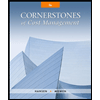
Cornerstones of Cost Management (Cornerstones Series)
4th Edition
ISBN: 9781305970663
Author: Don R. Hansen, Maryanne M. Mowen
Publisher: Cengage Learning
expand_more
expand_more
format_list_bulleted
Question
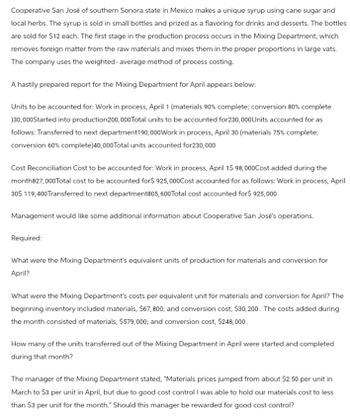
Transcribed Image Text:Cooperative San José of southern Sonora state in Mexico makes a unique syrup using cane sugar and
local herbs. The syrup is sold in small bottles and prized as a flavoring for drinks and desserts. The bottles
are sold for $12 each. The first stage in the production process occurs in the Mixing Department, which
removes foreign matter from the raw materials and mixes them in the proper proportions in large vats.
The company uses the weighted average method of process costing.
A hastily prepared report for the Mixing Department for April appears below:
Units to be accounted for: Work in process, April 1 (materials 90% complete; conversion 80% complete
)30,000Started into production200,000 Total units to be accounted for230,000 Units accounted for as
follows: Transferred to next department190,000 Work in process, April 30 (materials 75% complete;
conversion 60% complete)40,000 Total units accounted for230,000
Cost Reconciliation Cost to be accounted for: Work in process, April 1$ 98,000Cost added during the
month827,000 Total cost to be accounted for$ 925,000Cost accounted for as follows: Work in process, April
30$ 119,400 Transferred to next department805, 600 Total cost accounted for$ 925,000
Management would like some additional information about Cooperative San Jose's operations.
Required:
What were the Mixing Department's equivalent units of production for materials and conversion for
April?
What were the Mixing Department's costs per equivalent unit for materials and conversion for April? The
beginning inventory included materials, $67,800; and conversion cost, $30,200. The costs added during
the month consisted of materials, $579,000; and conversion cost, $248,000.
How many of the units transferred out of the Mixing Department in April were started and completed
during that month?
The manager of the Mixing Department stated, "Materials prices jumped from about $2.50 per unit in
March to $3 per unit in April, but due to good cost control I was able to hold our materials cost to less
than $3 per unit for the month." Should this manager be rewarded for good cost control?
Expert Solution

This question has been solved!
Explore an expertly crafted, step-by-step solution for a thorough understanding of key concepts.
Step by stepSolved in 2 steps

Knowledge Booster
Similar questions
- 1. What were the Mixing Department's equivalent units of production for materials and conversion for April? 2. What were the Mixing Department's cost per equivalent unit for materials and conversion for April? The beginning inventory consisted of the following costs: materials, $19, 251; and conversion cost, $9,177. The costs added during the month consisted of: materials, $88, 688; and conversion cost, $43,523. 3. How many of the units transferred out of the Mixing Department in April were started and completed during that month? 4. The manager of the Mixing Department stated, "Materials prices jumped from about $2.60 per unit in March to $3.10 per unit in April, but due to good cost control I was able to hold our materials cost to less than $3.10 per unit for the month." Should this manager be rewarded for good cost control?arrow_forwardRich company produces a variety of stationery products. One product, sealing wax sticks,passes through two processes: blending and molding. The weighted average method is used toaccount for the cost of production. Two ingredients, paraffin and pigment are added at thebeginning of the process and heated and mixed for several hours. After blending, the resultingproduct is sent to the Molding department, where it is poured into molds and cooled. Thefollowing information relates to the blending process for November:a) Work in process, November 1, had 20,000 pounds, 20% complete with respect toconversion costs. Costs associated with partially completed units withParaffin $ 120,000Pigment $ 100,000Direct Labor $ 30,000Overhead applied $ 10,000b) Work in process, August 31, had 30,000 pounds, 70% complete with respect toconversion costs.c) Units completed and transferred out totaled 500,000 pounds. Costs added during themonth were:Paraffin $ 3,060,000Pigment $ 2,550,000Direct Labor $…arrow_forwardStinehelfer Beet Processors, Inc., processes sugar beets in batches. A batch of sugar beets costs $39 to buy from farmers and $13 to crush in the company's plant. Two intermediate products, beet fiber and beet juice, emerge from the crushing process. The beet fiber can be sold as is for $21 or processed further for $13 to make the end product industrial fiber that is sold for $33. The beet juice can be sold as is for $41 or processed further for $37 to make the end product refined sugar that is sold for $73. What is the financial advantage (disadvantage) for the company from processing the intermediate product beet juice into refined sugar rather than selling it as is?arrow_forward
- Stinehelfer Beet Processors, Inc., processes sugar beets in batches. A batch of sugar beets costs $56 to buy from farmers and $13 to crush in the company's plant. Two intermediate products, beet fiber and beet juice, emerge from the crushing process. The beet fiber can be sold as is for $24 or processed further for $12 to make the end product industrial fiber that is sold for $31. The beet juice can be sold as is for $43 or processed further for $29 to make the end product refined sugar that is sold for $91. What is the financial advantage (disadvantage) for the company from processing the intermediate product beet juice into refined sugar rather than selling it as is? Multiple Choicearrow_forwardplease do allarrow_forwardKosakowski Corporation processes sugar beets in batches. A batch of sugar beets costs $66 to buy from farmers and $17 to crush in the company's plant. Two intermediate products, beet fiber and beet juice, emerge from the crushing process. The beet fiber can be sold as is for $23 or processed further for $13 to make the end product industrial fiber that is sold for $36. The beet juice can be sold as is for $42 or processed further for $20 to make the end product refined sugar that is sold for $84. How much more profit (loss) does the company make by processing one batch of sugar beets into the end products industrial fiber and refined sugar? Select one: a. $22 b. ($18) c. ($116) d. $4arrow_forward
