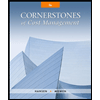
Cornerstones of Cost Management (Cornerstones Series)
4th Edition
ISBN: 9781305970663
Author: Don R. Hansen, Maryanne M. Mowen
Publisher: Cengage Learning
expand_more
expand_more
format_list_bulleted
Question
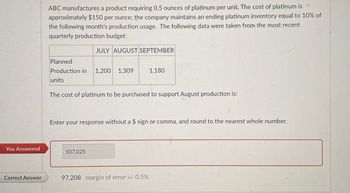
Transcribed Image Text:ABC manufactures a product requiring 0.5 ounces of platinum per unit. The cost of platinum is
approximately $150 per ounce; the company maintains an ending platinum inventory equal to 10% of
the following month's production usage. The following data were taken from the most recent
quarterly production budget:
JULY AUGUST SEPTEMBER
Planned
Production in 1,200 1,309
1,180
units
The cost of platinum to be purchased to support August production is:
Enter your response without a $ sign or comma, and round to the nearest whole number.
You Answered
107,025
Correct Answer
97,208 margin of error +/- 0.5%
Expert Solution

This question has been solved!
Explore an expertly crafted, step-by-step solution for a thorough understanding of key concepts.
Step by stepSolved in 2 steps with 2 images

Knowledge Booster
Similar questions
- The Simmons Company finished their sales projections for the coming year. The company produces one product. Part of next year's sales projections are as follows. Projected Sales in Units July 125,000 August 145,000 September 139,000 October 155,000 November 180,000 The budget committee has also completed the following information on inventories. Raw Materials Ending Balance, June, 50,000 lbs Desired ending levels (monthly 10% of next month's production needs) Work-In-Progress None Finished Goods Inventory Ending Balance, June, 22,000 units Desired ending levels: 20% of next month's sales The Engineering Department has developed the following standards upon which the production budgets will be developed. Item Standard Material usage 3 pounds per unit Material price per pound $2.00 per pound Labor usage 0.5 hours per unit Labor rate $40 per hour Machine hours 2 machine hours per unit The Simmons Company uses a modified allocation method for…arrow_forwardThe Simmons Company finished their sales projections for the coming year. The company produces one product. Part of next year's sales projections are as follows. Projected Sales in Units July 125,000 August 145,000 September 139,000 October 155,000 November 180,000 The budget committee has also completed the following information on inventories. Raw Materials Ending Balance, June, 50,000 lbs Desired ending levels (monthly 10% of next month's production needs) Work-In-Progress None Finished Goods Inventory Ending Balance, June, 22,000 units Desired ending levels: 20% of next month's sales The Engineering Department has developed the following standards upon which the production budgets will be developed. Item Standard Material usage 3 pounds per unit Material price per pound $2.00 per pound Labor usage 0.5 hours per unit Labor rate $40 per hour Machine hours 2 machine hours per unit The Simmons Company uses a modified allocation method for…arrow_forwardTucker Inc. makes dog treats. The material to be purchased from the production budget is as follows: April May JuneMaterial to be purchased 161,800 270,900 195,600 Tucker Inc. pays $0.40 per kilo for its material. 60% of a months purchases are paid for in th month of purchase, 40% is paid for in the following month. The March 31 accounts payable balance is $10,000 and will be paid in full in the first month. The total cash disbursement for April is ____________ The total cash disbursement for May is ____________ The total cash disbursement for June is ____________ The total cash disbursement for the quarter is____________arrow_forward
