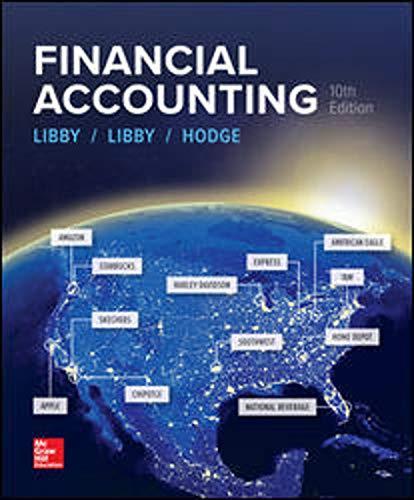
FINANCIAL ACCOUNTING
10th Edition
ISBN: 9781259964947
Author: Libby
Publisher: MCG
expand_more
expand_more
format_list_bulleted
Question
Dawson Company manufactures small table lamps and desk lamps. The following shows the activities per product and the total
Line Item Description | Units | Setups | Inspections | Assembly (dlh) |
---|---|---|---|---|
Small table lamps | 4,000 | 3,500 | 9,450 | 45,600 |
Desk lamps | 8,100 | 7,000 | 15,750 | 45,600 |
Activity | Total Activity-Base Usage | Budgeted Activity Cost |
---|---|---|
Setups | 10,500 | $95,550 |
Inspections | 25,200 | 168,840 |
Assembly (dlh) | 79,800 | 255,360 |
The total factory overhead to be allocated to desk lamps is
a. $315,145
b. $409,689
c. $567,261
d. $189,087
SAVE
AI-Generated Solution
info
AI-generated content may present inaccurate or offensive content that does not represent bartleby’s views.
Unlock instant AI solutions
Tap the button
to generate a solution
to generate a solution
Click the button to generate
a solution
a solution
Knowledge Booster
Similar questions
- Dawson Company manufactures small table lamps and desk lamps. The following shows the activities per product and the total overhead information: Units Setups Inspections Assembly (dlh) 2,700 4,000 8,000 8,000 Small table lamps Desk lamps Activity Setups 9,150 15,250 44,400 44,400 Total Activity-Base Usage Budgeted Activity Cost 12,000 $102,000 24,400 129,320 77,700 310,800 Inspections Assembly (dlh) The total factory overhead to be allocated to desk lamps is Oa. $456,995 Ob. $228,498 Oc. $587,565 Od. $326,425arrow_forwardRiverbed Manufacturing has five activity cost pools and two products (a budget tape vacuum and a deluxe tape vacuum). Information is presented below: Activity Cost Pools Ordering and Receiving Machine Setup Machining Assembly Inspection Budget $ Cost Driver Orders Setups Machine hours Deluxe $ Parts Inspections Overhead cost per unit Est. Overhead $144,000 311,400 1,023,000 1,624,000 314,000 per unit Est. Use of Cost Drivers Budget per unit 600 500 150,000 1.200,000 550 Deluxe 400 Compute the overhead cost per unit for each product. Production is 700.000 units of Budget and 200.000 units of Deluxe. (Round per machine hour and per part values to 3 decimal places, eg 52.711. Round overhead cost per unit to 2 decimal places, e.g. 12.25 and cost assigned to 0 decimal places, eg. 2,500.) 400 100,000 800,000 450arrow_forwardThe following table presents the activities and activity drivers that LampPlus uses in manufacturing Product 1 and Product 2. Complete the table: Activity Design Preparation Machining Finishing Inspection Packaging Shipping Cost Activity Driver $ 39,060 Design time $ 67,650 Labor hours 105,200 Machine hours $ Batches Units Orders $ 12,720 Packages Driver Usage Prod. 1 840 3,130 209 76 Prod. 2 1,330 hours hours 300 56 Activity Rate $ $ $ $ /hour /hour 20 /hour 50 /batch 17 /unit 302 /order /package Activity Cost:Prod. 1 $ $ $ $ 34,430 31,200 Activity Cost:Prod. 2 9,690 $ 12,986 $ 19,720 3,600arrow_forward
- Paparo Corporation has provided the following data from its activity-based costing system: Total Cost $1,005,000 Activity Cost Pool Assembly Processing orders Inspection Data concerning the company's product Q79Y appear below: Annual unit production and sales Annual machine-hours Annual number of orders Annual inspection hours Direct materials cost Direct labor cost Multiple Choice $168.52 per unit Total Activity 60,000 machine-hours 2,200 orders $ 83,930 $ 106,960 1,400 inspection-hours According to the activity-based costing system, the average cost of product Q79Y is closest to: $96.25 per unit $131.30 per unit O $151.15 per unit 350 1,100 100 40 $55.00 per unit $41.25 per unitarrow_forwardA company has provided the following data from its