- Dogarrow_forwardBoney Corporation processes sugar beets that it purchases from farmers. Sugar beets are processed in batches. A batch of sugar beets costs $54 to buy from farmers and $11 to crush in the company's plant. Two intermediate products, beet fiber and beet juice, emerge from the crushing process. The beet fiber can be sold as is for $16 or processed further for $15 to make the end product industrial fiber that is sold for $66. The beet juice can be sold as is for $49 or processed further for $19 to make the end product refined sugar that is sold for $66. What is the financial advantage (disadvantage) for the company from processing the intermediate product beet juice into refined sugar rather than selling it as is? Multiple Choice O ($33) ($2) ($21) ($75)arrow_forwardBoney Corporation processes sugar beets that it purchases from farmers. Sugar beets are processed in batches. A batch of sugar beets costs $46 to buy from farmers and $11 to crush in the company's plant. Two intermediate products, beet fiber and beet juice, emerge from the crushing process. The beet fiber can be sold as is for $16 or processed further for $15 to make the end product industrial fiber that is sold for $58. The beet juice can be sold as is for $41 or processed further for $19 to make the end product refined sugar that is sold for $58. What is the financial advantage (disadvantage) for the company from processing the intermediate product beet juice into refined sugar rather than selling it as is?arrow_forward
- Boney Corporation processes sugar beets that it purchases from farmers. Sugar beets are processed in batches. A batch of sugar beets costs $65 to buy from farmers and $24 to crush in the company's plant. Two intermediate products, beet fiber and beet juice, emerge from the crushing process. The beet fiber can be sold as is for $35 or processed further for $39 to make the end product industrial fiber that is sold for $87. The beet juice can be sold as is for $56 or processed further for $43 to make the end product refined sugar that is sold for $87. What is the financial advantage (disadvantage) for the company from processing one batch of sugar beets into the end products industrial fiber and refined sugar rather than not processing that batch at all?arrow_forwardBoney Corporation processes sugar beets that it purchases from farmers. Sugar beets are processed in batches. A batch of sugar beets costs $59 to buy from farmers and $18 to crush in the company's plant. Two intermediate products, beet fiber and beet juice, emerge from the crushing process. The beet fiber can be sold as is for $29 or processed further for $27 to make the end product industrial fiber that is sold for $75. The beet juice can be sold as is for $50 or processed further for $31 to make the end product refined sugar that is sold for $75. What is the financial advantage (disadvantage) for the company from processing one batch of sugar beets into the end products industrial fiber and refined sugar rather than not processing that batch at all? Multiple Choice O $15 per batch $16 per batch ($4) per batch ($135) per batcharrow_forwardHealthway uses a process-costing system to compute the unit costs of the minerals that it produces. It has three departments: Mixing, Tableting, and Bottling. In Mixing, at the beginning of the process all materials are added and the ingredients for the minerals are measured, sifted, and blended together. The mix is transferred out in gallon containers. The Tableting Department takes the powdered mix and places it in capsules. One gallon of powdered mix converts to 1,600 capsules. After the capsules are filled and polished, they are transferred to Bottling where they are placed in bottles, which are then affixed with a safety seal and a lid and labeled. Each bottle receives 50 capsules. During July, the following results are available for the first two departments (direct materials are added at the beginning in both departments): Overhead in both departments is applied as a percentage of direct labor costs. In the Mixing Department, overhead is 200 percent of direct labor. In the Tableting Department, the overhead rate is 150 percent of direct labor. Required: 1. Prepare a production report for the Mixing Department using the weighted average method. Follow the five steps outlined in the chapter. Round unit cost to three decimal places. 2. Prepare a production report for the Tableting Department. Materials are added at the beginning of the process. Follow the five steps outlined in the chapter. Round unit cost to four decimal places.arrow_forward
arrow_back_ios
SEE MORE QUESTIONS
arrow_forward_ios
Recommended textbooks for you
- Cornerstones of Cost Management (Cornerstones Ser...AccountingISBN:9781305970663Author:Don R. Hansen, Maryanne M. MowenPublisher:Cengage LearningManagerial Accounting: The Cornerstone of Busines...AccountingISBN:9781337115773Author:Maryanne M. Mowen, Don R. Hansen, Dan L. HeitgerPublisher:Cengage Learning
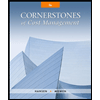
Cornerstones of Cost Management (Cornerstones Ser...
Accounting
ISBN:9781305970663
Author:Don R. Hansen, Maryanne M. Mowen
Publisher:Cengage Learning
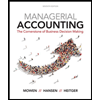
Managerial Accounting: The Cornerstone of Busines...
Accounting
ISBN:9781337115773
Author:Maryanne M. Mowen, Don R. Hansen, Dan L. Heitger
Publisher:Cengage Learning