1 2 Gross requirements Scheduled receipts Projected on hand Net requirements Planned order receipt Planned order release Ĉ E(3) & E(2) LT = 1 week Lot size: Lot-for-Lot 15 10 5 65 20 10 30 Skip Extension Tip: Double click to open in new tab Show Transcribed Text Develop the material requirements plan for component E using lot-for-lot ordering for all items. (Leave no cells blank - be certain to enter "0" wherever required.) Components A(2), B(1), C(4) E(3), D(1) D (2), F(3) E(2), D (2) Beg. Inv. 1 2 3 190 5 210 6arrow_forwardplease answer withinin 30 minutes.arrow_forward
- Which of the following is the planned order receipts using an MRP program with lot-for-lot policy if the inventory on hand is 0, scheduled receipts are 150, and gross requirements are 200? Now what about if the policy is EOQ = 500?arrow_forwardHi, I need help solving this Operations Mgmt. problem. Thanks!arrow_forwardProduction Company Universal Controlsmanufactures control units. Their new models areeI Argon I and eI Argon II. To make each unit ofArgon I, use 6 meters and 3 controllers. For fa-craft each unit of Argon II, they use 10 meters and Scontrollers. The company receives a total of 760 me-managers and daily controllers of their suppliers.How many units of each model can you produce?seriously? Assume that all parts are used. Note: Solve freely # OF ARGON UNITS I # OF ARGON UNITS IIarrow_forward
- Complete the MPS record below for a single item. (Enter your responses as integers. A response of "0" is equivalent to being not applicable.) Item: A Quantity on Hand: 80 Forecast Customer orders (booked) Projected on-hand inventory MPS quantity 1 70 40 ☐☐ January 2 70 65 80 Order Policy: 100 units Lead Time: 1 week February Week 4 40 0 5 45 35 50 70 45 0 8 50 0arrow_forwardExplain how is ordering in small lot sizes essential for just in time implementation and what benefi are epected to be achieved ?arrow_forwardGiven the following information a bout a product atMichael Gibson's firm, what is the appropriate setup time?Annual demand = 39,000 unitsDaily demand = 150 unitsDaily production = 1,000 unitsDesired lot size = 150 unitsHolding cost per unit per year = $10Setup labor cost per hour = $40arrow_forward
- ⢠1An advantage of a make-to-stock process is which of the following? o It responds directly to customer orderso It allows the firm to avoid inventory costso Rapid delivery of a standard producto All units of output are uniqueCorrect⢠2According to Littleâs law, which of the following can be used to estimate inventory?o Set up time times throughput rateo Process time times cycle timeo Process velocity times flow timeo Throughput rate times flow timeCorrect⢠3Which of the following is a principle of reengineering? o Integrate the outcomes of parallel activitieso Organize around the taskso Treat geographically dispersed resources as though they were centralizedo Capture information many times, at the source and where it is interpretedCorrect⢠4Which of the following is one of the major types of stakeholders impacted by most consulting projects?o International government regulatorso Other consultantso…arrow_forwardRick Wing has a repetitive manufacturing plant producing automobile steering wheels. Use the following data to prepare for a reduced lot size. The firm uses a work year of 300 days. Setup labor cost Annual holding cost Daily production (8 hours) Annual demand for steering wheels Desired lot size (2 hours of production) $60.00 per hour $19 per unit 1,040 units/day 33,000 (300 days x daily demand of 110 units) Q = 260 units a) Setup cost = $ b) Setup time = (round your response to two decimal places). minutes (round your response to two decimal places).arrow_forwardB15. The restaurant uses 24 bottles of wine to operate and it has 3 bottles in hand. Calculate the Desired Ending Inventory (DEl) if the number of days in the delivery period is 2 and the safety factor is 10%. Using the Periodic Order Method, calculate the number of bottles that the restaurant should order.arrow_forward
arrow_back_ios
SEE MORE QUESTIONS
arrow_forward_ios
Recommended textbooks for you
- Practical Management ScienceOperations ManagementISBN:9781337406659Author:WINSTON, Wayne L.Publisher:Cengage,Operations ManagementOperations ManagementISBN:9781259667473Author:William J StevensonPublisher:McGraw-Hill EducationOperations and Supply Chain Management (Mcgraw-hi...Operations ManagementISBN:9781259666100Author:F. Robert Jacobs, Richard B ChasePublisher:McGraw-Hill Education
- Purchasing and Supply Chain ManagementOperations ManagementISBN:9781285869681Author:Robert M. Monczka, Robert B. Handfield, Larry C. Giunipero, James L. PattersonPublisher:Cengage LearningProduction and Operations Analysis, Seventh Editi...Operations ManagementISBN:9781478623069Author:Steven Nahmias, Tava Lennon OlsenPublisher:Waveland Press, Inc.
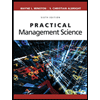
Practical Management Science
Operations Management
ISBN:9781337406659
Author:WINSTON, Wayne L.
Publisher:Cengage,
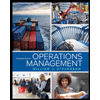
Operations Management
Operations Management
ISBN:9781259667473
Author:William J Stevenson
Publisher:McGraw-Hill Education
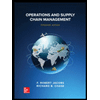
Operations and Supply Chain Management (Mcgraw-hi...
Operations Management
ISBN:9781259666100
Author:F. Robert Jacobs, Richard B Chase
Publisher:McGraw-Hill Education
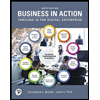
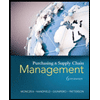
Purchasing and Supply Chain Management
Operations Management
ISBN:9781285869681
Author:Robert M. Monczka, Robert B. Handfield, Larry C. Giunipero, James L. Patterson
Publisher:Cengage Learning
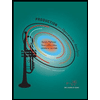
Production and Operations Analysis, Seventh Editi...
Operations Management
ISBN:9781478623069
Author:Steven Nahmias, Tava Lennon Olsen
Publisher:Waveland Press, Inc.