activity-based costing system: Activity Cost Pool Total Cost Total Activity Assembly Processing orders $70,578.60 $1,586,690 66,500 machine-hours 2,370 orders Inspection $124,500 1,660 inspection- hours The company makes 600 units of product A a year, requiring a total of 2,030 machine- hours, 108 orders, and 33 inspection-hours per year. The product's direct materials cost is $52.59 per unit and its direct labor cost is $19.32 per unit. The product sells for $175.60 per unit. According to the activity-based costing system, the product margin for product A is: (Round your intermediate calculations to 2 decimal places.) Multiple Choice $10,561.96 $8.086.96 $11,303.20 $62.214.00arrow_forwardActivity Base Entry Dining Total Machine hours 5,320 4,710 10,030 Direct labor hours 4,570 6,860 11,430 Number of inspections 1,940 610 2,550 Number of setups 310 70 380 Number of loads 700 190 890 Units produced 10,600 5,300 15,900 a. Determine the activity rate for each activity. If required, round the rate to the nearest dollar. Activity Activity Rate Casting per machine hour Assembly per direct labor hour Inspecting 24 per inspection Setup per setup Materials handling per load b. Use the activity rates in (a) to determine the total and per-unit activity costs associated with each product. Round the per unit amounts to the nearest cent. Product Total Activity Cost Activity Cost Per Unit Entry Lighting Fixtures Dining Room Lighting Fixturesarrow_forward
- Everlast Co. manufactures a variety of drill bits. The company's plant is partially automated. The budget for the year includes $432,000 payroll for 4,800 direct labor-hours. Listed below is cost driver information used in the product-costing system: Overhead Cost Pool Budgeted Overhead Cost Driver Estimated Cost Driver Level Machine setups $ 120,000 # of setups 120 setups Materials handling 104,400 # of barrels 8,700 barrels Quality control 264,000 # of inspections 1,100 inspections Other overhead cost 144,000 # of machine hours 12,000 machine hours Total overhead $ 632,400 A current product order has the following requirements: Machine setups 8 setups Materials handling 606 barrels Quality inspections 80 inspections Machine hours 830 machine hours Direct labor hour 336 hours What is the total manufacturing overhead for the current product order if the firm uses a plantwide rate based on direct…arrow_forwardActivity Rates and Product Costs using Activity-Based Costing Garfield Inc. manufactures entry and dining room lighting fixtures. Five activities are used in manufacturing the fixtures. These activities and their associated budgeted activity costs and activity bases are as follows: Activity BudgetedActivity Cost Activity Base Casting $560,000 Machine hours Assembly 75,000 Direct labor hours Inspecting 30,000 Number of inspections Setup 18,750 Number of setups Materials handling 14,000 Number of loads Corporate records were obtained to estimate the amount of activity to be used by the two products. The estimated activity-base usage quantities and units produced follow: Activity Base Entry Dining Total Machine hours 7,500 12,500 20,000 Direct labor hours 2,000 3,000 5,000 Number of inspections 500 250 750 Number of setups 150 100 250 Number of loads 400 300 700 Units produced 5,000 2,500 7,500 a.…arrow_forwardMack Precision Tool and Die has two production departments, Fabricating and Finishing, and two service departments, Repair and Quality Control. Direct costs for each department and the proportion of service costs used by the various departments for the month of March follow: Department Fabricating Finishing Repair Quality Control From: Direct Costs Repair $ 147,600 Service department costs Repair Quality control Total 112, 200 48,300 140, 210 $ Repair 8 0.3 0 $ Proportion of Services Used by Quality Control Fabricating Required: Use the reciprocal method to allocate the service costs. (Matrix algebra is not required.) Note: Amounts to be deducted should be indicated by a minus sign. Do not round Intermediate calculations. Round your final answers to the nearest whole dollar amounts. 0.3 Cost Allocation To: Quality Control 0.5 8.2 Fabricating $ Finishing 0.2 0.5 0 $ Finishingarrow_forward