- Coles Corporation, Incorporated makes and sells a single product, Product R. Three yards of Material K are needed to make one unit of Product R. Budgeted production of Product R for the next five months is as follows: a. b. August September October C. d. November December The company wants to maintain monthly ending inventories of Material K equal to 20% of the following month's production needs. On July 31, this requirement was not met since only 2,500 yards of Material K were on hand. The cost of Material K is $0.85 per yard. The company wants to prepare a Direct Materials Purchase Budget for the rest of the year. The total cost of Material K to be purchased in August is: 14,000 units 14,500 units 15,500 units 12,600 units 11,900 units $42,300 $33,840 $48,200 $40,970arrow_forwardThe production department of Zan Corporation has submitted the following forecast of units to be produced by quarter for the upcoming fiscal year: 1st Quarter 14,000 Units to be produced In addition, 24,500 grams of raw materials inventory is on hand at the start of the 1st Quarter and the beginning accounts payable for the 1st Quarter is $6,600. Req 1 and 2 Each unit requires 7 grams of raw material that costs $1.40 per gram. Management desires to end each quarter with an inventory of raw materials equal to 25% of the following quarter's production needs. The desired ending inventory for the 4th Quarter is 7,000 grams. Management plans to pay for 60% of raw material purchases in the quarter acquired and 40 % in the following quarter. Each unit requires 0.40 direct labor-hours and direct laborers are paid $15.50 per hour. Req 3 2nd Quarter 17,000 Required: 1. and 2 Calculate the estimated grams of raw material that need to be purchased and the cost of raw material purchases for each…arrow_forwardAccepting Business at a Special Price Power Pack Company expects to operate at 80% of productive capacity during July. The total manufacturing costs for July for the production of 45,000 batteries are budgeted as follows: Direct materials $375,000 Direct labor 160,750 Variable factory overhead 71,750 Fixed factory overhead 261,250 Total manufacturing costs $868,750 The company has an opportunity to submit a bid for 4,500 batteries to be delivered by July 31 to a government agency. If the contract is obtained, it is anticipated that the additional activity will not interfere with normal production during July or increase the selling or administrative expenses. What is the unit cost below which Power Pack Company should not go in bidding on the government contract? Round your answer to two decimal places. per unitarrow_forward
- Accepting Business at a Special Price Forever Ready Company expects to operate at 90% of productive capacity during July. The total manufacturing costs for July for the production of 34,200 batteries are budgeted as follows: Direct materials $272,100 Direct labor 100,000 Variable factory overhead 28,040 Fixed factory overhead 56,000 Total manufacturing costs $456,140 The company has an opportunity to submit a bid for 2,000 batteries to be delivered by July 31 to a government agency. If the contract is obtained, it is anticipated that the additional activity will not interfere with normal production during July or increase the selling or administrative expenses. What is the unit cost below which Forever Ready Company should not go in bidding on the government contract? Round your answer to two decimal places. per unitarrow_forwardThe production department of Zan Corporation has submitted the following forecast of units to be produced by quarter for the upcoming fiscal year: Units to be produced 1st Quarter 2nd Quarter 3rd Quarter 4th Quarter 7,000 10,000 9,000 8,000 In addition, 8,750 grams of raw materials inventory is on hand at the start of the 1st Quarter and the beginning accounts payable for the 1st Quarter is $5,200. Each unit requires 5 grams of raw material that costs $1.60 per gram. Management desires to end each quarter with an inventory of raw materials equal to 25% of the following quarter's production needs. The desired ending inventory for the 4th Quarter is 6,000 grams. Management plans to pay for 60% of raw material purchases in the quarter acquired and 40% in the following quarter. Each unit requires 0.20 direct labor-hours and direct laborers are paid $13.50 per hour. Required: 1. and 2. Calculate the estimated grams of raw material that need to be purchased and the cost of raw material…arrow_forwardNeed 1,2,3 pleasearrow_forward