- Mack Precision Tool and Die has two production departments, Fabricating and Finishing, and two service departments, Repair and Quality Control. Direct costs for each department and the proportion of service costs used by the various departments for the month of March follow: Department Fabricating Finishing Repair Quality Control From: Service department costs Repair Quality control Total Direct Costs Repair $ 132,600 94,200 40,200 242,740 Proportion of Services Used by Quality Control 0 0.3 Repair 0.3 0 Fabricating Finishing Required: Use the reciprocal method to allocate the service costs. (Matrix algebra is not required.) Note: Amounts to be deducted should be indicated by a minus sign. Do not round intermediate calculations. Round your final answers to the nearest whole dollar amounts. Quality Control Cost Allocation To: 0.5 0.1 0.2 0.6 Fabricating Finishingarrow_forwardplease answer within the format by providing formula the detailed workingPlease provide answer in text (Without image)Please provide answer in text (Without image)Please provide answer in text (Without image)arrow_forwardSilven Company has identified the following overhead activities, costs, and activity drivers for the coming year: Activity Expected Cost Activity Driver Activity Capacity $138,000 Number of setups 10,200 Number of orders 92,400 Machine hours 18,480 Receiving hours phones with the following expected activity demands: Setting up equipment Ordering materials Machining Receiving Silven produces two models of cell Model X 5,000 80 200 6,600 385 Units completed Number of setups Number of orders Machine hours Receiving hours Required: Model Y 10,000 40 400 4,950 770 120 600 11,550 1,155arrow_forward
arrow_back_ios
SEE MORE QUESTIONS
arrow_forward_ios
Recommended textbooks for you
- AccountingAccountingISBN:9781337272094Author:WARREN, Carl S., Reeve, James M., Duchac, Jonathan E.Publisher:Cengage Learning,Accounting Information SystemsAccountingISBN:9781337619202Author:Hall, James A.Publisher:Cengage Learning,
- Horngren's Cost Accounting: A Managerial Emphasis...AccountingISBN:9780134475585Author:Srikant M. Datar, Madhav V. RajanPublisher:PEARSONIntermediate AccountingAccountingISBN:9781259722660Author:J. David Spiceland, Mark W. Nelson, Wayne M ThomasPublisher:McGraw-Hill EducationFinancial and Managerial AccountingAccountingISBN:9781259726705Author:John J Wild, Ken W. Shaw, Barbara Chiappetta Fundamental Accounting PrinciplesPublisher:McGraw-Hill Education
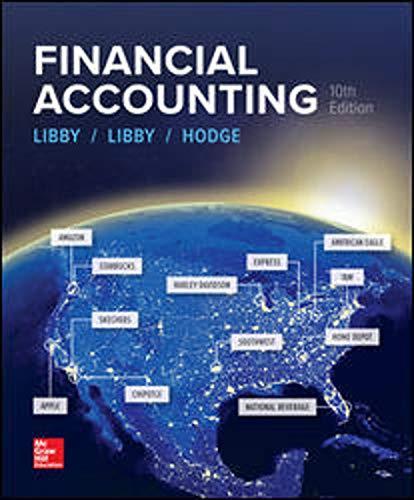
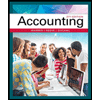
Accounting
Accounting
ISBN:9781337272094
Author:WARREN, Carl S., Reeve, James M., Duchac, Jonathan E.
Publisher:Cengage Learning,
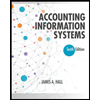
Accounting Information Systems
Accounting
ISBN:9781337619202
Author:Hall, James A.
Publisher:Cengage Learning,
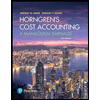
Horngren's Cost Accounting: A Managerial Emphasis...
Accounting
ISBN:9780134475585
Author:Srikant M. Datar, Madhav V. Rajan
Publisher:PEARSON
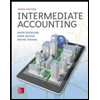
Intermediate Accounting
Accounting
ISBN:9781259722660
Author:J. David Spiceland, Mark W. Nelson, Wayne M Thomas
Publisher:McGraw-Hill Education
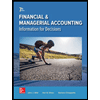
Financial and Managerial Accounting
Accounting
ISBN:9781259726705
Author:John J Wild, Ken W. Shaw, Barbara Chiappetta Fundamental Accounting Principles
Publisher:McGraw-Hill Education