- The production department of Zan Corporation has submitted the following forecast of units to be produced by quarter for the upcoming fiscal year: Units to be produced 1st Quarter 2nd Quarter 3rd Quarter 4th Quarter 12,000 15,000 14,000 13,000 In addition, 15,000 grams of raw materials inventory is on hand at the start of the 1st Quarter and the beginning accounts payable for the 1st Quarter is $6,200. Each unit requires 5 grams of raw material that costs $1.80 per gram. Management desires to end each quarter with an inventory of raw materials equal to 25% of the following quarter's production needs. The desired ending inventory for the 4th Quarter is 5,000 grams. Management plans to pay for 60% of raw material purchases in the quarter acquired and 40% in the following quarter. Each unit requires 0.40 direct labor-hours and direct laborers are paid $13.50 per hour. Required: 1. and 2. Calculate the estimated grams of raw material that need to be purchased and the cost of raw material…arrow_forwardHaresharrow_forwardThe production department of Zan Corporation has submitted Le following forecast of units to be produced by quarter for the upcoming fiscal year: Units to be produced In addition, 7,700 grams of raw materials inventory is on hand at the start of the 1st quarter and the beginning accounts payable for the 1st quarter is $4,580. Required production in units of finished goods Each unit requires 9.70 grams of raw material that costs $160 per gram Management desires to end each quarter with an inventory of raw materials equal to 20% of the following quarter's production needs. The desired ending inventory for the 4th quarter is 9,700 grams. Management plans to pay for 80% of raw material purchases in the quarter acquired and 20% in the following quarter. Each unit requires 0.40 direct labour-hours and direct labourers are paid $8.10 per hour. Required: 1. Prepare the company's direct materials purchases budget and schedule of expected cash disbursements for materials for the upcoming fiscal…arrow_forward
arrow_back_ios
SEE MORE QUESTIONS
arrow_forward_ios
Recommended textbooks for you
- Cornerstones of Cost Management (Cornerstones Ser...AccountingISBN:9781305970663Author:Don R. Hansen, Maryanne M. MowenPublisher:Cengage LearningManagerial AccountingAccountingISBN:9781337912020Author:Carl Warren, Ph.d. Cma William B. TaylerPublisher:South-Western College PubManagerial Accounting: The Cornerstone of Busines...AccountingISBN:9781337115773Author:Maryanne M. Mowen, Don R. Hansen, Dan L. HeitgerPublisher:Cengage Learning
- Principles of Accounting Volume 2AccountingISBN:9781947172609Author:OpenStaxPublisher:OpenStax CollegePrinciples of Cost AccountingAccountingISBN:9781305087408Author:Edward J. Vanderbeck, Maria R. MitchellPublisher:Cengage Learning
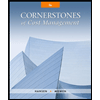
Cornerstones of Cost Management (Cornerstones Ser...
Accounting
ISBN:9781305970663
Author:Don R. Hansen, Maryanne M. Mowen
Publisher:Cengage Learning
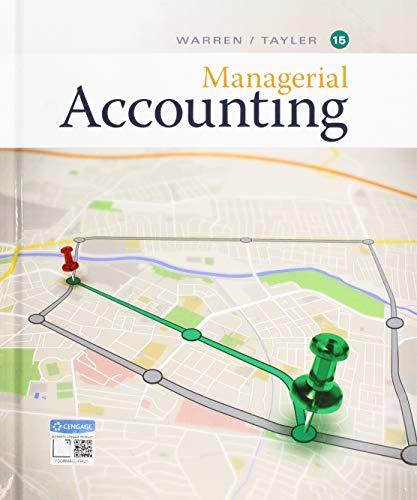
Managerial Accounting
Accounting
ISBN:9781337912020
Author:Carl Warren, Ph.d. Cma William B. Tayler
Publisher:South-Western College Pub
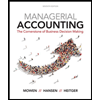
Managerial Accounting: The Cornerstone of Busines...
Accounting
ISBN:9781337115773
Author:Maryanne M. Mowen, Don R. Hansen, Dan L. Heitger
Publisher:Cengage Learning
Principles of Accounting Volume 2
Accounting
ISBN:9781947172609
Author:OpenStax
Publisher:OpenStax College
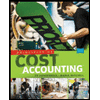
Principles of Cost Accounting
Accounting
ISBN:9781305087408
Author:Edward J. Vanderbeck, Maria R. Mitchell
Publisher:Cengage Learning
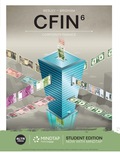